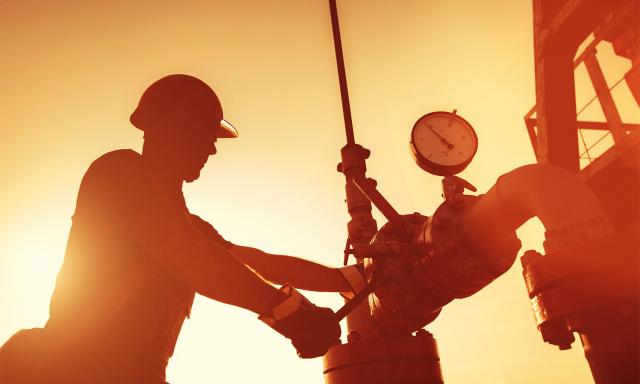
(Source: Tereshchenko Dmitry/Shutterstock.com)
Presented by:
Editor's note: This article originally appeared in the April issue of E&P Plus.
Subscribe to the digital publication here.
The drive to capture every molecule of efficiency across every facet of an E&P operation has manifested in plenty of positive ways for oil and gas companies: stronger, faster return on capital investments, shorter development cycles, larger commodity margins, and the list goes on.
As heavily as E&P companies have focused on operational efficiency, there’s one area that may still offer opportunity for substantial efficiency gains: shutdown, turnaround and outage (STO). While companies have spent millions to improve and reinvent processes, there’s still room for them to optimize, accelerate and simplify STO. Some companies, as digitally mature as they may be in certain aspects of their operations, continue to manage STO organically rather than strategically, with a patchwork of sometimes ill-fitting point solutions that hamper their ability to optimize this critical area of their operation.
And it appears they are paying the price for doing so. SAP calculates that by taking a more integrated approach to STO, a company can shorten a shutdown by 5% to 10%. For a production site, SAP projects that would translate into savings of $3.5 million to $6.5 million for the entire shutdown period.
While these figures are hypothetical, potential savings of this magnitude are reason enough for companies to take a closer look at their STO practices and processes as well as the technologies they use to manage them.
Pain points
As tempting as it may be to leave STO alone, the ramifications—financial and otherwise —are too large to overlook. Not only can STO account for up to 50% of a plant’s annual maintenance budget, it also can have a major impact on a company and its brand should there be an HSE-related incident. What’s more, the loss of revenue and income during a shutdown can amount to multiple times the cost of the shutdown itself.
STO is fraught with potential pain points, as SAP has learned from a recent analysis conducted with McKinsey. That analysis, drawn from dozens of interviews with executives at 18 companies around the globe, highlights some of them.
If some of those pain points seem all too familiar, then a company’s STO processes and the technology that underpins it could be ripe for scrutiny. The following sections highlight the best-in-class approaches and capabilities that SAP is seeing E&P companies deploy to tighten up their STO projects and capture efficiencies that go right to the bottom line.
Start with integration
Companies that are most efficient with STO tend to have one thing in common: their systems are fully and seamlessly integrated, enabling data and insight to flow freely among the various facets of the business touched by STO, throughout the entire process of scoping, planning, executing and project close-out. A patchwork of siloed systems driven by software that struggles to communicate can lead to uninformed decision-making, project bottlenecks, inefficient workforce deployment, safety issues and, ultimately, costly delays and less than desirable outcomes.
STO outcomes look much different when there’s a fully integrated digital system to help guide the process—when HR, procurement, finance, budgeting and costing, project management, third-party scheduling tools and the like are connected and working from a single source of truth. So information about scope changes, materials, logistics and completion of work flows to relevant parts of the business to support end-to-end strategic planning, processes and decision-making.
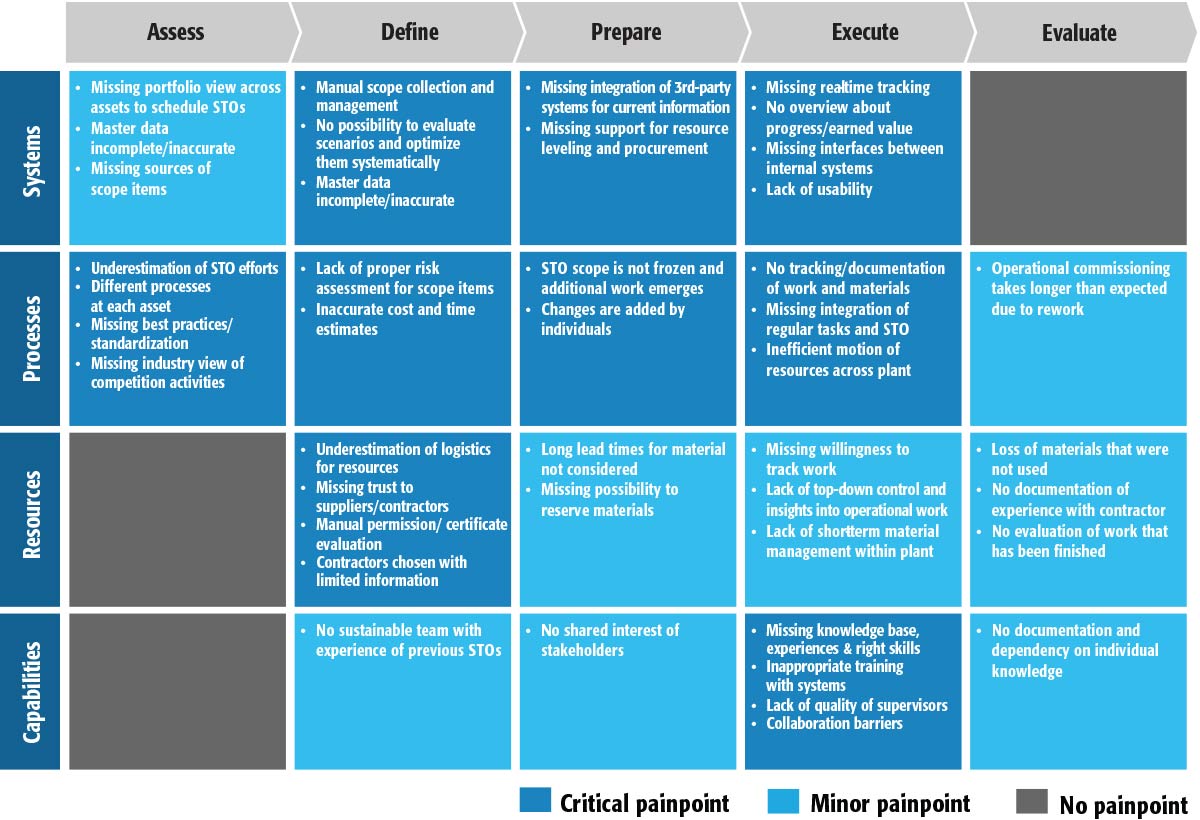
With a high level of integration across systems, key elements of STO, including scoping, and planning around cost, materials and operations as well as tactical planning and scheduling become much more straightforward. A company gains the ability to evaluate scenarios and systematically optimize processes. They also benefit from improved collaboration and cooperation within and across teams and departments.
In short, integration is a game changer.
Mobile makes a difference
With mobile capabilities as part of the integrated system, real-time connectivity becomes a two-way street between onsite workers (i.e., internal personnel, contractors and subcontractors) and the enterprise. Mobile-enabled workers can access resources (e.g., training and troubleshooting) in real time to help them execute tasks. They also can report in-the-moment findings during scope discovery, receive new tasks and log task completion in the moment instead of having to traffic paperwork at shift’s end.
Meanwhile, the enterprise can monitor workers remotely, tracking them with sensor-equipped wearable technology, informing them of plant conditions and sending them information relevant to the task at hand.
All this can result in a huge jump in worker productivity and workforce maximization.
Advanced modeling and predictive capabilities
The ability to quickly analyze data and model scenarios brings a new level of efficiency to asset performance management, speeding and strengthening decision-making throughout an STO project.
These tools are proving indispensable in generating risk, cost and time estimations for scope items and, more generally, in properly defining scope. iIn the STO world, a well-defined scope often leads to a positive project outcome with the ability to reduce STO duration by as much as 20%.
An execution control tower
Visibility into every aspect of an STO project is critical to a positive outcome. When decision-makers have the data right in front of them in a user-friendly digital environment—where they can access progress reports, details on next steps and real-time updates on HSE conditions; view key performance indicators based on real-time calculations; and assess the risk/cost/impact of potential scope and timeline changes—they’re better equipped to make decisions on the fly. Rescheduling and replanning in real time become a reality.
Ultimately, having a highly connected control center can increase workforce efficiency, reduce overruns, avoid scope creep, tighten issue resolution and optimize resources, all of which positively impact project finances.
Connectivity with suppliers, contractors and other external resources
Extending the seamless flow of data and insight as well as access to vital project information to key external players in an STO project is another way to improve overall project efficiency. Open connectivity with contractors enables them to access best practices, training resources and mobile apps for reporting on task status and plant conditions, among other items. And internally, key project supervisors and planners can keep close tabs on work progress and process adherence, and pass on change orders as they’re approved.
A similar level of connectivity with the supply chain enables a company to maintain a firm grip on logistics, materials, potential supply bottlenecks and other factors that can impact a project.
Standardization and governance
The goal with STO should be to make each project more efficient than the one prior. This entails standardizing processes across assets and projects, developing and disseminating STO best practices, and generally capturing the learnings from each and every project so they can be applied to subsequent projects. Establishing standards, milestones and benchmarks, ensuring process adherence and building institutional knowledge, analyzing the quality of contractors’ work—all of this is predicated on the existence of a readily accessible, simple-to-update knowledge base.
There’s no need to reinvent the wheel with every STO project. With higher levels of standardization and governance in those projects, an E&P company not only can capture new efficiencies in those projects, it can focus on its core business.
Recommended Reading
NOV Announces $1B Repurchase Program, Ups Dividend
2024-04-26 - NOV expects to increase its quarterly cash dividend on its common stock by 50% to $0.075 per share from $0.05 per share.
Repsol to Drop Marcellus Rig in June
2024-04-26 - Spain’s Repsol plans to drop its Marcellus Shale rig in June and reduce capex in the play due to the current U.S. gas price environment, CEO Josu Jon Imaz told analysts during a quarterly webcast.
US Drillers Cut Most Oil Rigs in a Week Since November
2024-04-26 - The number of oil rigs fell by five to 506 this week, while gas rigs fell by one to 105, their lowest since December 2021.
CNX, Appalachia Peers Defer Completions as NatGas Prices Languish
2024-04-25 - Henry Hub blues: CNX Resources and other Appalachia producers are slashing production and deferring well completions as natural gas spot prices hover near record lows.
Chevron’s Tengiz Oil Field Operations Start Up in Kazakhstan
2024-04-25 - The final phase of Chevron’s project will produce about 260,000 bbl/d.