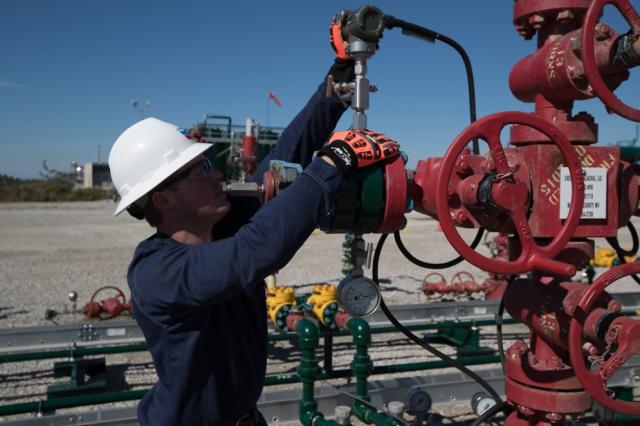
Several major global oil producers, such as Chevron, have established goals to either significantly reduce or eliminate carbon emissions throughout their operations. (Source: Chevron Corp.)
[Editor's note: A version of this story appears in the June 2020 edition of E&P. Subscribe to the magazine here. It was originally published June 1, 2020.]
By now, the situation in the oil and gas industry is a familiar one—the COVID-19 pandemic has weakened global energy demand by nearly 30 MMbbl/d less than last year, according to the International Energy Agency (IEA), with only incremental recovery expected. The historically weak demand has resulted in a global supply glut, pushing oil prices down and forcing producers worldwide to shut in wells and shut down rigs.
But despite the dire circumstances, the world still needs oil, and it will continue to need reliable supplies of energy as it begins the slow process of recovery. Amid these challenging circumstances, oil producers still must abide by state and federal emissions regulations, and many are resolute in maintaining their own internal goals of reducing emissions.
In fact, during the midst of the global energy crisis, both Shell and Total announced new efforts to meet their individual goals of net zero greenhouse-gas (GHG) emissions by 2050 or sooner, with Shell’s efforts among the most ambitious.
“With the COVID-19 pandemic having a serious impact on people’s health and our economies, these are extraordinary times,” said Ben van Beurden, CEO of Royal Dutch Shell, in a release announcing the company’s plans. “Yet even at this time of immediate challenge, we must also maintain the focus on the long term.”
According to the IEA, “Methane emissions from the oil and gas sector reached close to 80 Mt, or 2.4 billion tonnes of CO2 equivalent [CO2e], in 2017.” Energy producers around the world ranging from small independents to supermajors have taken on the challenge of reducing the industry’s carbon footprint, and the services market has answered the call with innovative technologies to help companies achieve their goals.
A supermajor’s reduction plans
Chevron is among the multitude of supermajors that have announced plans to either significantly reduce or move to net zero emissions over the next few decades. In October 2019, Chevron established new goals to reduce net GHG emission intensity from its upstream oil and natural gas operations by lowering upstream oil net GHG emission intensity by 5% to 10% and upstream natural gas net GHG emission intensity by 2% to 5% from 2016 to 2023. The company also is targeting reduced methane emissions intensity by 20% to 25% and flaring intensity by 25% to 30% from 2016 levels to 2023.
Sean Comey, senior adviser of external affairs with Chevron, said the company’s timing is aligned with the milestones set in the Paris Agreement on climate change.
“Effectively managing climate change risks and exploring new lower-carbon business opportunities is part of our responsibility to our stockholders,” he said. “Reducing greenhouse-gas emissions is a global issue that requires global engagement and action. We work with policymakers to design balanced and transparent GHG emissions reductions policies that address environmental goals and ensure consumers have access to affordable, reliable and ever cleaner energy.”
Chevron’s efforts at reducing emissions include carbon capture, utilization and storage (CCUS), methane emissions reductions, flaring reduction and increasing its use of renewable energy. The company’s emissions reductions initiatives include monitoring and verifying the integrity of its wells and production equipment with regular inspections and safety tests, Comey said.
“We have retrofitted or replaced more than 1,000 continuous high-bleed pneumatic controllers from our onshore U.S. facilities with low-emitting or noncontinuous-bleed technologies to reduce emissions,” he said.
In addition, Comey explained that where electricity is available, electric and air-driven controllers and pumps are used, which do not emit methane when actuated. He said Chevron has piloted several emerging technologies and remains encouraged that more effective and efficient tools will improve leak detection and repair performance in the future.
According to the company, methane accounts for about 5% of Chevron’s total GHG emissions. About one-third of the 5% is considered fugitive emissions, or leaks from equipment and piping, Comey said.
“We have developed internal country-specific plans to minimize gas flaring, and we are a member of the World Bank-led Global Gas Flaring Reduction Partnership,” he said. “In 2019 Chevron had one of the lowest venting and flaring rates of any company in the Permian Basin located in Texas and New Mexico. Chevron flares natural gas only when required for safety and operational purposes and in areas where pipelines and other alternatives for transporting gas do not exist.”
Tracking emissions
While producers around the globe have set out ambitious emission reduction plans, the technologies to help them achieve those goals are surfacing from service providers across the industry.
Emerson Automation Solutions offers an emissions reporting system geared toward helping companies track, manage and report GHG emissions from their equipment and assets throughout their operations. Emerson’s six-step leak detection and repair program structure identifies and monitors select components before any reparative actions are taken. According to the company, the intent of the system is to consolidate the sources of emissions information from across an operator’s enterprise and consolidate it into a coherent manner.
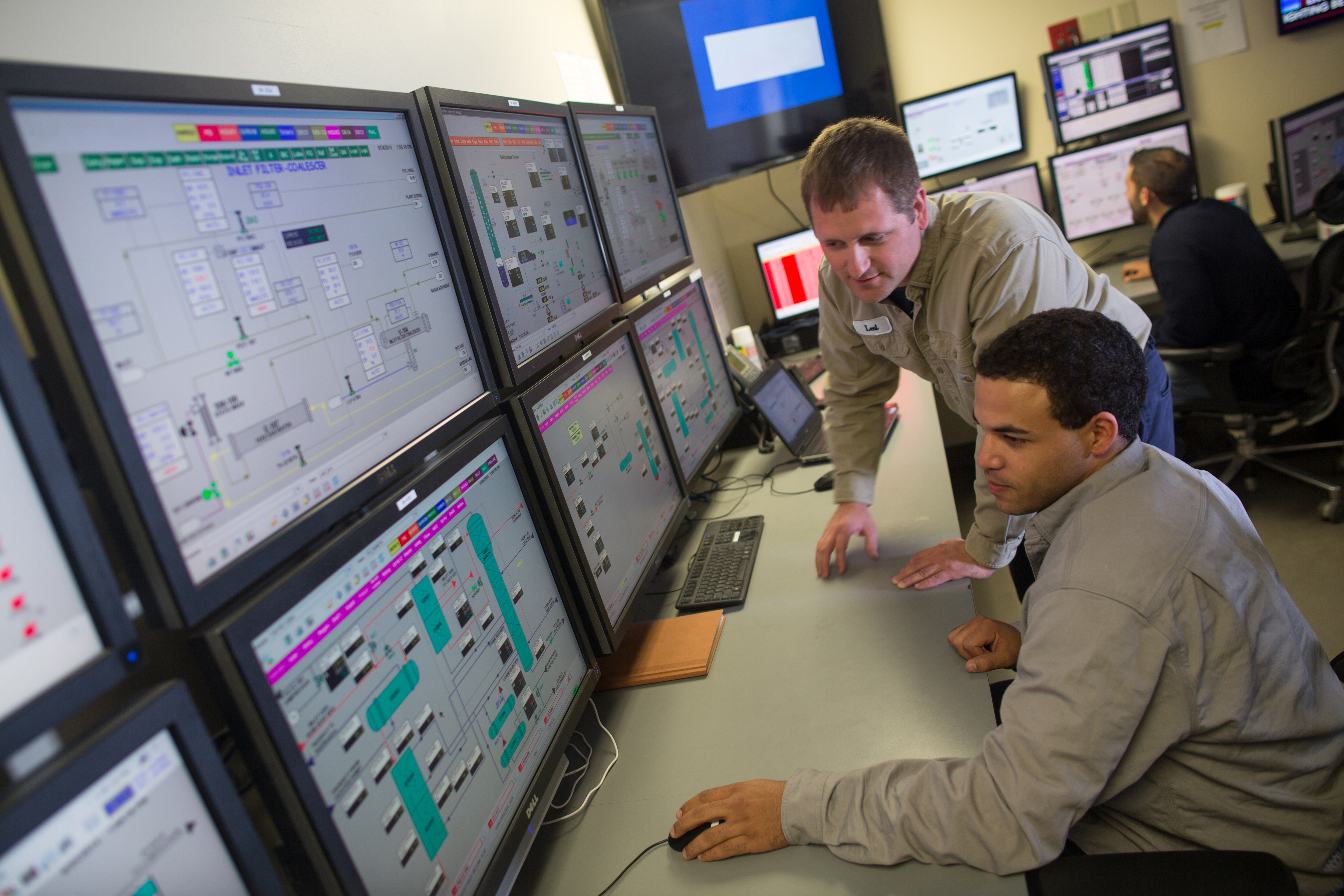
Automation Solutions)
“We started working on these types of solutions in Canada, where the regulators put more pressure on operators to reduce emissions,” said Manuel Arroyo, oil and gas manager of industry programs with Emerson. “One of the challenges those operators had was they operate assets in multiple locations. Not everything was in a single location. And every location had its own reporting system or database. It was very difficult for them to report a summary of all of their solutions.”
To consolidate all of that information, Arroyo said Emerson integrated all of the data sources and created a map where the operators can see all of their different assets in the different locations to increase visibility and keep track of those emissions. Emerson’s data management tool presents a hierarchy of assets across different locations and geographies, and it tracks, manages and reports total emissions, organized into operational and fugitive sources.
Upstream companies often have two sources of emissions—operational and fugitive. Operational emissions are those resulting from the day-to-day operations of oil and gas production, while fugitive emissions are those caused by equipment failures such as leaks.
“Fugitive emissions are where operators often focus their action plans,” Arroyo said. “They have to repair where emissions are emitting from. A lot of customers have started using pneumatic devices. They get the gas coming from their production, and in their normal operations they replace those devices. And for what they cannot replace, they repair.”
Arroyo explained that as a result of there being two different types of emissions, companies often have two different isolated databases—one for operations and one for emissions.
“Between operational emissions and fugitive emissions, everything starts to comingle into one single database,” he said. “Operational emissions are not an indication of asset health. If your asset health isn’t good, you’re going to have two different situations. You’re going to increase your emissions and you’re going to reduce your reliability of that asset. We are seeking to solve those two actions to reduce emissions.”
Visualizing emissions management
Understanding and managing the proliferation of data collected during a company’s emissions management programs often presents challenges with data organization and comes with steep learning curves. But visualizing problem areas of methane leaks can save time and money. Based on technology designed in collaboration with the U.S. Department of Defense, Geosite serves satellite imagery that detects methane emissions at scale.
“There is a chasm between the data and the end user,” said Burke Greer, lead geographical information systems scientist with Geosite. “It’s really hard for people, especially those who don’t have the training, to take those new data sources and use them in their workflows. One of the things that we’re doing at Geosite is making it easier for people to integrate real data into the workflows that they’re doing, and methane emissions are an example of that.”
Geosite’s technology combines a variety of data sources like satellite imagery, sensor data and drone mapping into an interactive operating system. It provides the ability to send workers in the field to the right location to mitigate methane emission leaks.
“At its heart, Geosite is a map,” Burke said. “It’s a map that contains spatial data and information. The way that we’ve structured our map, it’s able to leverage cloud technology. That means a lot of people in your organization can work with, access and see the same data and information on the map. For a use case like methane, what that means is we type in satellite-derived methane emission estimates that are visible on the map. And your team that’s out in the field can see those data.”
Burke explained that if a methane emission cloud is visible in the satellite data, the team working in the field can see the emission cloud in the map with different data layers integrated into the visible cloud. A team could then visit the site, add video imagery and more high-resolution data to further enhance the available information.
“For something like methane, our platform is really set up for integrating different data sources so you can take those safety data and emission data from the methane satellite imagery sources and use those in your workflows on the ground,” Burke said.
Mitigating flaring
One of the largest impediments to widespread emissions management success in the upstream oil and gas industry is the flaring of natural gas. Operators burn off the excess natural gas they can’t sell and also burn off methane in the gas in the process. But flaring also releases CO2 into the atmosphere. According to the U.S. Energy Information Administration, Texas totaled 0.65 Bcf/d while North Dakota amassed 0.4 Bcf/d of flared gas in 2017.
For companies looking to meet either internally established goals or regulatory rules for flaring reductions, technologies that detect carbon emissions and reuse associated gas have emerged as adaptable options.
Crusoe Energy System’s Digital Flare Mitigation system converts natural gas that would otherwise potentially be flared into electricity to power energy-intensive computing at the well site. Crusoe president and co-founder Cully Cavness explained that the flare mitigation system includes containerized mobile modular data centers and power generation modules located at the well site, which are fueled by the otherwise flared natural gas.
“The natural gas goes into the power generation module and is the fuel for a generator,” Cavness said. “A piece of equipment that is very common in the oil field is power generation, which is fueled by natural gas or diesel. We’re using a custom-designed and configured type of power generation equipment. Basically, it’s reciprocating engines or turbines.”
Cavness explained that power is generated by consuming natural gas and combusting it in the power generation process, generating electricity, which is then used to power the modular data center.
“Then that is distributed to a customized electrical distribution system that powers hundreds of servers inside of this containerized data center, and those are very energy intensive servers doing things like blockchain processing,” Cavness said.
According to Crusoe, the Digital Flare Mitigation system can reduce methane emissions by up to 95% and CO2e emissions by 39%.
“At the end of the day, we’re looking for really energy-intensive, constantly running computing processes so we can have a high demand for energy,” Cavness said. “That’s what pairs well with the flaring—it’s a high energy waste pairing with the high energy demand.”
Funding innovation
Securing funding for operations and new technologies in the upstream industry was challenging even before the COVID-19 pandemic, and it remains a substantial challenge amid the energy industry collapse. But the Oil and Gas Climate Initiative’s (OGCI) Climate Investments fund maintains a long-term view of emissions management technologies.
The OGCI Climate Investments is a $1 billion-plus fund that invests in technologies designed to help decarbonize, among others, the oil and gas industry. The fund supports technologies and applications that reduce methane and CO2 emissions and can recycle and store CO2, according to the OGCI website.
In April, the OGCI fund, along with others, provided Qnergy with $10 million in Series B funding to accelerate the deployment of its compressed air pneumatics product, CAP3. The application, which couples Qnergy’s remote power generators with air compressors, offers a low-emission alternative to gas pneumatic devices, which vent spent gas into the atmosphere and are often used in upstream oil and gas operations.
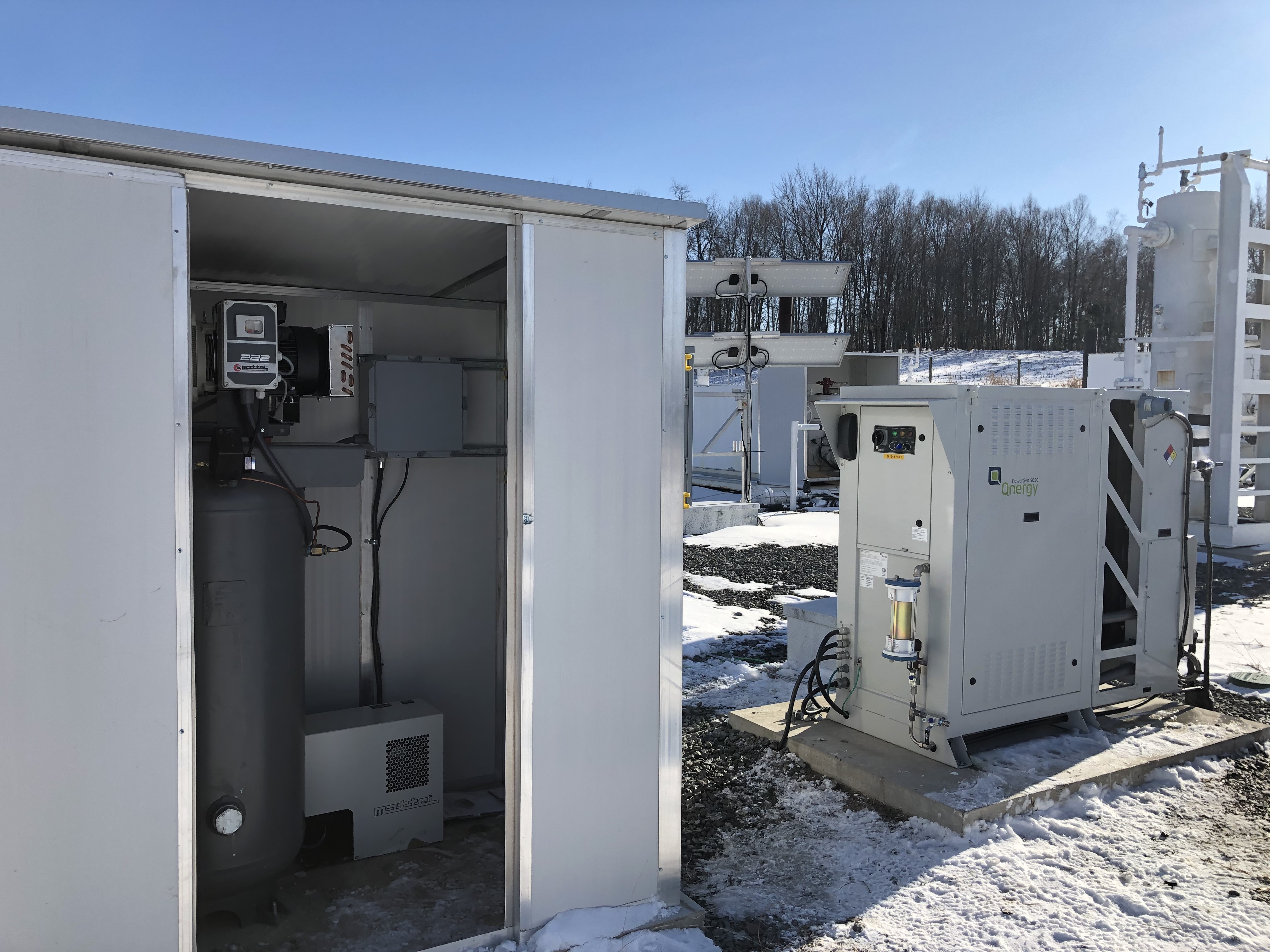
“Gas pneumatics are responsible for about 20% to 40% of the gas industry’s supply chain in North America,” said Qnergy CEO Ory Zik. “And methane is a very potent greenhouse gas at 25 or even 85 times more than CO2, and the gas industry is very sensitive to those methane emissions. Pneumatic devices are among the easiest to solve. The same technology that is used for these pneumatic devices can be used when you use compressed air or clean air as the source of power. All you need conceptually is a power generator that compresses the air and replaces natural gas or methane as a source of power with compressed air.”
Zik explained that Qnergy’s technology is based on the Stirling engine, which generates electricity by a cyclic compression of air and gas at differing temperatures. Qnergy’s CAP3 system combusts the normally vented methane.
“The oil and gas industry is focusing aggressively on reducing methane emissions throughout the supply chain,” Zik said. “About 20% of those emissions are low-hanging fruit that can be updated through pneumatic devices. After focusing intensely on fugitive emissions through leak detection and correction, now the next stage is venting, and this is what this technology serves.”
Sam Gabbita, OGCI Climate Investments venture director, said Qnergy’s technology was appealing to the fund because it offered low-cost and reliable energy that can be applied at scale across much of the industry.
“There are about 250,000 pneumatic devices just in the U.S. alone,” Gabbita said. “And these are emitting about 14 million tons of CO2 when you convert the methane equivalent. So the opportunity to use Qnergy’s remote power engine to basically run compressed air rather than typical methane was a beautiful marriage. We liked the fact that there was established technology, and we loved the fact that we could use this established technology to decarbonize an important part of the oil and gas value chain.”
Recommended Reading
NOG Closes Utica Shale, Delaware Basin Acquisitions
2024-02-05 - Northern Oil and Gas’ Utica deal marks the entry of the non-op E&P in the shale play while it’s Delaware Basin acquisition extends its footprint in the Permian.
California Resources Corp., Aera Energy to Combine in $2.1B Merger
2024-02-07 - The announced combination between California Resources and Aera Energy comes one year after Exxon and Shell closed the sale of Aera to a German asset manager for $4 billion.
DXP Enterprises Buys Water Service Company Kappe Associates
2024-02-06 - DXP Enterprise’s purchase of Kappe, a water and wastewater company, adds scale to DXP’s national water management profile.
Pioneer Natural Resources Shareholders Approve $60B Exxon Merger
2024-02-07 - Pioneer Natural Resources shareholders voted at a special meeting to approve a merger with Exxon Mobil, although the deal remains under federal scrutiny.
Parker Wellbore, TDE Partner to ‘Revolutionize’ Well Drilling
2024-03-13 - Parker Wellbore and TDE are offering what they call the industry’s first downhole high power, high bandwidth data highway.