The reservoir wells of the shale revolution, once gushing like geysers, are beginning to run dry.
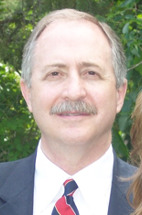
“Since [the shale revolution], there’s been about 100,000 horizontal shale wells drilled and put in production, [increasing] our production by about 6 million barrels a day,” Robert Downey, CEO of Shale Ingenuity, told Hart Energy. “But today, about a third of those wells are now producing less than 10 barrels a day because they come on like gangbusters and then they have a really steep decline. Pretty much all the wells drilled prior to 2015 are [almost] depleted.”
According to a Texas Bureau of Economic Geology study, the estimated typical oil recovery is about 6% of the oil in place, or as Downey explains, “you drill this horizontal well, spend $7 million on it and produce for 10 years. And by the time the well is pretty much producing nothing, you’ve recovered a whopping 6% of the oil.”
The Williston and Permian basins and the Eagle Ford Shale hold a combined 3.1 trillion barrels of oil. A 6% recovery at full development leaves 2.9 trillion barrels of oil in place, which is 77 times the proved reserves of the U.S. Getting that remaining 94% of oil is the challenge for oil and gas companies today.
SuperEOR is Shale Ingenuity’s solution to the shale wells running dry. The SuperEOR process is similar to huff and puff injection, as it involves injecting a solvent into the reservoir, which expands into a gas and drives the oil out of the rock. However, the solvent has a specific composition, making this process more sustainable than other EOR methods. That’s because the solvent is able to be recovered from the rock and reused multiple times.
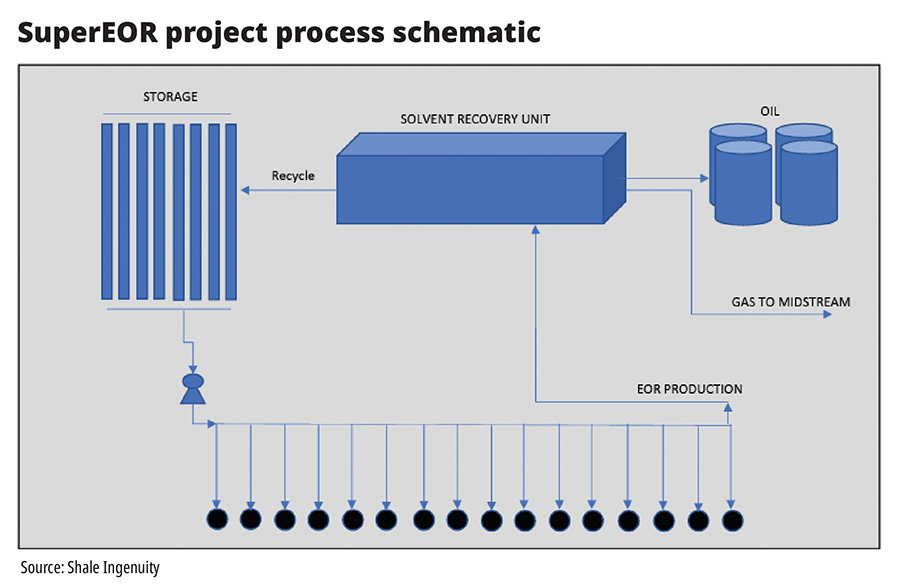
“It’s much different than if you just injected natural gas or CO2 [into the well], because with natural gas or CO2, you have to get the bottom of pressure up to 3,000 [psi] or 4,000 psi to get those gases to go into solution. Our solvent goes into solution at 700 psi,” Downey said. “Once you inject it, it forces all this oil through the pores. It expands to a gas and it flows up the wellbore and you recover it on the surface, condense it back into a liquid state, store it on location and then reinject it.”
When using SuperEOR for a core test, over 90% of the oil was able to be recovered out of the core, said Downey. The recovery process is also quick and efficient, as only five days to 10 days of solvent injection can lead to between 10 and 20 days of flowback.
“If you were injecting gas, you’d be injecting for one month to two months and then flowing back for three or four months, but our cycles are fast and the recovery is much greater. So, instead of getting maybe 10% to 40% more oil, we can get 300% to 500% more oil,” Downey said.
Another sustainable EOR solution is actually an OOR, or organic oil recovery solution.
California-based Titan Oil Recovery uses a specialized EOR process that takes advantage of indigenous microbes that have adapted to the environment over millions of years in order to extract oil from mature reservoirs.
Titan activates the biology and ecology of oil reservoirs by working with specific species of microbes that can physically deform oil, turning them into micro oil droplets. This allows the trapped oil in reservoirs to escape and be recovered. The technology has a low carbon footprint and can also reduce hydrogen sulfide production in oil fields.
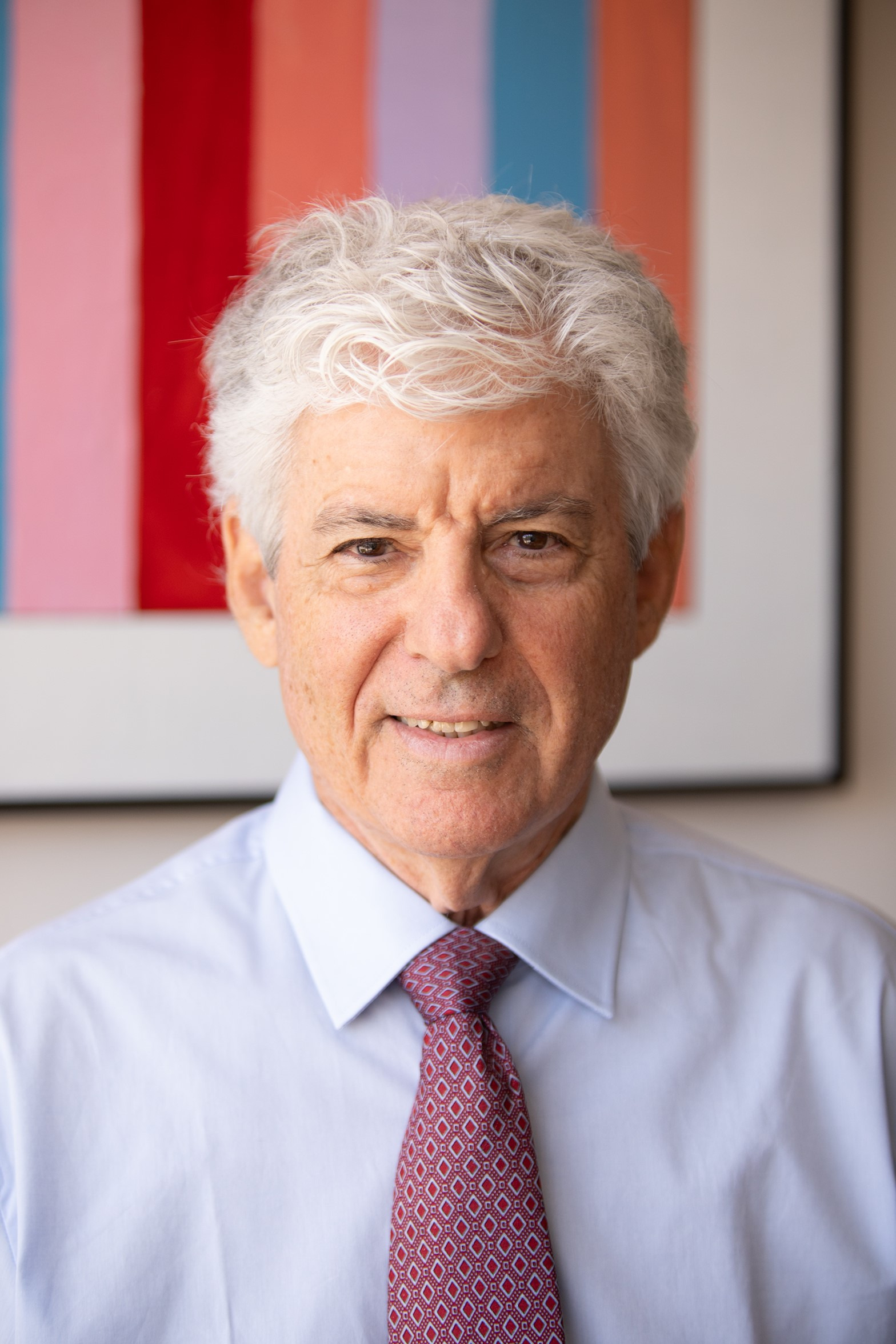
“We do an analysis in our lab and find out which species down [in the reservoir] we can work with,” Kenneth Gerbino, CEO of Titan Oil Recovery, told Hart Energy. “There are certain species that eat our food and we can change their living habits. Instead of wanting to be next to the water and the rock in the oil reservoir, the sandstone or the carbonates, they now want to be next to oil.”
The “food” Gerbino refers to is a complex formula of organic and biodegradable nutrients that is tailor-made for every field. The food causes the targeted microbes to multiply and induces the targeted microbes to become oleophilic (affinity for oils) and attach themselves to oil droplets.
The microbes also become hydrophobic (not wanting to be near water); they move away from the water and rock interface where they have always been and surround the oil, Gerbino said. They then physically deform the oil, creating micro oil droplets.
“They don’t ‘eat’ the oil,” Gerbino said. “They just surround it and they break it down. And now, for the first time, you have these micro oil droplets in a reservoir that can now escape from the tight spaces down there.”
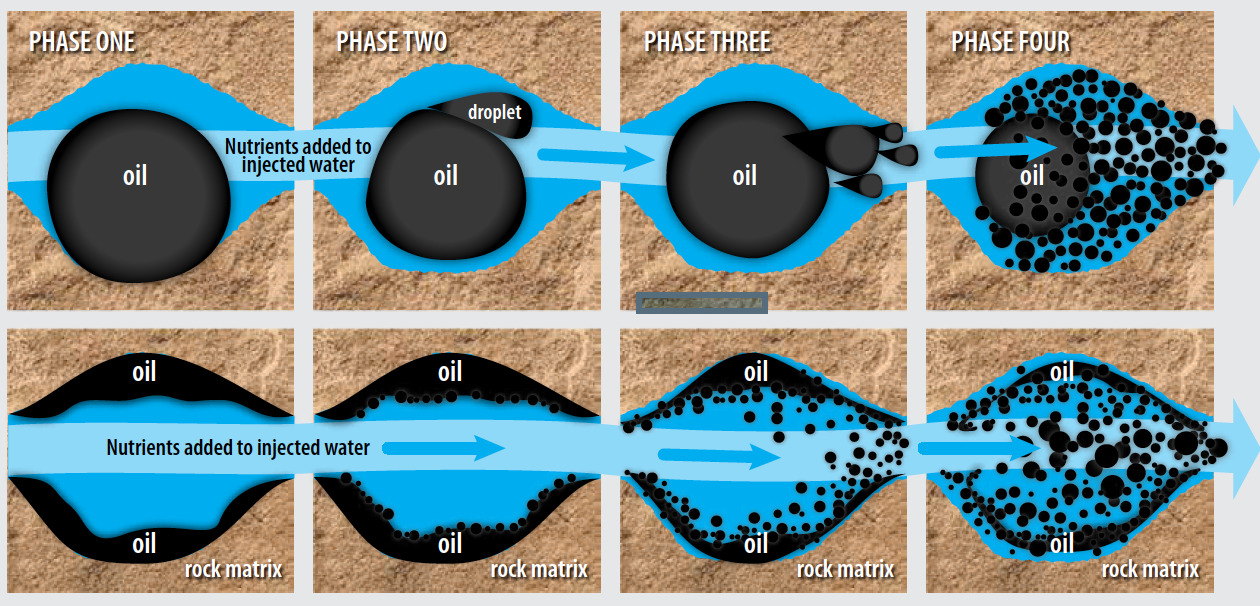
The Titan process works both onshore and offshore and is able to provide a high return on investment, because the initial investment is next to nothing. A peer-reviewed SPE paper by Husky Energy in Canada found that the cost of the recovery process was $6 per incremental barrel. Recent results in projects in both the Middle East and North Sea have returned over 1,000% ROI to customers.
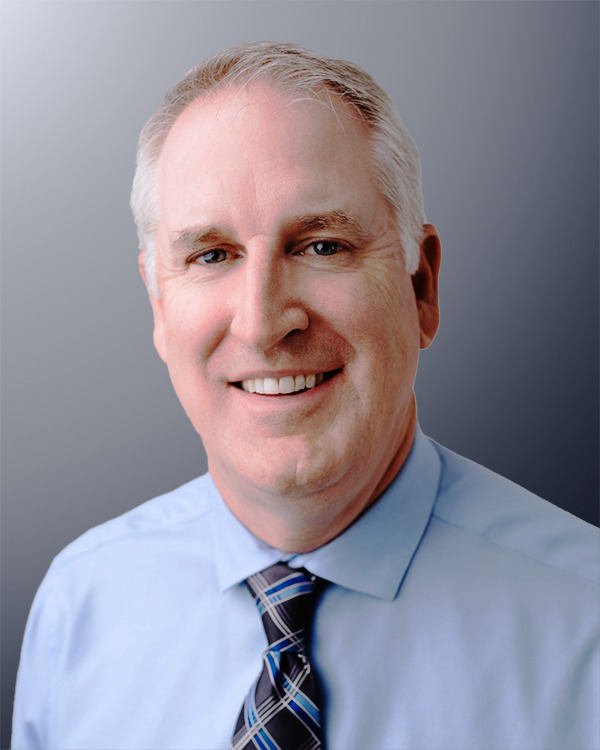
“What’s real important with our technology is that there’s zero capex … we’re not putting in and installing equipment or building things. We have the potential to move quicker than any other technology in the market to market,” said Mike Carroll, vice president of technology for Titan Oil Recovery. “We’ve got blending set up in the U.S., Canada, U.K., Holland, Dubai and Singapore. So, we can service the entire world already from our mark.”
Titan Oil Recovery has been in 63 oil fields on five continents with 350 well applications, including 275 injection well applications, and has delivered an average increase in production of over 90%, the company said. The SuperEOR process has been used in the Bakken Shale and the Utica Shale, as well as in other NDA-protected projects, and has recovered at least 20% more oil than traditional methods of EOR, the company said. The industry has been slow to embrace these less expensive EOR methods, tending to rely more on traditional drilling and completion methods.
“Everyone does the same thing. You drill, you frack, you produce, you drill, you frack, you produce. And that’s pretty much the entire focus. … Our industry has kind of gotten away from enhanced oil recovery. … EOR only accounts for about 1.5% of all production worldwide,” Downey said. “We’ve kind of gotten fat, dumb and happy as an industry drilling these shale wells and haven’t needed to do EOR. But as we’re starting to drill out our acreage and our wells are getting pretty mature and depleted, we’re going to have to start thinking about EOR.”
Currently, Shale Ingenuity works to install and operate projects for clients or license out their SuperEOR patent for a cost. Titan Oil Recovery, who has already worked with four of the top companies in oil and gas and has a partnership with Hunting Plc, is looking to find a service company to buy them out.
Despite the industry being slow to adopt these new methods of EOR, both CEOs believe a watershed moment is soon to arrive in the oil and gas industry.
Recommended Reading
TGS, SLB to Conduct Engagement Phase 5 in GoM
2024-02-05 - TGS and SLB’s seventh program within the joint venture involves the acquisition of 157 Outer Continental Shelf blocks.
2023-2025 Subsea Tieback Round-Up
2024-02-06 - Here's a look at subsea tieback projects across the globe. The first in a two-part series, this report highlights some of the subsea tiebacks scheduled to be online by 2025.
StimStixx, Hunting Titan Partner on Well Perforation, Acidizing
2024-02-07 - The strategic partnership between StimStixx Technologies and Hunting Titan will increase well treatments and reduce costs, the companies said.
Tech Trends: QYSEA’s Artificially Intelligent Underwater Additions
2024-02-13 - Using their AI underwater image filtering algorithm, the QYSEA AI Diver Tracking allows the FIFISH ROV to identify a diver's movements and conducts real-time automatic analysis.
Subsea Tieback Round-Up, 2026 and Beyond
2024-02-13 - The second in a two-part series, this report on subsea tiebacks looks at some of the projects around the world scheduled to come online in 2026 or later.