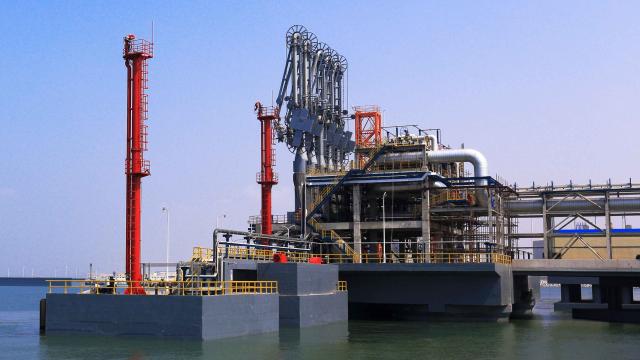
An LNG receiving station terminal. (Source: Shutterstock)
The oil and gas boom in the U.S. has made the country a major exporter of natural gas, in the form of liquefied natural gas (LNG), due to the large volume of inexpensive hydrocarbons found in shale gas. Natural gas is converted to LNG for transport overseas where placement of pipelines is not technically or economically feasible.
LNG—mainly composed of methane plus a small percent of ethane, propane and butane, and traces of nitrogen—is a gas that has been cooled to -260°F and converted to a liquid state. LNG in liquid form takes up approximately 1/600th the volume of natural gas as a vapor, making transportation more efficient and economical.
Demand for LNG is growing globally, particularly from customers in Asia. Demand growth in China, specifically, is driven by increasing demand for heating and cooking fuel, electricity generation and alternative transportation fuel.
China’s LNG demand continues to grow at a rate of approximately 40% per year. As a result, small-scale LNG production and large-scale LNG import terminals are being utilized to meet the new demands.
Feed gas pretreatment and contaminant removal are necessary to ensure the liquefaction process runs reliably without any upsets or interruptions. If feed gas is not treated to the appropriate specifications, contaminants can cause corrosion or clogging in the plant equipment, particularly in the main heat exchanger, which can reduce operating efficiency and production up time.
Meeting LNG specifications
Feed gas for liquefaction must be pre-treated to ensure proper conditioning to ensure LNG plants run without operating problems and to meet LNG sales specifications. The typical specifications to be met are:
- Hydrogen sulfide (H2S) removal to under 4 parts per million by volume (ppmv),
- Carbon dioxide (CO2) to below 50/ppmv;
- Total sulfur to less than 10/ppmv;
- Water (H2O) to less than 0.1/ppmv;
- Mercury to levels of 0.01 microgram per cubic meter; and
- Heavy hydrocarbons, C5+, including benzene, to below freezing limits in cryogenic heat exchangers, i.e., less than 0.1 mol%, and benzene to less than 1/ppmv.
The feed gas flow rate, pressure and composition will determine the design and operation of the gas pre-treatment units.
Many LNG plants use pipeline gas as feed gas. Typical pipeline gas quality specifications are shown in the adjoining table. Over time, levels of contaminants may vary within the limits. Therefore, it helps to know which gas sources—shale gas, conventional gas or associated gas—are feeding the pipeline to an LNG plant in order to establish a proper design basis. This will aid in the selection of the most appropriate technology and process configuration for the gas pretreatment section.
Depending on the feed gas composition entering the LNG plant, the design of the pretreatment section may require mercury/H2S removal, CO2 removal, water removal and hydrocarbon removal or recovery.
Mercury removal
Mercury removal is required to avoid the potential risks of mercury corrosion of the aluminum heat exchangers in the downstream cryogenic section of an LNG plant. Alloys of aluminum are prone to liquid metal embrittlement, causing serious structural damage, particularly when liquid mercury comes into contact with air or water.
As raw feed gas enters the LNG plant, it first enters a separator and then flows into the mercury removal unit (MRU). During the mercury removal stage, one approach to solve this issue is to use non-regenerative metal sulfides to remove mercury. These high-capacity mercury adsorbents, which are typically engineered using a copper-based active component finely dispersed across an alumina substrate, can result in longer lifespan, reducing the lifecycle cost of mercury removal.
After the gas flows through the MRU, it continues into the acid gas removal process.
Acid gas
An acid gas removal unit (AGRU) mainly removes acidic components such as hydrogen sulfide, H2S, and carbon dioxide, CO2, from the feed gas stream to meet the LNG product total sulfur specification and to avoid CO2 freezing—and subsequent blockages—in the cryogenic section of the liquefaction facility, respectively.
It also removes some amount of carbonyl sulfide, COS, mercaptans, R-SH, and other organic sulfur species that contribute to sulfur emissions. There are three commonly used solvent absorption processes (chemical absorption, physical absorption and the mixed solvents) for acid gas removal that can be used in LNG plants. However, formulated MDEA, or amine, solvents are most commonly used for H2S and CO2 removal.
For acid gas concentrations below 2%, NGL content below 2 gallons per thousand cubic feet, and feed flow capacities up to ~300 million cubic feet per day, Honeywell UOP has developed a simple and cost-effective “all in” adsorption process for LNG pretreatment. This solution eliminates the need for an amine unit and the management of liquid solvents.
All-in-SeparSIV is an adsorbent-based system that meets LNG specifications for CO2 (and H2S and RSH) and water and selectively removes C5+ hydrocarbons and volatile organic compounds (BTEX)—benzene, toluene, ethylbenzene and xylene. The process is based on proven technology that selectively removes impurities through a unique combination of adsorbents and a comprehensive control system. The resulting product gas is able to meet LNG specifications with very little pressure drop. With the addition of a Pressure and Thermal Swing Adsorption (PTSA) unit, regen purge gas is minimized to approximately 10% of the feed flow rate, which enables this gas stream to be used as fuel gas or it can be returned to the pipeline.
In the All-in-SeparSIV process, feed gas is fed to the Temperature Swing Adsorption (TSA) process unit, in which the impurities are adsorbed at low temperatures in a fixed-bed adsorber and desorbed by “swinging” the adsorbers from feed gas temperature (low) to regeneration temperatures (high) with hot regeneration gas.
With the proper portfolio of UOP proprietary adsorbents, multiple impurities including CO2, water, C5+ heavy hydrocarbons and BTEX can be removed simultaneously.
The adjoining process flow diagram depicts an All-in-SeparSIV system with a TSA followed by Pressure-Temperature Swing Adsorption (PTSA), which enables the regeneration purge gas to be minimized. In this configuration, water, C8+ hydrocarbons and BTEX are removed by the TSA and CO2 (and H2S and RSH), while C5-C7 hydrocarbons are removed by the PTSA.
The treated gas exits the adsorbers and is then filtered and delivered to the customer’s downstream processes.
Water and mercaptans
The molecular sieve unit design and performance are critical to assure all product specifications are met. Molecular sieves are used to dry the water-saturated gas leaving the AGRU to below 0.1 ppmv to avoid hydrate formation and freezing in the cryogenic section of the liquefaction unit. It can also be used for removal of mercaptans and other sulfur compounds to meet a total sulfur product specification of 10 parts per million or lower.
Molecular sieve dehydrators are typically installed in parallel beds of two, three or four vessels upstream of the liquefaction unit.
While moisture removal is traditionally done with smaller pore-sized molecular sieves, mercaptan and sulfur removal is done with larger pore types. 5A type molecular sieve is used for trace removal of H2S and mainly for removal of light mercaptans (C1/C2-SH), while 13X molecular sieve is used for adsorption of heavy and branched mercaptans.
The molecular sieves are produced to such precision that there is no spread in the pore size distribution. The standard zeolites each have a specific pore size, unlike silica gels and activated alumina that exhibit a skewed bell-shaped distribution curve with a tail. The molecular sieves can therefore target very specific separations, as molecules which are larger than the pore sizes are excluded while smaller ones can enter the pore structure.
In order to optimize the size and improve the performance of the molecular sieve units in LNG facilities, various techniques have been developed in recent years. For example, using multi-layer bed configurations of dense molecular sieves of different sizes can reduce bed voidage and reduce vessel volume.
Using high-quality molecular sieves with superior properties and improved regeneration methods can extend product life and improve reliability while also providing cost savings.
If the gas is O2-bearing, the feed gas flows into a closed-loop regeneration system. This system is used to mitigate water and sulfur formation by using a regeneration gas loop independent of the dry gas. This process removes all O2 makeup from the feed gas to prevent corrosion to the carbon steel in the cooler parts of the regeneration section of the LNG plant.
Pipeline gas is usually considered lean with respect to ethane, propane, and butane as these components are normally recovered to make higher value NGLs, while reducing the BTU value of the gas to acceptable levels. The levels of C5+ hydrocarbons may become elevated if an upstream NGL recovery plant goes offline or if certain lean gas wells do not flow through an NGL recovery plant at all.
Freeze-up problems
Since NGLs have already been extracted from pipeline gas in most cases, the primary purpose of removing heavy hydrocarbons upstream of an LNG facility is to prevent freezing in the downstream liquefaction section that could result in blockages and reduced capacity.
Using cryogenic technology is not the most cost-effective method to remove small quantities of C5+ hydrocarbons, due to the high capital and operating costs associated with expanders, columns and compressors. Additionally, there are process challenges since there may not be sufficient liquids to provide scrub column reflux during startup, and it may be necessary to purchase NGLs to make the process work.
For lean gases where the primary purpose is removal of trace heavy hydrocarbons and not NGL production, adsorption technology such as the SeparSIV process can offer a significant advantage.
The primary reason for this is that an adsorbent-based system operates at high pressure with a low pressure drop and does not require an expander and compressor commonly found in an NGL extraction unit. The adsorption system also has the advantage of removing heavy components without removing lighter hydrocarbons.
Therefore, the LNG heating value is comparable to that of the pipeline feed gas.
The primary differences between a molecular sieve dehydration unit and an adsorbent-based hydrocarbon removal unit are that hydrocarbon removal units generally have a shorter adsorption time of two to three hours, use series cooling and heating regeneration, require the use of internal insulation for the adsorbers to minimize regeneration heat requirements, and use different adsorbents.
However, these flow schemes do have a successful history as they are similar to CO2 removal in peakshaver units which run on fast cycles, and they may also use internal insulation to minimize the quantity of regeneration gas.
When feed gas is rich and the operator wishes to both recover NGLs and produce LNG, an NGL recovery unit can be integrated with the liquefaction unit. UOP refers to this as the Advanced Natural Gas Liquids Extraction (ANGLE) process. This integration makes use of shared equipment and refrigeration load to enable a very efficient and cost-effective solution to produce two value-generating products.
Cloud-based service
Some of challenges faced by operators include unplanned downtime, underperforming assets, managing human capital and meeting emission regulations. These challenges can be addressed in part by using Honeywell Connected Plant Services (CPS), a cloud-based service that will monitor, predict and improve plant performance by connecting plant data with Honeywell UOP analytical expertise. UOP’s Process Reliability Advisor and Process Optimization Advisor assess unit operation and process constraints using key process indicators built from UOP’s process models and operational experience.
CPS also provides early event detection to diagnose and mitigate issues, using embedded cause-and-effect relationship models. With this level of insight, a customer is able to improve process reliability—resulting in increased production yields, and overall operational efficiency.
Modular equipment
Engineering, procurement and construction contractors, and LNG owners and operators often wish to have process technology delivered as a modular equipment package. Modular fabrication offers several advantages over stick-built construction, including quality control, faster execution schedule, having a single point of accountability, lower total installed cost and reduced risk of cost escalation and schedule delays.
Honeywell UOP offers pretreatment solutions on truck-transportable skids for small to mid-scale LNG projects and large modular designs up to 1 billion cubic feet per day for baseload LNG projects. UOP has an extensive modular portfolio that spans refining, petrochemicals, renewables and gas processing technologies that also has been defined for decades. With more than 1,500 modular units in operation, UOP’s modular offerings provide a proven cost-effective solution to address the customer’s gas treating challenges.
LNG is in high demand in many countries, creating an export opportunity for U.S. producers. The selection of the most appropriate gas pretreatment technologies for LNG plants being fed with pipeline quality gas is very case-specific.
The most relevant parameters to be considered in the selection will depend on the conditions and objectives of the LNG project, including the required capacity of the trains in the plant, the operations philosophy and the project investment criteria for the project. Depending on the composition of the feed gas, there are a variety of design options that operators can choose from when partnering with Honeywell UOP.
Raj Palla is senior manager of gas processing, and Trevor Smith is senior product line marketing manager for Honeywell UOP USA.
Recommended Reading
Upstream, Midstream Dividends Declared in the Week of July 8, 2024
2024-07-11 - Here is a selection of upstream and midstream dividends declared in the week of July 8.
Solaris Stock Jumps 40% On $200MM Acquisition of Distributed Power Provider
2024-07-11 - With the acquisition of distributed power provider Mobile Energy Rentals, oilfield services player Solaris sees opportunity to grow in industries outside of the oil patch—data centers, in particular.
Trio Chairman Robin Ross Named CEO Less Than a Month After Return
2024-07-15 - Robin Ross, who last month returned to Trio Petroleum as board chair, has been named CEO while predecessor Michael Peterson will remain as a consultant.
Liberty Energy Warns of ‘Softer’ E&P Activity to Finish 2024
2024-07-18 - Service company Liberty Energy Inc. upped its EBITDA 12% quarter over quarter but sees signs of slowing drilling activity and completions in the second half of the year.
Equinor Subsidiary Contracts Valaris Drillship Offshore Brazil
2024-07-22 - Valaris and Equinor Energy do Brasil’s multi-year contract is valued at approximately $498 million.
Comments
Add new comment
This conversation is moderated according to Hart Energy community rules. Please read the rules before joining the discussion. If you’re experiencing any technical problems, please contact our customer care team.