Whether it is supporting production activities, measuring multiphase flow rates downhole or tackling the twin threats of sand and corrosion, downhole monitoring provides operators with increased insight and control over their reservoir operations and improved production. The same is the case with production logging tools run in completed wells to analyze fluids in or around the borehole during production or injection.
Yet, just as permanent downhole monitoring and production logging technologies have advanced, so have the demands that are put on them.
Such demands include the rise in deviated and horizontal wells, leading to multiple zones, complex flow regimes and downhole measurement challenges. These are ever more remote and challenging conditions, particularly with the rise in deeper wells and the growth in intelligent completions and smart wells that provide the potential for real-time zonal downhole monitoring of pressures
and temperatures.
Accessing the reservoir
Given all these advances and growing demands, it is therefore surprising that the sandface—the physical interface between formation and wellbore—and the lower completion is considered off limits when it comes to sourcing accurate, multizone information.
This can lead to expensive but suboptimal well and reservoir management with typical outcomes including flowing a well from only a short section of the sandface or selecting the wrong remedial action when faced with poor well performance.
The upper completion is the connection from the lower completion to the wellhead and includes the tubing and all other accessories that allow the well to flow. The lower completion interacts with the formation that the operator produces from and is usually finished with a packer at the top to isolate the lower completion from the wellbore.
Yet, the large majority of downhole monitoring equipment is installed above the production packer and is thus unable to monitor the dynamic changes in the reservoir and data from the lower completion.
In deeper wells, there are also the challenges of sourcing diagnostic data from the lower completion. In Figure 1, for example, the Roxar HS gauge is set at a depth of about 4,000 m (13,123 ft) but is still 1,500 m (4,921 ft) above the reservoir. While 4,000 m is certainly better than taking pressure measurements at the wellhead, there are still likely to be errors in the correction from density variations, such as gas bubbles or slugs, and from friction, turbulence and other factors.

In addition, the lack of downhole data is often exacerbated in horizontal and multilateral wells with multiple zones, where the horizontal part in the reservoir can be more than 3,000 m (9,842 ft) and the wellbore as long as 12 km (7.5 miles). In such cases, the actual downhole measurements are usually made some distance away and need to be corrected.
The result is that the lower completion is simply considered too costly and too complex for online monitoring. Traditional production logging, wireline, coiled tubing (CT) and other cable-based downhole solutions also are considered inappropriate and too risky. This is particularly the case in deviated and horizontal wells with stratified, multiphase flow where the data generated from such tools aren’t always reliable.
Bridging the information gap
The times are changing, however, with advances in downhole monitoring and wireless communication that can significantly reduce the complexity and costs associated with wired solutions, as well as open up areas previously considered inaccessible and help bridge the information gap.
One such example is the recently launched Intelligent Multistage Completion Network (IMCN), developed by Emerson in partnership with Metrol. The IMCN is the first wireless-enabled, integrated upper and lower completions downhole solution that communicates with instruments at the reservoir sandface via a new wireless interface (Figure 2).
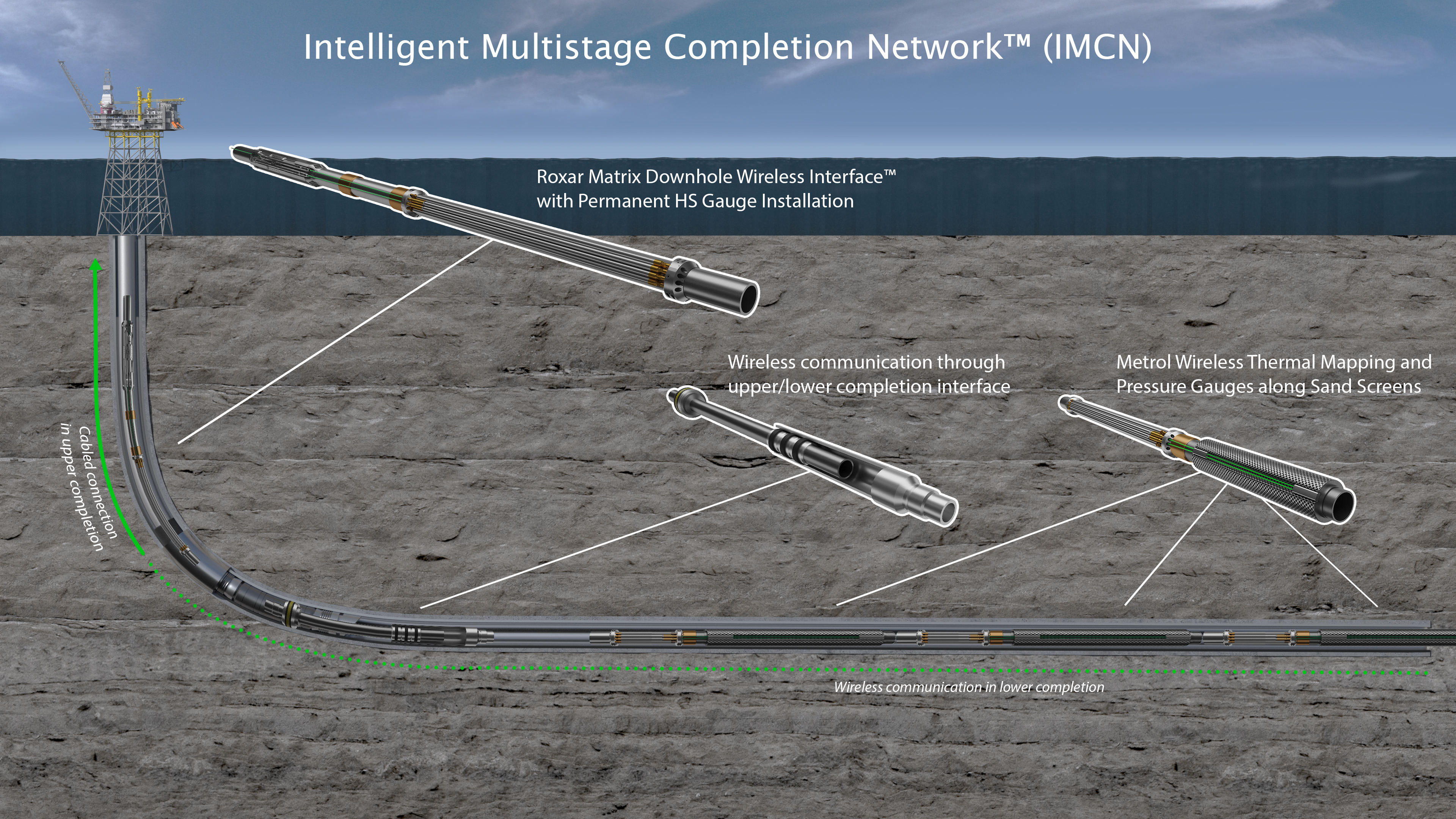
That interface—Emerson’s Roxar Matrix Downhole Wireless Interface built on wireless telemetry advances in which acoustic signals are sent through the tubing string—enables the operator to align the cabled permanent downhole gauges in the upper completion with the wireless sensors and controls along the reservoir sandface. This leads to insight into the reservoir’s flow and valuable, previously inaccessible data.
Installation of the system requires no need for additional penetrators (e.g., wet mates, connectors or tubing for fiber) to go through the defined well barriers, thereby significantly reducing risk. There are also no additional hardware requirements to the topside or subsea control system. Instead, operators have a single standard interface card providing access to all the in-well instrumentation.
What operators can expect
Operators can expect detailed reservoir data and control, an improved understanding of well performance issues, and the ability to select the correct types of intervention. No longer will operators have to make do without having diagnostic data from the lower completion. There is also no longer a need to consider costly and risky production logging, wireline, CT and other cable-based downhole solutions.
They can look forward to the wireless retrieval of pressure and temperature data from reservoir sands in a pilot hole for the first time, leading to an improved understanding of reservoir connectivity and drainage.
Operators also can access zonal flow data measurements without having to reduce flow rates; this is because operators also will have the added ability of wirelessly operating flow control valves in multiple locations in response to zonal data acquisition.
In addition, they can utilize reservoir and flow information to optimize their reservoir production operations.
An intelligent completion involves understanding formation behavior, diagnosing data in real time and understanding and wirelessly managing multizonal contributions without the need for packer penetrations or wired connectors, and without intervention, a goal which the IMCN helps achieve.
Recommended Reading
NOV Announces $1B Repurchase Program, Ups Dividend
2024-04-26 - NOV expects to increase its quarterly cash dividend on its common stock by 50% to $0.075 per share from $0.05 per share.
Repsol to Drop Marcellus Rig in June
2024-04-26 - Spain’s Repsol plans to drop its Marcellus Shale rig in June and reduce capex in the play due to the current U.S. gas price environment, CEO Josu Jon Imaz told analysts during a quarterly webcast.
US Drillers Cut Most Oil Rigs in a Week Since November
2024-04-26 - The number of oil rigs fell by five to 506 this week, while gas rigs fell by one to 105, their lowest since December 2021.
CNX, Appalachia Peers Defer Completions as NatGas Prices Languish
2024-04-25 - Henry Hub blues: CNX Resources and other Appalachia producers are slashing production and deferring well completions as natural gas spot prices hover near record lows.
Chevron’s Tengiz Oil Field Operations Start Up in Kazakhstan
2024-04-25 - The final phase of Chevron’s project will produce about 260,000 bbl/d.