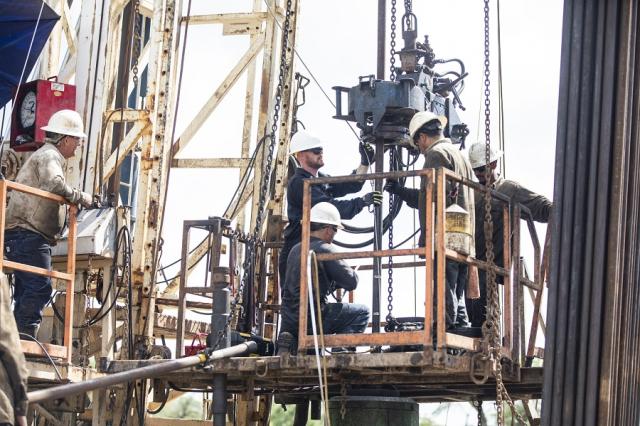
Deployment of Upwing’s SCS using industry standard equipment to increase the efficiency of the completion. (Source: Upwing Energy)
Until now, simulating multiphase well flow has largely been based on liquid-rich flow with associated gas, rather than gas flow with liquids, inhibiting the maximization of production in gas reservoirs.
Now, Upwing Energy has improved a simulation tool able to predict multiphase behavior and optimize the effects of phase change, liquid drop out, wellbore geometry and placement of artificial lift pumps.
Upwing announced on Aug. 10 significant advancements to its Enhanced Production Simulator (EPS) allowing for a deeper understanding of multiphase behavior and its impact on gas well performance. That understanding came through access to data and learnings from deployments of the company’s Subsurface Compression System (SCS) in customer wells. The EPS simulator tool is used in conjunction with the SCS artificial lift solution that increases natural gas production and recoverability.
David Biddick, director of technical field operations for Upwing Energy, told Hart Energy data is plugged into the company’s reservoir and compressor models.
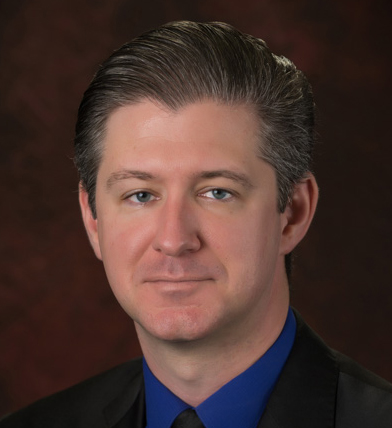
“The missing piece in between the two has been the wellbore model,” he said. “The wellbore model is where we're really refining this knowledge and improving the benchmark code that's translating the reservoir information to actual production.”
In short, he said, the EPS is “a handshake between the reservoir model, the compressor model,” and data from the wellhead. And part of the EPS output is a custom SCS design for the well in question.
Using simulations, Upwing is fine-tuning the benchmark matrix for multi-phase to better align with data from the wells, he said. Early in the development of the SCS, which started field trials in 2016, the company was focused more on the tool, but focus has shifted to understanding the whole system, he said.
“That goes from the reservoir all the way to the production facility,” he said. “We’ve started to get engaged with that system as a whole and how best to maximize both production, but also streamline how to unload a well efficiently and correctly from the beginning.”
As such, with every SCS deployment, Upwing is “instrumenting more than you would traditionally need to” with redundant sensors, gauges, permanent downhole gauges and memory gauges to improve the understanding of multiphase behavior and ultimately the simulations done through EPS.
“There's a general misunderstanding of, ‘this has been done for years for oil. Why is it so difficult for gas?’” Biddick said. “The reason is we just don't have a lot of case history for this, whether it be actually in the wells themselves or in the research industry. That is improving with time, but it's still not the main focus of a lot of the multi-phase physics that has been done historically.”
But being able to do so is important because it can revive a well.
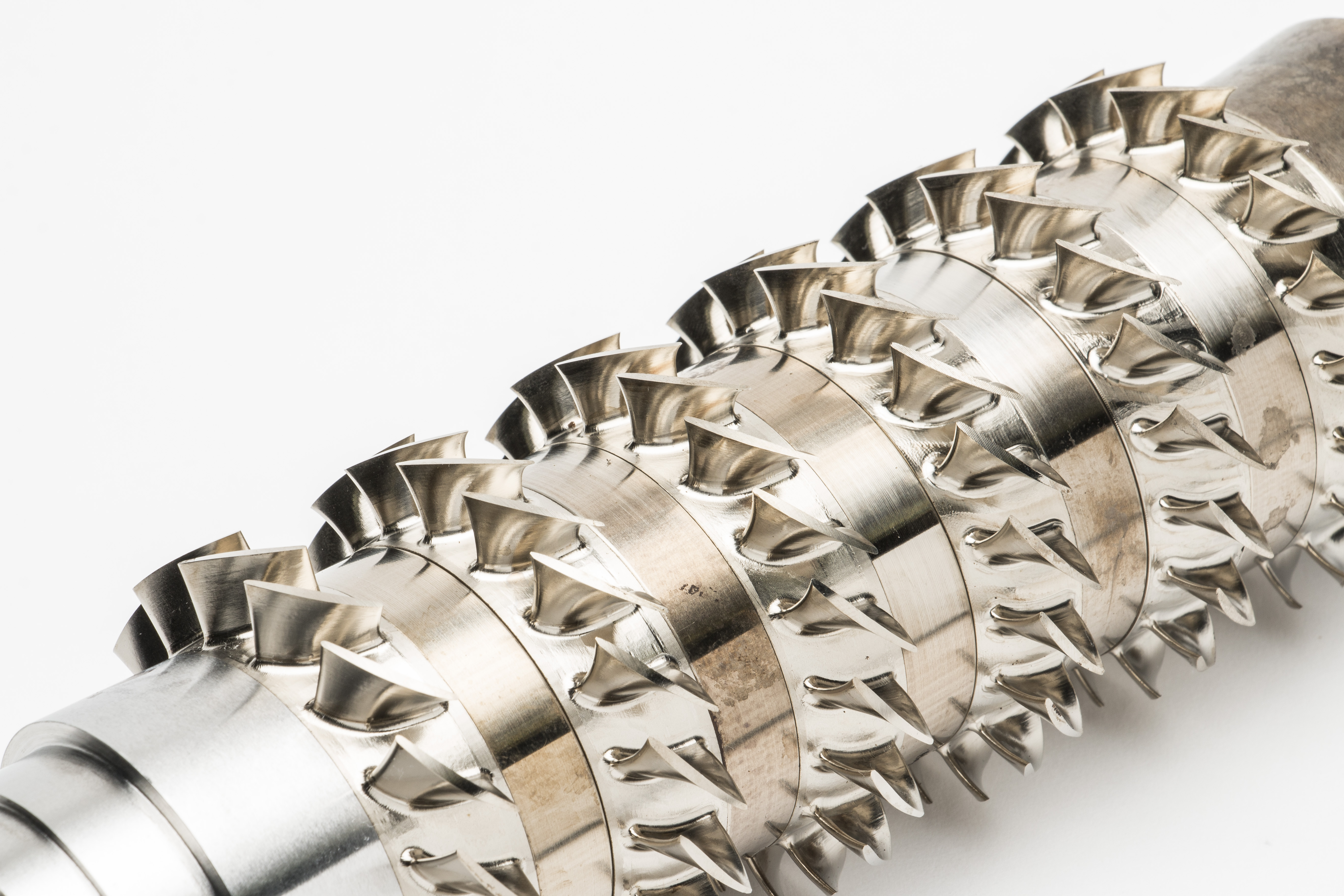
“We can actually have a liquid loaded well that's completely killed itself off over time, and we can predict what compressor needs to be developed in order to both deliquify it initially when we do the startup, as well as continually deliquify it over the life of the well with that compressor installed,” he said.
Upwing Energy is already using designs from the EPS to cut metal. The aim, Biddick said, is to be able to log a client well and install a custom SCS for that well in three to six months. Moving forward, the company will continue refining its database and streamlining the design and production phases.
The EPS is applicable for placement of SCSs in coalbed methane wells, unconventional wells and in fields with wildly varying conditions, whether onshore or offshore. Biddick said varying wellhead pressure would be one application.
“It could be a major field that has a lot of wells producing at the same time, we can equalize that across several wells. If you put several of these in a field, you can maintain that header pressure at the same time, and you don't have neighboring wells killing off lower pressure wells, which means you can extend the life of the field in general and you can draw down the reservoir significantly more over the life of the field.”
Recommended Reading
Going with the Flow: Universities, Operators Team on Flow Assurance Research
2024-03-05 - From Icy Waterfloods to Gas Lift Slugs, operators and researchers at Texas Tech University and the Colorado School of Mines are finding ways to optimize flow assurance, reduce costs and improve wells.
Defeating the ‘Four Horsemen’ of Flow Assurance
2024-04-18 - Service companies combine processes and techniques to mitigate the impact of paraffin, asphaltenes, hydrates and scale on production—and keep the cash flowing.
Exclusive: Halliburton’s Frac Automation Roadmap
2024-03-06 - In this Hart Energy Exclusive, Halliburton’s William Ruhle describes the challenges and future of automating frac jobs.
Fracturing’s Geometry Test
2024-02-12 - During SPE’s Hydraulic Fracturing Technical Conference, industry experts looked for answers to their biggest test – fracture geometry.
AVEVA: Immersive Tech, Augmented Reality and What’s New in the Cloud
2024-04-15 - Rob McGreevy, AVEVA’s chief product officer, talks about technology advancements that give employees on the job training without any of the risks.