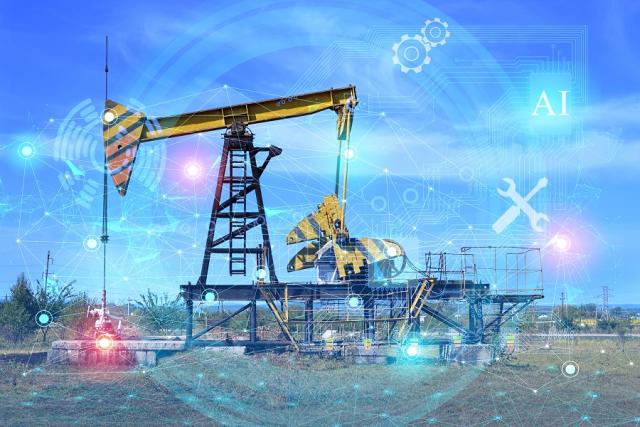
Diversified Well Logging CEO David Tonner informed URTeC attendees of the advancements in automation in the drilling world and what automation as a whole could mean for the industry. (Source: Shutterstock.com)
The first industrial revolution was powered by steam engines. The next by electrification. This was followed by the third, which focused on digitization.
The fourth—and current—revolution involves artificial intelligence, or AI, and automation. Diversified Well Logging CEO David Tonner recognizes both the benefits and disadvantages of these advancements. But the company has responded with the development of a collaborative robot to help them move forward.
“There's a lot of potential issues with that evolution, whether it's our jobs being taken away, or some of the other ethical considerations about autonomous systems as well,” Tonner said, speaking during the Robotics and Automation in Drilling and Logging Topical Luncheon at Unconventional Resources Technology Conference (URTeC) 2023.
However, he also sees the value in artificial intelligence, listing the positives as “enhanced safety, taking humans out of harm's way, improving the quality of life so we're free to not be involved in routine work, advancements in healthcare, economic growth and job creation.”
As a former mudlogger, Tonner is familiar with the menial tasks required by the drilling industry. He told attendees that the sample collection process for mudlogging has remained unchanged since the 1930s.
Tonner recalled his 12-hour shifts were often spent running up and down stairs to collect information about the mud being drilled. He would then walk across the lease to the shakers, collecting and bagging mud samples, rinsing the samples and then returning to his unit. The process was both labor and time intensive and slow relative to ROPs and didn’t give him a chance to analyze the findings and put his love and knowledge of geology to use.
Automation has helped provide a solution for that.
“The evolution of automation and drilling is all revolving around improving rig safety, reducing the number of people on the rig floor, be able to continue operating in harsh weather conditions, improving ROPs,” he said. The goal is to streamline drilling operations, such as tripping, adding precision to complex operations and “making the rig smaller, being more mobile to mobilize and demobilize faster and, and certainly embracing the remote operations.”
The number one goal: reduce joint costs.
The number one solution (so far): robots.
Robologger is Diversified Well Logging’s automated drill cuttings and collection analysis tool.
Robologger is one of the first co-bots (collaborative robots) being used by Diversified as they search for ways to incorporate geosteering and surface measurement while drilling capabilities to their AI software.
Drill cuttings and gas molecules are a free product of drilling operations and contain valuable information about recently drilled rock. Extracting maximum value from them improves drilling, completions, production and economics.
Automated collection provides more consistent data at higher resolution and a potentially lower cost. Higher volume of data improves real-time wellbore placement and provides data to build and identify the chemofacies (rock units that share chemical affinities) of reservoir. Robologger also reduces both the CO2 footprint and the risk of slips, trips and falls by removing manual mudlogging tasks and gets people out of the field.
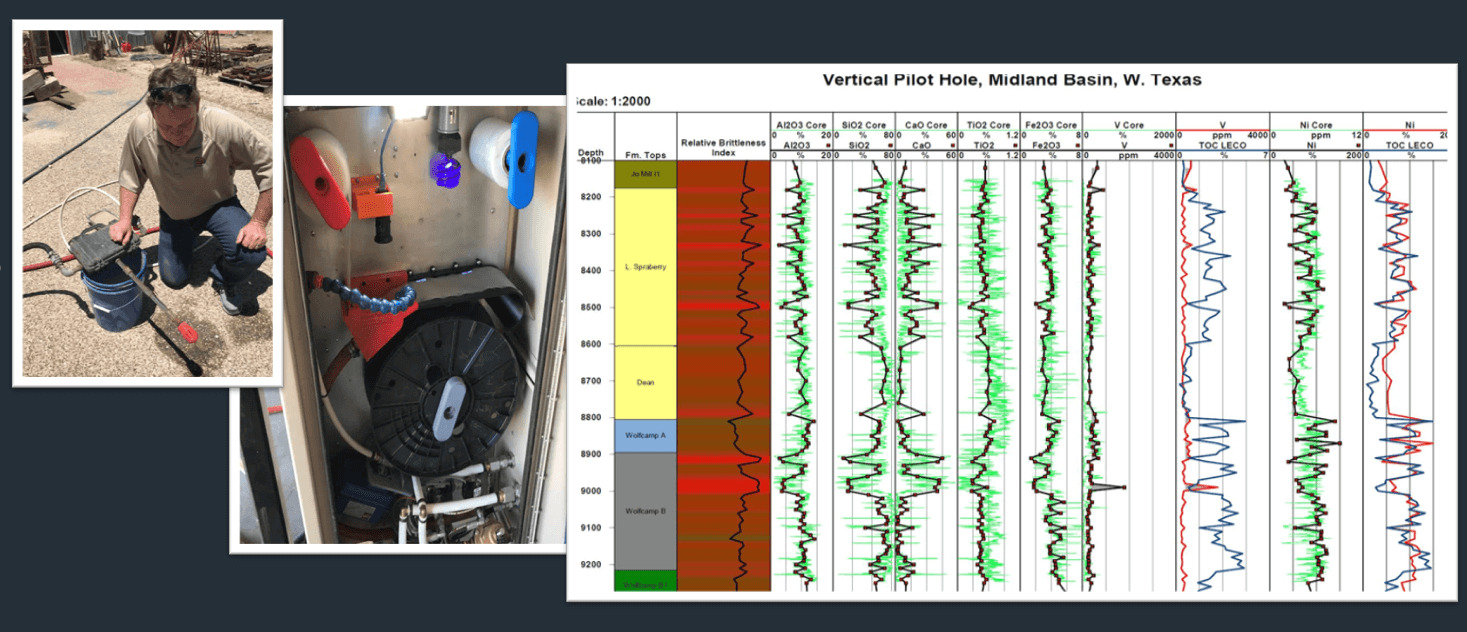
The Robologger consists of an “elephant trunk and possum belly sucking out a slurry of cuttings and liquids, which then come into the delivery system,” said Tonner. The solids and liquids are then separated using a No. 635 micron mesh. From there the cuttings are formed into a 20 gram to 30 gram “hamburger patty of drill cuttings.”
A high-resolution digital picture of the “patty” is taken and it’s stored in the machines collection chamber, where everything is viewable remotely.
But all that glitters isn’t necessarily gold when it comes to artificial intelligence.
According to the McKinsey Global Institute, between 400 million and 800 million people around the world could see their jobs automated by 2030, Tonner said. Both white collar and blue collar jobs are at risk, he said.
Despite his warning about the potential negatives of automation and AI, Tonner is fully behind the revolution.
“Whether you believe or not, that boat's left the harbor,” he said. “And our job is to be good custodians with that and work with it and be smart.”