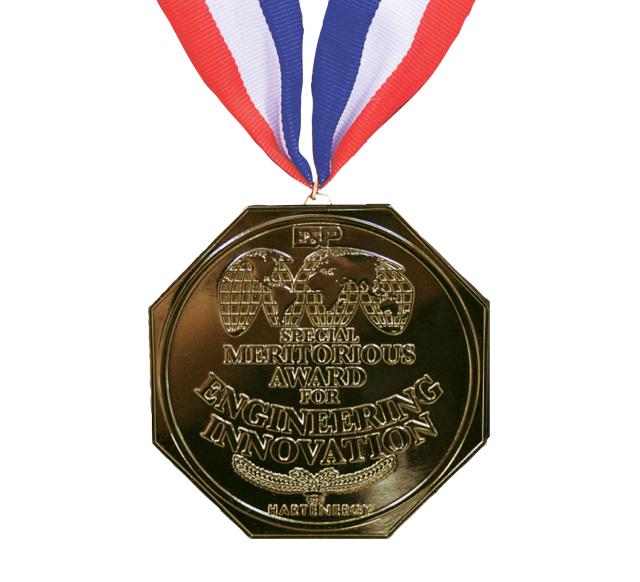
The E&P editors and staff proudly present the winners of the 2019 Special Meritorious Awards for Engineering Innovation, which recognize service and operating companies for excellence and achievement in every segment of the upstream petroleum industry. The following highlights 18 winners, picked by an independent team of judges.
The winning technologies represent a broad range of disciplines and address a number of challenges that pose roadblocks to efficient operations. Winners of each category are products that provided monumental changes in their sectors and represented techniques and technologies that are most likely to improve artificial lift, drillbits, drilling fluids/stimulation, drilling systems, exploration/geoscience, formation evaluation, HSE, hydraulic fracturing/pressure pumping, intelligent systems and components, IOR/EOR/remediation, marine construction and decommissioning, nonfracturing completions, onshore rigs, subsea systems and water management.
This year some of the brightest minds in the industry from service and operating companies entered exceptionally innovative products and technologies that have now been measured against the world’s best to be distinguished as the most groundbreaking in concept, design and application.
The awards program recognizes new products and technologies designed by companies and people who understand the need for newer, better and constantly changing technological innovation to appease the energy-hungry world.
The panel of judges comprised experts in business, engineering and the sciences representing operating and consulting companies worldwide. Each judge was assigned a category that best utilized his or her area of expertise. Judges whose companies have a business interest were excluded from participation.
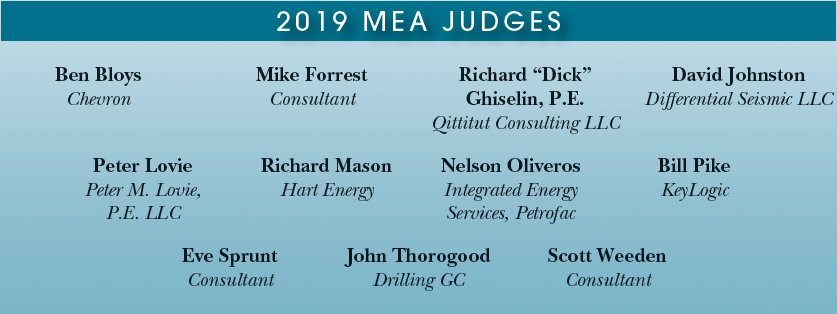
E&P would like to thank these distinguished judges for their efforts in selecting the winners in this year’s competition.
As in past years, E&P will present the 2019 awards at the Offshore Technology Conference in Houston. (UPDATE: To view the photos, click here.)
An entry form for the 2020 Special Meritorious Awards for Engineering Innovation competition is available at HartEnergy.com/mea. The deadline for entries is Jan. 31, 2020.
ARTIFICIAL LIFT WINNER
AccessESP | RIGLESS WIRELINE RETRIEVABLE ESP
AccessESP’s wireline retrievable electric submersible pump (ESP) system reduces the impact of deferred production and rig cost. A permanent magnet motor and a side pocket wet connect system were integrated to allow slickline/wireline ESP retrieval on a live well. The design also allows fullbore access to the lower completion when the ESP is retrieved. The goal is to integrate these technologies into a simplified rigless conveyance system that reduces HSE exposure and risks, reduces opex and offers cost-effective production optimization. Traditionally, when an ESP performance deteriorates or fails, or when an operator needs to access the lower completion for well repair or remediation, the only option is to pull the entire tubing string to surface, sometimes in remote or offshore operations with intervention costs ranging from $3 million to $15 million. There is often an opportunity cost associated with production downtime or well damage from kill fluid. HSE risks are associated with heavy workover operations. Many of these costs and risks can be eliminated when using wireline retrievable ESP. AccessESP systems mitigate these challenges, providing an alternative for well completion and ESP conveyance that allows ESPs to be changed out without a rig, on a live well and with reduced surface equipment.
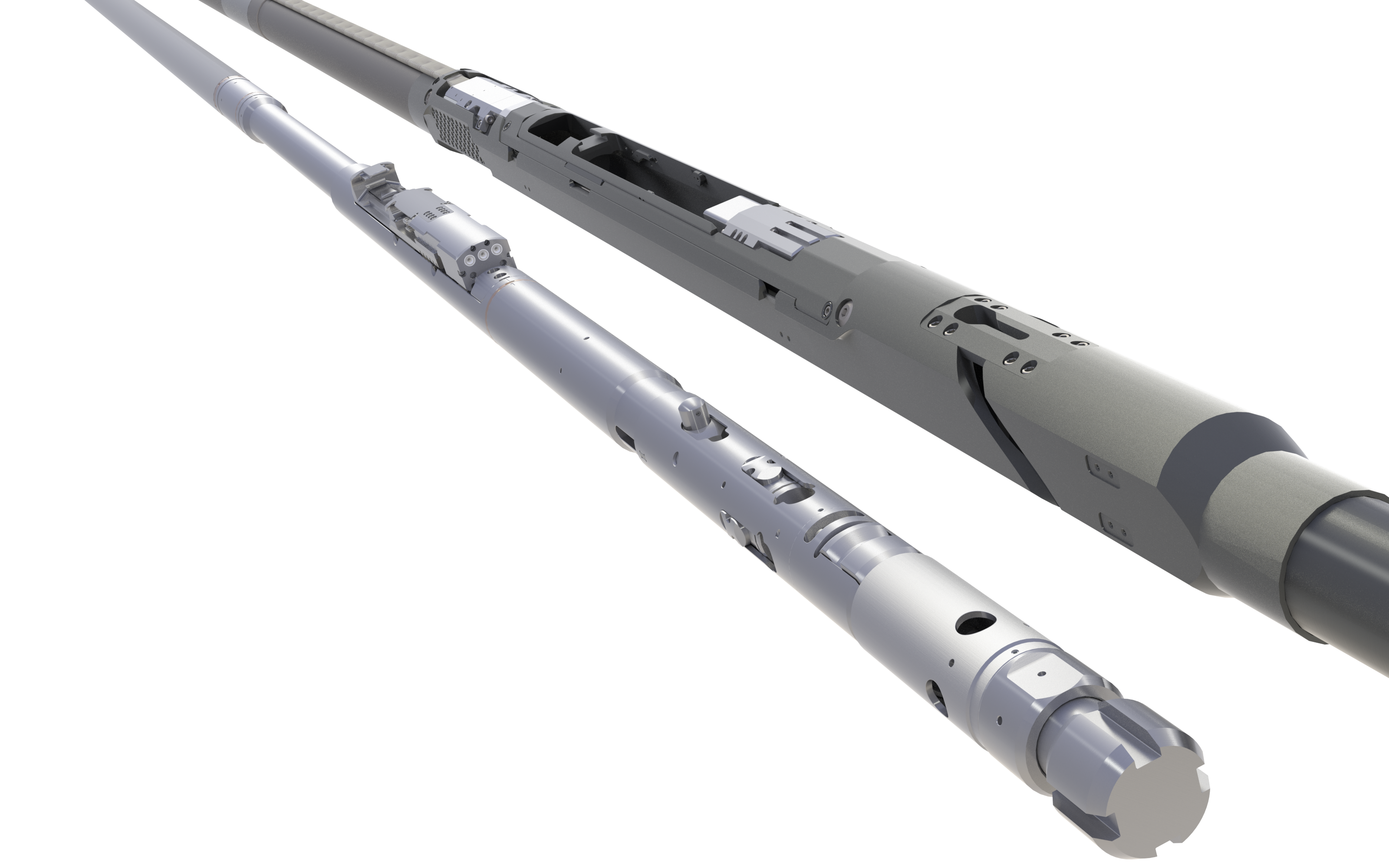
DRILLBITS WINNER
BAKER HUGHES, A GE COMPANY | DYNAMUS PDC DRILLBIT WITH ANTIWALK TECHNOLOGY
Downhole forces can cause inclination and azimuth deviations in the lateral sections of horizontal wells. When an adjustable kickoff motor assembly fails to track straight, rotation must be stopped to execute a slide and correct trajectory. Trajectory corrections slow drilling and cause tortuosity and undulations along the well path. The Dynamus drillbit technology from Baker Hughes, a GE company (BHGE), incorporates design elements such as StayTrue shaped inserts for enhanced stability, wear-resistant Optimus cutters for extended life, a SweepBlade layout for ROP performance and a new matrix material body with high-torque shank. Each of these components plays a vital role in drilling smoother, straighter and longer laterals in less time and at less cost. In addition, Dynamus bits feature an AntiWalk gauge pad configuration that regulates side-cutting response using lateral depth-of-cut control. The engineered gauge pad optimizes tracking to hold azimuth and inclination with reduced dogleg severity under random lower-level lateral forces, yet it does not hamper lateral aggressiveness while steering or building curve. The AntiWalk configuration essentially enables that bit’s side-cutting response to adjust to changes in the outside lateral forces acting on the bit for consistently smooth, on-target drilling with less tortuosity.
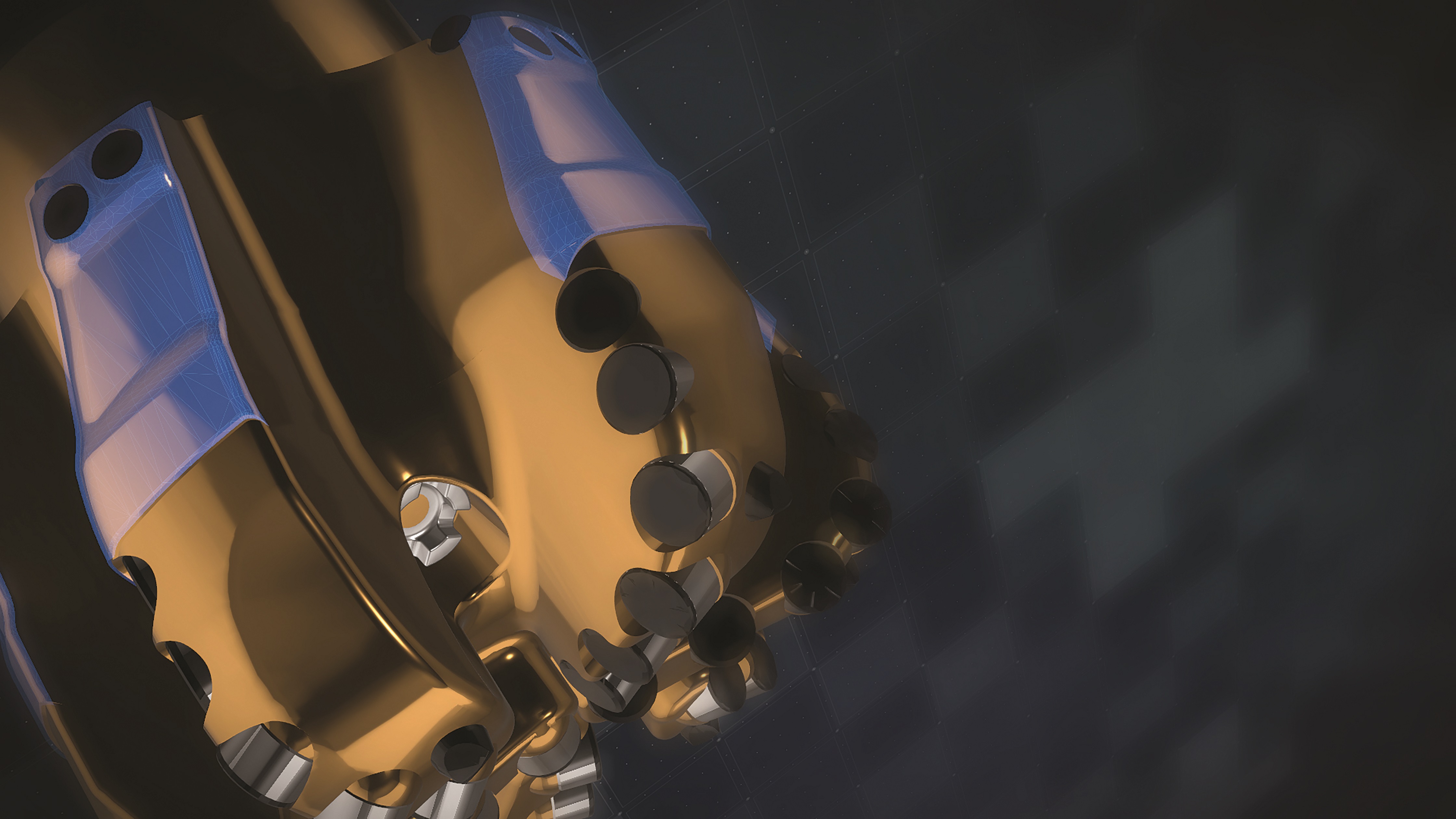
DRILLBITS WINNER
ULTERRA | SPLITBLADE PDC BIT
Poor cuttings evacuation from the toolface of the drillbit has long been known to limit ROP. When traditional drillbit designs leave cuttings trapped on the toolface, collecting around the cutters and junk slots, drilling energy is wasted, toolface control is compromised and the bit can be damaged as result of rising temperatures. Ulterra’s SplitBlade PDC drillbit design was developed to address the problem of poor cuttings evacuation. With its unique split blade geometry and double-barrel hydraulics, SplitBlade has enabled operators to achieve dramatically improved ROP, durability and directional control. The drillbit’s primary blades separate past the cone, creating large-volume flow channels for cuttings evacuation. Vectored nozzles create a double-barrel hydraulics effect, dramatically boosting the maximum cuttings dispersal rate. This design channels more fluid directly onto the cutters, continually sweeping the junk slots and causing cuttings to be cleared from the cone up to seven times faster than conventional PDC drillbits. This improved cleaning allows the bit face to engage and fracture rock unimpeded, increasing ROP. The hydraulics of SplitBlade keep cutters cleaner, lowering residual heat, reducing thermal damage and increasing bit performance and longevity.
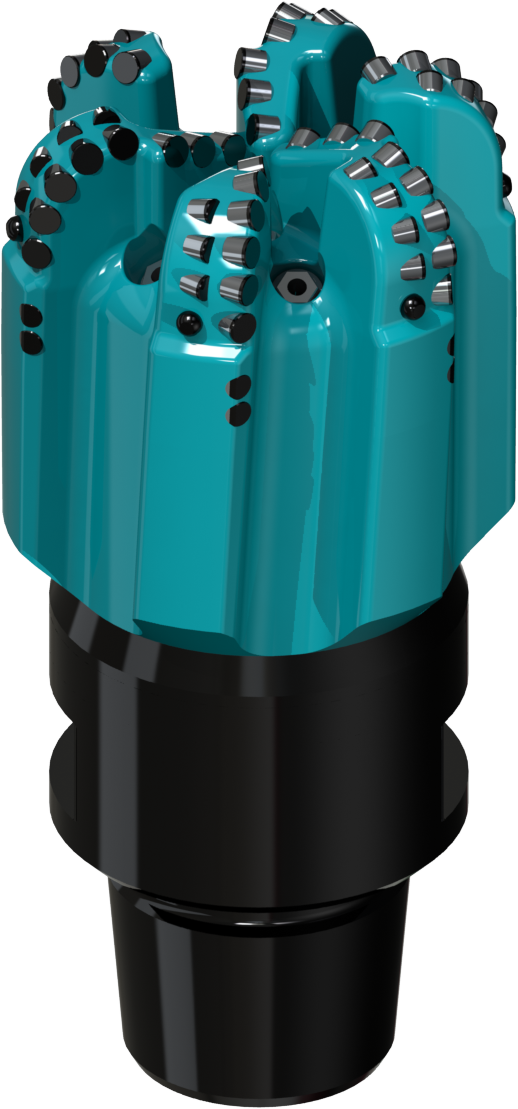
DRILLING FLUIDS/STIMULATION WINNER
BAKER HUGHES, A GE COMPANY | MAX-LOCK LOST CIRCULATION MATERIAL
Drilling fluid losses to the formation are often an expensive and all-too-frequent problem for oil and gas operators, leading to nonproductive rig time, additional well costs and heightened operational and HSE risks. By one estimate, the industry spends $2 billion annually to mitigate fluid losses, including pumping lost circulation materials (LCMs) such as calcium carbonate, cellulosic plant fibers and crosslink polymers. MAX-LOCK from Baker Hughes, a GE company (BHGE), is a step-change system for one of the industry’s oldest and costliest challenges. The magnesia-based LCM is a phase-transformation technology that exhibits thixotropic behavior during pumping and spotting. Once in place, the LCM will solidify into an acid soluble plug, which can be remediated later if needed. The thixotropic shear thinning fluid is easily mixed on site and pumped through the drillpipe. As MAX-LOCK enters formation voids and fractures, its viscoelastic properties thicken as its flow rate diminishes, building a gel structure that enables the LCM to effectively bridge the loss zone. Upon curing, it hardens into a high-compressive strength, nonporous plug that solidifies thief zones to enable drilling to resume. It is customizable so setting times can be formulated to match temperature, density and other application-specific variables.
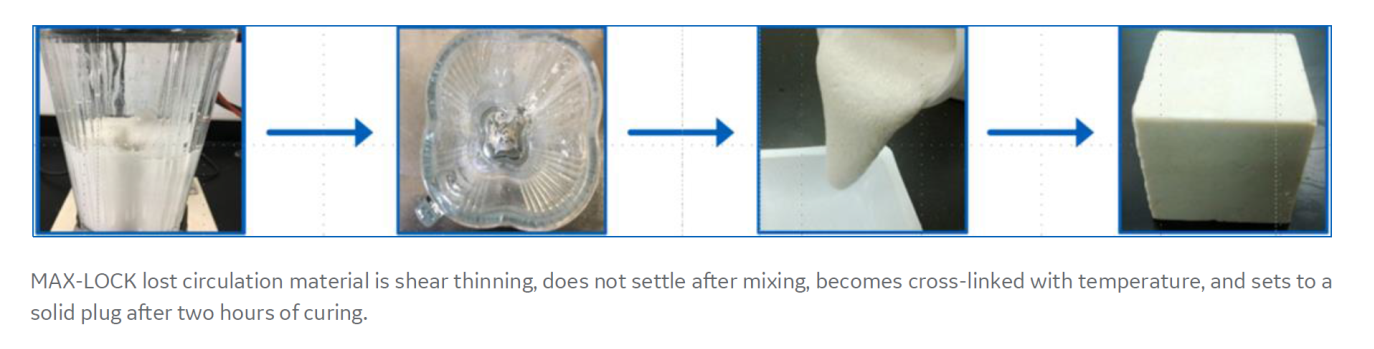
DRILLING FLUIDS/STIMULATION WINNER
M-I SWACO, A SCHLUMBERGER COMPANY | MEGADRIVE EMULSIFIER PACKAGE
When standard invert-emulsion systems are reused multiple times, low-gravity solids buildup can cause progressive gel strengths. As the cost of base oil continues to increase, the required dilution results in higher overall cost per barrel of nonaqueous fluids. Most oil-based systems are reliably and thermally stable, but many typically exhibit elevated, and sometimes severe, progressive gel strengths as drilling progresses. In recognition of this problematic trend in elevated gel-strength oil-based fluid applications, M-I SWACO, a Schlumberger company, has developed the MEGADRIVE emulsifier package. This new drilling fluid system delivers the durable and temperature-stable invert-emulsion fluid operators have requested, without the associated elevated gel strengths. In addition, this fluid withstands high-solids loading, enables lower HP/HT filtrate values and delivers high tolerance to seawater and cement contamination. The MEGADRIVE package uses the MEGADRIVE P primary high-performance emulsifier as well as MEGADRIVE S secondary high-performance emulsifier and coating agent to synergistically provide good emulsion stability with low filtrate. This MEGADRIVE package is designed to improve overall drilling performance of oil-based muds, potentially saving operators hundreds of thousands of dollars per pad.
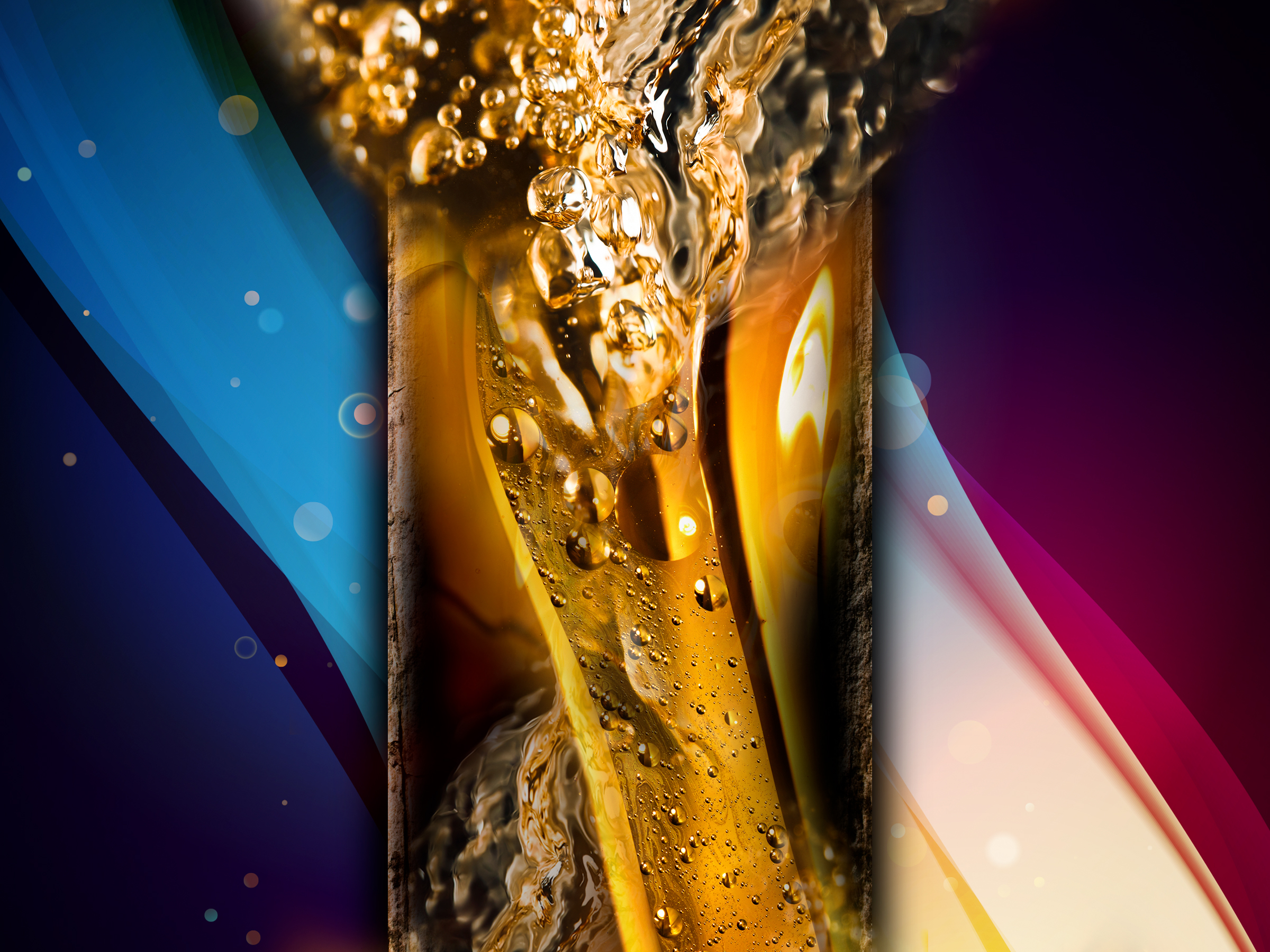
DRILLING SYSTEMS WINNER
AFGLOBAL | ACTIVE CONTROL DEVICE (ACD)
AFGlobal’s Active Control Device (ACD) for deepwater managed pressure drilling (MPD) seals and diverts annular wellbore returns using a nonrotating technology enabled by an actively pressurized sealing element. According to AFGlobal, the ACD system is the industry’s first active, nonrotating sealing device for MPD operations. MPD methods are broadly used to address many offshore operational and safety challenges. Sealing and diverting annular returns are critical to these operations. The ACD replaces the decades-old rotating control device (RCD) technology with a design that eliminates major sources of wear, maintenance and risk. In doing so, it improves economics and the application of MPD. Active control of the primary sealing mechanism independent of wellbore pressure contrasts with conventional RCD sealing mechanisms based on an interference fit. The active control ensures sealing integrity over the element’s full life cycle and enables monitoring and condition-based maintenance that improves efficiency and safety. The ACD transforms how deepwater MPD operations seal and divert annular flow. Its advanced design and new capabilities to monitor and control greatly reduce wear, maintenance and risk in this critical task. The ACD system has been designed so that catastrophic failure of the elements will not occur. The condition-based monitoring system included with the unit allows the operator to fully understand seal state with an estimated percentage of seal life remaining.
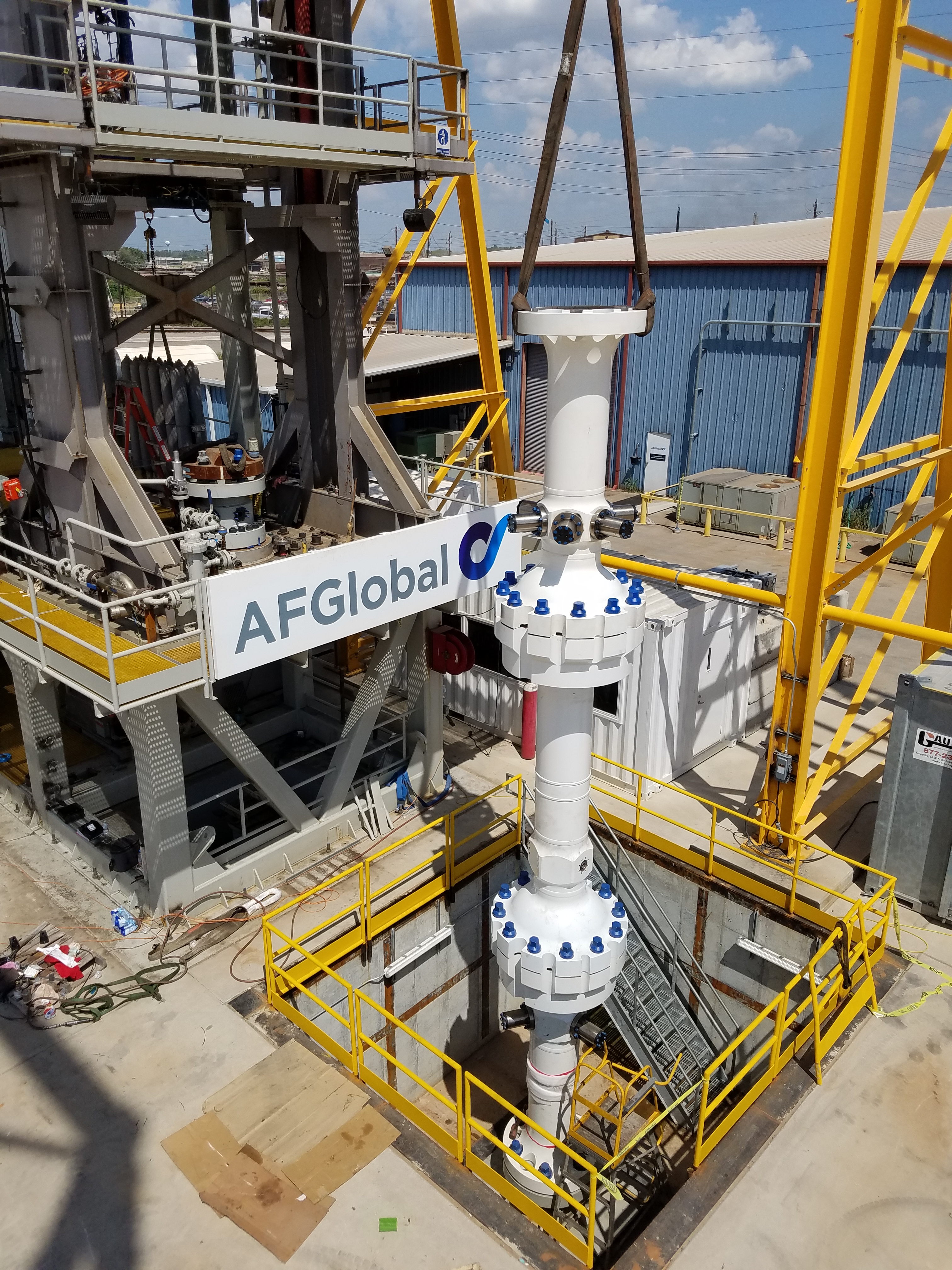
EXPLORATION/GEOSCIENCE WINNER
EMERSON | ROCK TYPE CLASSIFICATION WITH MACHINE LEARNING
Emerson E&P has developed a supervised machine learning approach called Democratic Neural Network Association (DNNA). The method reconciles multiple datasets to predict facies away from the wellbore. It employs an ensemble of many neural networks running in parallel that simultaneously learn from the multiresolution wellbore and seismic data using different strategies and associations. This architecture minimizes the possibility of biasing. It includes a secondary training stage where seismic data are introduced away from the wellbore and voted on for training set inclusion to stabilize network training while preventing overlearning. The outcome of this process is a probabilistic facies model description of the reservoir. It predicts the most probable facies distribution and associated maximum probability as well as the probability relative to each facies. This results in less guesswork when quantifying uncertainty in rock type distribution. Results are interactively generated in a 2-D and 3-D environment for in-depth analysis and are reservoir simulation ready. The outcome is critical for reservoir geologists and engineers to better understand reservoir behavior. Once considered nice-to-have technologies, the sheer volume of well and seismic data that need to be analyzed has made machine learning an effective approach for transformation and analysis of subsurface data. Automated machine learning produces outputs in minutes or hours rather than months or years. DNNA provides a practical approach to invert directly for the desired model facies resolution and heterogeneity, including fluid overprint. The method has been demonstrated to predict lithozones in both conventional and unconventional reservoirs.
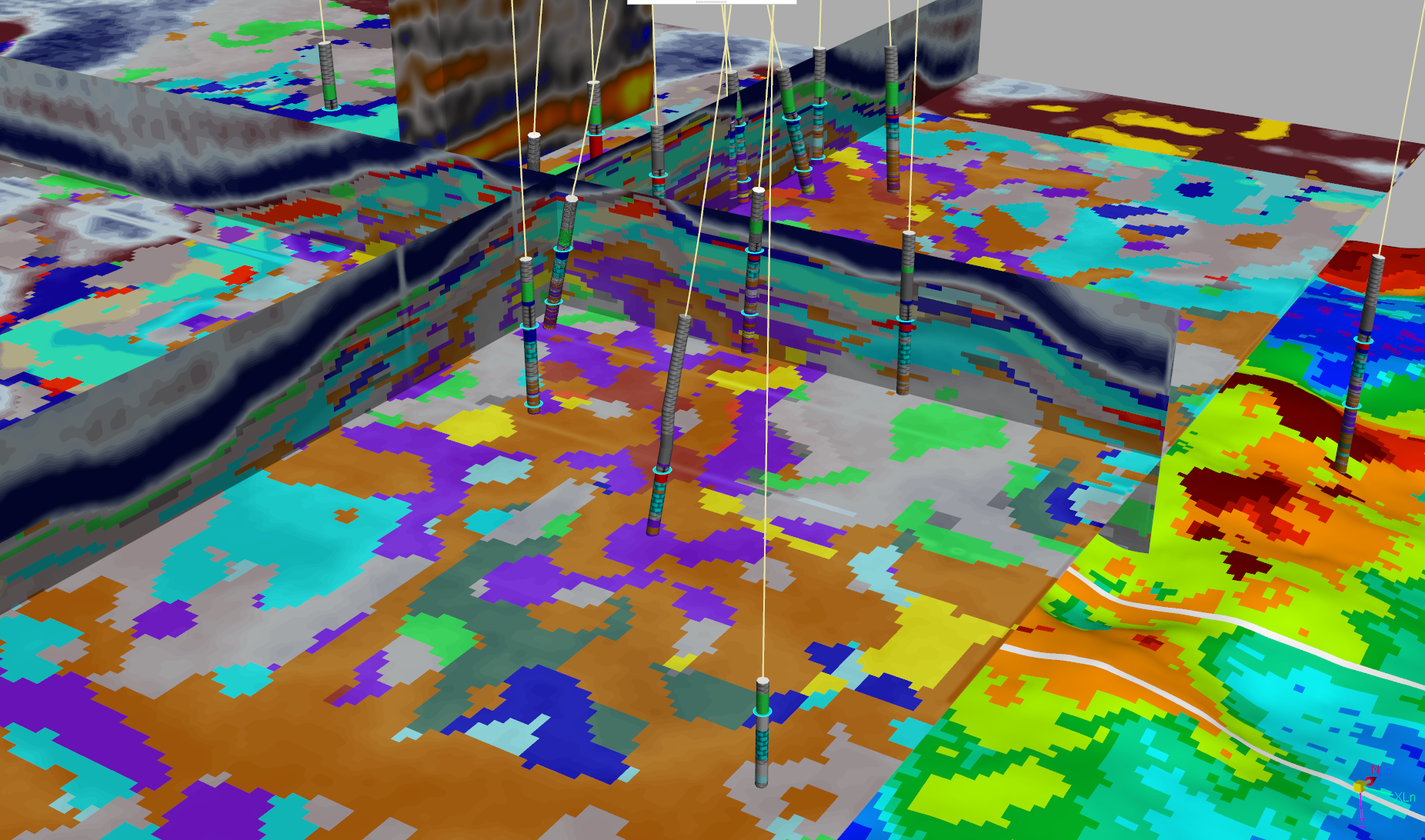
FORMATION EVALUATION WINNER
SCHLUMBERGER | CONCERT WELL TESTING LIVE PERFORMANCE
Concert well testing live performance from Schlumberger improves operational efficiency, optimizes HSE for both personnel and environment, and obtains high-quality data from surface and downhole to prove reservoir potential while empowering operators to achieve actionable test results. The Concert ecosystem digitally and autonomously acquires data from downhole tools, surface sensors and video, and it seamlessly makes data available with analytical capabilities to all testing team members and the operator wherever they designate so they can perform the well test as one team. The access and collaboration afforded by digital integration revolutionizes wellsite efficiency, informs timely decision-making, improves fluid-handling safety and mitigates environmental impact. Sensors and cameras are deployed across all surface test operations for data acquisition, monitoring and analysis via rugged tablets and wearable technology. Robust software drives web dashboards and video displays to tablets and wherever operators specify, with everyone viewing the same data, diagnostics and analysis. Concurrent analysis and advanced diagnostics refine the scope of work and predict operational events or raise an alarm when needed. Test efficiency and HSE improvements come from automated data acquisition eliminating exposure to manual sampling and monitoring. The integrated video cameras continuously monitor burner combustion to enable 24/7 surveillance for fallout, emissions and deluge water curtain without physically stationing personnel in visual monitoring proximity that subjects them to extreme heat radiation.
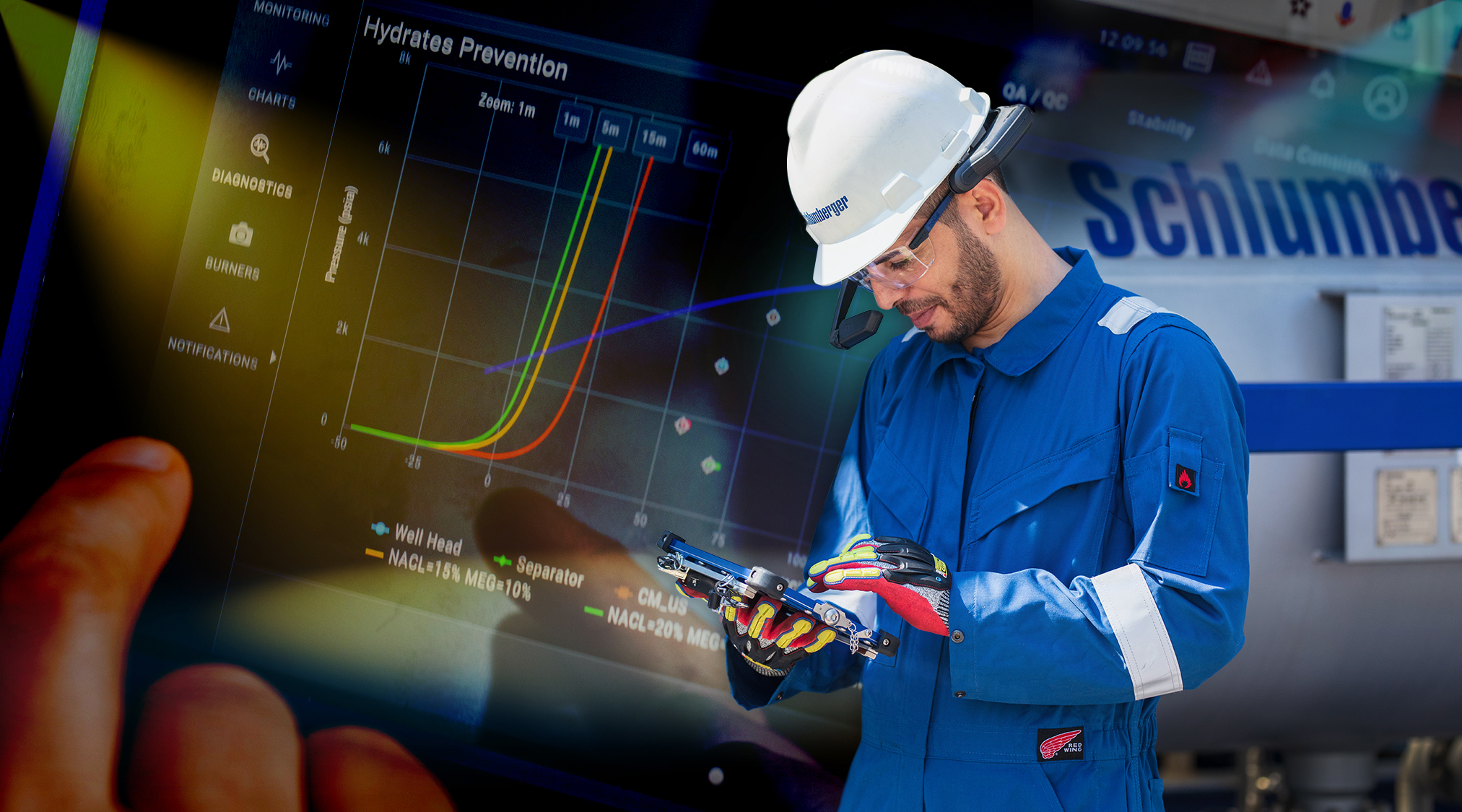
HSE WINNER
ION GEOPHYSICAL | MARLIN SMARTER MANAGEMENT OF MARINE OPERATIONS
Marlin ensures safety while reducing operational downtime in congested offshore theaters by giving all parties working in proximity full situational awareness of the planned activities of every other asset in the area. Marlin is the only commercially available marine intelligence platform that combines temporal project planning with 3-D situational awareness, analyzing and predicting operations using multiple real-time information sources like AIS, GIS and MetOcean data. Planned operations are combined with this live positioning data to flag potential conflicts based on operational objectives and HSE policies. This continuous assessment of operations reduces risks to safety and cost management, minimizing vessel and crew downtime due to scheduling conflicts. Gantt charts provide clear temporal visualization of operations in the area, with visual maps providing a real-time view of actual asset activities. All data are recorded over the course of a program so that operators can play back operations at a later date to investigate incidents or identify opportunities to improve SIMOPS performance in the future.
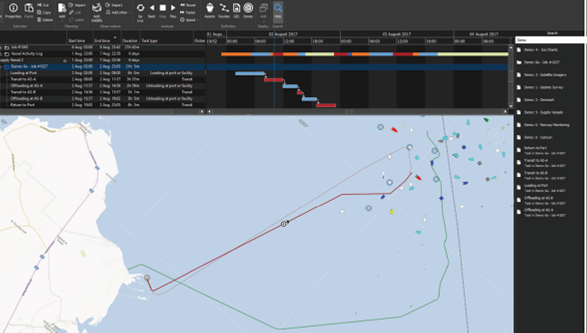
HYDRAULIC FRACTURING/PRESSURE PUMPING WINNER
AFGLOBAL | DURASTIM PUMP
The DuraStim hydraulic fracturing pump developed by AFGlobal offers far-reaching gains in frac pump performance and the execution of hydraulic fracturing treatments. Its advantages for high-pressure, continuous duty operation extend to offshore pumping applications. According to AFGlobal, the DuraStim pump is the industry’s first fully automated, long stroke, low frequency variable displacement pump. Developed for extreme duty on multiwell completions, the 6,000-hp pump comprises six individual pump units integrated by a computerized control, synchronization and automation system that varies pump rate hydraulically. A constant speed, zero emission 6,600-volt AC motor and six hydraulic rotary pumps drive the system. Electric and turbine drives are optimized by the constant speed operation, resulting in significant gains in fuel efficiency, reduced emissions and noise. Fluid-end stress, a key source of wear with conventional pumps, is greatly reduced by the new pump’s 48-in. stroke and a low cyclic rate of 20 cycles per minute or less compared to 200 cycles per minute with conventional pumps. The pump triples the horsepower produced from the same footprint as conventional pumps, significantly reducing frac spread complexity and improving wellsite logistics and safety. Cloud-enabled predictive maintenance and built-in diagnostics enhance continuous duty operation.
INTELLIGENT SYSTEMS AND COMPONENTS WINNER
IPT GLOBAL LLC | SURETEC
IPT Global LLC created SureTec, a software suite specifically designed to address the challenges commonly experienced in digital pressure testing. The software was created as a fit-for-purpose digital alternative to properly design, plan, test, report and archive the results of all required pressure tests throughout the life cycle of a well. IPT Global focuses on addressing the pressure testing workflow with a single integrated software platform designed to be the principal system of record for all pressure testing in upstream operations. SureTec provides real-time analysis of pressure, rate and volume data with preconfigured criteria so that tests can be objectively passed or failed. The tools were designed to be intuitive and allow the user to quickly create easy-to-edit complex schematics. The planning tool was designed with industry requirements in mind and contains several safeguards that inform the user of incomplete test plans, missing testing requirements and safety concerns.
IOR/EOR/REMEDIATION WINNER
BAKER HUGHES, A GE COMPANY | FATHOM XT SUBSEA226 BLACK OIL FOAMER
As subsea fields age and wells follow their natural decline curve, they begin to exhibit liquid loading, leading to fluid slugging in the flowlines connecting wells to production facilities. While common, these issues have historically been difficult to mitigate without expensive system upgrades and deferred production. The FATHOM XT SUBSEA226 black oil foamer is an economical alternative to combatting liquid loading and fluid slugging problems, enhancing the value of subsea assets. The FATHOM XT SUBSEA226 foamer effectively reduces liquid loading in deepwater subsea wells, minimizes fluid slugging in subsea flowlines and maximizes oil and gas production. The advanced chemistry foams 25 to 40 American Petroleum Institute gravity crude oil containing up to 60% water to increase well run times, maximize production rates and reduce opex in high-cost deepwater environments. Baker Hughes, a GE company (BHGE), developed the new foamer by its FATHOM XT qualification procedures to validate reliability, deliverability and system compatibility under demanding deepwater conditions. The SUBSEA226 foamer can be added directly to the well without dilution either on a batch basis or continuous basis, depending on the severity of liquid loading and the ultimate treatment objectives.
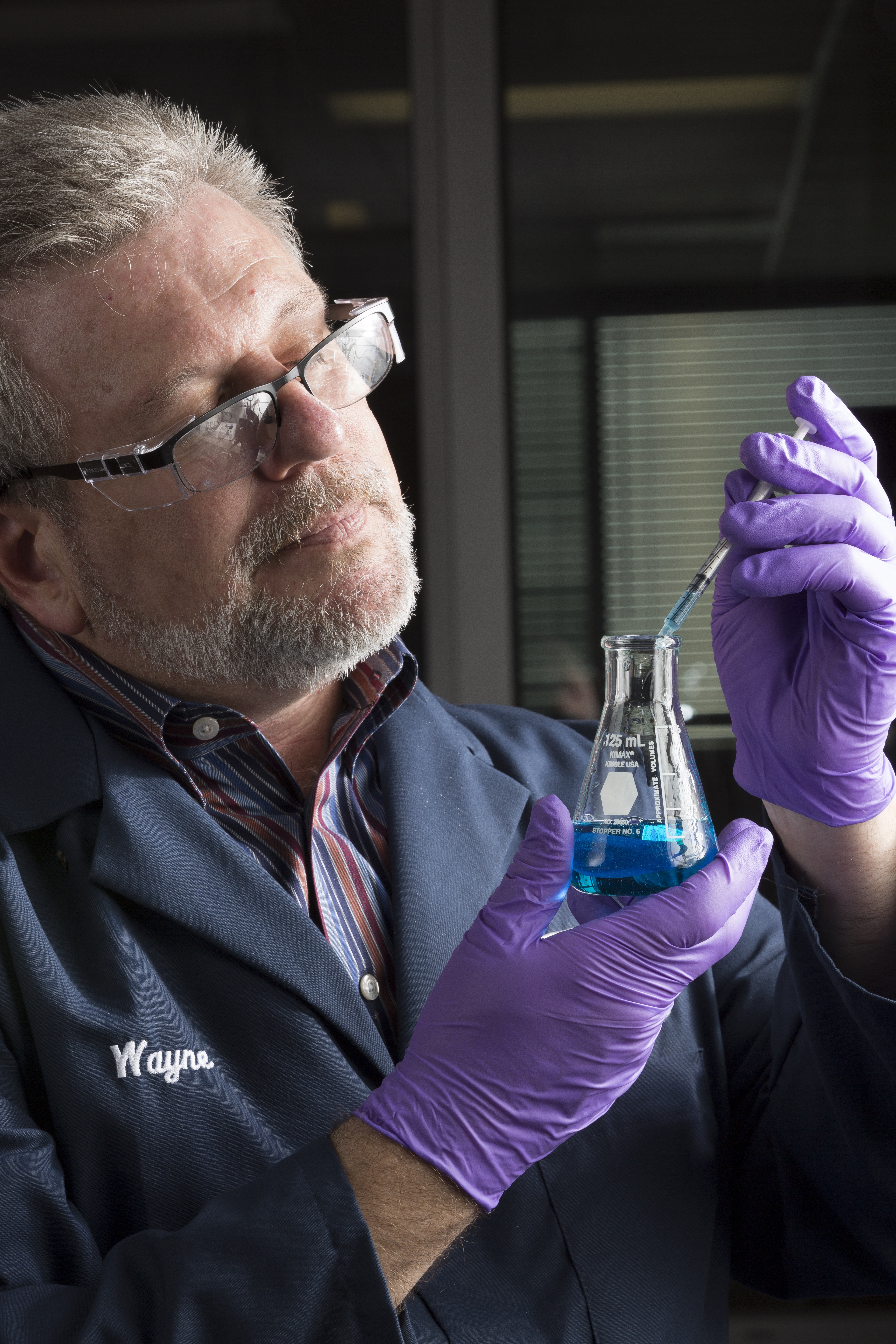
MARINE CONSTRUCTION AND DECOMMISSIONING WINNER
WEATHERFORD | MECHANICAL OUTSIDE-LATCH SINGLE-TRIP (M.O.S.T.) PLUS TOOL SYSTEM
Weatherford reinvented its subsea wellhead retrieval system by capitalizing on new technologies and redesigning components to increase cutting efficiencies. The M.O.S.T. (mechanical outside-latch single-trip) Plus tool includes a newly designed tension-cut mandrel, nonrotating flexible stabilizer (NRFS), large-diameter cutter and high-angle knives. The tool uses an advanced system that can reduce rig time by cutting and retrieving multiple cemented or uncemented strings in a single trip. The system uses custom cutting mechanism options to facilitate the most efficient cutting and recovery of subsea wellheads. These options include tension cutting with a top drive, compression cutting with a marine swivel or top drive rotary, compression cutting with a mud motor, and tension cutting with a mud motor. The M.O.S.T. Plus system confirms the cut without the need for tripping and easily latches and releases to inspect the cutting knives. It causes no damage to the internal wellhead sealing profile. The external latch mechanism helps to prevent swarf buildup by allowing more flow area in the high-pressure wellhead, which enables the cuttings to exit. The latch and unlatch also can be visually confirmed using an ROV on the seafloor. External latching also provides superior lateral support for the wellhead assembly to eliminate any lateral whipping that might impede cutting. The newly designed tension-cut mandrel enables the recovery of wellheads even where the ocean floor is at an incline. It recovers top-heavy wellheads or wellheads that protrude above the mud line, which can cause the wellhead to list and the partially cut-section to close in on the knives before the cut is fully severed. The tension-cut method can eliminate an additional run during wellhead cutting and retrieval.
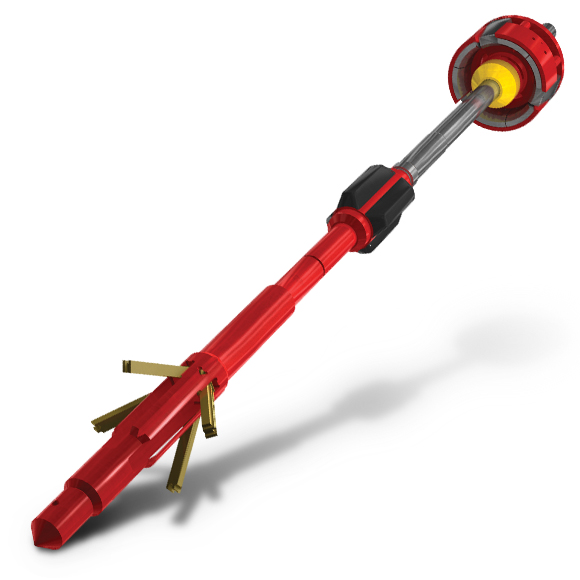
MARINE CONSTRUCTION AND DECOMMISSIONING WINNER
BAKER HUGHES, A GE COMPANY | PERSEUS PUMP-THROUGH CUTTER
Baker Hughes, a GE company (BHGE), has developed its Perseus pump-through cutter. The internal hydraulic tubular cutter is designed to cut a single string of casing as part of a plug-and-abandonment campaign, slot recovery, well intervention and other cut-and-pull operations. The tool is dressed with BHGE’s METAL MUNCHER advanced milling technology tungsten-carbide knives to cut or mill even the toughest steels. With an ability to increase mill life and penetration rates by as much as 1,000%, the carbide knives give the tool durable cutting and swarf control, while enabling more volume to be milled out in one run. Perseus is hydraulically operated and features on-demand knife activation to cut a single string of casing. When running above a mill or drillbit, the cutter remains dormant and retracted, a unique internal design that enables 100% flow through and maintains pressure integrity below the tool. This feature allows multiple operations to be performed during the same trip, including dressing a cement plug, removing scale, underreaming or milling short window sections. The cutting sequence is initiated by dropping a ball from the surface, and the three knives are activated by the flow of drilling or workover fluid through a ball catcher. When the ball lands in the catcher, the necessary pressure differential is established to activate a mandrel that moves the knives into the cutting position. The continued movement of the mandrel forces the knives to pivot around the knife pins. After a successful casing cut, the knives become fully extended and the mandrel strokes clear of the ball catcher. The fluid then flows more freely through this separation, reducing the pressure differential and signaling to the operator that the casing is fully cut. The cut casing section can then be retrieved via traditional spearing methods.
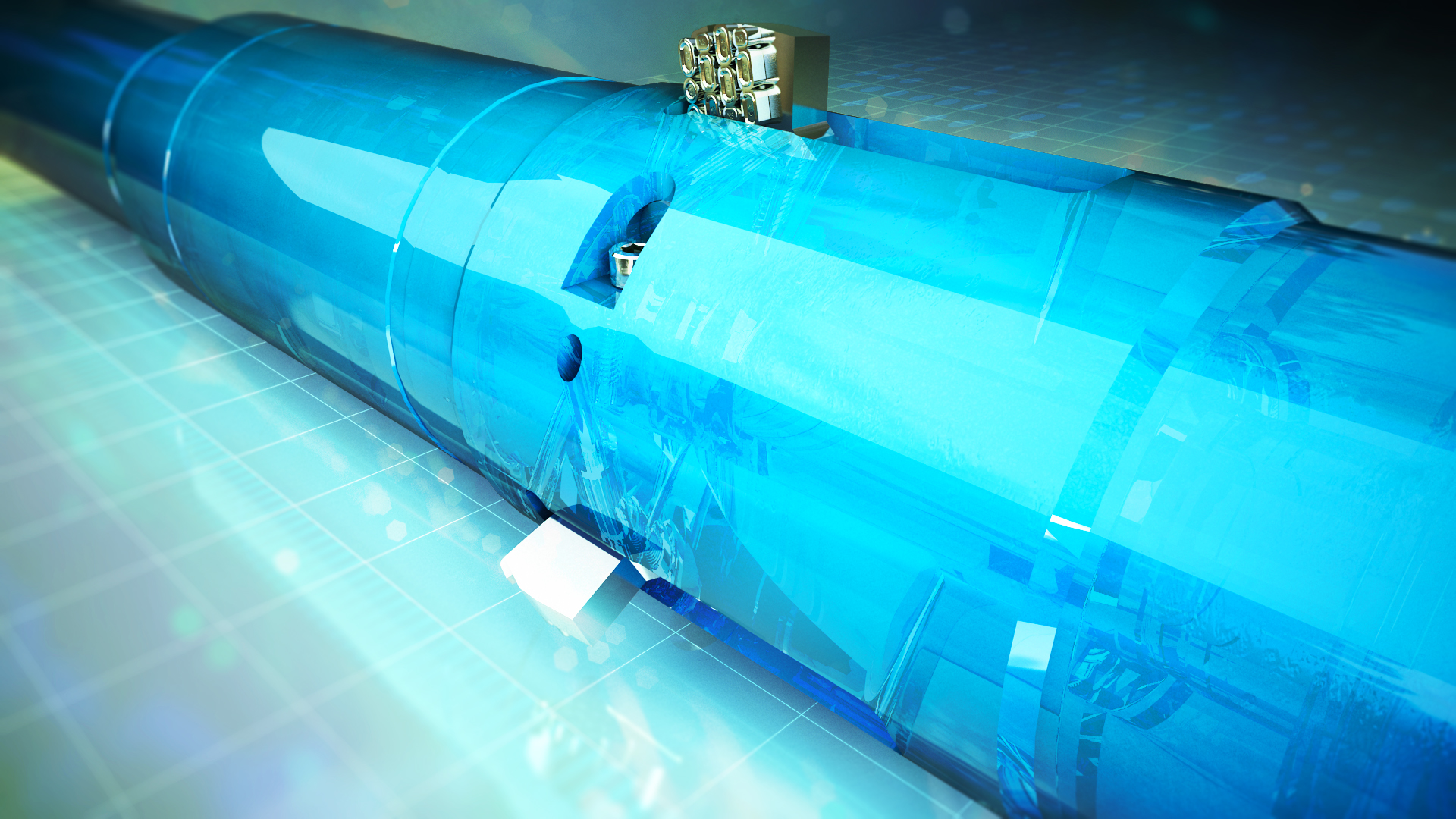
NONFRACTURING COMPLETIONS WINNER
WEATHERFORD | TR1P SINGLE-TRIP COMPLETION SYSTEM
Performing multiple operations in less time and with fewer personnel and equipment requirements sets the stage for dramatic, tangible benefits in deep water. The Weatherford TR1P single-trip completion system is a remotely activated system that enables installing both the upper and lower completion in one trip. This capability simplifies operations and reduces completion installations times by 40% to 60%, which reduces well costs by up to 25%. The TR1P system combines radio-frequency identification (RFID) technology and advanced completions tools into one system. The result is 100% interventionless operation without control lines, wash pipe, wireline, coiled tubing, wet connects and workover rigs. Before the TR1P system, many operational risks—involving well fluids management, well control, problems getting to the bottom, circulation problems and hydrocarbon influx—hampered single-trip operations to install both upper and lower completions. RFID integration provides true multicycle tool functionality throughout the completion string, which enables operators to set and test selective completion components, manage well control parameters, circulate the well from toe to heel and remotely bring the well online. RFID technology also gives operators a way to activate downhole tools without the usual mechanical limitations.
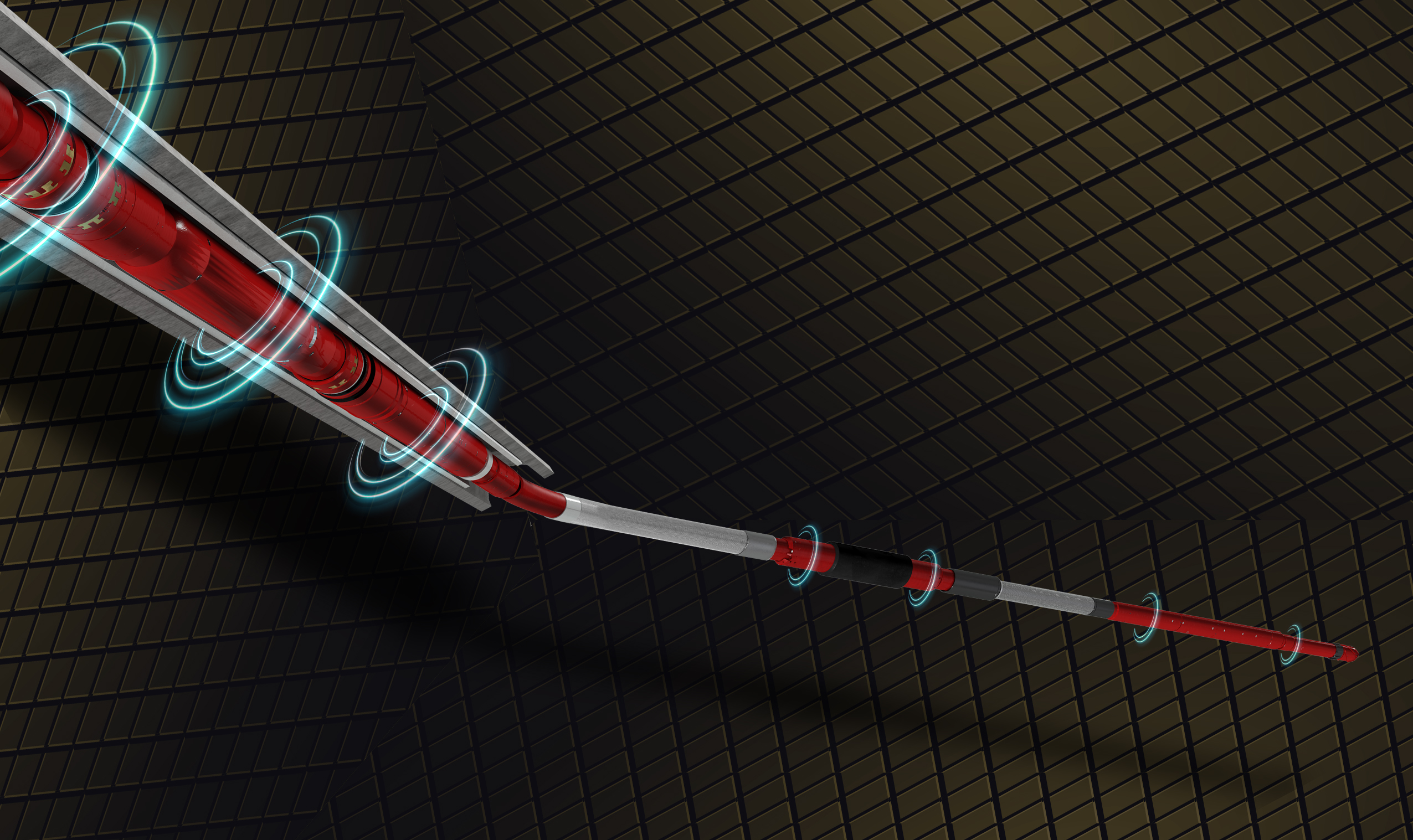
ONSHORE RIGS WINNER
FRANK’S INTERNATIONAL | COLLAR LOAD SUPPORT SYSTEM FOR STANDS (CLS-S)
The Collar Load Support System for Stands (CLS-S) of tubing is a nonmarking tubular handling
system that accommodates a wide range of pipe sizes. Unlike typical slip-type elevators and spiders, the CLS-S system allows the running of threaded and coupled stands of tubulars as well as single joints without causing damaging die penetration marks. In doing so, it eliminates the potential for corrosion cracking due to stress concentrations induced by conventional handling equipment. The risk of slip crush and iron transfer is minimized as the CLS-S system enables the tubular to be supported by the load face and not by penetration, avoiding the slippage issues prevalent on certain alloys with conventional inserts. Die and insert impressions, with or without iron transfer, may adversely affect the corrosion resistance and mechanical integrity of corrosion-resistant alloy (CRA) tubulars in conducive well environments. Although levels of susceptibility may vary, all CRA materials are susceptible to downhole corrosion mechanisms. Nonmarking technologies like the new CLS-S system are the preferred method in a safe and cost-effective approach to running stands of CRA tubulars.
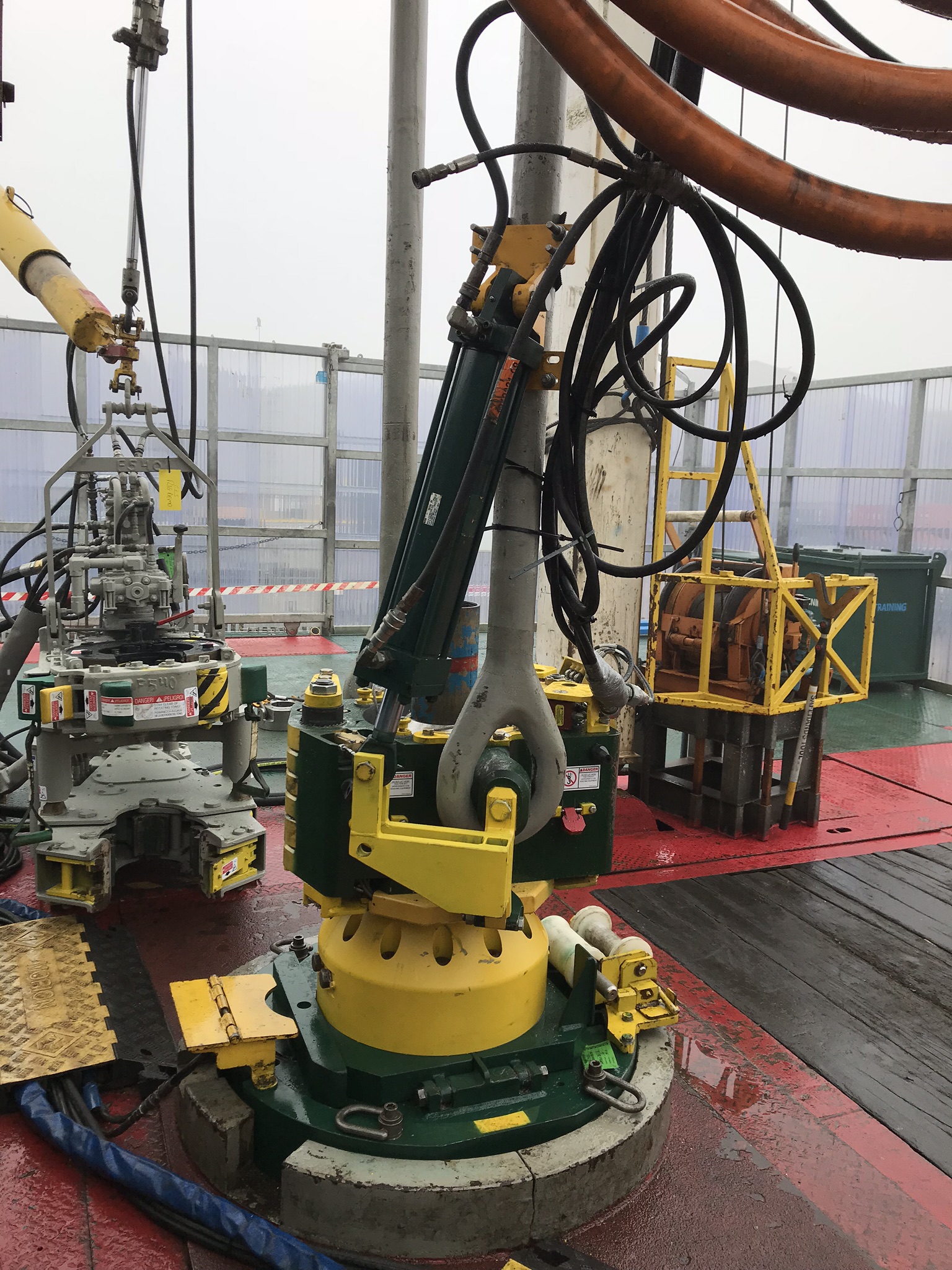
SUBSEA SYSTEMS WINNER
ONESUBSEA, A SCHLUMBERGER COMPANY | MULTIPHASE COMPRESSION SYSTEM
OneSubsea, a Schlumberger company, has developed, qualified and put into operation a multiphase compressor technology enabling boosting of unprocessed well streams. This minimal footprint, contra-rotating compressor technology is a subsea compressor concept that works at any combination of gas and liquid (0% to 100% gas volume fraction). It is a robust, yet highly efficient machine tolerating transient process conditions, such as large liquid slugs and variable process pressure. Subsea compression is used to extend plateau production, accelerate production, optimize reservoir drainage and maximize ultimate recovery. The Schlumberger multiphase compressor leverages extensive OneSubsea subsea pump system experience. Subsea boosting has accumulated more than 3 million operating hours—equivalent to 350 years—and is recognized as an important part of enhanced drainage strategies. Experience is being gained from a North Sea subsea gas field, where the robustness and versatility of the equipment have contributed to large value generation. The compressor has been used to kick off dead wells and enhance liquid recovery from the field. Its capability to handle large liquid loads (up to 100%) has been pivotal to unlocking this potential. The multiphase compressor system has operated with 100% regularity since startup and has reached Technology Readiness Level 7. A major advantage of subsea compression over topside compression is that the compressor is located closer to the reservoir; hence, the power required for the same differential pressure is less and the potential drawdown of the reservoir is larger. Subsea compression stabilizes the flow and reduces flowline pressure loss.
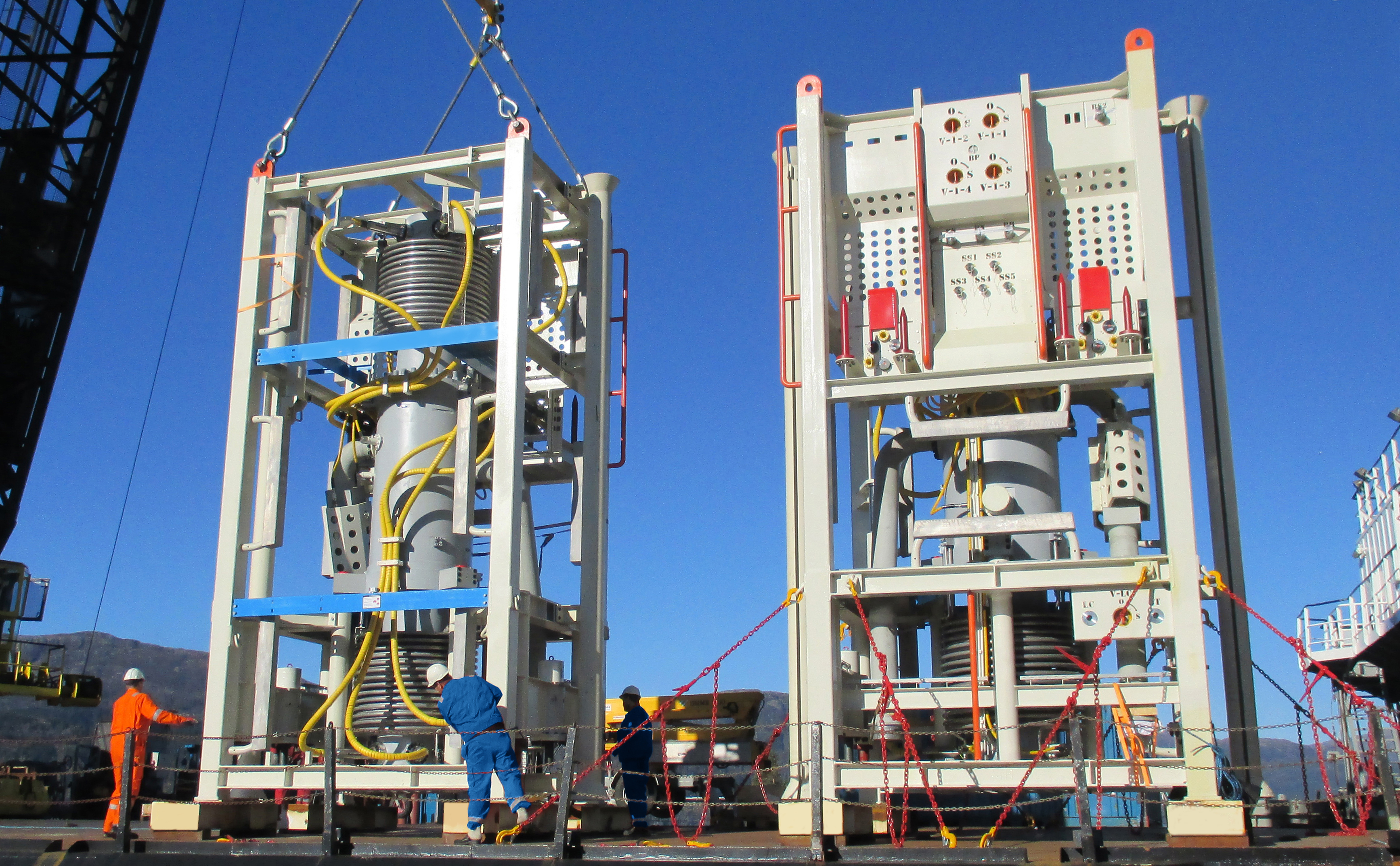
WATER MANAGEMENT WINNER
SCHLUMBERGER | AQUAWATCHER SURFACE WATER SALINITY SENSOR
The AquaWatcher Surface water salinity sensor is the latest-generation microwave sensor technology applied to continuous in-line water conductivity measurement in wet gas and multiphase (water-continuous) flow that provides real-time data output of water salinity. The sensor provides a high-accuracy, high-resolution determination of salinity across the full range of gas volume fraction to enable the detection of water property changes and identify the origin of produced water. Automating salinity determination brings several benefits to operators. It eliminates conventional manual sampling that provides only snapshots of salinity conditions and potentially exposes field personnel to H2S in the produced water. Not having to periodically deploy personnel also saves operating expenses. This mobile sensor can be installed as a standalone application upstream from the separator during well cleanup or flowback operations to monitor change in the water type for optimizing the duration of the well cleanup process. Standalone installations also are used to detect first water in extremely low concentrations. The AquaWatcher Surface sensor’s reliable detection of water droplets in the flow provides critical information for flow assurance purposes to help prevent hydrate formation and minimize the occurrence of scaling and corrosion that triggers the need to inject chemical inhibitors.
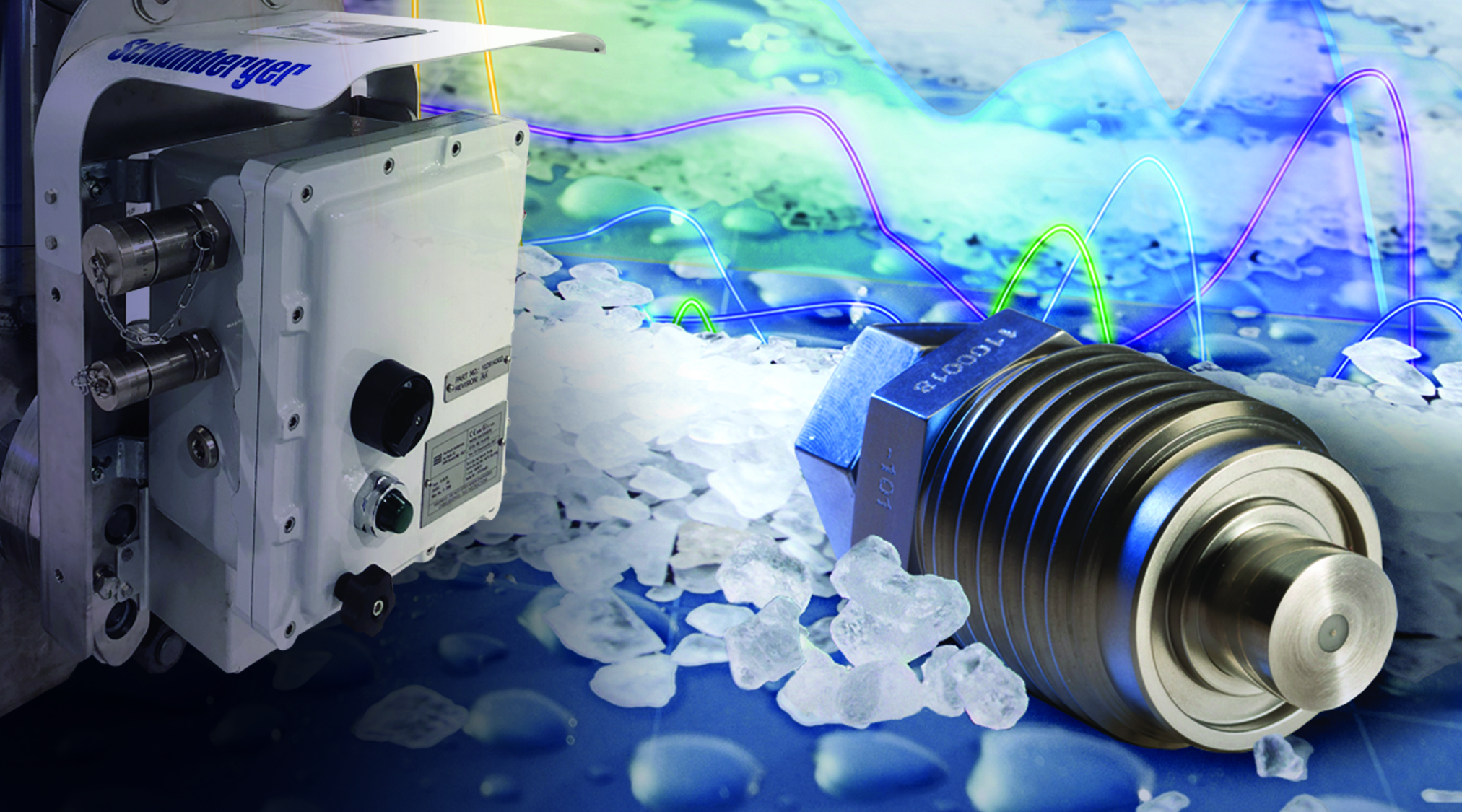
Recommended Reading
BP’s Kate Thomson Promoted to CFO, Joins Board
2024-02-05 - Before becoming BP’s interim CFO in September 2023, Kate Thomson served as senior vice president of finance for production and operations.
Magnolia Oil & Gas Hikes Quarterly Cash Dividend by 13%
2024-02-05 - Magnolia’s dividend will rise 13% to $0.13 per share, the company said.
TPG Adds Lebovitz as Head of Infrastructure for Climate Investing Platform
2024-02-07 - TPG Rise Climate was launched in 2021 to make investments across asset classes in climate solutions globally.
Air Products Sees $15B Hydrogen, Energy Transition Project Backlog
2024-02-07 - Pennsylvania-headquartered Air Products has eight hydrogen projects underway and is targeting an IRR of more than 10%.
HighPeak Energy Authorizes First Share Buyback Since Founding
2024-02-06 - Along with a $75 million share repurchase program, Midland Basin operator HighPeak Energy’s board also increased its quarterly dividend.