Presented by:
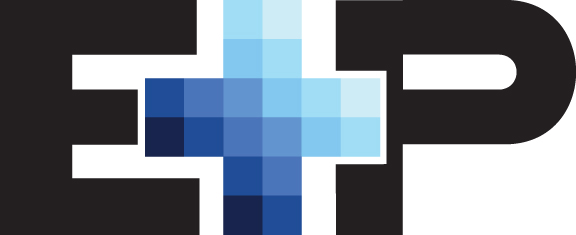
Editor's note: This article appears in the new E&P newsletter. Subscribe to the E&P newsletter here.
Over the last two decades, many offshore oil and gas activities have moved from relatively accessible shallow water to increasingly deep and ultradeep waters. Investment in fields off the Brazilian and West African coasts has driven demand for FPSO vessels, and this trend is likely to continue for the foreseeable future.
FPSOs offer several advantages compared to fixed platforms, including increased mobility, fast-track development, conversion possibilities and storage capacity. However, they often present technical challenges with regard to topsides design, engineering and construction. This is particularly the case for facilities operating in sour field developments.
In recent years, advances in the design of rotating equipment packages have helped FPSO operators meet demanding targets for capex and opex, production uptime, safety and emissions. When coupled with digitalization, producers have optimized facilities in ways that have previously not been possible.
Streamlining facility development
FPSO operators face a significant challenge in the current market environment: the need to reduce project risk and accelerate facility development cycles. Siemens Energy has seen an increasing number of offshore producers leveraging modular construction techniques to achieve these goals.
With modularization, packages for power generation, compression and/or e-houses arrive onboard as fully integrated and tested units with attributes like remote I/O and pre-flushing. Integration of packages at the factory facilitates plug-and-play installation and can significantly reduce onsite work and associated schedule interdependencies.
The success of modular strategies is often predicated on close coordination between several stakeholders, namely the EPC/fabrication yard, the original equipment manufacturer (OEM), and various subcontractors for automation, electrical and instrumentation. Consolidating the responsibilities of these parties under one single supervisory umbrella can be of significant value to operators, as it unlocks opportunities for synergies that result in schedule and cost savings, along with a reduction in overall project complexity and technical risk.
In some cases, project-specific conditions challenge the extent to which modular construction can be used. In regions like Brazil, one impediment for many suppliers has been compliance with local content requirements. To address this, Siemens Energy established a manufacturing and packaging facility in Santa Barbara d’Oeste in Sau Paulo in 2013.
The facility has played a vital role in meeting Brazilian regulations for local content and was integral in recent EPC contract awards for FPSOs. This includes modules for power generation, electrical transmission, distribution (e-houses), and gas processing and compression. Other equipment provided includes automation and control systems.
While the engineering, procurement and construction of the modules typically occur across Asia locations, packaging can occur at the Santa Barbara d’Oeste site.
PRESS RELEASE:
Siemens Energy to supply eight topside modules and support for FPSO vessel offshore South America
Addressing emissions
Once facilities become operational, operators face the challenge of optimizing performance. For FPSOs, this is highly contingent on rotating equipment packages that can efficiently deliver the horsepower to meet production, processing and compression requirements in a range of water depths and environmental conditions. At the same time, companies are under intense pressure to improve sustainability and decarbonize their operations.
OEMs like Siemens Energy have invested substantial time and resources in R&D over the past decade to make products more suitable for demanding offshore applications. One area where strides have been made is in the performance of dry low emissions (DLE) combustion systems.
Owing to their criticality, operators have historically favored reliability and fuel flexibility as the primary factors in selecting gas turbines. This has inevitably resulted in a sizeable offshore fleet of turbines with wet low emissions (WLE) systems. These units are widely recognized for reliably burning fuels over a wide range of calorific values. Still, they exhibit high levels of NOx and carbon monoxide (CO) emissions.
DLE gas turbines have been used extensively in onshore applications but (up until recently) were not typically considered for offshore applications due to concerns about their reliability. However, advancements in lean combustion technology have enabled DLE systems to perform comparably with WLE.
DLE turbines are now capable of reliably achieving more than 90% reduction in NOx and CO emissions relative to non-DLE units without compromising the high dynamic loading response of the turbines. By eliminating the need for water or steam injection, they can also lower operating costs associated with water treatment.
Siemens Energy has 100 DLE units installed offshore.
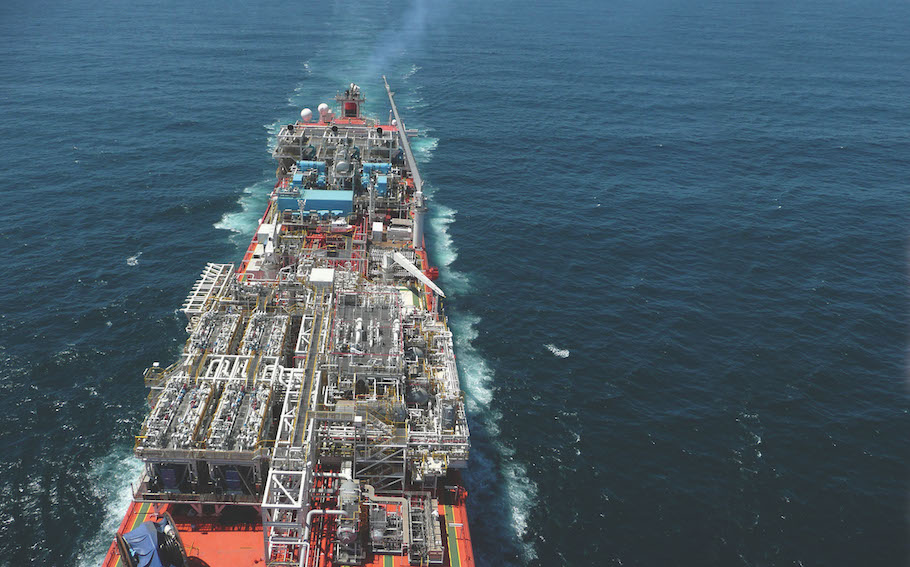
Further emissions reductions are possible by leveraging digitalization to optimize the power output of gas turbines.
Most FPSOs feature power plants with multiple gas turbines. By collecting real-time data from the turbines and analyzing it against facility power requirements, operators can run units (collectively) at an optimal set point, thereby reducing carbon emissions.
Take, for example, an FPSO with an average power demand of 80 MW being met by four 30-MW gas turbines (120 MW of total installed capacity). Determining how to supply the 80 MW for the various processes on the vessel in the most efficient manner requires consideration of multiple variables that are constantly changing, including current demand, ambient conditions and performance degradation. In this case, just a 1% increase in power plant efficiency would equate to an emissions reduction of approximately 6,500 metric tons of CO2 annually.
Extending maintenance intervals
In addition to decarbonization, FPSO operators are also placing a greater focus on extending equipment overhauls to reduce maintenance and facilitate de-manning. There are now many examples across the industry where equipment condition monitoring, in conjunction with asset performance management software and other predictive analytic tools, has enabled operators to optimize maintenance and reduce opex. The development of a digital twin as part of a holistic digital transformation strategy is becoming more accepted as well.
Another maintenance strategy that requires virtually no upfront investment is dynamic lifting.
It is common for operators to schedule service activities on their equipment using standard operating hours. In the case of gas turbines, this typically assumes that the unit will be run at 100% of its rated load in an unchanging external environment, which is never the case.
Equivalent operating hours is a metric that considers critical variables (e.g., load, temperature, fuel composition, the number of starts and stops, and emergency shutdowns) to provide a more accurate picture of the as-is condition of the unit. This allows the end user to potentially adjust the turbine's operation so the time between overhauls can be extended—ideally to a time when scheduled maintenance on the platform is set to take place.
Conclusion
The offshore industry faces several difficult hurdles in the coming years. Chief among these include the need to improve sustainability and ensure profitability in an uncertain price environment. Recent advances in equipment design, coupled with increased digitalization and proven development strategies (e.g., modularization), can go a long way in helping operators address these challenges. As is often the case, maximizing the value that these levers can deliver requires adopting a holistic approach and engagement with strategic partners from the earliest phases of the project life cycle.
RELATED CONTENT:
June 11, 2021 What's the Next Leap for Subsea Production Control Systems?
June 9, 2021 Siemens Energy to Deliver Subsea Equipment for Brazil’s Bacalhau Field
Oct. 3, 2018: IndustryVoice: Topsides 4.0 Enhances Efficiency and Reduces Costs Offshore
Recommended Reading
Keeping it Simple: Antero Stays on Profitable Course in 1Q
2024-04-26 - Bucking trend, Antero Resources posted a slight increase in natural gas production as other companies curtailed production.
NOV Announces $1B Repurchase Program, Ups Dividend
2024-04-26 - NOV expects to increase its quarterly cash dividend on its common stock by 50% to $0.075 per share from $0.05 per share.
Initiative Equity Partners Acquires Equity in Renewable Firm ArtIn Energy
2024-04-26 - Initiative Equity Partners is taking steps to accelerate deployment of renewable energy globally, including in North America.
Repsol to Drop Marcellus Rig in June
2024-04-26 - Spain’s Repsol plans to drop its Marcellus Shale rig in June and reduce capex in the play due to the current U.S. gas price environment, CEO Josu Jon Imaz told analysts during a quarterly webcast.
Ithaca Deal ‘Ticks All the Boxes,’ Eni’s CFO Says
2024-04-26 - Eni’s deal to acquire Ithaca Energy marks a “strategic move to significantly strengthen its presence” on the U.K. Continental Shelf and “ticks all of the boxes” for the Italian energy company.