Hydraulic fracturing may seem like a relatively new phenomenon that came along with the shale revolution in 2008, but it’s been around since the 1940s. The first frac jobs were done in summer 1947, and Halliburton completed the first commercial frac in 1949. Since then, the industry has transitioned to massive hydraulic fracturing, with injections of over 300,000 pounds of proppant.
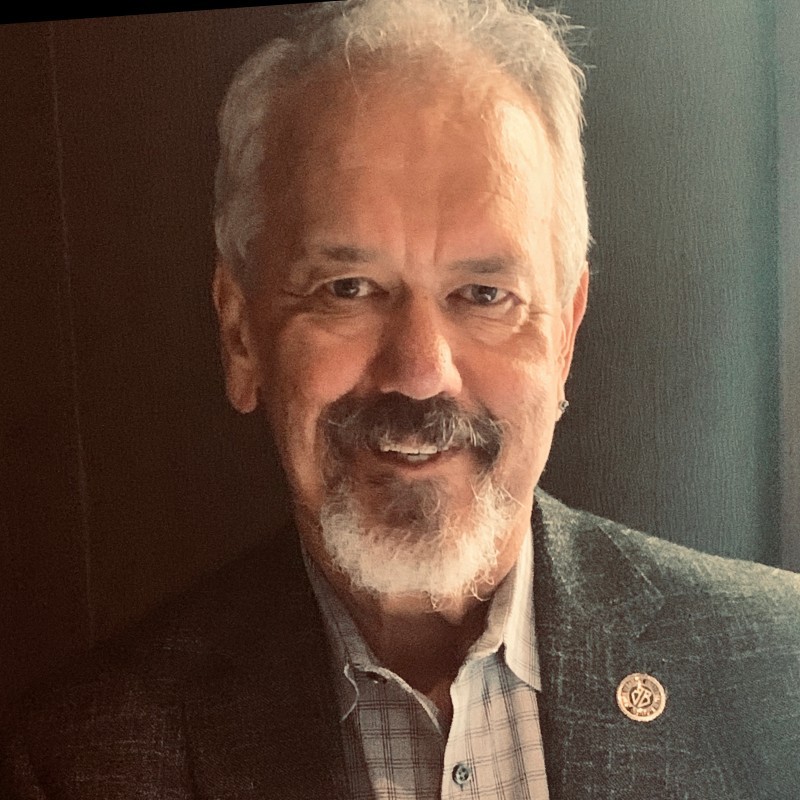
While massive fracturing dominated the industry, a lot of the methods used for drilling those wells were “not conducive to completing shale reservoirs,” Lyle Lehman, founder of Frac Diagnostics and 50-year veteran in the oil industry, told Hart Energy.
“Shale reservoirs were considered to be the source rock for the formation above them. Over geological time, the thought was that the hydrocarbons in the shale would migrate up into the sand or limestone sitting above the shale and swap out some of the water that’s in the sand or limestone,” Lehman said. Mitchell Energy tested this theory in the Barnett Shale in Fort Worth, said Lehman, but they received “iffy” results.
The “iffy results” were due to Mitchell Energy pumping traditional, thicker fluids into the well to stimulate it. While the well was stimulated, it was much harder to clean up, making the well much harder to complete and not economically viable. It wasn’t until Mitchell, which was acquired by Devon Energy in 2002, returned with a thinner fluid that the wells in the Barnett could be economical.
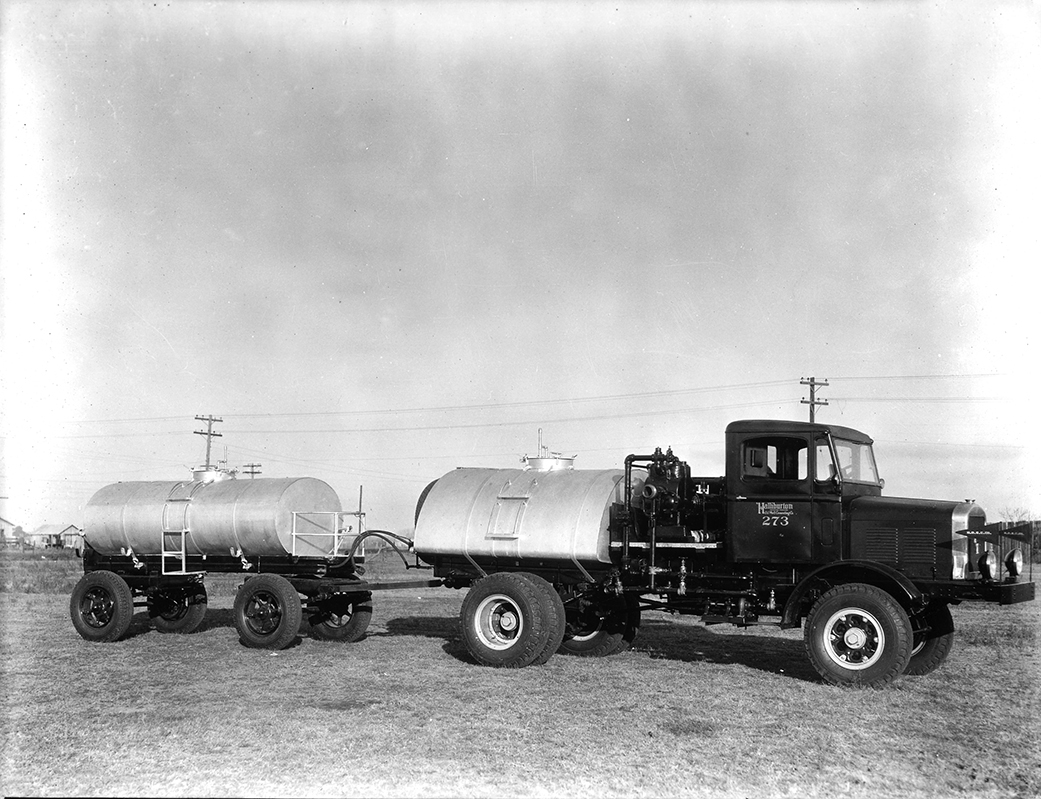
Horizontal drilling
Eventually, production from shale reservoirs became more common due to the introduction of horizontal wells.
“The first horizontal wells that were fractured in the North Sea were in the late ’80s and early ’90s. So, the sliding sleeve, the frac sleeve technologies were some of the first things, but really what’s blown the North America market open has been the … plug and perf operations,” Ron Dusterhoft, Technology Fellow at Halliburton and 40-year oil industry veteran, told Hart Energy.
Zonal isolation techniques like “plug and perf” cause a higher density of fractures by increasing the number of fractures per well and reducing the distance between those fractures.
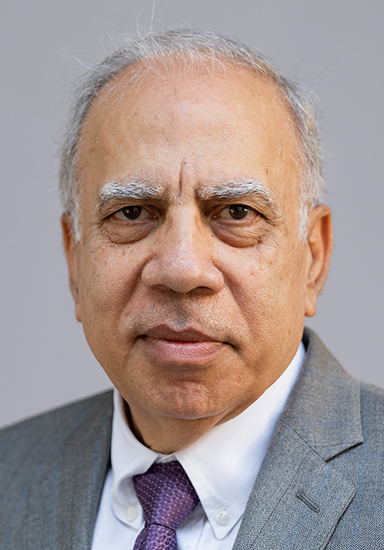
“You have packers or a bridge plug. You put it in, you fracture a well, then you move,” said Mohamed Soliman, department chair and The William C. Miller endowed chair at the University of Houston and named a 2023 Legend of Hydraulic Fracturing by the Society of Petroleum Engineers.
“When we started fracturing horizontal wells, we created fractures one at a time,” he said. “You go from toe to heel; you do it near the toe, then you move, you put another bridge, you plug, you perforate the oil cased wells. Then you perforate, you create one fracture, another bridge, you plug and perforate, and so on and so forth.”
The new techniques create multiple fractures at a time, making the process more efficient and allowing for numerous fractures to intersect a horizontal well.
Sliding sleeve is newer than plug and perf and speeds up multi-stage frac jobs because it allows multiple stages to be fractured with a single pumping session. Sliding sleeve tools are permanently placed in open holes with mechanically actuated sleeves before perforation occurs. The constant downhole pressure cuts out the plug, perf and repeat process, reducing completion time.
Plug and perf, and sliding sleeve completions were pivotal in the development of unconventional resources such as shale because they were more effective at opening wells than many of the previous methods. They were especially effective in horizontal drilling, which further advanced the oil industry.
Horizontal wells proved much more effective than vertical wells in producing oil from tight formations beds. Those beds are usually nearly horizontal, so horizontal wells have much larger contact areas with the target formation.
“If you know the orientation of those natural fractures, drilling horizontal wells will give you a lot higher probability that you intersect those fractures,” Soliman said.
Shale revolution
Eventually, the wider adoption of horizontal wells led to the shale revolution in 2008. Prior to that, the U.S. economy was highly dependent on oil imports from countries like Venezuela and Saudi Arabia. Now the U.S. is a net exporter of crude oil.
“Mitchell Energy in the Barnett Shale gets all the credit for the early shale wells because what we found early on … is that the tight gas technology, the fracturing for tight gas, did not seem to work in shale, and we didn’t really understand why,” Dusterhoft said. “And if you look at what Mitchell did, they transitioned into a water frack, got rid of the polymer … and as a result, that really was what opened the floodgates on the shale market.”
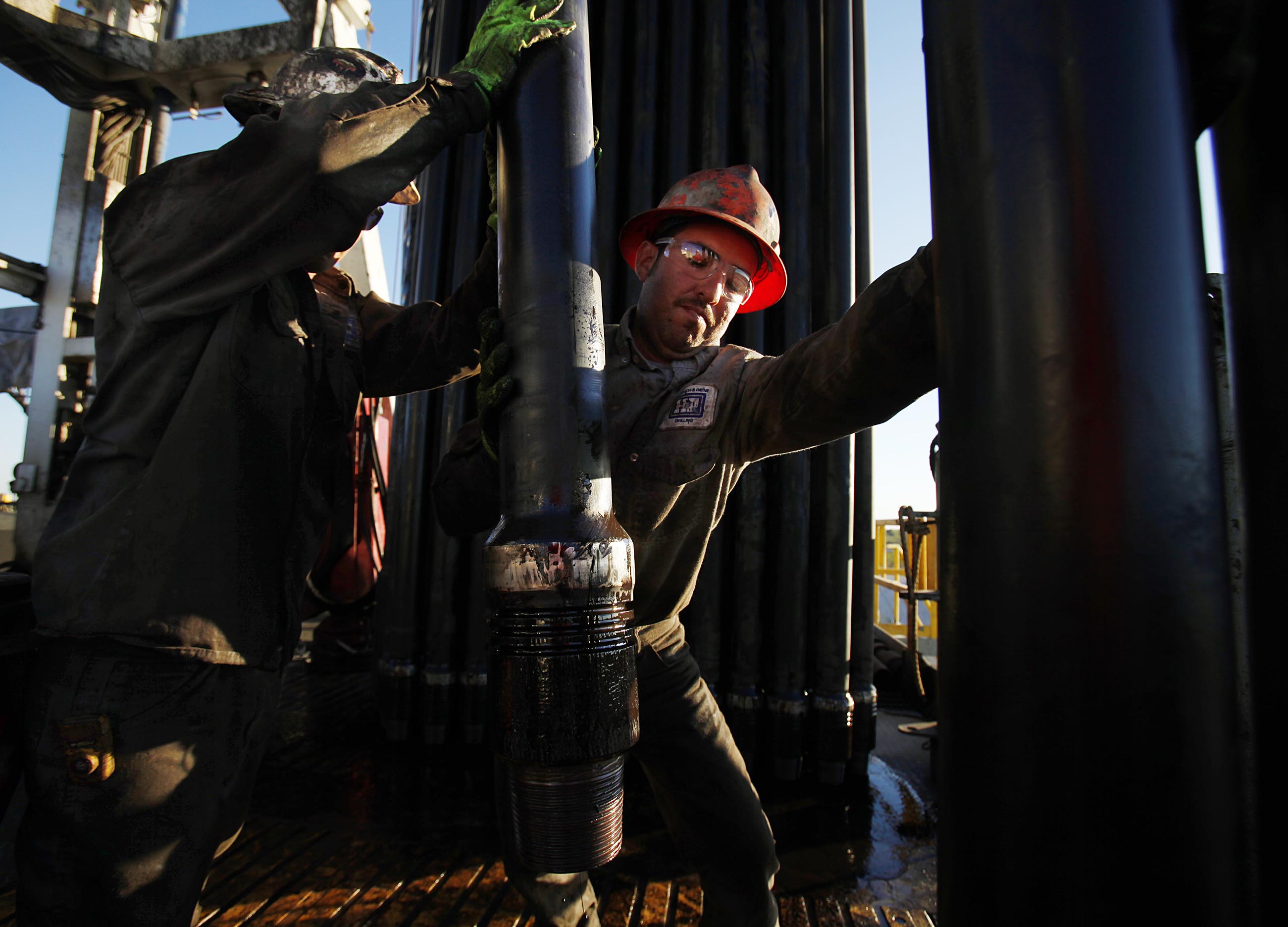
Another reason shale development took off was the implementation of drilling data analysis technology. Adding computer technology to the drilling process the operator to predict the path a newly formed fracture might take. It could also determine the stress contrast of the well and enable operators to identify the best reservoirs.
“The incorporation of well data [helped the operator] understand where to place fractures along the horizontal so that they would all open equally,” Lehman said. “Just because I put a perforation here, here and here, it doesn’t mean they will all open up the same and take the same amount of fluid. We have to understand what the stress is along the wellbore so that we move those perforations around and place them in a lower stress area so that the stress differential is minimal.”
Well data also makes the well stimulation process easier through the use of “proxy” data, a form of AI that takes drilling data and converts it to formation properties—particularly rock strength—so that the treatment of the well can be performed optimally.
But even with all the benefits that collecting well data provides, managing it can be difficult.
“Data is a wonderful thing, but it’s also a huge monster that we have to deal with,” Dusterhoft said. “The challenge we have today is with the unconventional fracturing. We probably have an order of magnitude—maybe two orders of magnitude—more data coming in than we ever did in the past. So, managing that data and putting it in a useful format is a challenge and we’re making steps there.”
Operators are looking to use data through automation, machine learning and AI. Halliburton has been working on this technology since the 1990s, Dusterhoft said. Halliburton’s automatic remote-control equipment allowed operators to run jobs without having to put people on the trucks or in the red zones.
The current mission in the fracking space is achieving sustainability. Even with the energy transition, production from oil and natural gas is still incredibly important to the energy industry, so operators are focused on safer ways to produce.
“Chemical containment, fluid containment are things that we’ve advanced tremendously on, but also emissions reduction, and things like dual fuel to power our trucks,” Dusterhoft said.