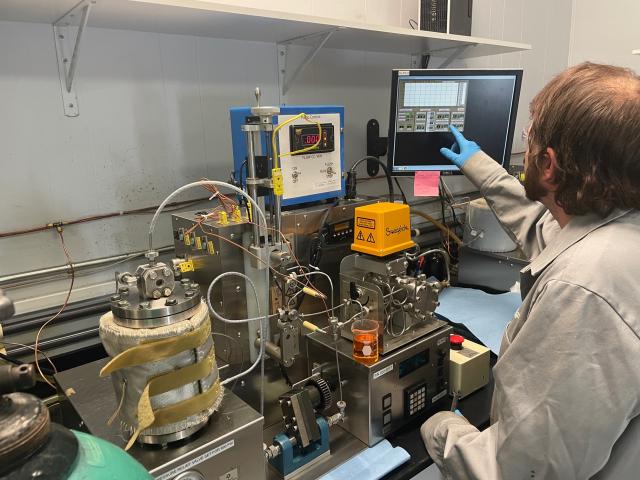
The last 18 months have seen a rise in the development of new recycled or bio-derived fuels and other chemicals designed to replace their traditional counterparts. (Source: SPL)
Every day we see headlines highlighting oil and gas companies looking to reduce carbon footprints. At one end of the scale, they are cutting emissions at job sites and at the other they’re adding green energy to their portfolios.
Houston-based Southern Petroleum Labs (SPL) offers end-to-end testing, measurement and reporting solutions across the entire hydrocarbon value chain and is working on adding the ability to test new environmentally-friendly fuels and other liquids before investors build pilot plants to manufacture them.
Any fuel or other liquid flows through many stages in the manufacturing process. For a new substance, it is vital to know beforehand how it will behave in those conditions where pressure and temperature changes are the norm. Developers must learn how the fuel or lubricant itself will respond, as well as how corrosive it may be to the tubing and machinery carrying it. And ultimately, will it still perform as the developer intended?
SPL’s Arlington facility was originally Alcor Petro Lab, which was bought out by SPL in 2018. The Finished Products Group at that lab primarily tests lubricants and refined petroleum products, but occasionally clients in those areas will ask the lab to test upstream substances.
A large part of the lab’s business involves standardized testing to military specifications among other standards, along with support testing for research and development. This latter category was the lab’s entry point for evaluating environmentally related substances.
One of those is the Hot Liquid Process Simulator (HLPS) test. It simulates the heat exchanger process in a refinery or processing plant as heat is used to transform molecules of one type into something else. In the oil and gas industry, refineries are concerned about asphalt deposition or other carbon-based fouling in the coils of the heat exchanger as liquids cool.
With few new petroleum-based fuels being developed, this procedure is now rarely used in that industry. But the rise of investment in alternative fuels has given new life to the formerly semi-retired HLPS.
The lab still tests lubricants, but the last 18 months have seen a rise in the development of new recycled or bio-derived fuels and other chemicals designed to replace their traditional counterparts.
These new substances may come from renewable feedstocks including recycled plastics, wood chips or others. When developers reach a point where the lab tests appear successful, they’re poised to start larger scale production. First, however, the new molecules must be tested in conditions that simulate the manufacturing process.
They primarily need to know:
- What is the substance’s fouling rate in a heat exchanger?
- What is the corrosion rate of the materials exposed to it?
- What is its optimal processing temperature?
The fouling rate is key because built-up deposits reduce the heat exchanger’s efficiency. The faster the buildup, the more often the heat exchanger and related tubing must be shut down for cleaning. The cleaning process itself may be costly, and the factory doesn’t generate a sellable product while it’s down.
Because new biofuels have varying acidity levels, facilities developers must tailor the composition of pipes, pumps and tanks to the level needed for resisting corrosion without overspending on higher quality materials than are needed. A highly corrosive fuel can quickly destroy an inadequately designed heat exchanger, costing the developer millions of dollars right at the start.
The optimal processing temperature decision balances the need for producing the product properly with minimizing the fouling and corrosion rates and overall production costs. For example, a developer’s lab test shows that the process must run between 50 C and 90 C, and it begins to break down at around 70 C. So the lab will run a series of tests covering the entire range so the designer can evaluate the best temperature for optimizing production processes.
Engineers require data like this because the production operation is based on temperatures, flow rates, pressures and materials, all of which must be properly adjusted.
Designers also need the data in order to properly equip the plant. An improper facility design—learned only after it a plant failure—can cost millions of dollars and greatly delay introduction to the market. In other words, proper testing more than pays for itself in loss prevention.
Testing of renewables is new enough that there is yet to be a standardized system for this like there is in oil and gas. Having a large existing arsenal of available tests, however, gives lab technicians many options for adapting those tests to the growing needs of the new breed of designers.
Developers may ask for a particular test that already exists, but with one or two changes to accommodate the differences in fuels. Sometimes that may require building custom components. To properly design a test, SPL technicians must first understand what the expected process conditions could realistically be in the proposed manufacturing facility.
Being willing and able to accommodate this customization of tests has opened the door to an entirely new market for the lab. The growth of opportunities to create new tests for the latest renewables makes this an exciting time for forward-thinking labs and their employees.
As the ESG push began in earnest in 2020, many investors began putting resources into these renewable fuels and other substances. Now many of them have advanced enough to be ready for pilot plants or full production. They’ve progressed from “interesting science project” to “almost-ready-for-market” status.
It is also important to note that these tests are only mitigating risk from known challenges. In the R&D phase, there is still the possibility of a surprise when it enters production.
As the flow of renewables continues, there will most likely be new tests designed to evaluate those previously unknown issues.
While this does not involve reinventing the wheel, it does require redesigning it.
Recommended Reading
E&P Highlights: Aug. 26, 2024
2024-08-26 - Here’s a roundup of the latest E&P headlines, with Ovintiv considering selling its Uinta assets and drilling operations beginning at the Anchois project offshore Morocco.
OMV Makes Gas Discovery in Norwegian Sea
2024-08-26 - OMV and partners Vår Energi and INPEX Idemitsu discovered gas located around 65 km southwest of the Aasta Hansteen field and 310 km off the Norwegian coast.
E&P Highlights: Sep. 2, 2024
2024-09-03 - Here's a roundup of the latest E&P headlines, with Valeura increasing production at their Nong Yao C development and Oceaneering securing several contracts in the U.K. North Sea.
Breakthroughs in the Energy Industry’s Contact Sport, Geophysics
2024-09-05 - At the 2024 IMAGE Conference, Shell’s Bill Langin showcased how industry advances in seismic technology has unlocked key areas in the Gulf of Mexico.
Devon Energy Expands Williston Footprint With $5B Grayson Mill Deal
2024-07-08 - Oklahoma City-based Devon Energy is growing its Williston Basin footprint with a $5 billion cash-and-stock acquisition from Grayson Mill Energy, an EnCap portfolio company.
Comments
Add new comment
This conversation is moderated according to Hart Energy community rules. Please read the rules before joining the discussion. If you’re experiencing any technical problems, please contact our customer care team.