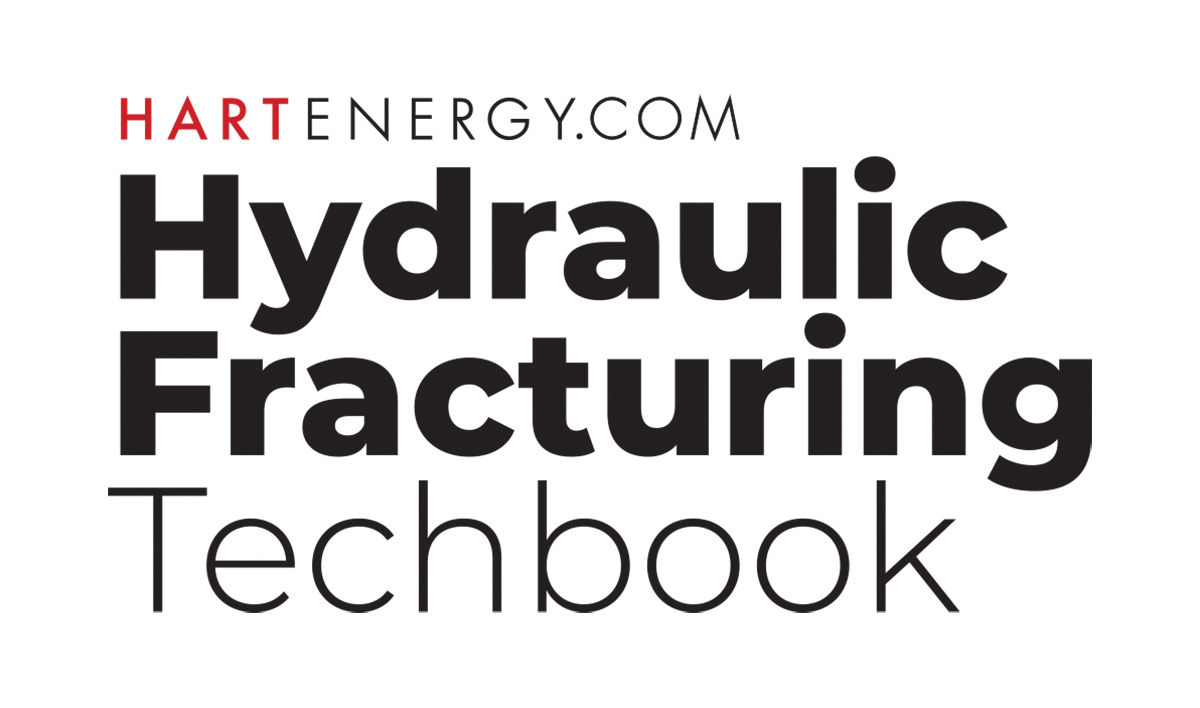
Today’s unconventional oil and gas developments bear scant resemblance to those of a decade ago, and experts designing new technologies say things will look even more different in the next few years.
That’s because the focus of operators has shifted from maximizing production to maximizing shareholder distribution and reducing debt, said Ryan Duman, Wood Mackenzie’s director of upstream research.
“That has shifted the focus to technologies that improve efficiency,” he told Hart Energy.
Partly, that stems from operators acquiring step-out acreage and adding to their inventories between 2016 and 2019.
“Now, they need to find the most efficient way to harvest what they already have, and that means doing more with less,” Duman said.
For many companies, that has meant exploring ways to leverage automation software and AI to streamline operations.
“Using data captured in real time, 24/7, provides a clearer picture of operations, which leads to better decision-making,” Duman said.
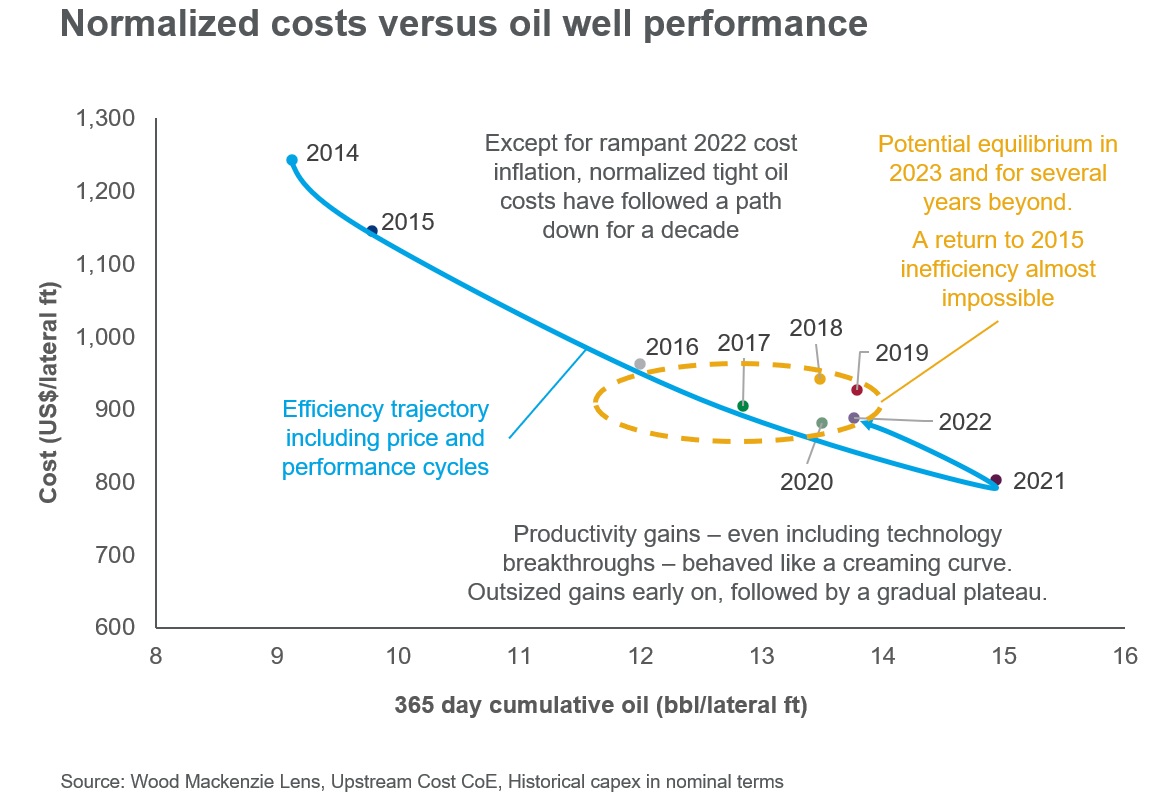
Operators are using operational data to fine-tune processes and are applying advanced analytics to real-time data, monitoring the performance of tools and equipment, and decreasing downtime through predictive maintenance.
“The market demand for ESG reporting is another driver that has made operators more bullish for technology such as electric equipment, on-site gas turbines to generate electricity, no-bleed pneumatics, and lower-emitting kits,” he said, noting that reducing the environmental footprint of operations and improving economics are sometimes competing priorities.
Despite the challenges, Duman said the industry overall has embraced ESG, and companies are making changes that allow them to market themselves attractively to investors.
“They are reducing methane and flaring, and the cost of the technologies that are helping them achieve those goals is more than offset with incremental revenue gains,” he said.
Wood Mackenzie will continue to watch refracturing and EOR technologies, which Duman believes are ripe for greater innovation.
“Because of the potential benefits associated with 45Q [tax] credits, there is going to be a push for CCUS development as well,” he said, referring to carbon capture, utilization and sequestration. “This tends to make sense from a core competency standpoint because companies can leverage in-house knowledge.”
Electrification, alternative fuels, and the value of automation
To Sam Sledge, CEO of ProPetro, the most dramatic change in the past couple of years is the transition from diesel to mostly natural gas as a primary fuel source.
“The transition away from diesel has been going on for three years, but right now, there is a massive recapitalization from a hard asset and financial standpoint going on in our space, and it might be one of the biggest changes at the well site,” said Sledge, whose hydraulic fracturing company is 100% focused on the Permian Basin.
The primary reason for the transition is pure economics, he said.
“It is much less expensive to burn a molecule of natural gas than a molecule of diesel,” Sledge said. That economic inducement is aligned with the environmental objective of lowering emissions. “If we want to talk about environmental sustainability, I think it is strongest when it runs parallel with economic incentives. We live in a free-market, capitalist country, and the goal of a company is to make money, but our goal as citizens and members of a community is to take care of the place where we live.”
The result?
“We are pushing harder and faster to the future, especially from an equipment standpoint,” Sledge said. “The main part of that story is electrified equipment, which is mechanically simpler with fewer moving parts, allowing it to be operated precisely and accurately.”
ProPetro planned to deploy its first electric fleet in early summer 2023, but the company already employs dual-fuel engines—technology pioneered by Caterpillar that enables the engine to burn diesel and natural gas at the same time.
“We think this is a bridge to more electrification,” Sledge said. “This is possibly the only application in the world that consumes diesel and gas simultaneously.”
Sledge expects many more innovations going forward.
“We are on a continuum, and we don’t know where the end of the continuum is. There are so many smart people and so much entrepreneurial spirit in the oil and gas sector that I think you’re going to see a lot of amazing things happen over the next 10 to 20 years,” he said.
Displacing diesel
Leen Weijers shares Sledge’s sentiments about economics continuing to drive innovation.
“Every company wants to add efficiencies to produce each barrel of oil more economically,” said Weijers, Liberty Energy’s vice president of engineering.
One of the ways Liberty is going about achieving that is by inventing and manufacturing operational equipment such as the Scorpion sand delivery system and the Mantis screwless sand delivery system, which moves sand directly into the blender tub.
“This equipment has enabled us to effectively pump local wet sand, which can be purchased at a lower cost than sand traditionally used for hydraulic fracturing operations,” he said.
The company also is developing ways to manage fuel consumption and equipment performance. For example, the company’s new digiFrac fleets enable diesel replacement with natural gas or CNG, both of which are much less expensive per energy unit.
“As we roll out digiFrac equipment, we now regularly break daily records for diesel displacement in the basins where we operate,” Weijers said.
The company also has made moves to address the vulnerabilities associated with gas-only equipment by taking ownership of the natural gas/CNG delivery system through Liberty Power Innovations (LPI) to provide a reliable source of field gas (through mobile gas processing) or CNG to power its lower-emission solutions.
Underpinning the digiFrac and digiPrime fully electric frac system technology are Rolls-Royce gas reciprocating engines, which, according to Weijers, have the best thermal efficiencies of any engine available.
“Measuring performance in terms of hydraulic horsepower hours (HHP/hr) pumped for 70% daily pump efficiencies, gas reciprocating engines have about 45% lower emissions than Tier IV diesel and are three times as clean as gas turbines,” he said.
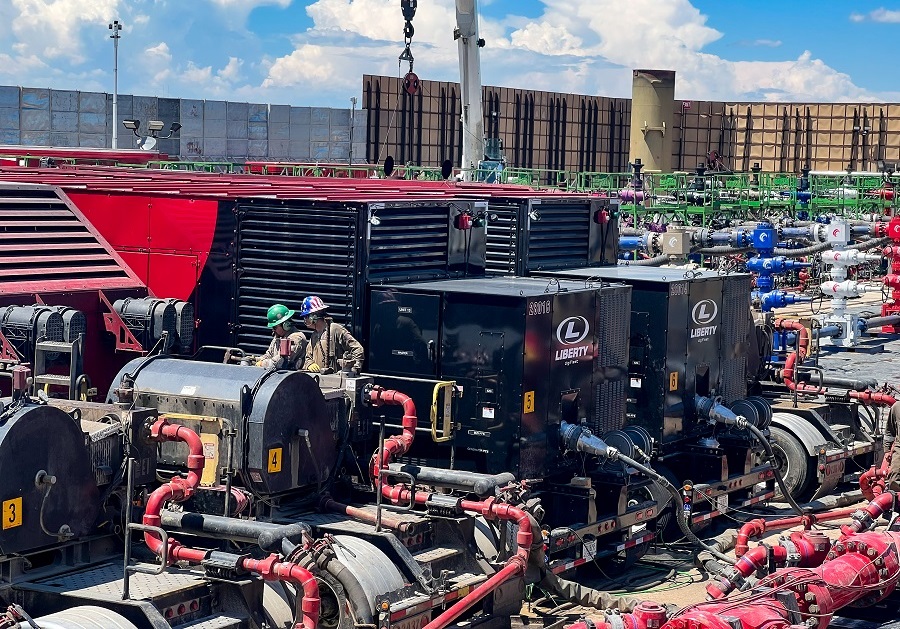
It’s critical to improve operations incrementally, so Liberty focuses on putting new technologies to work as soon as it is practical.
“We are always looking for ways to cut emissions, reduce our footprint, minimize noise and curtail the number of trips to the work site to be a better neighbor in the areas where we work,” Weijers said.
Liberty Energy is among the companies that have developed software that uses field data to increase efficiencies and ultimately improve the bottom line. Weijers described his company as “laser focused on reducing the barrel cost of production.”
Liberty achieves this, in part, by leveraging its FracTrends database and performing statistical economics analysis using Fraconomics and fit-for-purpose calibrated modeling tools.
“We are helping to focus our industry on cost-effective ways to provide ever larger and denser fracture networks and to evaluate trade-offs, for example, between well density and fracture treatment size,” he said.
Results over the last decade demonstrate that the company has helped lower well costs by 50% and enhanced well productivity to reduce the cost per barrel of oil produced by as much as 75%, Weijers said.
Innovators at Halliburton are likewise well down the path of deploying electric fracturing equipment. By providing the same horsepower at the wellsite with half as much equipment, these innovations allow a company to reduce its carbon footprint, as well as make strides in efficiency and reliability.
“We see about 30% faster transition times, which leads to more pumping hours,” William Ruhle, Halliburton’s strategic business manager, told Hart Energy. “That gives us 11% more hp-hr pumped per month than diesel, which is about equivalent to completing an extra seven wells per year per crew.”
Removing the need for diesel has saved up to $2.5 million per month in diesel costs for zipper crews and reduces emissions by approximately 30%, Ruhle said. While there is a cost for electricity to run the equipment, it is considerably less than the cost of diesel.
On a project for Diamondback Energy in the Permian Basin, a Halliburton simul-frac crew achieved exceptional results using the company’s Zeus electric fracturing system, which Ruhle said can achieve up to 5,000 hydraulic hp per pumping unit without downtime during stage transitions.
“By combining simul-frac operations with electric, Diamondback has realized completions savings of $50 a foot,” he said.
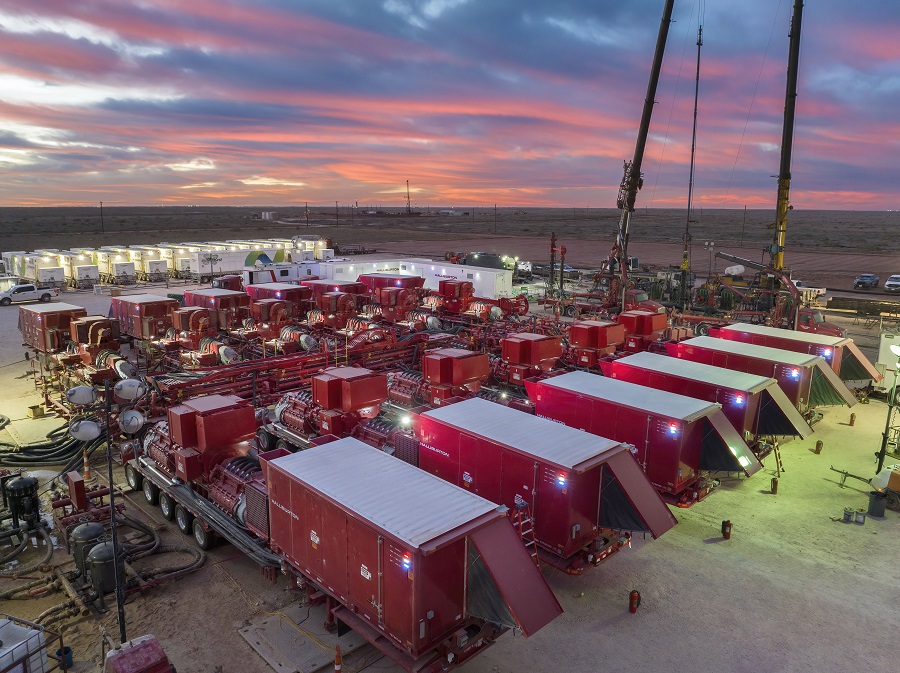
Electrification is driving down costs and reducing emissions, but operators need to capture more efficiency gains, and that has led to expanded use of subsurface monitoring and using operational data gathered to optimize recovery.
“Digitization is embedded in everything we do and build; ML (machine learning) and AI aren’t discrete solutions, they are embedded in processes and solutions,” Ruhle said.
One example is the company’s Octiv intelligent fracturing platform, which fully automates the fracturing process from a single system.
“Within that platform, we use technology such as AI and ML to predict equipment failures, identify anomalies, see how operations are running and respond automatically,” he said. “Octiv automates up to 90% of the decisions made to control our surface equipment, and that leads to better reliability and consistency.”
In North America, the system has completed thousands of stages using full-spread automation, controlling the fracturing process and executing condition-based protections that help prevent downtime across operations.
Capitalizing on data analysis and specialized chemistry
James Segars, director of solutions engineering at Universal Pressure Pumping, said his company is delivering value by analyzing data to optimize perforation efficiency.
“A huge amount of effort has gone into analyzing fracture geometry with regard to perforation design in the past few years,” he said, noting that complex analysis goes far beyond simply creating the longest possible fracture. “We are targeting a high degree of recovery within the near wellbore section to make the most of the wellbore spacing plan. From our standpoint, that is making the output more predictable, and that creates a positive impact on the economics of the program.”
The company’s solutions engineering team uses data to help operators with predictive analysis.
“We use output from laboratory testing to generate a hydraulics model to estimate pipe friction, which allows us to set expectations for surface treatment conditions. Ultimately, we can solve for the expected hydraulic horsepower hours and can generate a high-level assessment for cost and ESG consideration through fuel savings,” he said.
Engineers also compare the predicted pressure to the actual pressure in end-of-stage variance reporting and examine the data to determine when there is a difference, then share the findings with the operator to evaluate opportunities for improvement.
“We also know proppant delivery on a stage basis is critical to recovery as is controlling the volume of fluid we’re injecting. In addition to managing differential pressure, we are looking at the volume of proppant used and identifying stages in which more or less fluid was pumped than expected. Many inefficiencies are rooted in variances between what was designed and what was delivered,” Segars said. “Operators spend a lot of time and effort developing the fracture sequence, and they know what works best for their reservoir. Our job is to help them deploy that in a predictable and consistent manner.”
Universal is also investing in developing tailored chemistries to help resolve challenges that routinely surface in the field. One of these is increased friction resulting from the use of higher salinity brines in place of fresh water, particularly in parts of New Mexico and Texas.
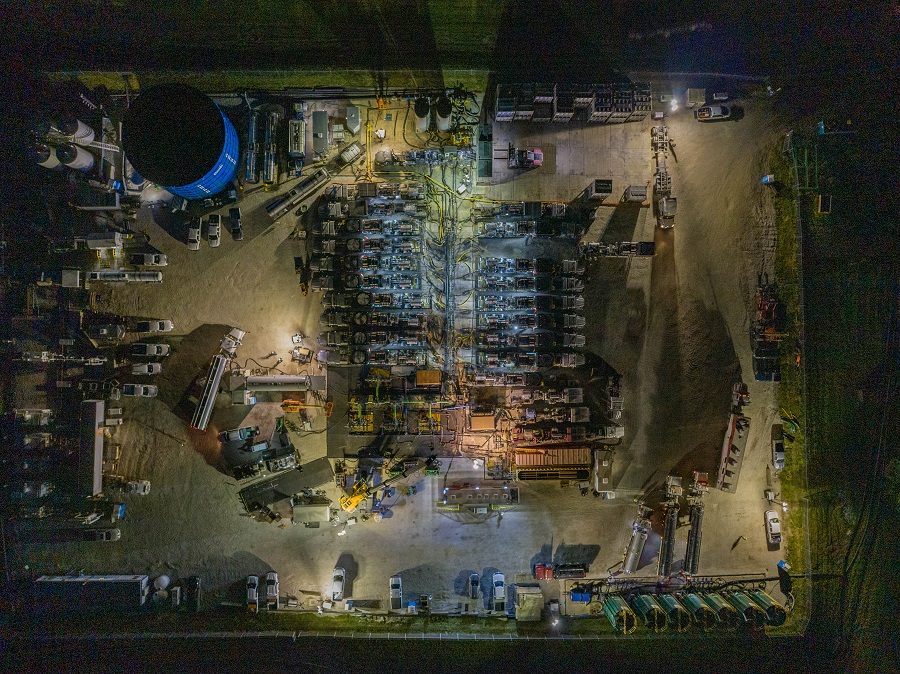
“Chemical technology is being improved upon daily to allow the use of as much brine as possible and to ensure produced water is reusable,” said Joe Pinkhouse, Universal’s chemistry domain champion.
Water is a valuable resource and scarce in some areas where there is widespread drilling. Increasing the amount of fresh water that can be reused cuts down on water usage as well as treatment and disposal costs, he said.
The industry is trying to figure out whether the use of produced water is beneficial to the reservoirs, Pinkhouse said.
“Historically, the view overwhelmingly has been negative, but new research shows that the produced water—as long as it is used appropriately—has the ability to enhance the performance of the reservoir and perhaps eliminate some of the chemical needs.”
Making headway with these initiatives depends on changing the perception of chemicals as commodities rather than specialty materials — and assuming, for example, that one clay stabilizer is the same as another.
“That’s simply not true,” he said. “There is a lot of time and energy that goes into developing the chemistries, and we work with operators to ensure they are looking at data and comparing the products in a meaningful way.”
Pioneering technology and the art of oilfield economics
Software advances continue to improve field operations and ResFrac, a company that provides computational subsurface modeling, is taking software to the next level.
COO Garrett Fowler explained how the solutions developed by his company address problems that have arisen from erroneously applying “factory mode” development to oil and gas operations.
“Wells interact. Rock is variable. And there are nuances that differentiate individual wells and locations, so applying a single well design across a range of wells does not produce consistent results,” he said.
What is known about the subsurface continues to expand.
“Diagnostics today give us the ability to see into subsurface an order of magnitude better than 10 years ago,” he said. “And applying first principles physics will unlock even better understanding.”
Multiple things happen in the subsurface simultaneously, but the traditional methodology for subsurface modeling has been to segment activities and use separate pieces of software to calculate them independently. Fowler said that’s why modeling software has struggled to produce a truly cohesive picture of the subsurface.
“It is computationally and mathematically challenging to model all of the variables in one self-consistent, coherent set of equations where everything happens at once, but it is possible,” he said.
ResFrac initiates the process by building a “why” model using first principle physics.
“Once we have a model that accurately describes how things are acting in the rock, we apply algorithms that use data analytical techniques,” Fowler said. “Optimization algorithms run a variety of hypothetical simulations—moving a well 50 feet deeper, for example, or using twice as much fluid—to determine the best next step in the development process.”
Fowler contends that this approach makes it possible to see the interaction between oil prices and well spacing.
“The ideal distance between the existing wellbore and new wellbore depends on oil price because if you look at an internal rate of return, or net present value analysis, or other financial metrics, the degree of interference you tolerate is tied to the amount of revenue you can expect per barrel of oil,” he said.
He believes the future of the industry is in prescriptive design that derives from enhanced understanding of the subsurface, where it is now possible to observe what is happening and explain why.
“The industry is mature enough to layer surface engineering, subsurface engineering and financial engineering to get a clearer picture of what should be done in a given situation,” he said.
Building a computation framework for understanding these systems is crucial to establishing a foundation for extrapolating beyond hydrocarbons and examining how resources are extracted generally.
“That could lead to enabling extraction of other resources such as geothermal heat or exploiting the open pore space in the subsurface for carbon sequestration,” Fowler said. “It becomes a matter of looking at what resources exist and what expertise we have as an industry to extract those resources.”
Recommended Reading
Oilfield Service Companies Dril-Quip, Innovex to Merge
2024-03-18 - Dril-Quip Inc. and Innovex Downhole Solutions Inc. will emerge as a new company, Innovex International, with expanded reach in global markets.
Talos Energy Sells CCS Business to TotalEnergies
2024-03-18 - TotalEnergies’ acquisition targets Talos Energy’s Bayou Bend project, and the French company plans to sell off the remainder of Talos’ carbon capture and sequestration portfolio in Texas and Louisiana.
EQT, Equitrans to Merge in $5.45B Deal, Continuing Industry Consolidation
2024-03-11 - The deal reunites Equitrans Midstream Corp. with EQT in an all-stock deal that pays a roughly 12% premium for the infrastructure company.
Continental Resources Makes $1B in M&A Moves—But Where?
2024-02-26 - Continental Resources added acreage in Oklahoma’s Anadarko Basin, but precisely where else it bought and sold is a little more complicated.
Permian Activity in ‘Low-to-no-growth’ Mode for First Half
2024-02-22 - After multiple M&A moves in 2023 and continued E&P adherence to capital discipline, Permian Basin service company ProPetro sees the play holding steady.