Although the Permian Basin’s prolific oil and gas fields have been at the forefront of growth for many E&P companies, thanks to the memories of the most recent market downturn, efficiency has remained a focus unlike in past boom and bust cycles. One method operators in this region have determined can help improve productivity is the consolidation of their oil, gas and water assets. However, when doing this, new complexities often emerge since fluids and gases from different reservoirs can combine at the surface, increasing the chance of scale formation from incompatible fluids.
Iron sulfide scale, a common byproduct of oilfield fluids, reduces efficiencies in oil, gas and water production. It also can damage oilfield equipment by acting as a catalyst for pitting corrosion. Iron sulfide damages and remediation costs for an operator can range from tens of thousands to millions of dollars annually.
With water becoming an increasingly valuable commodity in the Permian Basin, as it’s used for reservoir pressure maintenance, fracturing, stimulation and workover, operators must minimize iron sulfide buildup to succeed long term.
To solve this challenge, one Permian Basin operator recently turned to newly developed solutions and technologies that covalently bond to iron under challenging conditions and create a water-soluble as well as lower corrosivity byproduct. In addition, this solution provides operator advantages in water transport, use, reduced bottlenecks and costs.
Understanding the problem
Before it can be combatted, the makeup of iron sulfide must first be understood, as well as how it’s formed, its life cycle and methods to predict/quantify its buildup. Iron is a common component of oilfield metallurgy found in connate water from the reservoir and is introduced during workover, completions and stimulation. Sulfide, on the other hand, is common in oil and gas process streams where native H2S exists or is proliferated through the conversion of sulfate by oilfield bacteria. Iron sulfide can form when sulfide anions attack carbon steel and have the opportunity to agglomerate within the production stream. Though iron sulfide has multiple structures, Iron(II) sulfide is the less stable and amorphous form commonly found in production water.
Understanding iron sulfide’s life cycle requires a traditional holistic approach to properly identify and locate the sources of iron and sulfide from production and/or external water sources that were consolidated. Further, to predict and quantify iron sulfide scale, items such as water analysis, coupons, filters, sight glasses, molecular modeling and more must also be inspected.
Permian case study
A Permian Basin operator earlier this year consolidated water from multiple production sources that were incompatible and experienced physical evidence of iron sulfide in the produced water, in-line filtration and separator interface (Figure 1). This caused poor oil quality, corrosion and flow restrictions, which limited the producer’s overall operational efficiency.
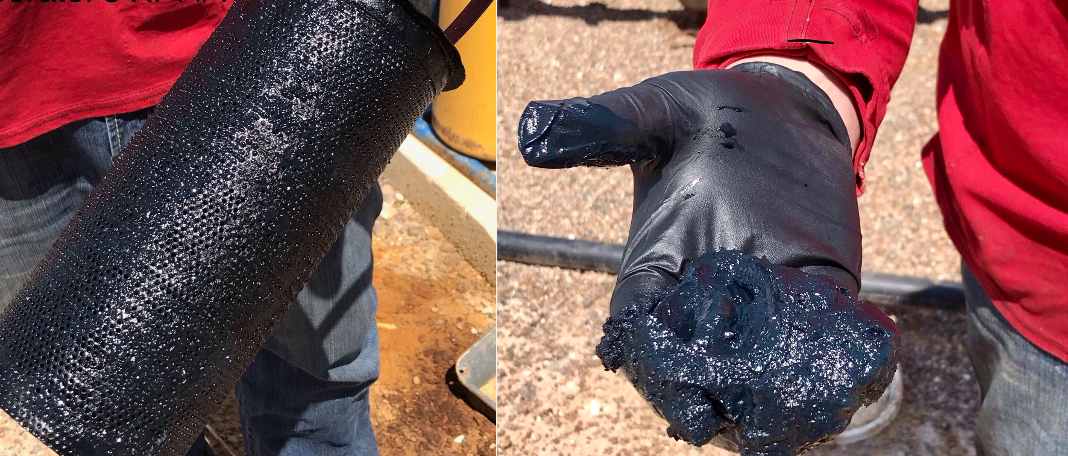
Tetrakis hydroxymethyl phosphonium sulfate (THPS) was being applied to help solve the iron issue, but it also presented the producer with new challenges. This is because THPS, which originated in the 1970s, can chelate iron in low (pH) acidic environments but not high (pH) environments. The latter environment is what is often influenced by man-made additives, chemicals, etc., and as a result, iron typically still remains when THPS is used. Further, THPS introduces sulfate, a known molecule that converts to sulfide, and therefore creates a new iron sulfide issue. It also can form costly barium, calcium and strontium sulfides. This is what the Permian producer was experiencing.
To solve these issues, the operator brought in Solugen Inc., a specialty chemicals manufacturer. Solugen has developed a bio chelate called ScavSol that chelates iron and remediates iron sulfide over a wide pH band as well as forms covalent bonds with iron to produce highly desirable water-soluble and nonreactive molecules. ScavSol provides the industry with an iron control option that is less expensive and has a lower environmental impact compared to existing solutions. It also does not contain sulfates, which alleviates industry concerns of sulfate scale and reactive sulfide species.
Taking a total system approach that involved testing fluids from several points in the process stream, Solugen found iron in the bulk water and discovered iron sulfide in the water streams that were being circulated through the flowline filtration and primary separator. A remote tank battery feeding the process also contained spent liquid from a sulfide scavenging process, which utilized a common scavenger known as triazine—a cyclic nitrogen-bearing aromatic with a high pH (greater than 10). This stream further contributed to the ineffectiveness of THPS controlling the iron sulfide. As the fluids commingled, pH elevated and provided reduced chelation of iron as well as generated iron sulfide.
An approach to control iron and remediate iron sulfide, focused on the inlet to the power water system, was implemented. This method covered both customer objectives regarding remediation and control.
Application
Before ScavSol’s application, total iron was observed in the water phase at levels around 70 ppm as ferric and ferrous, which later converted into iron sulfide. The high concentrations of iron were attributed to the semiclosed power water system and built up over time. Water from this system was then recirculated, and it commingled with newly produced water from adjacent facilities, exacerbating the precipitation of iron sulfide.
For the application, ScavSol injection rates required a 24-hour remediation stage followed by a control stage once physical evidence was eliminated. In-line filters and sight glass were used as physical indicators to monitor the application.
Once the injection point was established, ScavSol was continuously injected at 40 gal/d (272 ppm based on net water produced and circulated) over 24 hours and monitored frequently. After 24 hours, the in-line filters had no precipitated iron sulfide, and the sight glass displayed a clean oil and water interface (Figure 2). Post remediation involved the reduction of ScavSol by 10% every 24 hours to a base injection rate of 3 gal/d (20 ppm). The system was monitored for weeks and has had no returning evidence of iron sulfide.
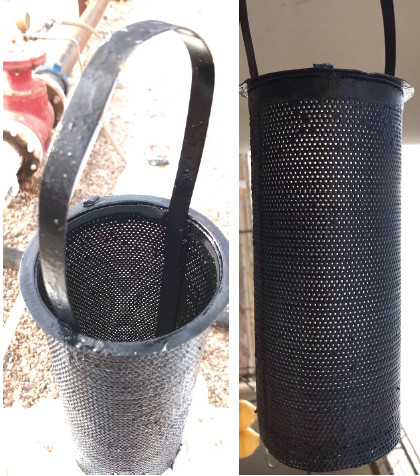
Iron sulfide immediately dropped from 70 ppm to 5-10 ppm after 24 hours of application, giving the operator a level of confidence in removing sources of corrosion and reducing waste in recycling crude oil and water. Specifically, ferrous sulfide ions were immediately reduced in 24 hours and maintained at less than 1 ppm while ferric sulfide compounds reduced over time to less than 10 ppm.
The overall estimated savings to the operator is more than $200,000 per year when accounting for labor, offspec crude oil and chemical spend as well as other operational requirements.
Gaining operational efficiency
The industry’s control of iron, iron sulfide and its byproducts will continue to be at the forefront of operational efficiency where water is used and produced. Systems focused on controlling iron sulfide and allowing operators to streamline the commingling of new fluids will be a key asset in the Permian Basin and other basins for years to come.
Recommended Reading
Tellurian, Institution Investor Agree to New Loan Repayment Terms
2024-02-22 - Tellurian reached an agreement with an unnamed institutional investor to pledge its interest in the Driftwood project as collateral.
Tellurian Executive Chairman ‘Encouraged’ by Progress
2024-03-18 - Tellurian announced new personnel assignments as the company continues to recover from a turbulent 2023.
Mitsubishi Makes Investment in MidOcean Energy LNG
2024-04-02 - MidOcean said Mitsubishi’s investment will help push a competitive long-term LNG growth platform for the company.
Mexico Pacific Appoints New CEO Bairstow
2024-04-15 - Sarah Bairstow joined Mexico Pacific Ltd. in 2019 and is assuming the CEO role following Ivan Van der Walt’s resignation.
Shell’s CEO Sawan Says Confidence in US LNG is Slipping
2024-02-05 - Issues related to Venture Global LNG’s contract commitments and U.S. President Joe Biden’s recent decision to pause approvals of new U.S. liquefaction plants have raised questions about the reliability of the American LNG sector, according to Shell CEO Wael Sawan.