
Digital fabric maintenance uses artificial intelligence to map out future corrosion on an asset (Source: Vidya Technology)
Everything ages. Everything gets old.
As time passes, things tend to deteriorate or lessen in quality. That’s simply the circle of life. But what if there was a technology that forecasted how something ages? A solution that mapped out the life of an asset, allowing for necessary changes to assist in its preservation?
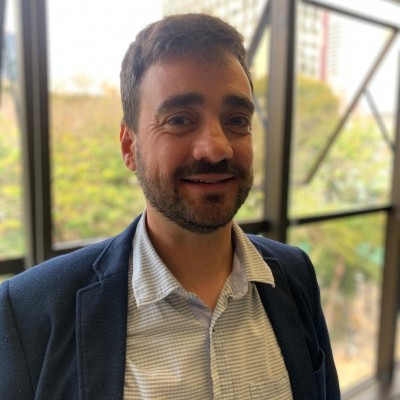
“[Companies] need us because they spend around tens of millions of dollars a year to perform maintenance of coating in offshore installations and they need to apply it properly and in a smarter way,” Vidya Technology CEO Otavio Correa told Hart Energy. “So they need to have data to get the scope of work of… because it's a lot of money and a failure on that can result in a shutdown, which is even more money.”
Vidya Technology is a Brazil-based asset performance management that handles any complex asset in the oilfield that deals with risks. Vidya inspects assets including offshore installations such as FPSOs or ships and even refineries and other onshore installations. The Digital Fabric Maintenance is the company’s latest solution for corrosion management of an asset. A digital twin platform creates a representation of the asset in a virtual world and uses AI algorithms to map out its life, forecasting the progress of coatings, external corrosion, thermal insulation, temporary repairs and the overall integrity of the asset.
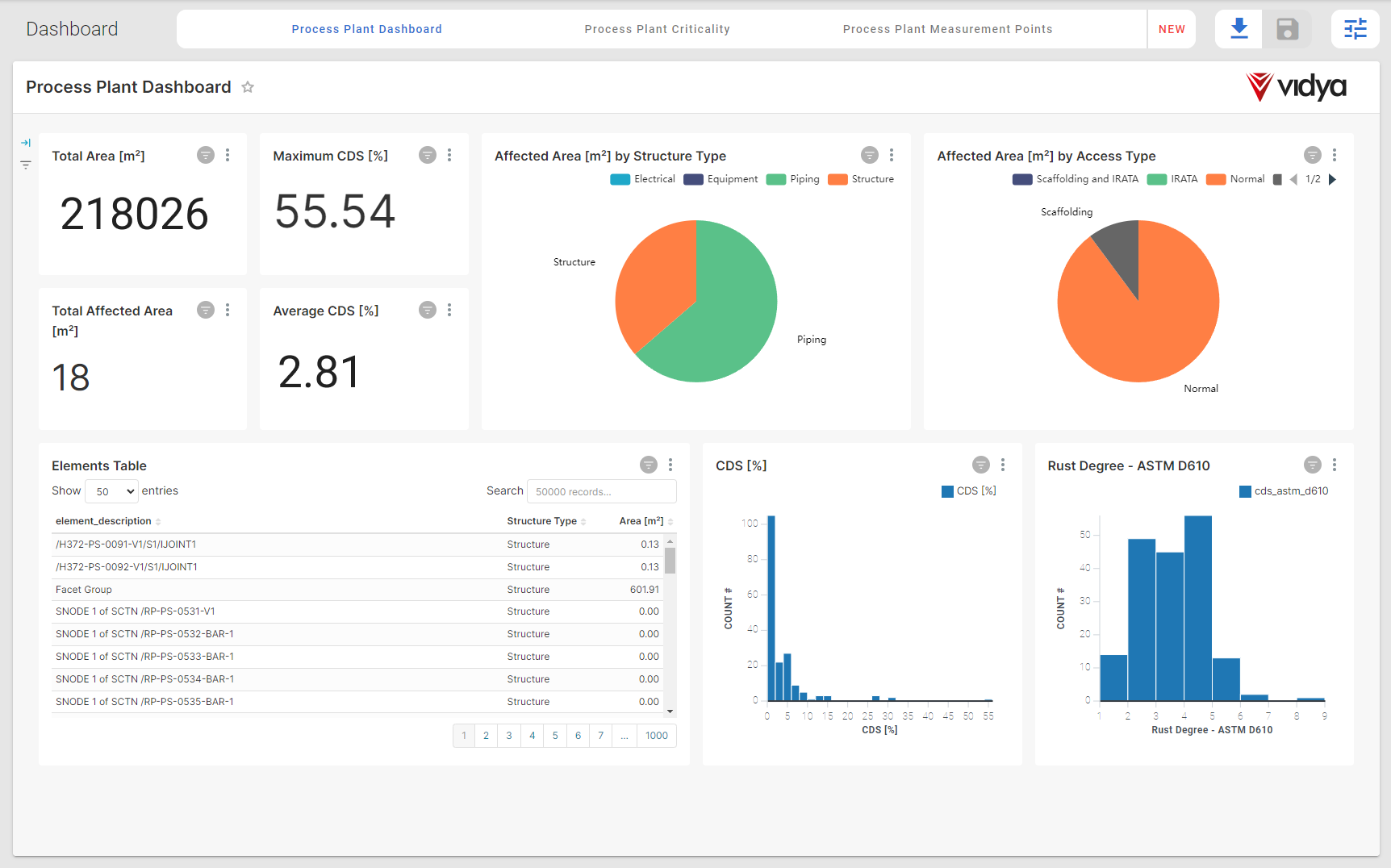
“What we do here is transform images into maintenance actions and absorb the whole process to transform the visual status of your asset into maintenance action,” Correa said. “Our purpose is to get answers to the people in charge of operation of the assets.”
Vidya is able to get these answers by applying more than a decade of experience in the energy industry, coupled with three years of implementation of the Digital Fabric Maintenance solution. During that time, they have inspected more than four million square meters of surface area. Each time an area is inspected, Vidya’s AI models are reassessed and updated, said Correa. Now, the models can guarantee 90% precision in corrosion identification.
The software has an original framework that combines artificial intelligence, reality capture technology, digital twin technology and machine vision to deliver outputs in 30 days. The solution was also a finalist at the MP Corrosion Innovation Awards 2023 from the Association for Materials Protection and Performance and is currently implemented onboard MODEC, Equinor, Ocyan, SLB and Petrobras assets.
“In the case of Equinor’s Peregrino Bravo, we started making the assessment of the fixed platform structure using drones and AI to identify and map all the corrosion problems and map all the corrosion problems in the main structures. We did in only two days on board and the post-processing in only 10 days,” Correa said. “We saved 80% of the necessity of rope access for the inspectors to go there with like escalating the structure and to make the visual inspection.”
Vidya also used its Digital Fabric Maintenance on the Peregrino FPSO and was able to completely map out the external hull, topside, flare, cranes, living quarters and deck in only 13 days with just two people on board. “In fact, the whole project took us only 120 days from the signature of the contract to the delivery of results,” said Correa, adding that they were able to make the whole project safer by reducing rope access to higher areas by 90%.
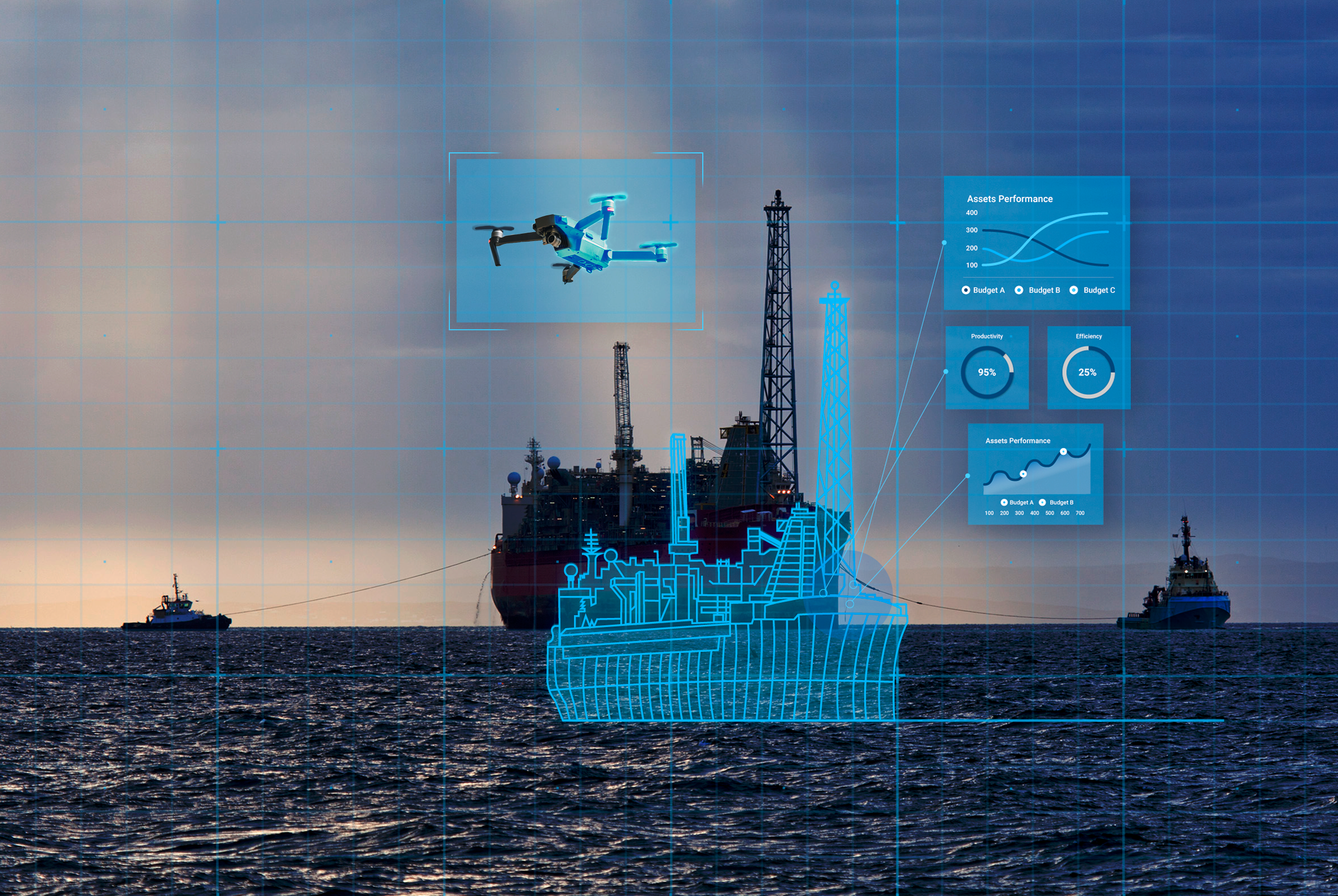
Vidya’s Digital Fabric Maintenance has a few techniques that differentiate it from the competition, allowing the company to deliver solutions faster than others. One of these techniques is its use of photogrammetry, the science of extracting information from photographs, to link drone images with a 3D environment. Vidya is also able to deliver accurate solutions at high speeds because it controls its own data processing platform.
“Since we have our platform and use proprietary data engines, we can ingest information coming from engineering or maintenance to quickly process this data. We can start a project from scratch and in less than four months have a whole scope of work delivered,” Correa said.
In the period of one year of application, the Digital Fabric Maintenance solution saved $965,000 for an FPSO, requiring fewer people on board and detecting 254% more corrosion anomalies than the usual approach. In total, Vidya lessened the number of days spent from inspection to coating maintenance planning from 172 to 49 while achieving better results. They also reduced the number of person on board days per year from the usual 97 days to just 6 days per year.
While still a small company, Vidya has a strong track record of success and looks to continue advancing its product and bring it to the U.S.
Correa’s vision of the future for the platform is to “use robots in the field to acquire the images and reduce the maximum number of people needed on board, in the field or in hazardous areas.”
Recommended Reading
Baker Hughes Awarded Saudi Pipeline Technology Contract
2024-04-23 - Baker Hughes will supply centrifugal compressors for Saudi Arabia’s new pipeline system, which aims to increase gas distribution across the kingdom and reduce carbon emissions
From Restructuring to Reinvention, Weatherford Upbeat on Upcycle
2024-02-11 - Weatherford CEO Girish Saligram charts course for growth as the company looks to enter the third year of what appears to be a long upcycle.
TechnipFMC Eyes $30B in Subsea Orders by 2025
2024-02-23 - TechnipFMC is capitalizing on an industry shift in spending to offshore projects from land projects.
Patterson-UTI Braces for Activity ‘Pause’ After E&P Consolidations
2024-02-19 - Patterson-UTI saw net income rebound from 2022 and CEO Andy Hendricks says the company is well positioned following a wave of E&P consolidations that may slow activity.
ProPetro Reports Material Weakness in Financial Reporting Controls
2024-03-14 - ProPetro identified a material weakness in internal controls over financial reporting, the oilfield services firm said in a filing.