Water’s role as the largest byproduct of oil and gas production has become increasingly problematic.
“If you can’t handle the produced water or if you can’t manage it and it gets out of hand, then it will impact your operations as it will impact energy production,” Devesh Mittal, vice president and general manager at Aquatech Energy Services, told Hart Energy. “So, while it is a byproduct, it can be a sort of hindrance if you’re not able to manage it.”
Produced water comes out of the well along with crude oil when a reservoir is being produced. It can contain both soluble and non-soluble oil and organics, suspended solids, dissolved solids and other chemicals used in the production process. Operators are required by law to manage that waste.
Traditionally, produced water has been injected into underground disposal wells. However, the capacity of these injection wells is limited and the increased use of disposal wells has, in some instances, been linked to seismic activity such as earthquakes. This has led to stricter regulations on the use and development of disposal wells.
Mitigating the impact
That’s where companies like Aquatech come in.
“We are working to reduce the impact of the increasing volumes of produced water. We’ll recover and purify that and then treat that recovered water to make it suitable for a variety of applications, tailored to a customer’s specific needs,” Mittal said.
Aquatech’s go-to solution is reuse and recycling. For produced water to be reused, the chemicals and organics from the formation must be removed. For water with a high level of total dissolved solids (TDS), Aquatech employs clarifiers and evaporators to use at or near the wellpad. In Oman, Aquatech has one of the largest evaporator systems on produced water, Mittal said, treating about 300,000 bbl/d.
“In certain instances, depending on the TDS of the produced water, it can be recovered using membrane systems such as our Osmotically Assisted Reverse Osmosis (OARO),” Mittal said.
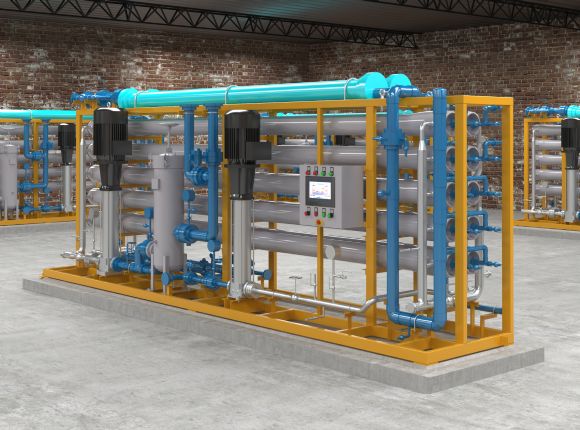
Reverse osmosis is a popular method for water purification in the industry due to its low energy consumption. During the process, seawater or brackish water is forced through a semipermeable membrane, leaving salt and other contaminants on the pressurized side of the membrane while pure water is allowed to pass through.
Aquatech uses a variety of membrane-based solutions, most notably its Advanced Recovery Reverse Osmosis (ARRO) process. ARRO uses modular configuration and automation technology to reduce operator intervention and achieve water recovery rates of over 95%, which is 20% better than traditional reverse osmosis solutions.
In addition to ARRO, Aquatech’s High Efficiency Reverse Osmosis (HERO) system places reverse osmosis membranes in a high pH environment, causing them to remain in a “continuous cleaning mode.” This prevents contaminants from collecting in the pores of a filtration membrane and restricting water flow.
Once rid of the various contaminants in the water, the produced water is available for reuse in applications such as EOR or even irrigation of crops if the water is pure enough.
Adding lithium extraction
Aquatech is also stepping into water reuse in lithium production.
Most produced water has only a small concentration of lithium, but since the amount of produced water from traditional oil and gas operations is significant, a reasonable amount of lithium can be gathered from the process. Lithium, used in batteries, opens up a completely new pathway for Aquatech customers to generate revenue from water.
“Finding ways to extract lithium out of produced water is a way to reduce the cost of managing this water,” said Mittal. “Right now, it’s a waste, but if you can convert it into a critical mineral source and you can recover revenue out of it, then it might offset some of the overall water management costs.”
The company has succeeded in the oil and gas industry for more than 40 years because of its ability to scale treatment solutions, Mittal said. Now it’s working on scalability for lithium production.
“The quantity of produced water is increasing, so we have to work to find innovative ways to supplement our current ways of dealing with produced water to provide long-term sustainability,” Mittal said. “That’s where we are putting our minds and money.”
Recommended Reading
CEO: Coterra ‘Deeply Curious’ on M&A Amid E&P Consolidation Wave
2024-02-26 - Coterra Energy has yet to get in on the large-scale M&A wave sweeping across the Lower 48—but CEO Tom Jorden said Coterra is keeping an eye on acquisition opportunities.
Endeavor Integration Brings Capital Efficiency, Durability to Diamondback
2024-02-22 - The combined Diamondback-Endeavor deal is expected to realize $3 billion in synergies and have 12 years of sub-$40/bbl breakeven inventory.
Patterson-UTI Braces for Activity ‘Pause’ After E&P Consolidations
2024-02-19 - Patterson-UTI saw net income rebound from 2022 and CEO Andy Hendricks says the company is well positioned following a wave of E&P consolidations that may slow activity.
CEO: Magnolia Hunting Giddings Bolt-ons that ‘Pack a Punch’ in ‘24
2024-02-16 - Magnolia Oil & Gas plans to boost production volumes in the single digits this year, with the majority of the growth coming from the Giddings Field.
E&P Earnings Season Proves Up Stronger Efficiencies, Profits
2024-04-04 - The 2024 outlook for E&Ps largely surprises to the upside with conservative budgets and steady volumes.