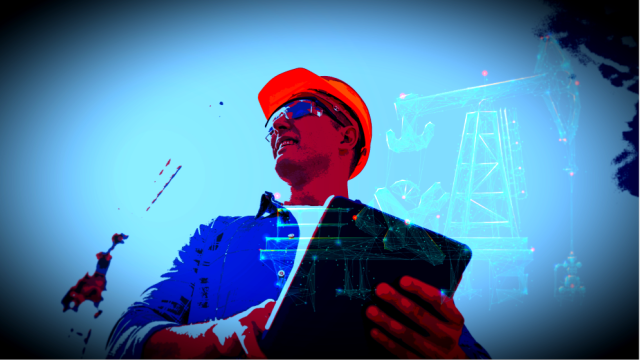
(Source: Shutterstock.com)
[Editor's note: A version of this story appears in the August 2020 edition of E&P. It was originally published Aug. 3, 2020. Subscribe to the magazine here.]
Oil and gas operators and producers have been steadily utilizing digital technologies to enable improvements in operations, production and safety, addressing crucial business challenges. However, significant future improvements require operators to step up their efforts on digital transformation. An approach that is gaining momentum across many Industrial Internet of Things-based industries is the use of digital twins. While many digital twin efforts have focused on manufacturing and aerospace, the oil and gas industry is now evaluating the concepts and testing the waters.
“The transition to the digital oil field has been ongoing for more than a decade, and the goals and benefits that we targeted are finally being actualized,” Noble Energy senior technology executive Gary Birdwell said. “We see digital twins as a natural evolution in our digital oilfield strategy, enhancing our ability to optimize capital efficiency and effectively manage operating expenses for the life of an asset.”
There are already high-profile efforts and results in the space. One example of digital twin technology is in Equinor’s Johan Sverdrup Field, where digital twins are helping to optimize operations on a field expected to account for 25% of Norway’s total offshore production. Another example is bp’s simulation and surveillance system, APEX. The system reportedly creates digital twins of all its production systems. In 2017 bp reported that APEX added 30,000 bbl of production globally.
Digital twins trace their roots back to NASA’s Apollo program. To address practical needs, Apollo engineers created models of physical devices that could be analogs for actual space devices. Experiments and simulations created the exceptionally detailed processes and flight plans used by astronauts. In the “Apollo 13” movie, engineers worked through attempt after attempt to prepare for reentry while adhering to specific power requirements. This was a physical replica, but the idea is the same—each attempt or trial was a simulation. Ultimately, the engineers found the right sequence and the crew reached home successfully.
Today’s technology and computational models allow truly stunning digital copies of physical devices and processes to exist as digital twins. These virtual models combine advanced computational capabilities with extensive engineering data and real-time sensor streams, enabling simulations of new operational conditions, improved predictions and detailed instructions on how to change the behavior of devices in the physical world.
Field applications
Many operators are establishing and running operations centers to perform remote diagnostic analysis. Benefiting from the collection of nearreal- time sensor streams, digital twins can enable these centers to determine the root cause of many issues before dispatching field teams. As the digital twin includes a detailed asset inventory, the field team can be provided with a set of necessary parts based on the failure diagnosis.
“Operators have quickly shifted digital transformation funding from capex to opex and G&A levers,” said Adam Hutchinson, president of Stonebridge Consulting. “The seemingly simple measure of LOE per barrel presents a very complex problem statement for optimization often leading to OpsCenter strategies starting with the highest return on investments projects and then continuing down the cost-benefit list—improve well performance, reduce G&A, optimize water management, outsource telecommunications and so forth.”
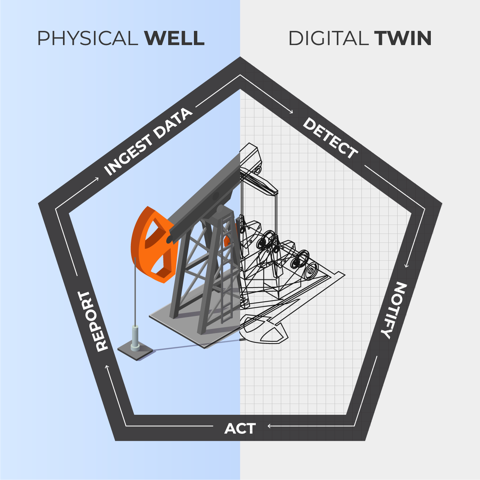
Across industrial sectors, Gartner Inc. has predicted in a recent report that “half of all major industrial companies will be using digital twins by 2021, potentially increasing operational effectiveness by 10%.” Recent research by MarketsandMarkets indicates substantial growth in the digital twin market, projecting up to $35 billion in market worth by 2025.
Digital twin adoption
Being digital representations of physical devices or processes, digital twins are only as good as the source data available to them. Data must be aligned, cleaned and reconciled before use in any form of advanced analytics.
OspreyData has shown that the task of collecting and maintaining wells’ reference logs is often challenging for organizations where different teams work on a patchwork of solutions across vendors. Teams will only prioritize this data collection when the answers that technology enables become a strong imperative for growth and profitability.
The various sectors within upstream oil and gas offer different data representations, challenges and opportunities for digital transformation and the use of digital twins. In exploration, much attention is given to seismic data, reservoir data, lateral spacing, and frac and completions design, including proppant and frac fluid. In production, many analytical models focus on the well history that can be instrumental in creating digital models. However, to have an impact on what is happening in real time and reap higher economic benefits, operators must be able to model wells and fields by analyzing streaming data.
Lowering the lease operating cost and increasing production with existing wells may be key to survival. A digital twin approach for active producing wells has more value now than ever, with fewer new wells starting to date in 2020 and increased investor focus.
A starting point in a gas-lift optimization scenario could be to collect sensor readings on gas injection rate and daily production, allowing production engineers to estimate the net effect of gas injection rate changes on production. Engineers can benefit from evaluating and visually plotting the inferred gas-lift valve in use to determine injection depth. As gas-lift wells are complex operations with fluid dynamics, potentially competing network effects and interactions among adjacent wells, taking an incremental approach to building their digital twins allows organizations to see significant value and operational improvements step by step.
Many digital twin use cases rely on a combination of in-depth well and petroleum engineering data, coupled with sensor streams to construct the digital models that mirror the physical behavior.
Simulations with digital twins
Advancing the capabilities of digital twins is creating new dueling digital models. Simulation models provide computational models, typically based on physics, to calculate the expected behavior of a device. Many simulation solutions are used today to determine design configurations or to periodically revise set points and operational parameters.
A new class of models based on empirical review and evaluation of operational data points is being used to create machine learning models. These models are often used to compare a device’s operational behavior to previously observed behaviors. A new era of simulation models will provide nearly instantaneous results. Periodic reviews for one well, which usually take engineers days to complete, can now be executed hundreds of times per day for entire fields of wells.
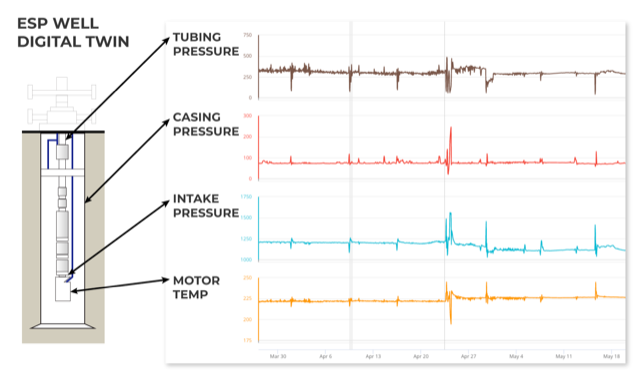
Conversely, coupling high-fidelity sensor data and automating traditional simulation processes can potentially allow far richer, complex and realistic views into production operations. Operators continue to be challenged by new economic realities, shifting workforce skills and increasing environmental scrutiny. There is a heightened emphasis throughout organizations to provide cost transparency. Operators willing to embark on this journey will assess and understand their current operations more deeply and improve operations with automated management, efficient equipment allocation and improved maintenance scheduling.
“Technical challenges exist in this, or really any type of transformation, but they are few in comparison to the cultural and organizational impacts, which can be huge,” Birdwell said. “Establishing an understanding of your current state, challenging assumptions of what you do and why, [and] driving to an agreement on change is critical.”
Elaborating on the importance of using reporting and metrics to quantify the true value gained, he said, “Finally, ensure that you have measures in place to track progress; that is the only quantifiable way to ensure you are improving operations.”
Against the backdrop of recent industry pressures, what-if scenarios can be run across digital twins to determine if wells should be pulled from operations amid the current price drop. Understanding the complexities of a well’s operational environment might help operators avoid costly workovers from issues like sand buildup. Performing a similar analysis on restart order and processes could improve setpoint determination and may prove to be critical in avoiding production misses.
Adoption challenges
Many operators have prior experience in digital transformation and have begun these complex undertakings.
Digital twin efforts continue to drive teams to evaluate the organization’s abilities, especially along dimensions of data management, change management and technical agility. Constructing digital twins requires an expanded mix of skills, involving business intelligence, process simulation, petroleum engineering, data science, data engineering and IT. Digital twin frameworks are still early and rapidly evolving. Based on OspreyData’s experience, operational challenges around machine learning are outside the scope and experience of most operators. This should not hinder operators from engaging in digital twin efforts but should highlight the importance of having an objective review of internal capabilities and what may require external partners and solutions. Though these approaches have existed for years in multiple industries, new advances and approaches are driving new benefits, and the time has come to consider their benefits and suitability within oil and gas
Recommended Reading
Talos Energy Expands Leadership Team After $1.29B QuarterNorth Deal
2024-04-25 - Talos Energy President and CEO Tim Duncan said the company has expanded its leadership team as the company integrates its QuarterNorth Energy acquisition.
Energy Transfer Ups Quarterly Cash Distribution
2024-04-25 - Energy Transfer will increase its dividend by about 3%.
ProPetro Ups Share Repurchases by $100MM
2024-04-25 - ProPetro Holding Corp. is increasing its share repurchase program to a total of $200 million of common shares.
Baker Hughes Hikes Quarterly Dividend
2024-04-25 - Baker Hughes Co. increased its quarterly dividend by 11% year-over-year.
Weatherford M&A Efforts Focused on Integration, Not Scale
2024-04-25 - Services company Weatherford International executives are focused on making deals that, regardless of size or scale, can be integrated into the business, President and CEO Girish Saligram said.