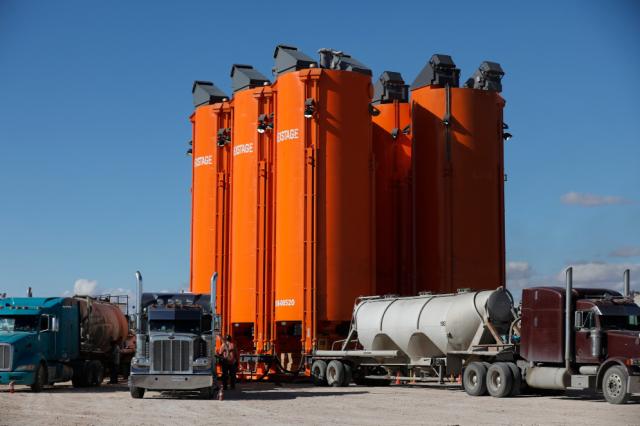
The execution of hydraulic fracturing operations often requires silo storage systems able to handle millions of pounds of silica proppant. These high sand intensity completions also put a premium on fast setup and breakout, and reliable execution. All of it must meet an array of HSE objectives from silica dust mitigation to noise and traffic management.
The economic and operational challenge is further complicated by the diversity of hydraulic fracturing operations that vary widely in specifications from completion design to wellsite configuration. Optimizing wellsite sand storage ultimately depends on the ability to match the silo technology to the needs and objectives of a particular completion.
The NexStage silo system is a versatile proppant storage solution with high volume options to meet the demands of the largest hydraulic fracturing jobs, and the technology to optimize safety, operations and economics.
The system puts storage on the ground fast. Each NexStage vertical silo is delivered using a specially designed, crane-free transport system that erects the silo in about two hours. Combining transport and erection in one unit speeds set up and breakout, enhances safety, and reduces equipment needed at the wellsite. There’s no feeling around in the dark for a solution—work around the silos is illuminated by high intensity LED lighting to improve visibility and work quality.
The vertical NexStage silos maximize storage while minimizing the wellsite footprint. Each silo holds 4,400 cubic feet of 100 mesh sand, with a standard set of six proving onsite storage of about 2.5 million pounds of 100-mesh sand. Flexible silo configuration makes storage capacity and wellsite footprint easy to customize for the job.
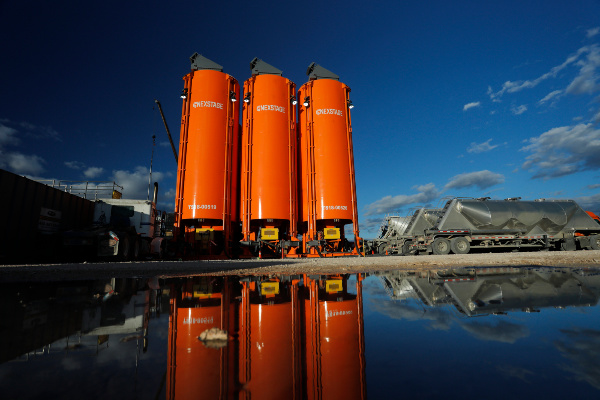
Silo loading options ensure optimal truck fleet use. To assure truck fleet versatility and efficiency, NexStage silos are configured for both pneumatic transfer or gravity-fed systems using hopper bottom trucks.
The specialized gravity-fed system offers unique advantages for faster, safer sand handling. Hopper bottom trucks are quickly unloaded to our Top Fill Conveyor in a drive-through process that takes about 10 minutes—a major time reduction compared to the hour it typically takes for pneumatic sand delivery. Traffic and total loads are also reduced by the hopper-bottom truck’s greater capacity—about 27 tons versus 24.5 tons for a pneumatic truck.
Top loading the NexStage silos eliminates most of the silica dust associated with pneumatic operations, which addresses both OSHA-PEL regulations and equipment damage concerns. The process also reduces associated noise and exhaust, and enclosed conveyor belts further improve dust control and safety.
During the frac job, reliable, precise delivery of high sand volumes is critical to successful execution of the completion. The NexStage system delivers exact amounts of sand from the silos to the conveyor through precision rotary valves that measure sand with industry-leading accuracy. Real-time silo inventory monitored using PropDispatch software enhances job reliability and execution by constantly measuring the exact amounts of proppant in each silo and how much was pumped with each stage—even while loading and pulling sand.
From the silos to the blender, another specialized NexStage conveyor system, PropBeast, provides highly reliable delivery of sand to the blender at up to 23,000 lb/minute. The system seamlessly moves sand from the selected silo to the frac job with enclosed conveyance that further enhances safety.
A full scope of specialized equipment and software are the foundation for efficient wellsite storage and handling of high volumes of sand. The NexStage silo storage system provides the technology and flexibility to achieve economic and operational success across a full scope of high sand intensity completions.
For more information on how our NexStage Silo System can improve your wellsite operations, please visit nexstagesystems.com.