Presented by:
Editor's note: This article appears in the E&P newsletter. Subscribe here.
McDermott is digitizing the subsea project life cycle and revolutionizing traditional work processes by embedding automation into standard global processes through a cloud-based platform calledSubseaXD. The digital platform consolidates and modernizes existing processes for the disciplines involved in project delivery. It provides an alternative, digital methodology to manage change in a dynamic way.
Digitalization is valuable for tracking project parameters and enables automated alterations. This feature allows users to have a quicker turnaround on projects and runs scenarios to better understand consequences behind design decisions.
Digital technologies are the driving force behind the platform that integrates all project data and tools and eliminates siloed information. This results in lean and standardized engineering processes, improved cost effectiveness and fully digital project delivery.
Through collaboration with universities and close contact with operators, McDermott continues to expand its use of digital technology. The McDermott SubseaXD team develops the subsea engineering calculation modules in accordance with relevant international codes (API/DNV/ASME) and liaises with global engineering teams to keep calculation modules up to date and consistent with their needs.
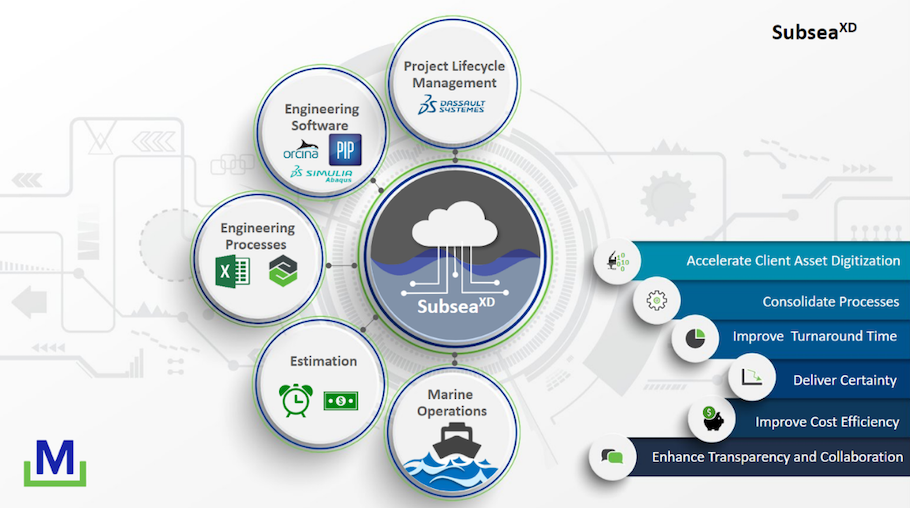
Marine assets and operations
The packing tool module calculates the required number of vessel trips, based on laying the pipelines in a specified order with the selected lay vessel. The user decides the pipeline installation order based on the field architecture in SubseaXD. The packing results and the metadata from the field architecture in FieldAP are then imported into the marine activities generator tool to generate a list of offshore installation activities. The Marine Activities Generator Tool iterates through the packing order and finds potential solutions for spooling, first end installation, normal lay and second end installation. It uses this logic to come up with the first draft schedule with basic activities and associated durations. Users can easily compare multiple concepts during the FEED and tender stages.
Flow assurance
The flow assurance module is integrated with PIPESIM (steady-state multiphase flow simulator) in the backend. The module takes care of repetitive tasks such as model creation, running simulations, post-processing and report generation. The digital twin stores and reflects the latest design iteration, engineering calculations and project information—and, consequently, makes collaborations with other engineering disciplines efficient. Compared to traditional workflows, where the flow assurance engineer’s bandwidth is occupied by many tasks, digital twin-based workflows allow engineers to streamline the process and focus on important technical analysis and decision-making.
Dynamic analysis
The dynamic analysis tool can perform dynamic analysis of installation configurations under various wave and current conditions after the user defines the environmental data. The user defines the acceptance criteria used to determine allowable sea-states for a given installation step as well as customize what parameters to extract from the models for review. Results are displayed along with the calculated configuration.
Riser catenary
The riser catenary tool generates real shapes of risers reflecting material properties, linear weight, buoyancy parameters, contents as well as geometrical data (depth, declination at hang-off) and summarizes associated loads in the SubseaXD. The user downloads OrcaFlex files representative of the pipe cross-section and configuration considered.
Pipeline design
The pipeline design tool performs various pipeline design calculations for various international codes (API/DNV/ASME) and specifications. The user chooses the type of calculation to perform for the selected pipeline from the field architecture in SubseaXD. Results are viewed in the application but can also be exported into a simple memorandum.
Recommended Reading
Chevron’s Tengiz Oil Field Operations Start Up in Kazakhstan
2024-04-25 - The final phase of Chevron’s project will produce about 260,000 bbl/d.
Rhino Taps Halliburton for Namibia Well Work
2024-04-24 - Halliburton’s deepwater integrated multi-well construction contract for a block in the Orange Basin starts later this year.
Halliburton’s Low-key M&A Strategy Remains Unchanged
2024-04-23 - Halliburton CEO Jeff Miller says expected organic growth generates more shareholder value than following consolidation trends, such as chief rival SLB’s plans to buy ChampionX.
Deepwater Roundup 2024: Americas
2024-04-23 - The final part of Hart Energy E&P’s Deepwater Roundup focuses on projects coming online in the Americas from 2023 until the end of the decade.