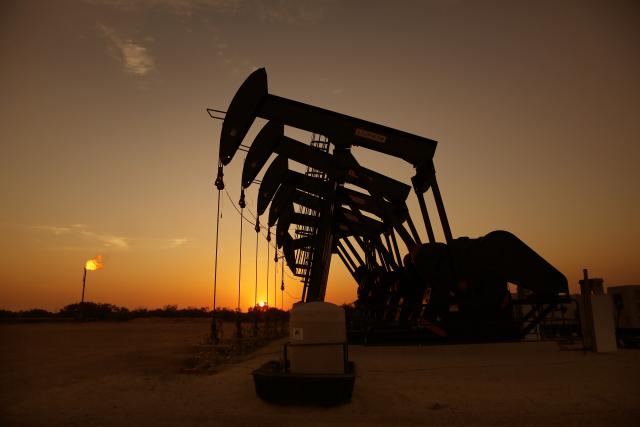
The sun sets behind six pumpjacks producing on a wellpad outside Cotulla, Texas. (Photo by Tom Fox, courtesy of Oil and Gas Investor)
The dynamics of the oil and gas industry can seemingly fluctuate as quickly as the next day’s closing bell on Wall Street. An oil and gas company’s operations are highly predicated on market conditions, and today, the market and its investors demand that the industry sprint to low capital-intensive production.
But to produce oil and gas at the levels demanded, operators must have first laid the foundations for large-scale production while possessing a mentality to adopt the technologies to optimize that production.
The evolution from single-well development to multiwell pads has provided operators the bandwidth to upscale their production operations and do so while maintaining fiscal prudence. Meanwhile, the adoption of digital technologies such as machine learning and artificial intelligence (AI), and at costs that operators are finding more reasonable, offers producers a wealth of means to get the most oil and gas out of a reservoir as they can.
Since about the middle of 2015, many operators have made the transition from single-well pads to multiwell pads to optimize operational efficiency and improve production. According to Energent, about 25% of the development in the Midland Basin consisted of multiwell pads in the second quarter of 2015. By the end of 2018, that amount more than doubled to more than half of all well development.
The results, of course, have led to the U.S. becoming the world’s largest oil producer. Now operators need to find ways to continue record-level production operations but do so while cutting costs.
One of the potential solutions identified by industry analysts is the widespread adoption of digital technologies. In a report analyzing the impact of digital transformation in upstream oil and gas, the Deloitte Center for Energy Solutions suggested that digital applications offer the potential of more than $20 billion of additional cash flow in production operations alone.
Identifying such cost savings through operational efficiencies rather than through, for example, staff reductions, is likely to appeal to an industry that has steadied itself after the price collapse in 2014.
“Upscaling your operations is about high-grading your operations, high-grading your field and your assets,” said Alex Robart, CEO of Ambyint, an artificial lift production optimization company. “It’s about high-grading your people’s time so that you can scale your operations and scale production without having to scale headcounts.”
Upscaling production
As producers move from single-well pads to pads with eight, 10 and sometimes a dozen or more wells and as they upscale their production operations, they also must address a multitude of logistical and infrastructure challenges. Locking in takeaway capacity, deciding on the optimal artificial lift strategy, and later, tertiary recovery methods, and how to apply digital technologies like machine learning and AI are among the many decisions operators must make along the way to implementing a manufacturing mode of production.
Like all other oil and gas producing operations such as conventional production and offshore development, upscaling production begins with a firm understanding of the reservoir.
“Upscaling always starts with subsurface characterization and better understanding [of the reservoir],” said Ole Engels, director of geoscience and petroleum engineering, North America, for Baker Hughes, a GE company (BHGE). “When you go through a field development plan and you first understand your hydrocarbons in place and you understand your formation, your landing zones and you understand the optimization of the hydraulic fracturing process, that leads you to development economics.”
Those economics have changed dramatically over the past half-decade. When oil prices eclipsed $90/bbl, operators were flush with cash and spending heavily on drilling new wells. In September 2014, when the daily price of oil averaged $93.31/bbl, operators were running the highest number of rigs ever—1,931, according to the BHGE rig count. Now with the price of oil hovering in the $60/bbl range, operators have been forced to cut expenses. That has meant utilizing fewer drilling rigs but also getting more oil and gas out of the ground at a manageable breakeven cost. Among those efficiency gains has been the rise of large-scale production operations.
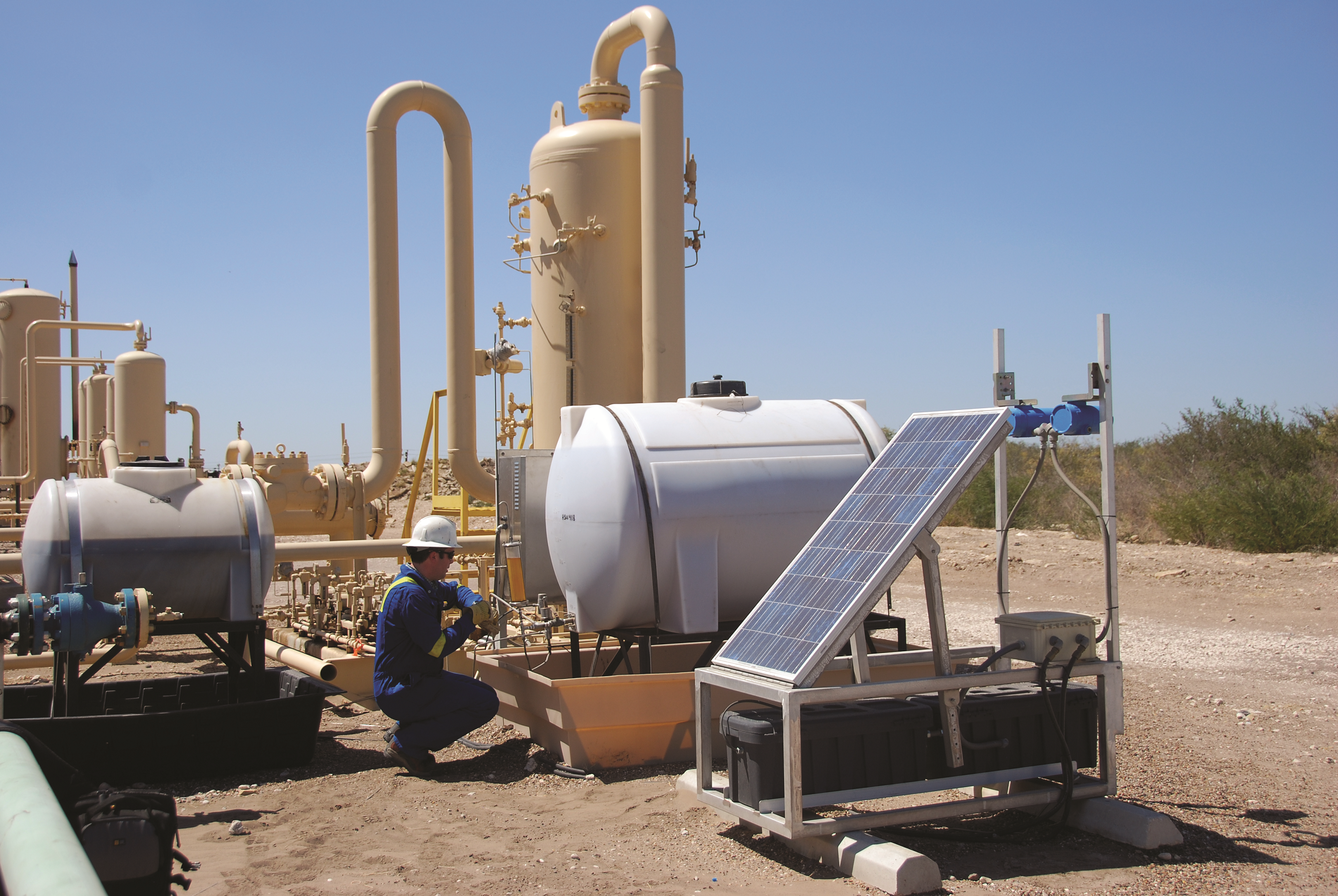
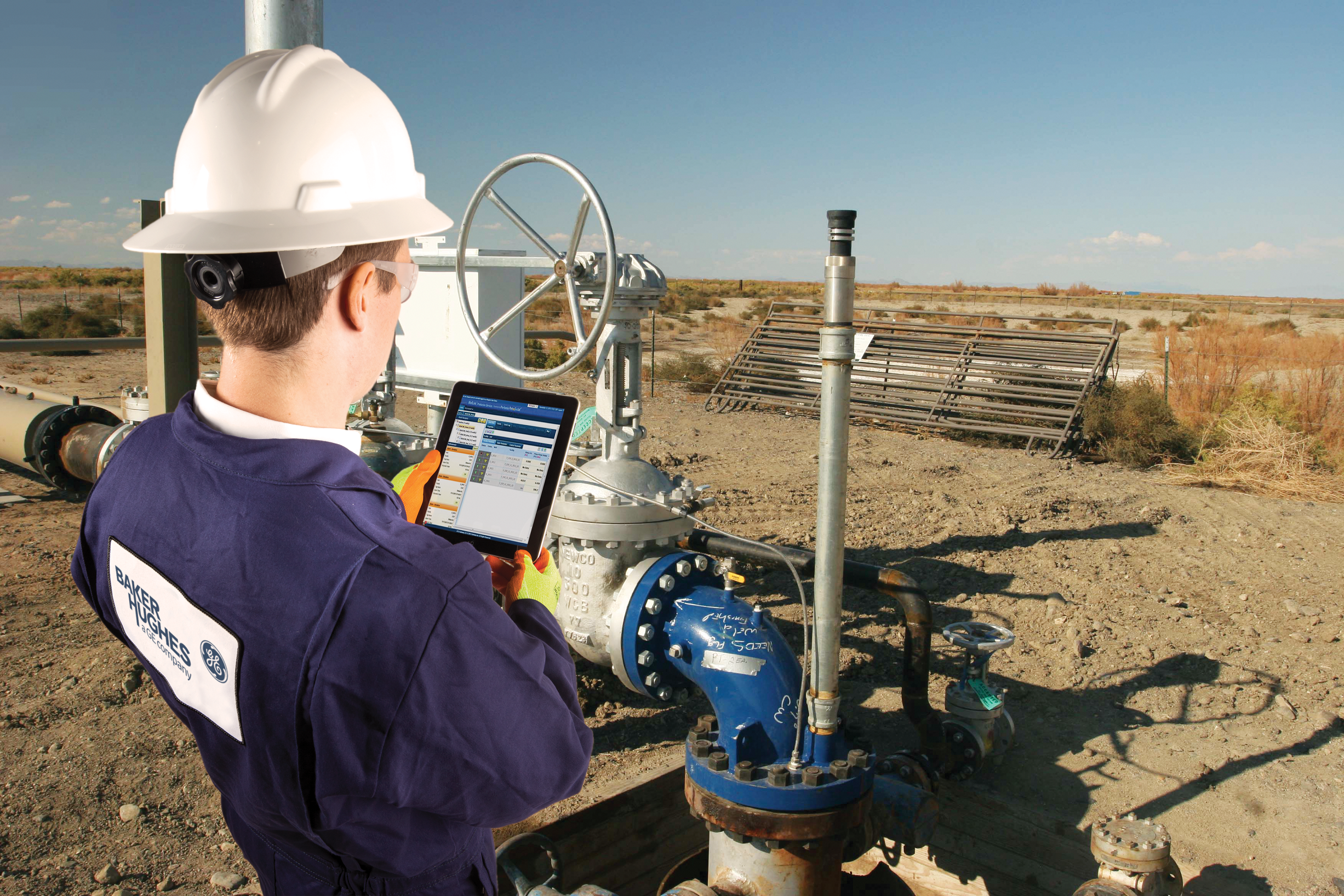
But large-scale manufacturing mode operations also lead to challenges to replace lost production. As Robart explained, one of the dynamics of unconventional wells is high IP but a sharp decline curve. “What that means is that with much more activity on an ongoing basis, continuing to backfill that decline curve is much more of a large-scale program shift to more of a manufacturing mode and thinking about how to run an operation at scale,” he said.
Along with an understanding of reservoir characteristics and a production scheme to alleviate a well’s decline, establishing infrastructure such as pipeline capacity is a key component of upscaling production operations.
“The challenge for operators is always to have more infrastructure to get the hydrocarbons to market. That freedom allows operators to have a more robust field development plan,” said Rob Hull, Halliburton’s senior regional manager of consulting and project management, North America. “Operators can drill all the wells as fast as they can, but if they can’t sell it through the pipeline, there’s no reason to drill it quickly.”
With multiple operators competing for a place for their product in the pipeline, particularly in places like the Permian Basin, bottlenecked takeaway capacity could result in E&P companies cutting back their activity, Hull said. Over the course of the next year or so, several pipelines are expected to begin operations in the Permian Basin, including the Cactus II, EPIC Crude Oil, Gray Oak and Jupiter pipelines.
Once a full understanding of the reservoir is achieved, and the proper infrastructure is in place, a full-scale development plan begins to take shape.
Paul Mahoney, president of production and automation technologies for artificial lift company Apergy, said service providers often work with producers early on during the planning stages to gain an understanding of what their long-term production goals are to implement the right secondary and tertiary production strategies as well to understand the rights types of technologies to introduce.
“As an artificial lift, production-oriented company, we work with operators during that phase to understand what those long-term production goals are,” he said. “We want to know what the field strategy is in terms of number of wells, types of wells, locations, producing formations, etcetera, which allows for us to consult what the right depletion strategy is. What is the right depletion mechanism to do secondary or tertiary recovery that allows them to complete this full economic model?”
Optimizing production
Two of the primary challenges that E&P companies face when implementing large-scale production operations are ensuring all of their wells are producing to their full potential and recovering as much of the hydrocarbons in place as possible. Hull and Robart see room for improvement in both arenas.
“What we see out there is that only 15% to 20% of wells in onshore North America are actually optimized,” Robart said. “What I mean by that is, of those wells, only 15% to 20% of those wells are producing up to their potential. That’s because people don’t have the time to look at those wells. They are overwhelmed, they are in reactive mode and they don’t have the time to manage the set points to keep those wells and all the levers available to them on their controls at the optimal place to get the most out of that well.”
Robart said he believes that the vast majority of wells—perhaps as many at 70%—are running too fast, with extra strokes and with overuse of electricity consumption, much of which can result in production failures.
Hull explained that the average recovery factor in a mature field is about 35%, and advancements in production technology are needed to go after the stranded 65%. He suggests companies apply reentry techniques, apply different chemical recipes and institute other EOR practices to help recover some of those hydrocarbons.
“I think that everybody gets enamored with the horizontal technology, which they should because you are automatically connecting into those reserves by being able to drill precisely into them,” Hull said. “But on the production side, there are techniques with workovers, refracs, re-perfs and EOR that are still available. Over the years, these applications have come down in price and are much more cost-effective. They are much more optimized than when we first started using them.”
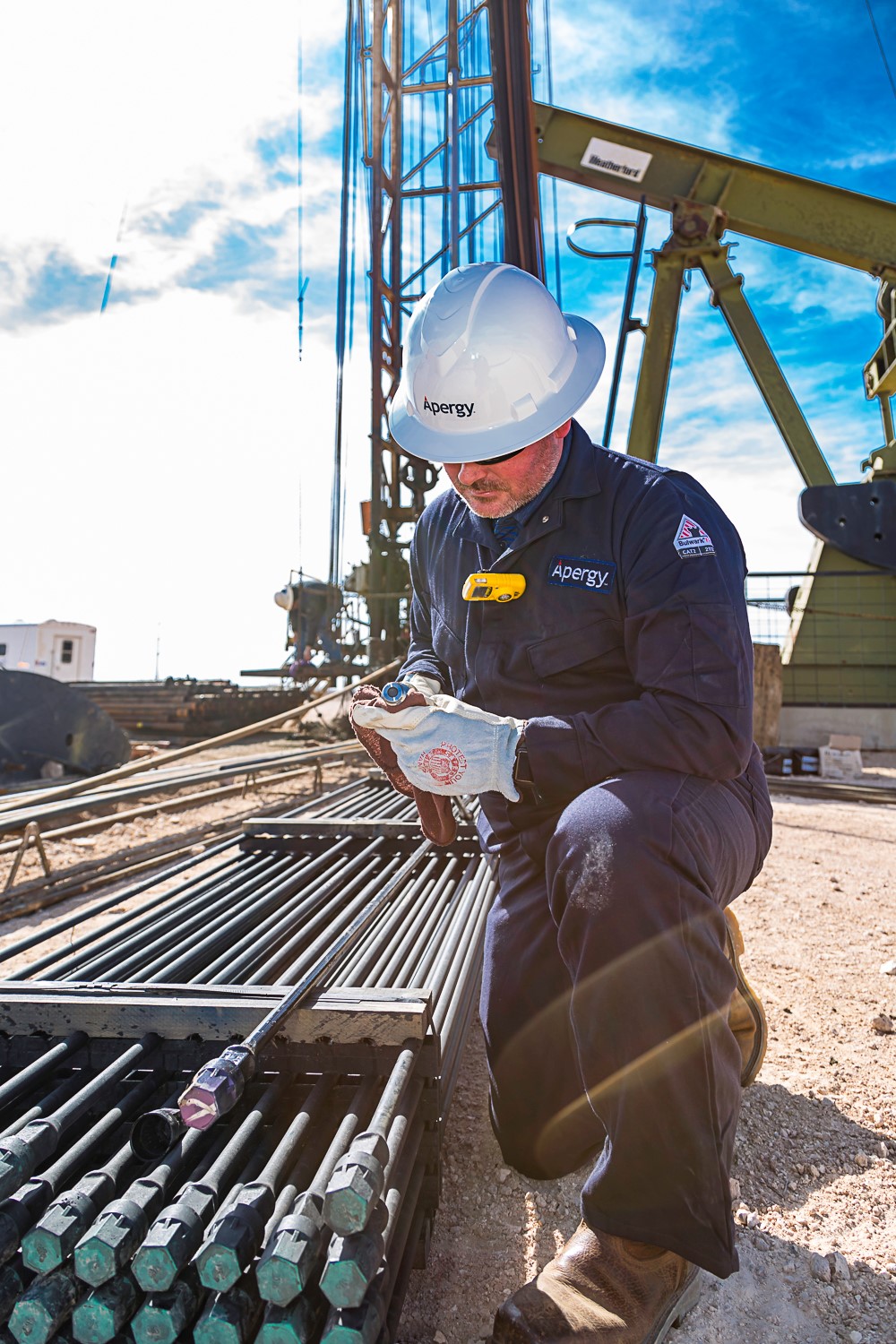
Depending on their production strategy, operators have sought methods and technologies to ensure wells stay productive for a longer period of time. However, Hull believes managing production rates is more than simply adjusting a well’s choke size.
“Eventually, every well is going to go on the decline. To suppress a decline, you can either work the well over and introduce new technology, such as a refrac or something similar, or maintain a good program to try to lessen your decline curve as much as you possibly can, thus getting a longer well life. At the end of the day, all wells will reach the economic limit, and at that time, it is all about successfully abandoning the well with good barrier assurance,” he said.
In an effort to optimize a well’s production capabilities, Ambyint provides machine learning and AI systems, such as its Amplify real-time controller that captures and analyzes high-frequency, stroke-based data. The system provides set-point adjustments to optimize every well in a field, according to the company. Robart explained that Ambyint’s approach is to get the most out of the well as it exists, rather than conducting workovers.
“Our AI systems help take some of the control of that well to deliver optimization and get those wells up to their production potential so operators can stay on their decline curve plan to meet their production target,” he said. “In our world of production, we are not going to go back and restimulate that wellbore; we’re not going to go back and redesign that wellbore. That wellbore is in the ground, so let’s take what we have and get the absolute most out of that well using some technology and improving the process around it.”
Applying digital technologies
Robart explained that the oil and gas industry has not always made process optimization for production a priority, particularly when oil prices were high. A highprice environment often allowed operators to lose track of discipline in the chase for more hydrocarbons sold at a higher price. “But when times are bad, you just hammer through, cut jobs and shut down activity,” he said. “That cycle from extreme up to extreme down doesn’t really lend itself to process optimization.”
But as prices have stabilized, producers have made operating efficiencies a priority in an effort to generate higher profits. “In this new kind of normal price range where companies are making money, but not enough to lose discipline, they are thinking harder about processes and what they can do on a sustainable basis to take out the cost to improve margins asset by asset,” Robart said. “And that’s what is leading to digital as one of the major tools to help drive things to the next level.”
Digital technologies, machine learning and AI have been deployed in every facet of upstream oil and gas operations, but they are particularly applicable in production operations, where emerging technologies are helping producers fine-tune their rod stroke efficiencies, select the best artificial lift system for a particular well and predict equipment failures.
In addition to improved functionality, Halliburton’s Hull believes that another key reason digital technologies are becoming more accepted in the industry is improved costs. A few years ago, companies often wanted to adopt digital technologies in their operations, but Hull noted that those technologies were typically not cost-effective.
“Now with being able to implement digital technology, we see the move to not only save cost on location but making operations much more efficient,” he said. “[Digital] is able to really and truly provide value for the first time, so now we are starting to see more people putting fiber down a hole and move to a neural network-based optimization of the field. This is all driven by cost and efficiency. If lifting cost is going to be impacted by applying digital and a company is not getting value, then the company is not going to do it. An operation must bring value for its cost.”
Manoj Nimbalkar, global vice president of production automation and software at Weatherford, said one of the most significant components of production operations in which cost savings can be found is through predictive failure. Among its many capabilities, Weatherford’s ForeSite production optimization platform provides predictive failure capabilities for artificial lift systems such as rod lifts and electric submersible pumps (ESPs).
“When you think about rod lift, one of the reasons why operators want to apply this technology is because they want to save costs,” Nimbalkar said. “Once operators know that there could be a potential equipment failure, they can try to find out ways to mitigate that failure in advance. And if it is inevitable that the failure will happen, then it gives operators a better way of structuring the logistics for maintenance. Similar logic applies to ESP wells where the cost of deferred production is much higher than the cost of fixing the failed equipment itself. So the benefit is more of predictive maintenance as well, in addition to predictive failure identification.”
Intelligent algorithms such as those applied in Weatherford’s ForeSite have led to what Nimbalkar calls “edge” computing, or abilities that bring computation and data storage produced by Internet of Things (IoT) devices to be processed closer to the location where it is needed rather than sending it to data centers to improve response times and save bandwidth.
“Because of the computing power available at the edge, clients can actually get much more insight into what is happening in their field as opposed to what used to happen,” he said. “For example, when you look at rod lifts, because of the high-frequency data and the availability of the intelligence at the edge, today our clients can get the data for every rod lift stroke.”
He said that in previous iterations of controller technology, operators might see 1,300 dynamometer cards for a particular artificial lift. “Now, with this new technology, our clients can get 3.1 million cards for one particular well,” Nimbalkar said.
That information can then be applied to advanced analytics and allow operators to have a better understanding as to what is truly occurring with their production operations.
“When you get the high-frequency data for a gas well or a gas-lift well, they can identify in advance if there is slugging happening in the well, which would take traditionally maybe a day or so to figure out,” Nimbalkar said. “But now today, with the combination of the high-frequency data, the IoT-based notifications and our intelligent algorithms on the edge, the clients will come to know about slugging occurring in less than one hour’s time. And they can take preventative action on that.”
Mahoney explained that the emergence of widespread multiwell pad development presented new challenges to service providers like Apergy. And with the current climate demand, cost-cutting and downsized drilling and completion operations, applying new technologies to help operators maximize revenue has become paramount, he said.
“The desire for a company such as ours in production and automation technology is to really step up to the new challenges of multiwell pad and to horizontal developments with some newer technologies that allow for maintaining that dollar per boe without increasing new wells and drawing more capital,” Mahoney said. “How do we get more sustaining dollars out of our capital invested? We need technology to maintain that level of dollar per boe.”
Recommended Reading
Kinetik Holdings Enters Agreement to Pay Debt
2024-04-04 - Kinetik Holdings entered an agreement with PNC Bank to pay down outstanding debt.
Summit Midstream Launches Double E Pipeline Open Season
2024-04-02 - The Double E pipeline is set to deliver gas to the Waha Hub before the Matterhorn Express pipeline provides sorely needed takeaway capacity, an analyst said.
Summit Midstream Sells Utica Interests to MPLX for $625MM
2024-03-22 - Summit Midstream is selling Utica assets to MPLX, which include a natural gas and condensate pipeline network and storage.
Kinder Morgan Sees Need for Another Permian NatGas Pipeline
2024-04-18 - Negative prices, tight capacity and upcoming demand are driving natural gas leaders at Kinder Morgan to think about more takeaway capacity.
Targa Resources Forecasts Rising Profits on 2024 Exports
2024-02-20 - Midstream company Targa Resources reports a record fourth quarter in volumes and NGL fractionation.