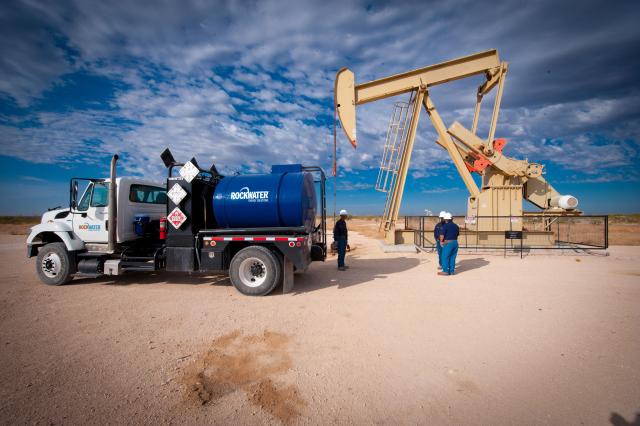
Producing wells in today’s climate requires a consistent review of fluid conditions to keep production levels within the expected decline curve range. (Source: Rockwater Energy Solutions)
Thousands of domestic wells in the field underperform their projected production potential. An effective well maintenance program is essential to provide the engineering, testing, application and monitoring experience to remedy the myriad production problems that hinder well profitability. Effective communication between service company scientists and engineers and production engineers is required to identify underperforming wells and engineered solutions as well as to monitor treatments to verify treatment results post job. The objective is to maximize production and minimize the total cost of operations in a reliable and sustainable manner.
Background
Lower than expected production and higher than expected costs can occur for a variety of reasons. These reasons can range from residual drilling or completion fluid that creates a blockage to organic or mineral deposits that restrict flow paths. It is important that one understands the problem to be addressed when planning well maintenance operations.
An underperforming well may demonstrate lower than expected oil or gas production, mechanical problems or high water cut. A decline curve of more than 10% below the normal decline may indicate a problem. The operations manager or engineer is usually the best source for data to determine the root cause of a potential well problem. The production engineer will have detailed data such as well tests, daily production plots and a wellbore diagram. The history of the well should be detailed, including well workover and production history; well response to stimulation treatments; produced fluid properties and composition; interaction of produced fluids with stimulation treatments; and reservoir conditions.
A review of well fluids can help determine reasons for a well production decline. Oil, water and gas analysis should be performed. The oil analysis may determine if paraffin, asphaltenes or emulsion are blocking conductive paths. A review of the water could determine the potential for mineral scaling based on fluid chemistry, temperature and pressure. The operator also can provide a history and perhaps samples of solids and deposits from past remediation work such as workovers, swabbing jobs, or rod and tubing pulls.
Well remediation technology methods build upon a long history of production chemistry advances and expertise. Treatments can be designed to target production robbing flow assurance issues or provide treatments to maintain asset integrity.
Acidizing
Well acidizing is a stimulation technique designed to remove mineral scales and/or remove nearwellbore skin damage. A variety of acids are used including hydrochloric acid, hydrofluoric acid, acetic acid and formic acid. Acid selection can be made based on the type of deposit to be removed and downhole temperature.
In many stimulation jobs, the target is typically near-wellbore pore plugging due to mineral scale or formation fines. For both deposit removal and well stimulation, 15% hydrochloric acid is a common acid used. That amount is typically used because it provides significant acid strength while minimizing the pressure needed to flow the spent acid and dissolved solids back out of the well. Spent acid will increase in viscosity as it becomes saturated with dissolved material.
Mineral scales dissolved with hydrochloric acid include calcium carbonate, iron sulfide and other iron scales such as iron carbonate and iron hydroxide. Hydrochloric acid is not effective against halite blockages and barium sulfate. Hydrochloric acid is only marginally effective against calcium sulfate scales. Water is an effective solvent for halite deposits.
Barium scales and calcium sulfate scales are particularly difficult to remove but can be treated with the appropriate scale inhibitor to prevent deposition. Mechanical removal such as milling or drilling out the scale may be the only recourse for removing tubing blockages that prevent a chemical treatment from contacting the solid. Often equipment replacement is required for severe scaling deposition. Prevention with a chemical scale inhibitor is often the most cost-effective remedy when dealing with sulfate scales.
Organics removal
Experience shows that there is often a dominant damage mechanism by organic deposits in the near-wellbore of producing wells. Examples of organic deposits are paraffin and asphaltenes. These deposits can create a secondary problem of stabilized emulsions. There are products designed to remove organic deposits from the near-wellbore area. This product range consists of blends of surface-active agents formulated in a solvent. These products will remove organic deposits and dissolve and disperse asphaltenes. They also contain demulsifiers that will resolve stabilized, near-wellbore emulsions without adversely impacting crude dehydration in surface facilities.
Case history
Newly drilled wells in Canadian County, Okla., in the Woodford Formation experienced a severe iron sulfide tubing deposition problem. Untreated wells that experienced tubing plugging would require mechanical and chemical intervention every few weeks. Initially, injection of tetrakis hydroxymethyl phosphonium sulfate (THPS), an iron sulfide chelator, into the annulus was used to control the iron sulfide. The corrosive nature of THPS prevented its use as a long-term solution. The producer sought a nonacid iron sulfide control solution.
Chemical additives were tested on samples of the solids. Laboratory testing indicated dispersing and antiagglomeration of the iron sulfide to prevent deposition, rather than dissolving it, was a viable option. A blend of readily available surfactants was prepared. Stability tests were run on the blend to make sure it was suitable for the 76.6 C (170 F) bottomhole temperature. In addition to the stability tests run, corrosion tests were run to ensure the blend would not corrode bottomhole tubulars. The iron sulfide blend exhibited 98% reduction in the corrosion rate versus a blank in sparged beaker corrosion tests using a synthetic field brine at 76.6 C.
The test data on the new blend met customer specs and were approved for a field trial. Fieldwide use of the nonacid iron sulfide dispersant proved it was successful at keeping the production tubing free of iron sulfide deposits. Iron and manganese readings were reduced and total dissolvable solids at saltwater disposal locations improved with the use of the new product. Fieldwide application of the new iron sulfide control product proved it was an effective nonacid solution for the control of iron sulfide.
Conclusion
Economics should be considered when developing a well maintenance or stimulation project so the cost of a treatment program does not exceed the market price of oil and gas. If well intervention is required, the expected breakeven point on the total cost of treatment would include shut-in time, rental equipment costs, chemical costs and time required to recover the treatment fluid. If large volumes of displacement fluid are required to displace the tubing and casing, there may be a significant time period before this fluid is recovered and hydrocarbon production is reestablished.
A proper understanding of well problems is required for an effective well maintenance program. Effective design and application at the proper time can reduce field expenses and lower the time between well failures. Operators depend on their production chemistry partners to deploy an effective maintenance and stimulation program to improve field economics and improve asset valuation.
Recommended Reading
US Shale Leaders Set Pricing for Tamboran Resources’ IPO
2024-06-17 - Tamboran Resources’ appraisal wells indicate the Beetaloo Basin target formation is similar to the Marcellus Shale in its geophysical properties.
Aussie Shale’s Tamboran Resources Prices IPO in Range but for Fewer Shares
2024-06-27 - Among those buying the Australian shale-gas developer’s pre-trade shares were U.S. wildcatter Bryan Sheffield and completions pressure-pumper Liberty Energy.
Scott Sheffield Among Investors in Australian Shale Gas IPO
2024-06-27 - The operator who sold Pioneer Natural Resources Co. to Exxon Mobil in May for $59.5 billion joins his son Bryan Sheffield in shale gas investment Down Under.
BPX’s Koontz: The Rise of a Shale Man
2024-07-02 - CEO Kyle Koontz takes the reins of BPX Energy’s rapid onshore growth amid big changes at BP.
Halliburton Sees NAM Activity Rebound in ‘25 After M&A Dust Settles
2024-07-19 - Halliburton said a softer North American market was affected by E&Ps integrating assets from recent M&A as the company continues to see international markets boosting the company’s bottom line.