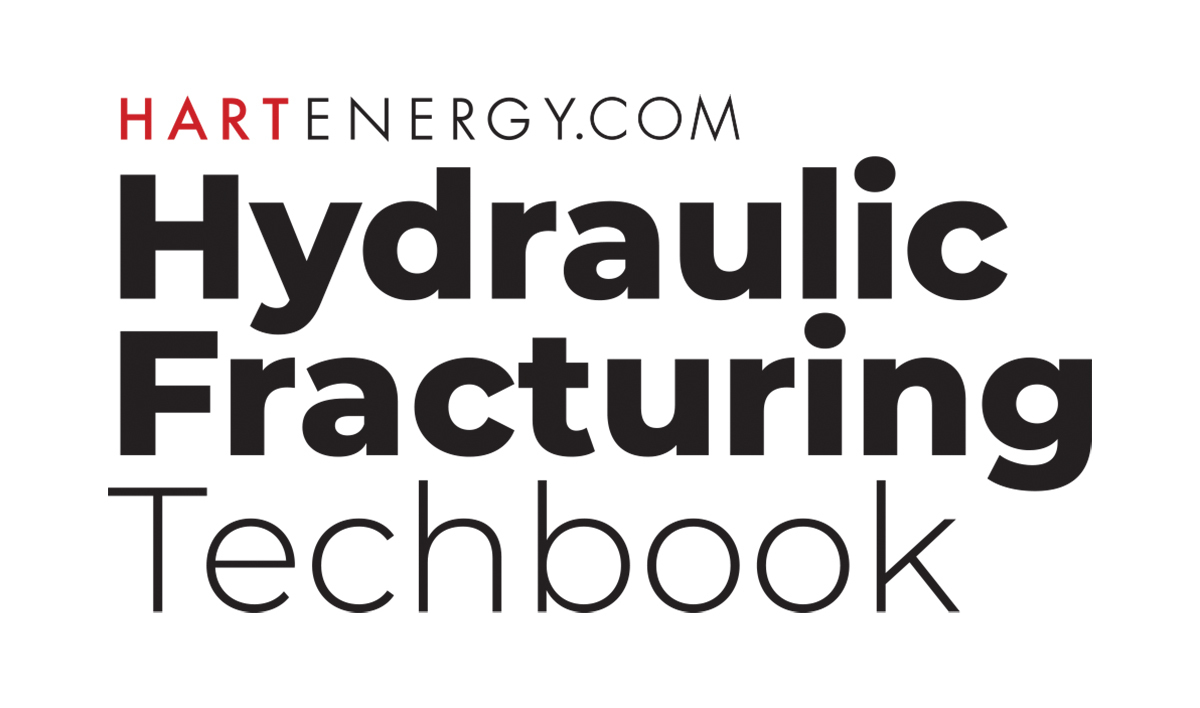
Proppants, the sandy heroes of the shale revolution, are rising in demand for offshore wells, particularly in the Gulf of Mexico (GoM)’s Lower Tertiary Wilcox Trend.
The Lower Tertiary’s reservoirs are sandstone, not the more common offshore carbonate reservoirs that require acid fracturing to maintain permeability. And the play is steadily gaining the attention of offshore operators.
Alexander Pirogov, senior fracturing engineer with Baker Hughes’ global production enhancement product line team, said one of the chief trends he’s observed is that offshore operators are increasingly starting to produce wells tapping the Lower Tertiary.

“They’re going after these tighter, deeper, hotter formations, versus the old, established, maybe slightly shallower, unconsolidated formations they have been going after for decades,” Alexander Pirogov, senior fracturing engineer with Baker Hughes’ global production enhancement product line team, told Hart Energy. “That means that we are shifting to a more complicated, more complex type of completion.”
Because these tend to be larger jobs, he added, the offshore logistics become more complicated. That makes it more important than ever to plan from the perspective of fracturing, not just production.
“Previous wells would be drilled for production predominantly, and maybe have some sort of sand-control process in place,” he said. “But now they’re planning for a fracturing job targeting these lower permeability type of reservoirs.”
That signals a shift to operators pre-planning wells with stimulation in mind, compared to past operations in which they largely only anticipated production, he said.
And they also are keeping in mind the potential for later workovers, he added.
Lower Tertiary formations require more exposure to the reservoirs, said Marty Usie, pressure pumping North America offshore service delivery technical manager at Baker Hughes. The longer fracture length requires more proppant and fluids, he said, but operators have to contend with higher pressure and temperatures in these formations.
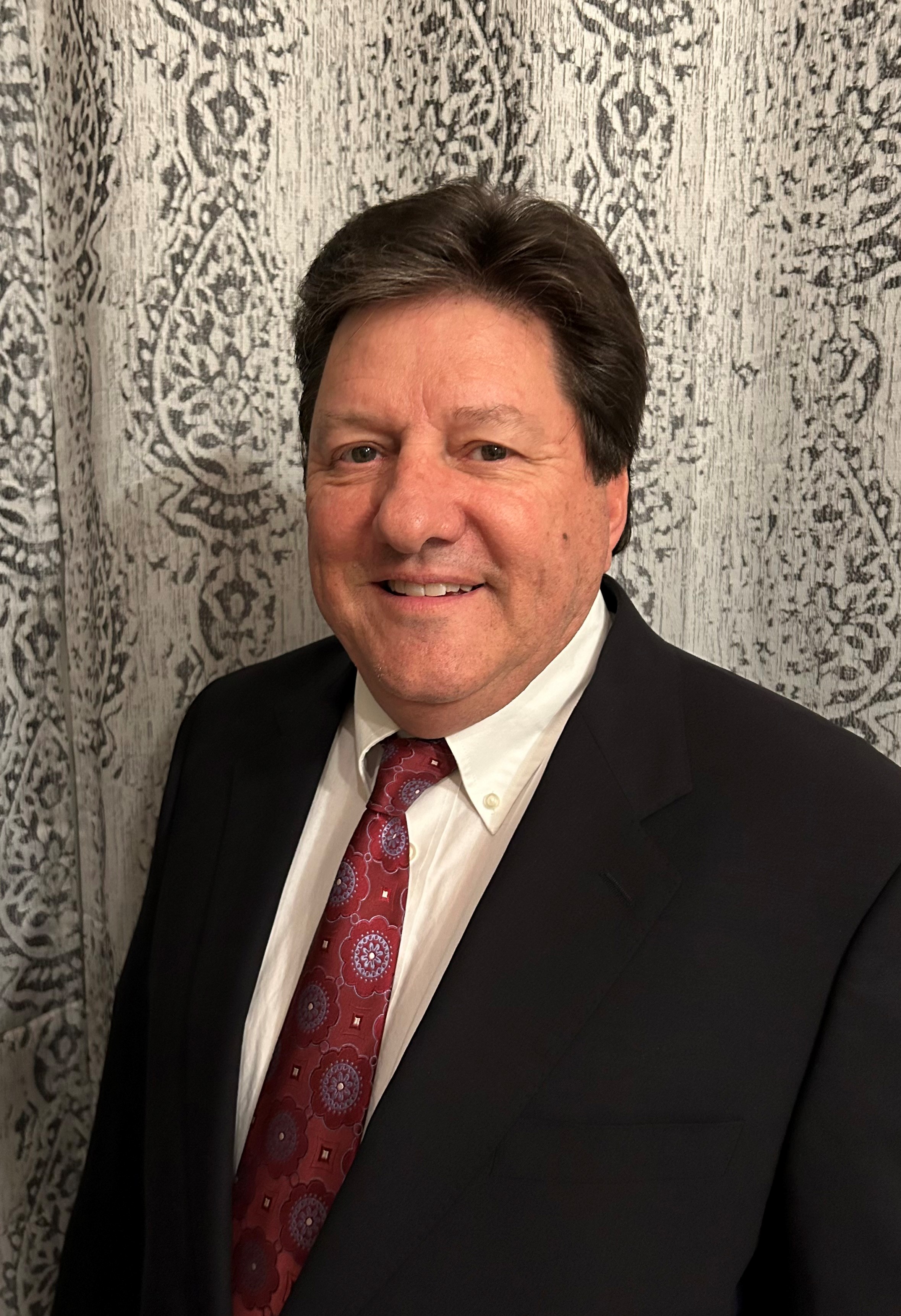
“We’re going to specialized fluid systems, specifically tailored with additives that address their reservoir needs, including surfactants and potential scale-inhibiting type of products during the completion,” Usie said. “We’re using high-end proppants, not sand, to maintain the fractures.”
In one Lower Tertiary well in the Keathley Canyon area of the Gulf of Mexico, Pirogov said, Baker Hughes’s M/V Blue Tarpon pumped 4.4 million pounds (MMlb) of KryptoSphere HD 25 proppant into a well to cover five stacked zones. This set a GoM record for the most proppant pumped into a single well.
In a second Keathley Canyon area well, the M/V Blue Tarpon pumped a GoM record amount of that same proppant—almost 1.1 MMlb—into a single zone of a three-zone well.
Usie said these types of jobs require much more logistics planning, including using multiple vessels to carry all the proppants and supplies.
Completing a multi-zone well in a single trip or multiple trips depends on how much proppant a vessel can carry. For multi-zone wells completed in a single trip, Usie noted, “You don’t have the luxury of coming back into the dock.”
“Usually, there’s alternative supply vessels and in some cases, multiple stimulation vessels required to support the project and having to reload on location.”
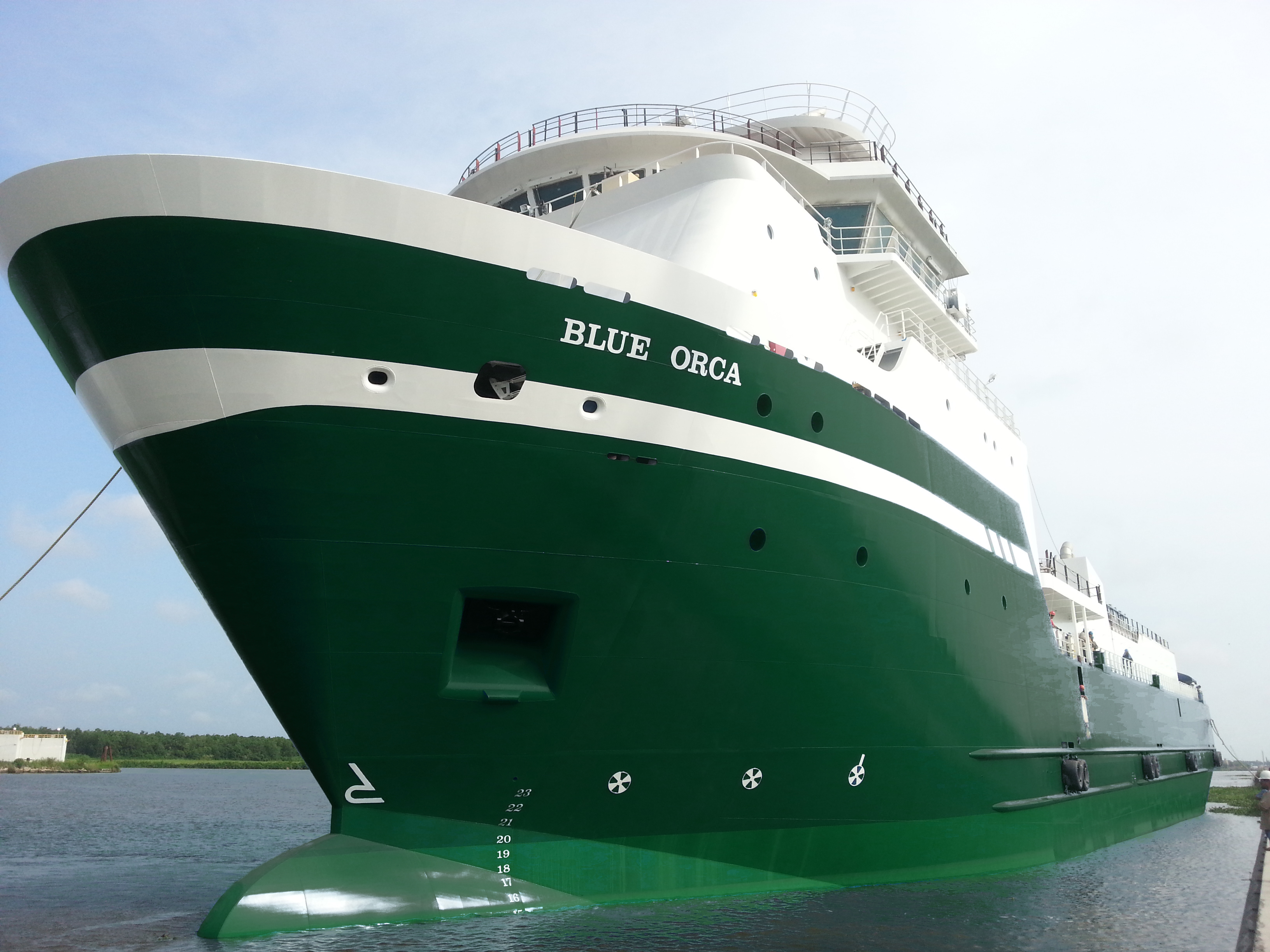
Fewer trips, fewer emissions
As Paul Hosein, SLB’s director of stimulation and reservoir performance, pointed out, offshore is a high-stakes area.
Never have expenditures, carbon impact and emissions profiles mattered more, he said.
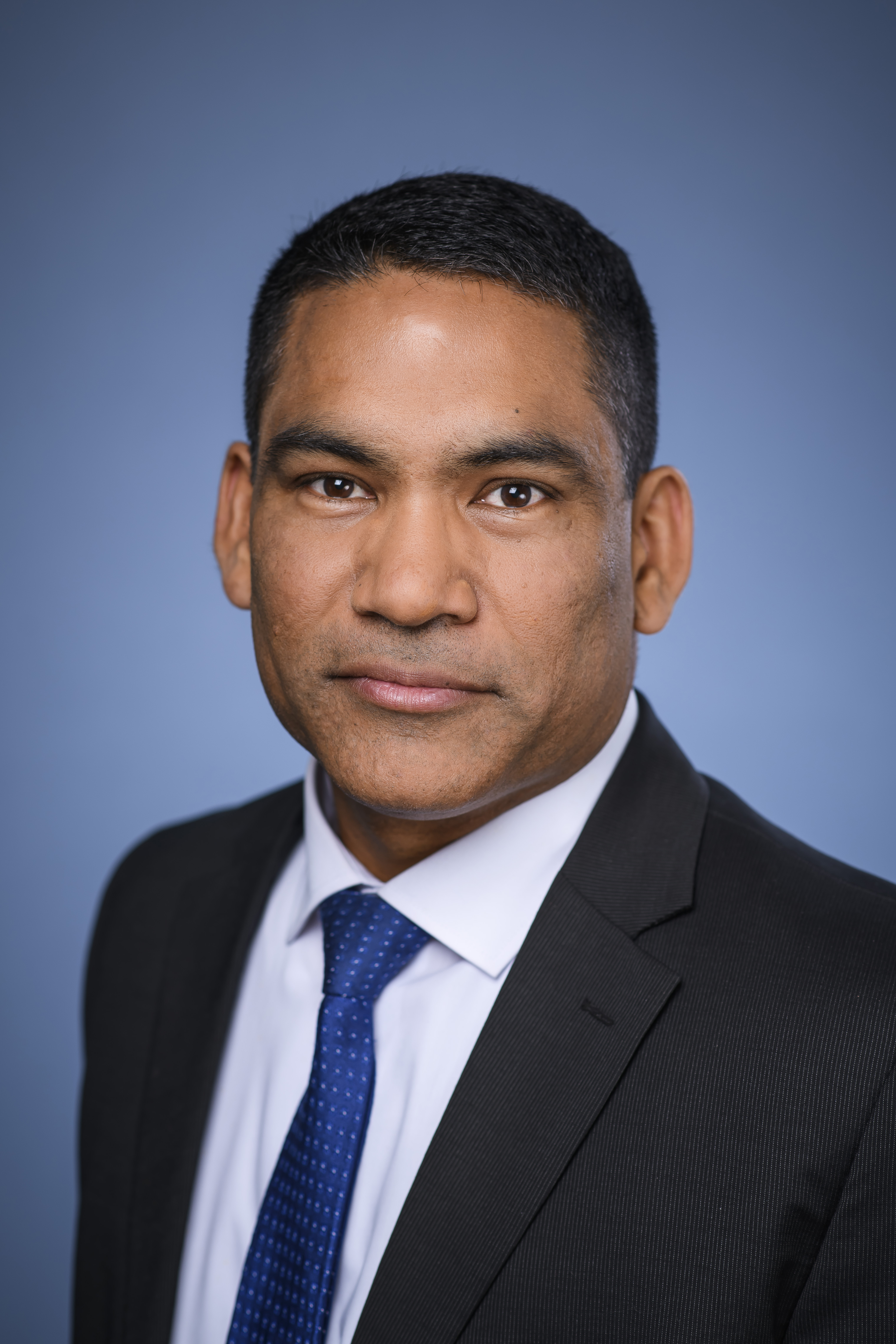
“You need to get it right the first time,” he said. “The cost of failure is so high. On top of that, you generally don’t want to go back to the well when you’re finished.”
Because offshore wells are increasingly deeper and more complex, that can mean more complicated completions requiring more materials—along with the right personnel and equipment—at the right time, Hosein said.
“From a fracture design perspective, typically you need to get deep reservoir penetration during fracturing,” he said. “In general terms, the longer you get the fracture half-length, the better chances you have with long-term sustained production.”
Getting such a fracture right requires a good design up front, he said.
“It’s like a Formula 1 race. You know you have that one shot, and you don’t want to miss it,” Hosein said.
SLB’s Kinetix software makes it possible to plan the hydraulic fracture program based on mechanical properties of the reservoir using various fracture models. For acid fracturing, it allows simulation of frac fluid reactivity with the reservoir.
The software helps model offshore hydraulic fractures around the globe, including for some wells targeting a sandstone reservoir West of Shetland.
“By being able to accurately simulate with the reservoir data, the interaction of the fracture with the reservoir, and get it correctly placed, we’ve actually enabled this operator to change the economics of the whole operation,” Hosein said.
SLB was involved from the beginning, he said, and is now helping the operator with the second and third phases of the development.
Hosein noted that operators are concentrating on lowering their carbon footprint at every step of the well-construction process.
When working offshore, minimizing the amount of materials needed can minimize the number of vessel trips required to transport the materials, which drops costs and improves the emissions profile.
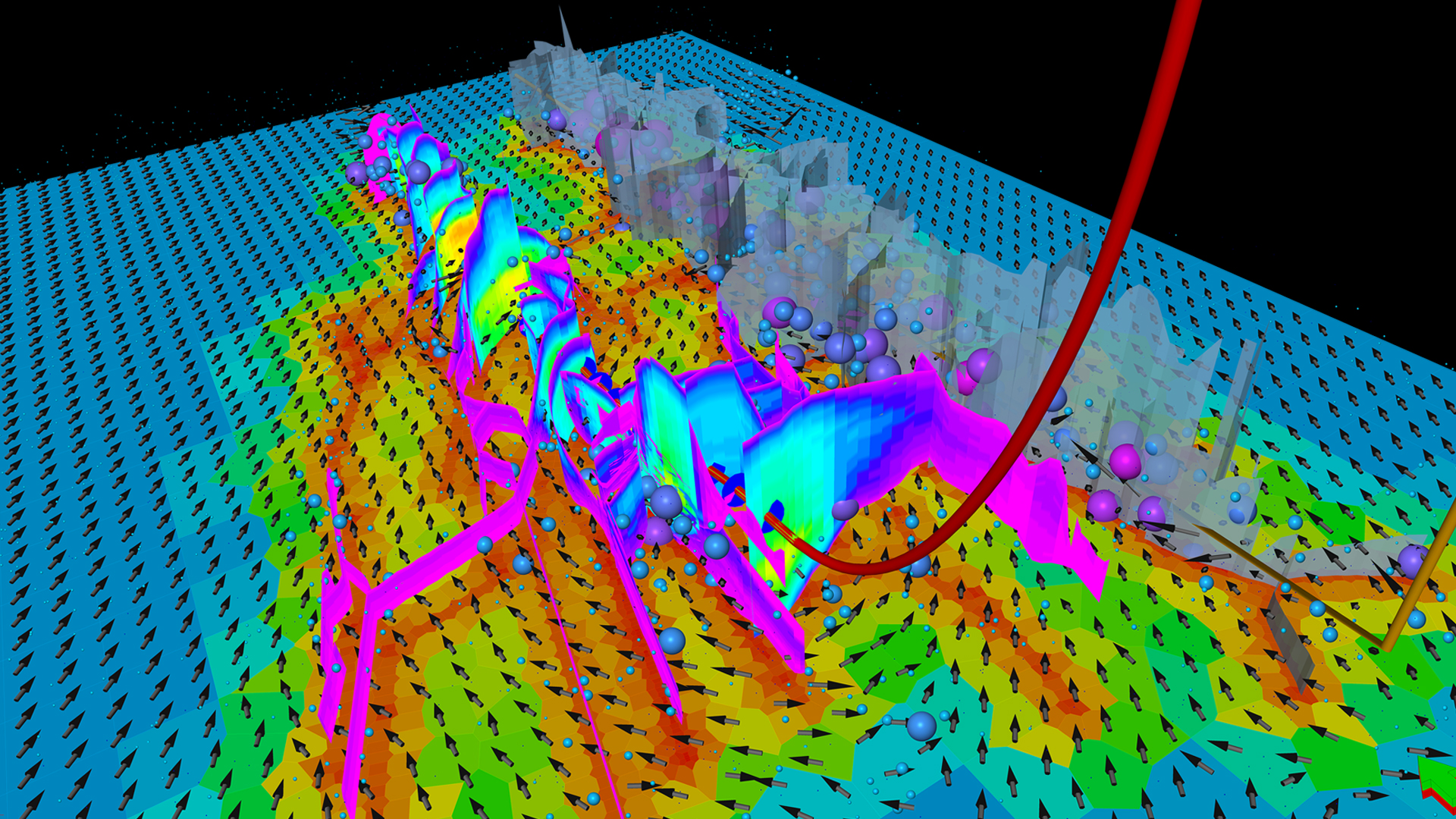
An offshore frac job may require more than 2,000 bbl of water. These operations typically used fresh water.
“That’s hard to do,” he said.
SLB’s UltraMARINE seawater-base fracturing fluid solves that logistics challenge by making it possible to use seawater, instead of shipping in fresh water.
“You actually can pull seawater on the fly,” Hosein said. “You can continuously mix from the ocean and mix it with your proppant.”
As a result, operators do not worry about carting freshwater from shore, which burns a lot of fuel and generates a lot of emissions, he said.
“If you can actually use seawater for hydraulic fracturing, it really does reduce your emissions impact,” he said. “The largest part of the emissions of an offshore fracture job is not the job itself. It’s the logistics of moving all the materials.”
While proppant fracturing is growing offshore, it is still used less frequently than acid, which is a type of hydraulic fracturing that uses reactive fluids, Hosein said. This is because the types of rock typically stimulated offshore are more frequently carbonates than sandstones.
Opening up carbonates
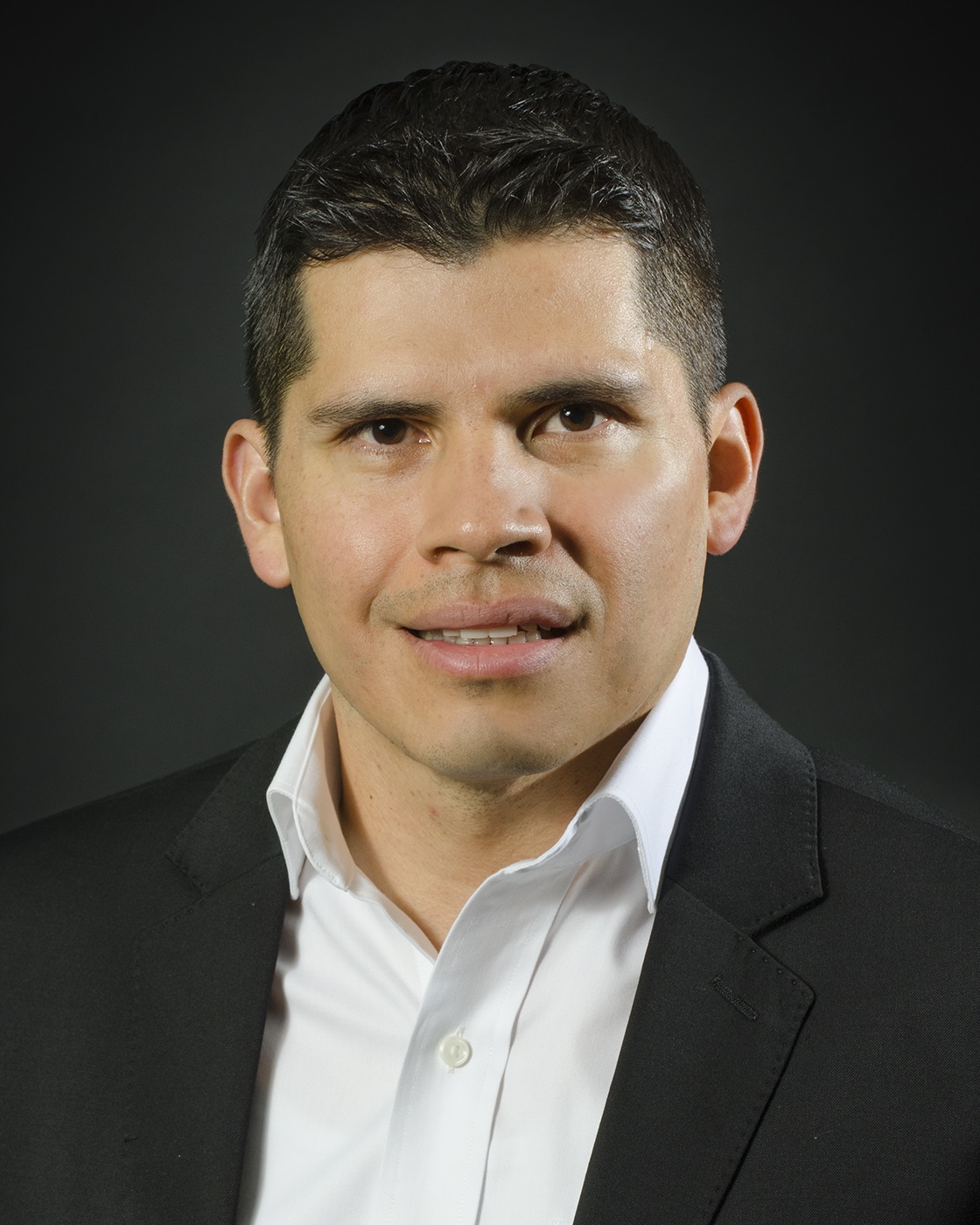
Julio Vasquez, product manager for Halliburton’s production solutions and production enhancement product service lines, said reactive fluids are typically intended for formations. However, for carbonates, HCl-based treatments are applied for matrix acidizing and acid fracturing, and reactive fluids eat away at—or etch away—the rock to create larger pathways for hydrocarbons to flow through back to the wellbore.
A little over 18 months ago, Halliburton commercialized X-Tend acid stimulation service, a low-viscosity, delayed-acting acid, for matrix and acid frac of carbonate formations offshore to allow deeper penetration of the live acid into the formation.
“It is very easy to prepare, and we can mix it on the fly or batch mix it,” Vasquez said.
Since commercialization, X-Tend has been used on about 100 jobs globally, he said. It is used in carbonate formations up to 350 F, but can be taken to higher temperatures. Using X-Tend, he said, has resulted in oil production increases of between 2,000 bbl/d and 3,000 bbl/d.
World of water
Offshore water handling is particularly challenging, Vasquez said.
“Produced water has to be disposed of or reinjected back into the formation,” he said. “You have a lot of restrictions with surface facilities handling water production.”
WaterWeb, a technology Halliburton commercialized over a decade ago, selectively reduces permeability to water with minimal impact to hydrocarbon production, which means there is no need for mechanical isolation, he said.
However, while the WaterWeb polymer initially worked well in sandstone formations, it did not perform as well in calcite-rich formations, he said. Following some research and chemistry modification, he said the product now works in both sandstone and carbonate formations.
In one carbonate application offshore Mexico, the water cut—the ratio of water produced compared to the total volume of liquids produced in a well—was 36%. After Halliburton pumped 370 bbl of WaterWeb into the well, the water cut dropped to 4% while oil production increased by 600 bbl/d, Halliburton said.
In a sandstone application producing from a multi-layered reservoir, water cut was reduced from 80% to 60%, and oil production increased by 300 bbl/d after deployment of WaterWeb.
While produced water is something that needs to be handled, water is needed for some operations. Halliburton’s SeaQuest service makes it possible to use seawater instead of freshwater for fracture fluid or frac-packing operations.
“We don’t have to go back to the port to get more freshwater,” Vasquez said. “We’re saving a lot of non-productive time, a lot of CO2 emissions as well, while providing an optimum frac fluid rheology.”
Recommended Reading
Pembina Pipeline Enters Ethane-Supply Agreement, Slow Walks LNG Project
2024-02-26 - Canadian midstream company Pembina Pipeline also said it would hold off on new LNG terminal decision in a fourth quarter earnings call.
Waha NatGas Prices Go Negative
2024-03-14 - An Enterprise Partners executive said conditions make for a strong LNG export market at an industry lunch on March 14.
EQT CEO: Biden's LNG Pause Mirrors Midstream ‘Playbook’ of Delay, Doubt
2024-02-06 - At a Congressional hearing, EQT CEO Toby Rice blasted the Biden administration and said the same tactics used to stifle pipeline construction—by introducing delays and uncertainty—appear to be behind President Joe Biden’s pause on LNG terminal permitting.
Williams Beats 2023 Expectations, Touts Natgas Infrastructure Additions
2024-02-14 - Williams to continue developing natural gas infrastructure in 2024 with growth capex expected to top $1.45 billion.
Wayangankar: Golden Era for US Natural Gas Storage – Version 2.0
2024-04-19 - While the current resurgence in gas storage is reminiscent of the 2000s —an era that saw ~400 Bcf of storage capacity additions — the market drivers providing the tailwinds today are drastically different from that cycle.