[Editor's note: This story first appeared in the 2020 Hydraulic Fracturing Techbook. View the full supplement here.]
Operators have attempted many techniques utilizing more modern frac designs to recover the reserves left behind in understimulated, older wells. Some have used particulate diverters to isolate and divert flow, while others have involved coiled tubing (CT) and packers. While the primary driver for any refracturing work is to boost base production and unlock stranded reserves with low capital investment, tangible and financial success depends predominantly on isolating existing perforations.
Coretrax has developed ReLine MNS technology, which provides a single-trip solution with no shoe milling. The technology clads and seals various wellbore integrity concerns with minimal loss of inner diameter (ID), while providing high burst and collapse ratings (Figure 1).

The cased-hole system is designed for deployment on jointed pipe and can cover long or short intervals from 30 ft to 7,000 ft. It can be configured to expand and seal across various ID restrictions in the wellbore such as nipples or frac sleeves.
This technology allows mature wellbores to be recompleted enabling refracturing with modern frac designs, as successfully demonstrated in an older Bone Spring Formation well with vintage frac completions in southeast New Mexico.
Isolating existing perforations
The Bone Spring Formation lies directly under the Delaware Mountain Group and over the Wolfcamp Formation. It consists of interbedded (settled between existing layers) siliciclastic, carbonate and shale rocks up to 4,000 ft thick and is divided into four intervals—each of which has very low permeability.
With the introduction of hydraulic fracturing and horizontal drilling, hydrocarbon production has increased considerably. The number of producing wells in the Bone Spring grew from 436 in January 2005 to 4,338 wells in mid-2019, when average monthly production reached 0.6 MMbbl of crude oil and 1.7 Bcf/d of natural gas.
While the U.S. Energy Information Administration (EIA) expects Bone Spring production to drive growth in the Permian Basin, the produced volumes in vintage wells were lower than new wells in the same acreage. Therefore, the forecasted EUR values, using the original production trends, were not economic.
Additionally, the level of depletion around the wellbore was presumed to be small. As the wellhead was rated to 10,000 psi, a wellhead isolation tool was not needed to test the casing to 6,200 psi, which was 80% of the burst rating and the expected pressure during the frac treatment. Since the produced volumes were low, the level of depletion around the wellbore was presumed to be low. Additional frac stages with higher proppant volumes per foot would increase the stimulated reservoir volume and would contribute to higher recovery.
Single-trip tool
A heel frac planned for this well had run into operational issues, and eventually it was decided to perform a full-lateral refrac since the well passed the refrac selection criteria. Unlike other expandable systems, the ReLine MNS running tool configuration can be decoupled from the inner string expansion mechanism during the hydraulic expansion process. This allows the liner to be expanded in multiple load conditions. Importantly, it can be left at a neutral position before anchoring the top seal and exiting the liners with the inner string. This neutral load condition is critical for reliability in severe fracturing downhole environments.
In preparation, artificial lift equipment was pulled from the well and a retrievable bridge plug was set at the planned depth on top of the expanded liner to test the integrity of the original 5½-inch casing. Multiple cleanout trips were needed to clean the lateral wellbore section. To ensure the liner could be run to the intended depth and expanded, a drift was performed. The liner was then run in-hole on an inner string without any issues (Figure 2).
The expansion cone was activated hydraulically to expand the bottom anchor seals, securing the liner to the original casing. The remaining liner was then expanded mechanically using overpull. At the last joint, weight was slacked off to put the expanded liner into neutral, relieving all the tension in the liner joints. The top anchor seals were then expanded hydraulically to anchor the top of the liner to the original casing.
Greater reliability and increased production
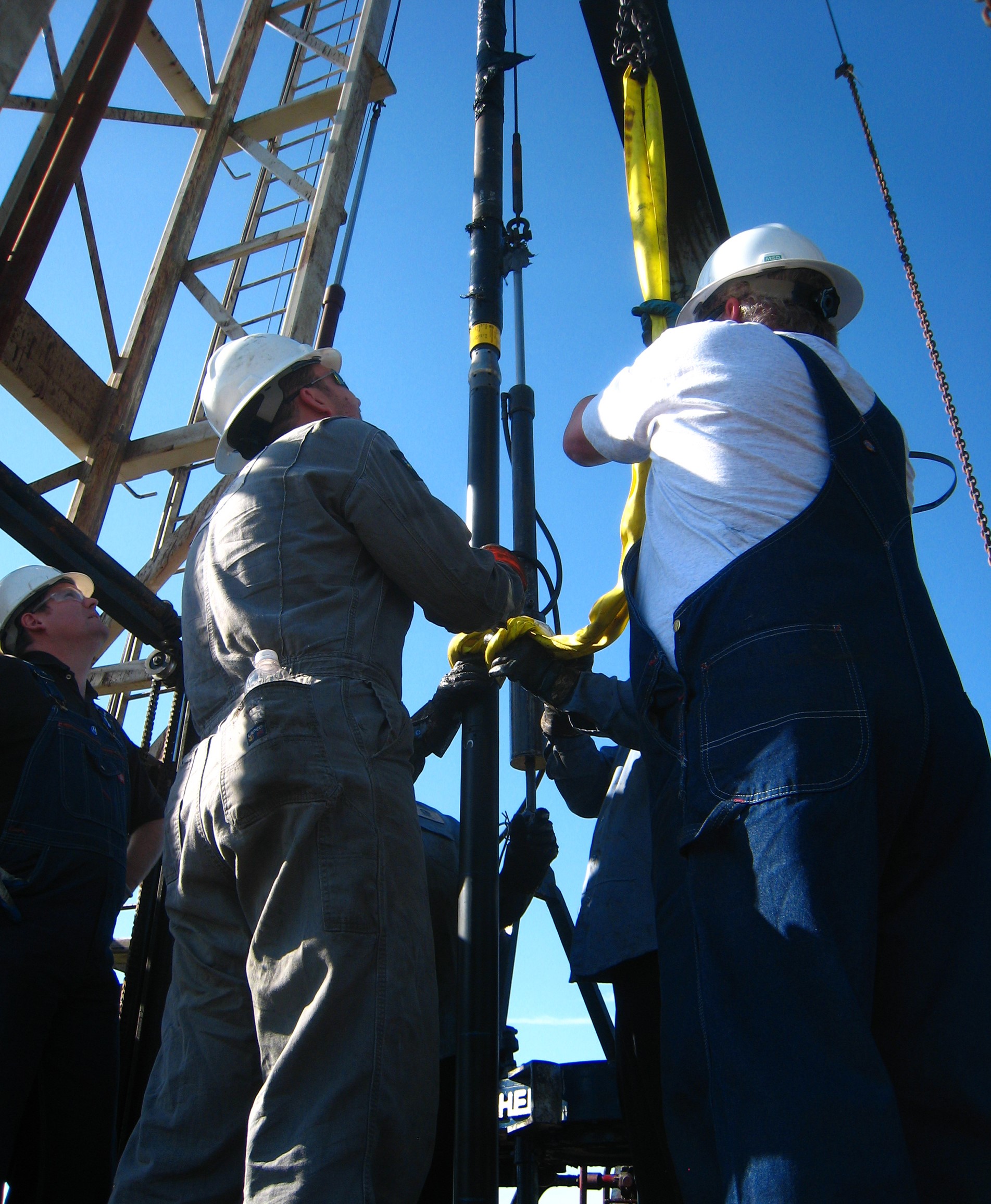
IP after refracturing was double the original completion IP. The forecasted EUR almost tripled, and the rate of return was more than 100%. Among other expandable technologies trialed on this project, the ReLine MNS had the lowest operational cost of the four systems tested by the operator with minimal nonproductive time.
Mechanical isolation using expandable liner technology is a more reliable and effective method for refracturing wells than cementing casing to re-line the previous producing interval. With the ability to leave the expanded liner in neutral while maintaining the speed of expanding the liner using overpull, the operator stated this would be the system of choice for future full-lateral refracturing.
Refracturing unlocks unrecovered reservoirs
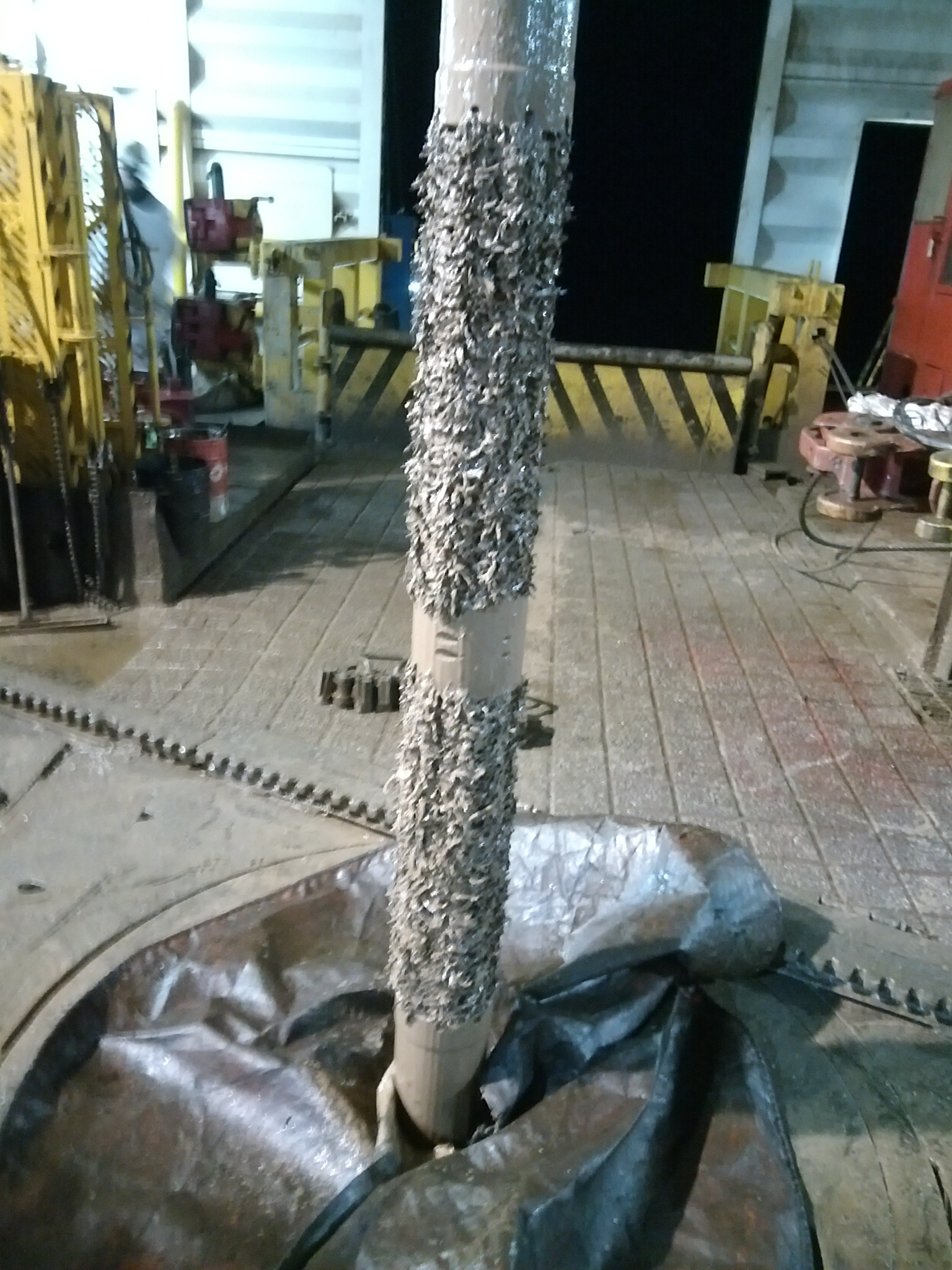
generation of debris in the wellbore. (Source: Coretrax)
It is estimated that drilling and completion of a new well can range between $5 million and $10 million per well to perform. In today’s cost constrained climate, full-lateral refracturing unlocks unrecovered reserves at a lower cost than newly drilled wells.
While the operator will have access to original surface equipment, and the original wellbore, the risk associated with getting that second bite of the cherry is dependent on embryonic technology development and availability. The use of expandable technology is the ideal example of new innovation that would not have been available a decade ago. Like any operation, the risk of doing what is well known but expensive compared to what is unknown and more cost-effective is the daily conundrum to support the evolution of effective, productive and sustainable drilling and completion.
A comprehensive study of the candidate history, including recent interventions and chemical treatments, should therefore be seriously considered while assessing the amount of preparation and cleanout needed (Figure 3).
Investing in R&D
Coretrax, which was formed in March 2020, following the merger with three oil and gas technology firms (Coretrax, Mohawk Energy and Churchill Drilling Tools) now has a portfolio of more than 50 technologies offered through three innovation platforms and plans to launch disruptive technologies to market this year. With a unified innovation offering designed to improve production performance and well intervention efficiencies, the business intends to reinvest more than 15% of revenues into R&D each year.
About the author: CTO Scott Benzie joined Coretrax in 2019 following the integration with Mohawk Energy, which he founded in 2004. References for this article are available upon request.
Recommended Reading
Swift Solar, with Backing from Italy’s Eni, Raises Tech Financing
2024-06-12 - Swift Solar, with backing from Italy’s Eni and others, has raised a total of $44 million for work transforming the solar energy landscape with perovskite tandem solar projects.
Utility, Clean Energy Company Allete to Go Private in $6.2B Deal
2024-05-06 - The Minnesota-based utility said on May 6 it agreed to be acquired by a partnership led by Canada Pension Plan Investment Board and Global Infrastructure Partners.
Berntsen Joins Xcel as Executive VP, Chief Legal and Compliance Officer
2024-05-22 - Rob Berntsen is assuming the role from Amanda Rome, who had been in the position on an interim basis.
Riley Permian Increases Stake in West Texas Power JV with Conduit
2024-05-22 - Riley Exploration Permian increased its ownership in RPC Power, a JV with Conduit Power, to 50% from 35% and has agreed to sell up to 10 MMcf/d of natural gas as feedstock supply for the generation facilities as RPC plans to sell to ERCOT.
Earthstone’s Anderson Relaunches, Seeks Conventional
2024-05-24 - The new E&P PetroPeak Energy will also take a look at unconventional property in the Eagle Ford and Austin Chalk.