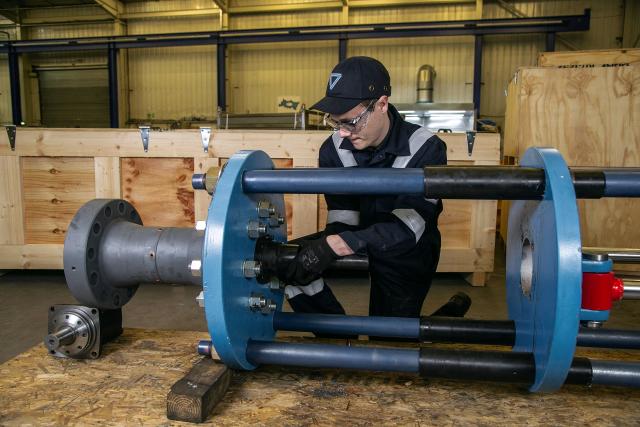
The SIS can secure cost savings of up to 75% in a single deployment. (Source: Unity)
Intervention operations are a vital activity in the lifetime management of wells, ensuring long-term efficient production and integrity and enabling maximum economic oil and gas recovery. The global well intervention market reached an estimated value of nearly $6 billion in 2017, and this is likely to expand at a significant 6% value compound annual growth rate through 2026 as operators continue to invest, according to a recent industry report.
A well can require intervention for a host of reasons, either to address integrity or flow challenges such as wellbore restrictions, sand and water ingress, downhole equipment failure, leaks, cracks and corrosion, or to boost production through, for example, fracturing operations or artificial lift.
Usually, wireline or coiled tubing (CT) intervention equipment is deployed, along with heavyweight well control packages, to address these requirements. Such operations often involve multiple vendors and personnel, complicated logistics and a large wellsite footprint. Associated nonproductive time (NPT) is also incurred during the intervention, rigup and rigdown, all factors resulting in significant costs and risks for the operator, especially offshore. While this process is necessary for deeper well intervention activities, shallow depth operations can benefit from a more refined and cost-effective solution.
The “Wells Insight Report 2018,” published by the U.K.’s Oil and Gas Authority, notes that well integrity problems were the single biggest cause of production losses in the U.K. Continental Shelf, accounting for 43% of the total 33 MMboe loss, of which 10 MMboe was due to wellhead, christmas tree and annulus failures.
Unity, a FrontRow Energy Technology Group company and well integrity specialist in Europe, developed the Surface Intervention System (SIS). The compact tool is an alternative intervention system that does not rely on conventional heavyweight equipment and delivers cost savings of up to 75% in a single deployment.
Tool development
The SIS started out as a gate valve milling tool, originally conceived in 2017 when Unity was asked by an existing customer to develop a system capable of milling stuck gate valves in offshore christmas trees. This common issue leads to wells being shut in, resulting in a loss of production.
Unity developed a compact milling system with a special set of mill bits capable of milling through stuck valves, including those with tough tungsten carbide overlay. Technically, the hydraulic system needed to achieve fine control alongside large forces and meet stringent operational and safety specifications within budget. The new technology is capable of milling gate valves in less than an hour, significantly faster than traditional intervention methods.
Subsequently, and in close collaboration with its clients, Unity identified multiple applications for a low-cost, compact and shallow intervention system with interchangeable tools.
Investing in further R&D and product testing throughout 2018, Unity’s technology team developed the more versatile, multi-use SIS.
With the option to include an integrated well control package, the SIS can be used across a variety of operations including near tubing or tubing hanger plug setting, christmas tree removal, well inspection, milling and wellbore cleanout. Consecutive tasks can be performed during the same deployment, with the system only requiring two people for operation compared to the four to six personnel often needed for conventional methods, increasing efficiency.
The SIS can be used with a number of running/ deployment tools, making it fully compatible with industry standard intervention equipment. This also enables simple switching between functions at the well site. It can operate at wellbore pressures up to 10,000 psi and has a hydraulic motor driving a push, pull and rotate function, rivaling wireline or CT capability. This, combined with compact dimensions of 660-mm-wide by 3.45-m-high (2.16-ft by 11.34-ft) and a weight of 2,337 lb delivers a small wellsite footprint and great ease of mobilization.
The unit is self-contained and can be used for a number of tasks, including the setting of shallow plugs, removal of christmas trees, installation of protective sleeves inside the tree, milling, cleanout operations and inspections.
Case study
In its first deployment, the SIS was mobilized for a major international operator off the coast of Tunisia to set two frac sleeves on two wells. Tree saver sleeves protect the production valves and internals of the christmas tree during fracturing, cementing, chemical or other high-pressure injection treatments. They allow more mature assets to be modified rather than replaced with more expensive, higher rated equipment. The project was completed quickly and successfully, with each sleeve set in under 3 hours, including rigup and rigdown time. This is a significant speed compared to the 24-hour schedule for conventional intervention methods and delivered considerable NPT cost savings for the operator. The cost and risk associated with personnel on board was kept to a minimum as only two engineers were required to perform the installation.
Unlocking reserves and reducing costs
Extending the life of fields is vital to the continued production of mature basins across the globe. The introduction of new technology that can ensure the integrity and thereby increase production rate and recovery will enable assets to operate well past their originally planned lifespan and deliver an incremental financial return.
The SIS enables continued production through ensuring surface equipment integrity. However, it also provides efficiencies and cost benefits in the end phase of well plug and abandonment (P&A) activity, through plug setting and the removal of christmas tree and wellhead surface equipment. In addition, it can be used to carry out inspection and remedial work of the internals of the surface equipment and tubulars prior to removal. The P&A market is a growing sector with regulatory requirements driving operator activity. As the broader industry remains focused on maximizing economic recovery, the SIS is a strong example of how technology can assist operators in achieving the goal of increased productivity.
_____________________________________________________________________________________________________________
Have a story idea for Offshore Solutions? This feature highlights technologies and techniques that are helping offshore players overcome their operating challenges. Submit your story ideas to Group Managing Editor Jo Ann Davy at jdavy@hartenergy.com.
Recommended Reading
CEO: Baker Hughes Lands $3.5B in New Contracts in ‘Age of Gas’
2024-07-26 - Baker Hughes revised down its global upstream spending outlook for the year due to “North American softness” with oil activity recovery in second half unlikely to materialize, President and CEO Lorenzo Simonelli said.
Pemex Hits Debt Target, Struggles to Reverse Production Declines
2024-07-26 - Pemex achieved its long-term debt target, which aimed to gets its financial obligations below the $100 billion, while struggling to halt production declines.
Dividends Declared in the Week of July 22
2024-07-25 - Second quarter earnings are underway, and companies are declaring dividends.
NextDecade Appoints Former Exxon Mobil Executive Tarik Skeik as COO
2024-07-25 - Tarik Skeik will take up NextDecade's COO reins roughly two months after the company disclosed it had doubts about remaining a “going concern.”
Freeport LNG Parent Receives Junk-level Credit Score From Fitch
2024-07-25 - Credit-rating firm Fitch Ratings cited the 2 Bcf/d Texas plant’s frequent downtimes among the factors leading to lowering Freeport LNG Investments LLLP’s credit grade on July 25.