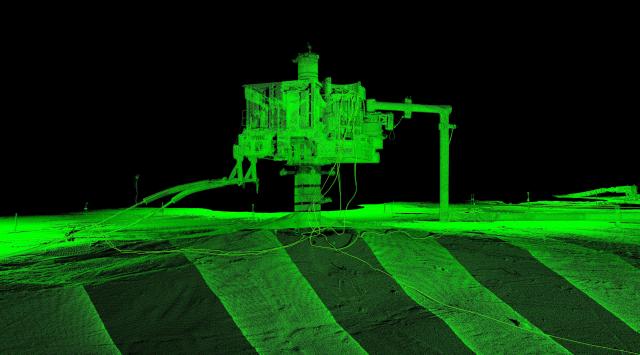
A point cloud image of a subsea production well is generated with the data acquired during the subsea LiDAR scanning process. (Source: 3D at Depth)
Light detection and ranging (LiDAR) technology is used to acquire highly sophisticated 3-D models of structures and natural features. The concept is simple: illuminate a target with laser light and measure how long it takes for the reflected signal to return to the source. For many years the technology was used in terrestrial and airborne surveying, space mapping, and weather. It has now become an industry standard due to the proven ability to create repeatable and accurate datasets.
LiDAR’s features compared to other “triangulation” laser technology includes unlimited range—hence the space applications and the ability to extract critical information from complex 3-D datasets. As the technology continues to expand into other applications like the use of unmanned aerial vehicles or drones to perform remote asset inspection, subsea can now be added to LiDAR’s list of survey and inspection capabilities with the development of the world’s first commercially available subsea 3-D laser scanning system by 3D at Depth.
3D at Depth’s SL1 and SL2 subsea laser technology was fast-tracked from invention and pilot programs through commercialization due to the support of the Research Partnership to Secure Energy for America (RPSEA) Ultra-Deepwater Research Program.
Considered the world’s first subsea 3-D LiDAR company in the oil and gas industry, 3D at Depth recently completed another world’s first, delivering subsea survey and inspection data to 3-D print an accurate 1:1 physical model of a damaged well part. The ability to deliver this type of complex and accurate data to subsea operations and inspection has positive implications across a wide range of applications subsea. But before the technology could “beam,” it had to prove its reliability and capability through tests and pilots made possible through its selection as a research project under RPSEA.
Getting started
The idea for subsea LiDAR came from above.
“While I was in the aerospace industry, I could see firsthand the incredible impact LiDAR technology was bringing to the remote sensing of soft and hard targets, including mapping, surveying and inspection. I watched the number of value-add applications grow for the technology for multiple industries including terrestrial, airborne and aerospace,” said Carl Embry, managing director of 3D at Depth. “And then we looked at the subsea world and saw an open market. So 3D at Depth approached the problem from the technology side and said, ‘This is something we can build,’ and we began the process of building it.”
It was through identifying the challenges encountered with topside surveying, construction, retrofits, as-built analysis and decommissioning that the 3D at Depth team could see that terrestrial and airborne LiDAR was gaining considerable traction to address the same issues that existed subsea.
“It appeared to be a good opportunity, and the market was proven for several terrestrial applications, with lots of tools and software being developed along with best practices and procedures. We weren’t completely creating the wheel, as a lot of the infrastructure was there,” Embry said. “What was really needed was the specialized hardware to go subsea. We have since come to realize subsea is different enough compared to topside that new best practices and procedures needed to be developed. But the hardware was the key; it was the first stepping stone required to make it possible.”
3D at Depth was awarded a RPSEA contract in January 2011 to bring high-resolution 3-D laser imaging for inspection, maintenance, repair and operations from a laboratory setting into an underwater environment for the oil and gas industry. Included in the project were two underwater trials that demonstrated the feasibility of using LiDAR technology in a subsea environment. To accomplish this, 3D at Depth worked with CDL Inc. and UTEC Survey to marinize a LiDAR acquisition system. Thirteen months later at the conclusion of the project’s Phase 1, the world’s first demonstration of a subsea LiDAR occurred, with 3-mm measurement accuracy at greater than 8 m (26 ft) for an underwater laser sensor integrated with a ROV.
Phase 2 saw the development of a LiDAR system capable of working at greater water depths, with the first successful open water trial performed in March 2013. A primary goal of this phase was the development of a sensor that could perform and survive multiple deployments into an ultradeepwater environment.
In the time since the company has gone on to use its LiDAR system on a variety of surveying and mapping projects in the Gulf of Mexico, Australia, the North Sea, the Mediterranean, the Pacific Ocean, the Caribbean and elsewhere, including the USS Arizona at Pearl Harbor. As of press time the company had completed more than 100 projects and 175 spool-metrologies worldwide.
3-D model project
Fugro and 3-D at Depth announced in late October 2016 the use of subsea 3-D data to 3-D print a physical model of a damaged wellhead part. It was the ability to use accurate spatial data in the fabrication of the subsea part, according to a press release. This subsea part fabrication was part of a larger project conducted in early 2016 using 3D at Depth’s SL 2 technology and point cloud software on a well abandonment project offshore in Oceania.
The plugged and abandoned wells were located in a water depth of 110 m (361 ft) and were drilled decades earlier and suspended at the time of drilling, the release said. Access to accurate data on the manufacture and specifications of these wellheads was limited due to their age. The 3D at Depth system was selected to acquire the detailed measurement needed to determine feasible abandonment options.
Fugro’s Rem Etive multiuse vessel was fitted with two work class ROVs, with one of the two ROVs equipped with the SL2 subsea LiDAR system mounted on its crash bar. Near real-time data were sent to the operator on the vessel using a fiber-optic multiplexor.
About 44 million datapoints were collected at the well in 13.5 hours. The LiDAR laser data were processed using point cloud processing tools to compute the spatial relationships, measurements and orientations of the seabed structures. The resulting deliverables included a 3-D point cloud database, a dimensional report for each well, computer-aided design (CAD) files and a 360-degree animation of each well, modeled from the point cloud, the release said.
To create a 1:1 model for the design of an appropriate hot tap connector, a 3-D print of the top of the well with its damaged stub at full scale was required. As the large size of the well cap structure made the cost prohibitive, a hybrid computer numeric control machining process combined with a 3-D print of the damaged part was proposed by 3D at Depth as a viable alternative solution.
The first step was to reprocess the point cloud data from the top of the well and then create 3-D CAD models of the separate parts. However, this process proved more challenging than first thought due to the complexity of the shape. For this particular part the auto meshing algorithms, which convert point clouds into surfaces, did not perform well, and as a result the CAD model was developed manually, which is also common when modeling complex shapes from terrestrial laser scans, the release noted.
The part was then 3-D printed by means of fused deposition modeling technology using acrylonitrile butadiene styrene thermoplastic material. One of the other two computer numeric control machined parts was made from acetal and the well cap from ultrahigh-molecular- weight polyethylene.
Editor’s note: Visit rpsea.org/projects/09121-3300-06 for detailed project reports and presentations on the “High Resolution 3-D Laser Imaging for Inspection, Maintenance, Repair and Operations” project.
Contact the author, Jennifer Presley, at jpresley@hartenergy.com.
Recommended Reading
Oceaneering Won $200MM in Manufactured Products Contracts in Q4 2023
2024-02-05 - The revenues from Oceaneering International’s manufactured products contracts range in value from less than $10 million to greater than $100 million.
E&P Highlights: Feb. 5, 2024
2024-02-05 - Here’s a roundup of the latest E&P headlines, including an update on Enauta’s Atlanta Phase 1 project.
CNOOC’s Suizhong 36-1/Luda 5-2 Starts Production Offshore China
2024-02-05 - CNOOC plans 118 development wells in the shallow water project in the Bohai Sea — the largest secondary development and adjustment project offshore China.
TotalEnergies Starts Production at Akpo West Offshore Nigeria
2024-02-07 - Subsea tieback expected to add 14,000 bbl/d of condensate by mid-year, and up to 4 MMcm/d of gas by 2028.
US Drillers Add Oil, Gas Rigs for Third Time in Four Weeks
2024-02-09 - Despite this week's rig increase, Baker Hughes said the total count was still down 138 rigs, or 18%, below this time last year.