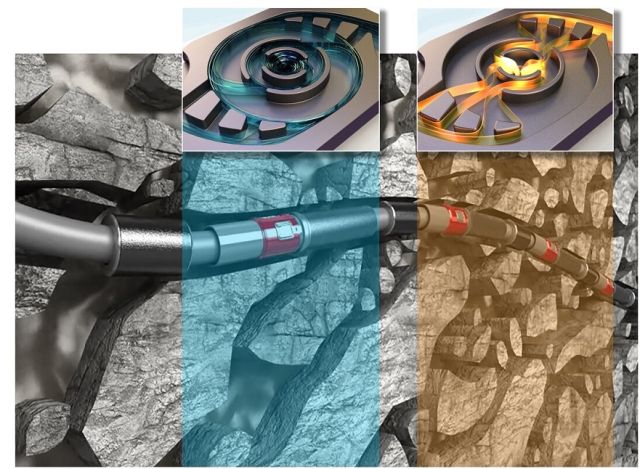
Halliburton’s viscosity-based EquiFlow autonomous inflow control device detects viscosity changes to differentiate oil from water and gas and restricts the flow of water or gas. (Source: Halliburton)
When the goal is to get as much oil or gas out of the ground as possible, controlling the flow of hydrocarbons— and other fluids — is critical. Knowing which fluid is which is all part of the challenge.
Inflow control devices (ICDs) are typically installed as part of a completion. Advances from the mid-to-late 2000s made it possible for the device to autonomously shut off the flow when an interval was producing unwanted water or gas to maximize oil production.
“The original AICDs (autonomous inflow control devices) were just kind of on-off tools” that restricted production from an unwanted water or gas producing zone or were used to balance production across the horizontal well, John O’Hara, Halliburton’s global business development manager for advanced completions, told Hart Energy.
When water was produced, they restricted total production or shut off the individual zone. Much like how intelligent completions went from intervention avoidance or to open, or shut off, AICDs have advanced from their original designs, he said.
“They've become more reservoir management tools than just on-off or intervention avoidance technologies,” he said. “Now AICDs have more capability in allowing wanted oil production while restricting only unwanted fluids."

AICD technology was originally developed by Equinor — then known as Statoil — and used widely across the Norwegian Continental Shelf (NCS) with well-documented use in the Troll Field.
Halliburton is working to develop advanced AICDs that apply to a wider range of wells, he said.
Halliburton’s viscosity-based AICD technology detects viscosity changes to differentiate oil from water and gas. Still, that’s not effective when oil and gas or water have the same or similar viscosity, he said.
A newer autonomous inflow control device technology detects different densities in the well fluids and restricts the flow of undesired fluids, he said.
“We have those reservoirs where the oil is very similar to water (density). We can still shut off that water and maximize that oil production,” he said.
While detecting viscosity is fairly straightforward, O’Hara said the biggest hurdle in developing a density-based AICD came down to orienting it in the well to account for gravity. In essence, he said, Halliburton developed a mechanical centrifugal switch.
“It creates artificial gravity that then identifies the difference in buoyancy forces,” he said. “By doing that, it allows us to close off a valve, basically, or shut off flow when it’s water and have it reopened if it becomes oil again.”
Part of what Halliburton worked out is how to create the centrifugal force for the artificial gravity in a small tool that could be packaged; sent downhole; and then operate reliably over the life of the well, O’Hara said. There were, he added, some unique engineering challenges around the mechanical switch, which Haliburton calls the “fluid selector”.
“It allows us to prevent a water-producing interval from dominating the overall production in the well,” O’Hara said. “One of the big advantages of that is we leave water in place rather than handling water at the surface.”
In early testing, he said, one unexpected outcome of the new density-based AICD is that it performed equally well in producing gas while still restricting water versus traditional oil producing wells.
That’ll help meet a gap in the market, he said, because one of the limitations of existing AICD technology across all vendors has been a device that shuts off water in gas wells.
Halliburton’s density-based tool, slated for field testing with a large Middle East operator in first-quarter 2024, is intended for mature fields with high water cuts or unwanted gas. Following the Middle East trial, additional deployments are planned on the NCS as well as in South America and the Asia-Pacific, he said.
AICD deployment is simple, whether it’s viscosity-based or density-based, he said. The AICD integrates with perforated pipe or screens as part of the completion.
“We don't have any control lines from the surface, we don't have anything we need to connect to actuate the balance. Again, they're autonomous,” he said.
Typically, one density based AICD would be placed per screen joint.
“It allows you to truly compartmentalize over long horizontals,” making it possible to shut off where the water zone happens to be while still allowing for maximum production in the other producing oil intervals, O’Hara said.
In multi-phase flow, the AICD responds to a defined water cut, but it still allows a small amount of flow to proceed, he said.
Halliburton’s current density based AICD is a 3.5-inch tool and a 5.5-inch tool is planned. Together, those tools will be able to serve lower flow rate, mature fields like those in the Middle East, along with higher flow rate Norwegian Continental Shelf applications, he said.
The service company has also been working to merge the viscosity-based and density-based AICDs with gravel pack and intelligent completions technologies, O’Hara said.
While AICDs can be retrofitted, he said they are most typically installed as part of the original completion design.
O’Hara said he has seen an uptick in industry use of AICDs.
“Your overall recovery rate is very important, so what we see is, with that need to squeeze every drop out of existing reservoirs or existing fields, technologies like AICDs become critical because as that field ages, it does produce more water,” he said. “We're being challenged to squeeze more oil out of rock. This is very much an enabling technology that still has a cost advantage in that it doesn't have complex infrastructure tied to it.”
Recommended Reading
Tech Trends: Halliburton’s Carbon Capturing Cement Solution
2024-02-20 - Halliburton’s new CorrosaLock cement solution provides chemical resistance to CO2 and minimizes the impact of cyclic loading on the cement barrier.
NAPE: Chevron’s Chris Powers Talks Traditional Oil, Gas Role in CCUS
2024-02-12 - Policy, innovation and partnership are among the areas needed to help grow the emerging CCUS sector, a Chevron executive said.
NAPE: Turning Orphan Wells From a Hot Mess Into a Hot Opportunity
2024-02-09 - Certain orphaned wells across the U.S. could be plugged to earn carbon credits.
Exxon Versus Chevron: The Fight for Hess’ 30% Guyana Interest
2024-03-04 - Chevron's plan to buy Hess Corp. and assume a 30% foothold in Guyana has been complicated by Exxon Mobil and CNOOC's claims that they have the right of first refusal for the interest.
Petrobras to Step Up Exploration with $7.5B in Capex, CEO Says
2024-03-26 - Petrobras CEO Jean Paul Prates said the company is considering exploration opportunities from the Equatorial margin of South America to West Africa.