Cost, access and inefficiency drive the push for EOR research and the results — using nanobubbles and NGLs — are showing promise.
Even as drilling costs rise, leasing on government lands is getting tighter. At the same time, current production methods leave as much as 90% of the reserves in the ground, and many producers believe it is more efficient to revisit current formations than to solely rely on drilling for new production.
C3 Oilfield Services and Nano Gas Environmental are making advances in EOR and IOR technologies. C3 is updating NGL injection into formations in a process called SingleShot IOR Technology, while Nano Gas Environmental uses a specially designed nozzle to inject thousands of nanobubbles of nitrogen into the reservoir to boost oil recovery.
Fluffy water
Nano Gas Environmental co-Founders Len Bland, CEO, and Jeff Hardin, chief scientist, were looking for something revolutionary when they found nanobubble technology. The process could multiply the amount of gas a liquid could hold. Bland nicknamed it “fluffy water.” They considered it to be world-changing.
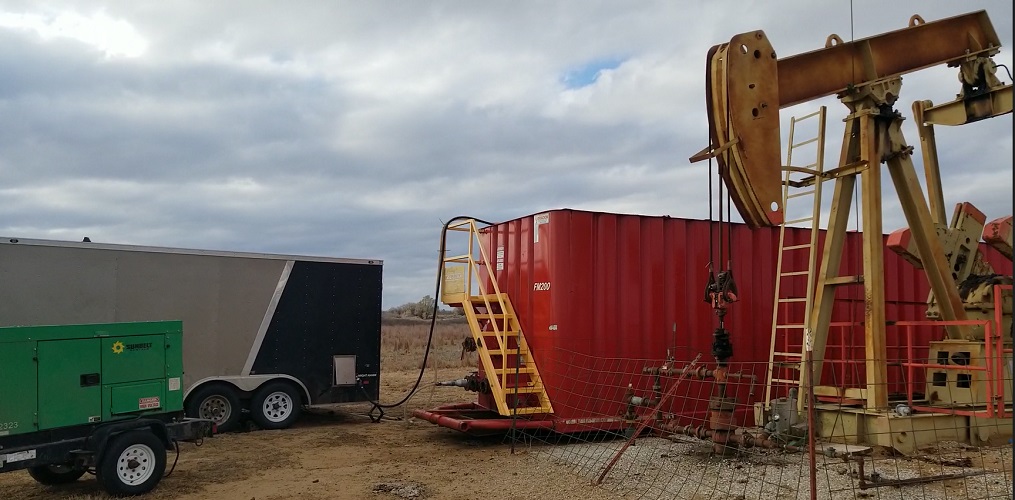
“We have to be part of it,” Bland said.
While the amount of the gas increase has not been fully measured, Bland and his team think it is 3,500 times the amount of gas that would be in water naturally. Nanobubbles are invisible under a light-based microscope but become visible and measurable with a device called a NanoSight.
“You can see them using dynamic light scattering, which is shooting a bunch of lasers through the liquid,” Bland said.
That extreme concentration alters the liquid’s physical, biological and chemical characteristics. The company has used all three for EOR, cleaning produced water and eliminating dredging for sewage lagoons.
Nanobubbles stay evenly distributed throughout the liquid and reduce surface tension with surrounding surfaces. They attach to downhole rocks, making them water wet, which pushes out the oil and sends it to the surface.
The patented Nitro Nano process achieves concentration levels in a single pass that could take other methods multiple passes to reach, according to the company.
Under high pressure, the bubbles become as hard as stainless steel ball bearings. This allows them to penetrate and drive oil out from interstitial cracks, much as fracturing does.
In the lab, in the field
The company originally used the procedure to clean produced water for companies that wanted to do three things: recover oil for sale into the market, reduce dangerous hydrogen sulfide and iron sulfide and drop out total suspended solids from the water. Nanobubbles accomplish all three, which is why, Hardin said, “we create reusable produced water.”
They also used nanobubbles to recover oil and remove solids from tank bottom water. That temporarily increased the oil’s API gravity by up to 22%, allowing it to flow and become a salable product.
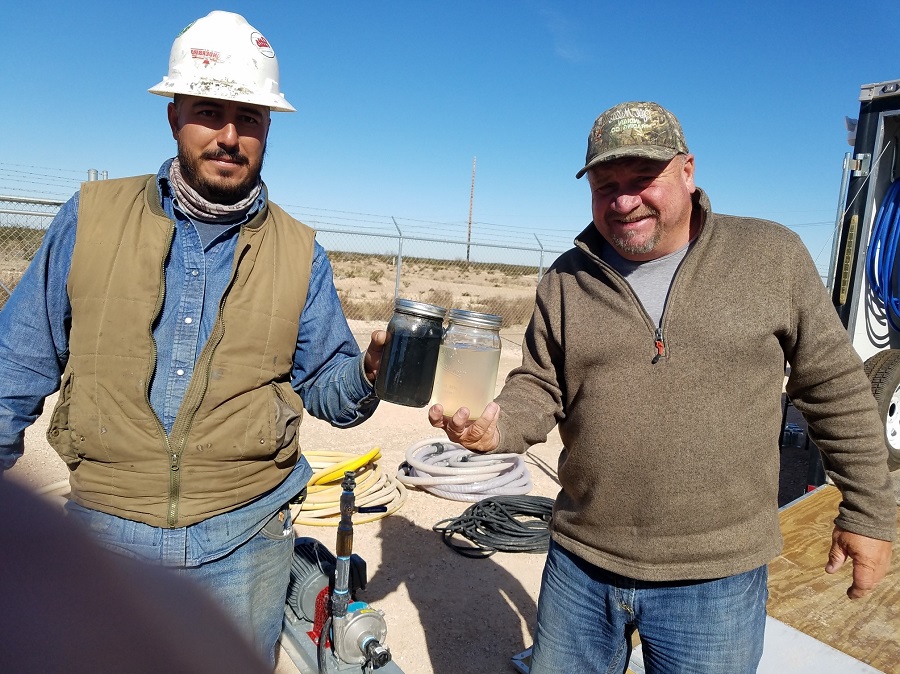
“If we can do that there,” Hardin said, “we should be able to recover oil in an oil well.”
Nitro Nano showed positive results in the lab. Starting with a core infused with 12°API gravity oil, they subjected the core to EOR-ready saltwater, with no results after four days. In the same amount of time, Nitro Nano released oil and gas, with some of the observed gas possibly being nitrogen bubbles.
The company has now tested the process on four stripper wells. The company said each well saw production increase to 200% of the normal rate. A Kansas well in a limestone formation achieved a 540% production improvement after 90 days, and was still at 200% after 150 days. The other three are in sandstone formations in Oklahoma.
Those tests were done as one-time stimulation injections, keeping the treatment close to the wellbore. Bland suggested that those wells could be treated again in six months or so, “like with an acid job. The difference is, we have water and nitrogen that we’re pulling from the air. It’s all natural.”
The ultimate goal, however, is to use nanobubbles on a larger scale.
“We think it will work terrifically as a waterflood. We want to test that application as well,” he said.
The company aims to expand testing to more productive wells to determine if the procedure scales up production in that category.
One shot
In 2019, Oil Technology Group asked Universal Chemical Solutions (UCS)’ Susan Starr, vice president of engineering, and Dave Szabo, engineering adviser, to research the use of NGLs such as propane and butane in EOR. The company wanted to operationalize its initial production, which used propane and butane in a “huff and puff” cycle to potentially double a shale well’s ultimate recovery.
“NGLs have been used over the decades anecdotally for remedial well treatments and for spiking field gas into the gas injection stream in miscible enhanced oil recovery floods, commonly known as water alternating gas injection,” Starr said.
During their research, Starr and Szabo connected with Tadd Wallace, president of C3 Oilfield Services, who had experience using NGLs in fracturing at his previous company, Gas Frac Energy Services. The three realized their complementary ideas and experience would speed the project. In 2020, after a year’s worth of R&D, the company patented Single Shot IOR technology.
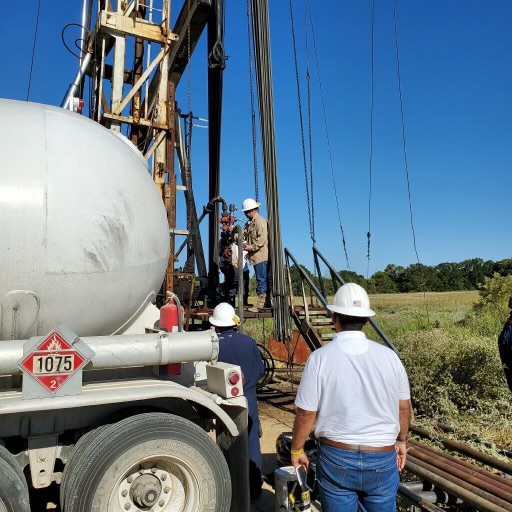
The purpose was to “address anything impeding the reservoir’s ability to flow hydrocarbons,” Starr said.
In fractured wells, she said, the purpose is to re-establish a well’s original stimulated rock volume.
Single Shot’s technology involves chemistry designed to address the cause of the damage and to let NGLs carry it deep into the formation. Starr said most other stimulation methods involve water, which seems counterintuitive in water-sensitive formations. She sees Single Shot as the first reasonable alternative to water-based fluids.
There is also the challenge that treating hydraulically fractured horizontal shale wells involves diverting the treatment fluid from the well’s heel. Single Shot was designed to include multiple diversion states to push the fluid “beyond the path of least resistance,” she said.
Developing the treatment
They began by focusing the design on horizontal shale wells with laterals of 5,000 ft or longer. In those laterals, much of the frac water gets trapped in the formation, reducing the amount of oil it can release. Starr said that University of Texas Professor Mukul M. Sharma hypothesized in a 2015 paper that “the natural connection to the natural fracture system during the hydraulic fracturing process distributes the frac fluid way beyond the induced fracture system.”
From that hypothesis, she added, “we believe this trapped water impedes the reservoir’s ability to flow oil toward the hydraulically fractured wellbore. The Single Shot IOR treatment employs a surfactant that has an affinity for water and will transfer from the NGL to water, making the water less viscous and letting it flow much more easily.”
Testing involved partnering with UCS, which had the equipment and initial production to pump NGLs. Although the researchers’ original focus was on horizontal wells, treating those wells with NGLs in the field could be prohibitively expensive with standard equipment. So, they started the testing process on vertical wells.
But they also realized that the horizontal process was so costly because it used much more horsepower than was needed for Single Shot. The company developed fit-for-purpose equipment to make the procedure more cost-effective for operators, Starr said.
“To our knowledge,” said Starr, “previous attempts at using NGLs for remedial well stimulation did not use additives or diversion. Single Shot combines the NGLs with chemistry, principally surfactant and inhibitors designed specifically for use in propane and butane, and diversion techniques to attempt to open up damaged intervals. The Single Shot proprietary [initial production] IP is designed to eliminate emulsification of the NGLs or the oil/water it contacts downhole. The surfactant is designed to transfer from the NGL to water it contacts in the formation and mobilize the water that is interfering with oil/gas production.”
Single Shot also works on paraffin.
“We developed an inhibitor that is carried in the NGL into the formation. The NGLs dissolve the paraffin in the tubulars and the inhibitor is designed to prevent deposition for a period of time during production,” Starr said.
RELATED: Uinta Rivals the Best of Permian, XCL Resources Contends
To date C3 has tested the procedure on 14 wells, all of which had improved production.
“Half the treatments focused on proving up the technology while the other half applied the technology to treat well damage and increase [initial productions] IPs,” Starr said. “Our vertical well treatments have proven successful in cleaning out condensate blockage in gas wells in the Rodessa and Olmos formations in Texas and removing water block in water-sensitive gas formations like the Jack Fork in Oklahoma.”
Recommended Reading
Russia Orders Companies to Cut Oil Output to Meet OPEC+ Target
2024-03-25 - Russia plans to gradually ease the export cuts and focus on only reducing output.
BP Starts Oil Production at New Offshore Platform in Azerbaijan
2024-04-16 - Azeri Central East offshore platform is the seventh oil platform installed in the Azeri-Chirag-Gunashli field in the Caspian Sea.
Exxon’s Payara Hits 220,000 bbl/d Ceiling in Just Three Months
2024-02-05 - ExxonMobil Corp.’s third development offshore Guyana in the Stabroek Block — the Payara project— reached its nameplate production capacity of 220,000 bbl/d in January 2024, less than three months after commencing production and ahead of schedule.
What's Affecting Oil Prices This Week? (Feb. 5, 2024)
2024-02-05 - Stratas Advisors says the U.S.’ response (so far) to the recent attack on U.S. troops has been measured without direct confrontation of Iran, which reduces the possibility of oil flows being disrupted.
Tinker Associates CEO on Why US Won’t Lead on Oil, Gas
2024-02-13 - The U.S. will not lead crude oil and natural gas production as the shale curve flattens, Tinker Energy Associates CEO Scott Tinker told Hart Energy on the sidelines of NAPE in Houston.