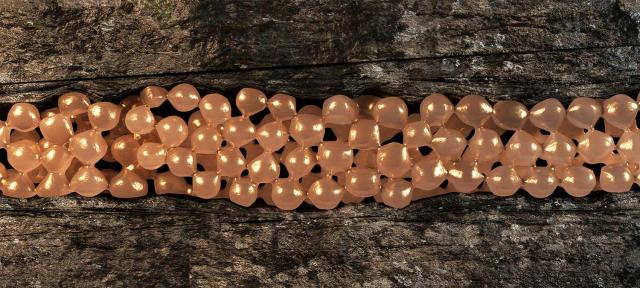
PropCure on-the-fly curable resin coating is added directly to the blender tub during hydraulic fracturing. (Source: Hexion)
Presented by:
Editor's note: This article originally appeared in the April issue of E&P Plus.
Subscribe to the digital publication here.
Proppant flowback continues to be a challenge for operators in the oil and gas industry. It has been well documented how proppant flowing out of the formation can damage downhole and surface equipment once the wells are put on production. It is also well understood that production pathways for oil and gas can be restricted as proppant shifts into the wellbore and fractures pinch off near the wellbore. This can result in reduced EUR and potential long-lasting well damage. Traditional proppant flowback solutions have been an added expense that operators have a hard time incorporating into their overall budget, especially in a low oil price environment.
In 2018 Hexion launched its PropShield proppant flowback control additive. This liquid additive is added directly to the blender tub to coat the proppant as it is pumped downhole. This has proven to be a more economical solution compared to traditional means of proppant flowback mitigation. While PropShield additive has been pumped in hundreds of wells and remains in use, there are other challenges that operators have that were out of the original scope of development. These include proppant flowback control in high-temperature wells, improved crush resistance of the substrate, improved conductivity of the proppant pack and improved EUR.
New technology
Hexion has since developed a new technology: PropCure on-the-fly curable resin coating. This coating allows operators to produce curable resin-coated proppants in the blender tub. PropCure has an affinity for the substrate, seeking it out in the blender tub while leaving the equipment clean. Once downhole, the coated proppant grains bond together and create a unified proppant pack. This provides proppant flowback control at high temperatures and high well flow rates; improved crush resistance and fines immobilization; and improved conductivity of the proppant pack.
Additionally, the coating has a tailored surface chemistry that alters the relative permeability of the proppant pack, allowing improved flow of hydrocarbons. Since it is a liquid additive, PropCure offers flexibility in job design and delivers significant savings compared to traditional proppant flowback control technologies.
Application
PropCure is a two-part system that arrives on location in isotainers or totes depending on the job size. The two components are pumped through standard liquid additive pumps (gear pumps) and combine in an inline static mixer that feeds into the blender tub. The two components are pumped at a 1:1 ratio by weight. Once combined, the typical application rates are 0.5% to 1.5% by weight of sand (BWOS).
Job flexibility is a critically important feature of this technology. It can be used with any type or mesh size of proppant, including ceramic. PropCure can be added as a tail-in, lead-in, combination of tail-in and lead-in or pulsed depending on expected proppant flowback regimes. It can also be pumped during 100% of the stage as long as proppant is being pumped. Optimization of the job can take place once field, formation and flowback regime characteristics are fully understood.
Laboratory testing
Measuring bond strength has been an important aspect in the development of PropCure coating to ensure proppant flowback control can be achieved. The unconfined compressive strength (UCS) test was designed to assess the bond strength of traditional resin-coated proppants but has proven useful in validating the effectiveness of PropCure. All testing done to date shows that the additive provides outstanding bond strength that is comparable to a premium traditional resin-coated proppant and is effective over a wide range of temperatures (105 F to 350 F-plus).
Third-party conductivity testing was performed to ensure that fluids can freely flow through the coated proppant pack. Data show up to 10 times improvement in conductivity observed in the standard API conductivity test at 10,000 psi compared to the control of uncoated substrate. This improvement in conductivity can be attributed to fines encapsulation and reduced fines migration.
Crush testing was used to further test and validate the coating ability of the additive to reduce proppant fines. A 40/70 Northern white mesh sand was treated with a 1% BWOS PropCure coating and subjected to 10,700-psi closure stress. The same untreated sand was used as the control. The results of the test showed the coating reduced fines generation by 44%.
Oil flow rate testing was conducted to demonstrate how the tailored surface chemistry of the coating can alter the relative permeability of the proppant pack. In this test, treated proppant is packed in a test cell and saturated with oil. After full saturation, the rate of flow is calculated. Untreated proppant is used as a control. PropCure had a flow rate that was more than two times higher than the untreated control. Running this technology even at low concentrations could reduce or eliminate the need for additional surfactants because it is acting as a long-term surfactant coating on the proppant.
Field study
A Bakken operator ran a field trial on a seven-well pad comparing three wells that utilized PropCure to four wells that used 100% uncoated frac sand. These wells had a bottomhole temperature of 270 F, laterals of roughly 10,000 ft and an estimated closure stress of 8,000 psi. The proppant usage was 200,000 lb/stage at 40 stages for a total of 8 MMlb per well. The fluid system was slickwater for all wells in the dataset. The wells with PropCure treated the first 7.5% of the sand in each stage and the last 17.5% of sand in each stage. The dosage used for PropCure was 1% BWOS.
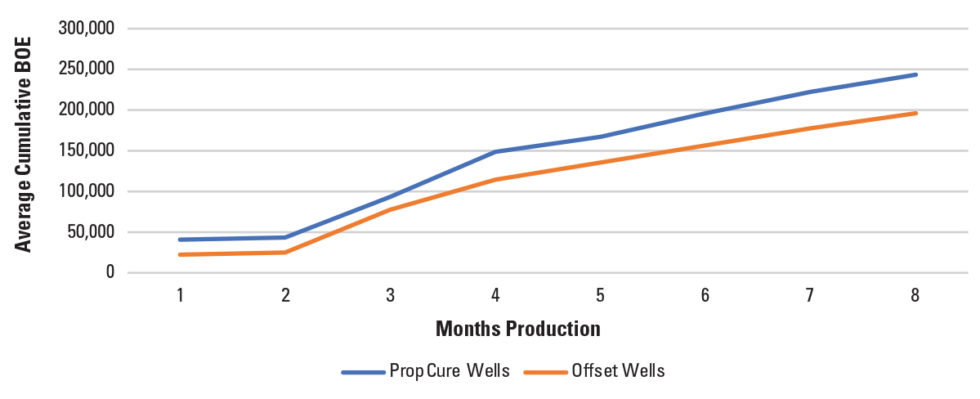
The operator reported that once the wells were put on production, there was no proppant flowback for PropCure wells while all of the uncoated offset wells continued to produce sand. Additionally, after eight months of production, it was communicated that the coating wells were producing on average 200 bbl/d more oil than the uncoated offsets.
The operator plans to continue to use the coating in their upcoming completions in the Bakken. Additional completions with multiple E&Ps are planned for most regions in North America in the coming months
Recommended Reading
Equinor to Operate Ammonia-powered Supply Vessel
2024-08-26 - Equinor said the Viking Energy Supply vessel will be the world’s first supply vessel to use ammonia as fuel.
Comments
Add new comment
This conversation is moderated according to Hart Energy community rules. Please read the rules before joining the discussion. If you’re experiencing any technical problems, please contact our customer care team.