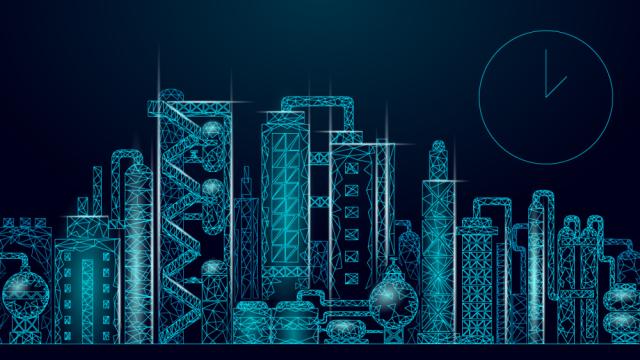
(Source: Schlumberger)
Pinpoint the cause of operational issues and remedy them before they occur
Avoid unplanned downtime that compromises system performance and productivity
Unexpected downtime cuts into production and profits, and it remains a perennial challenge for operators. As gathering systems, production equipment, and facilities handle ever-increasing throughput, operational issues can crop up more frequently—and also leave greater production volumes at stake.
To minimize the effects of lost production, engineers and operators must quickly and accurately investigate issues and get equipment back up and running. Historically, this has been challenging, because engineers have needed to rely on multiple different software applications to analyze individual system components. This makes it difficult to understand how the system interacts and can lead to improper repairs or misdiagnosis of the root cause of operational issues.
Make smarter decisions quicker with holistic system analysis
With an integrated process and pipeline simulator, engineers can combine gathering system and processing facility analysis into a single application. Simulations run in applications like these provide the insights necessary to understand how systems currently operate, how they will change over time, and what actions to take to maximize uptime and profit. The Symmetry process simulation platform breaks down internal silos with accurate system-wide modeling that helps operators reduce the risk of unplanned downtime. Available to operators through the cloud-enabled DELFI cognitive E&P environment, it can be run on any laptop and can be purchased on a subscription basis.
- Scenario 1: Understand your system
A thorough understanding of a system is an essential baseline but is difficult to obtain when working with disconnected applications. Through integrated modeling, operators and engineers can access gathering system and battery flow sheets in both steady-state and dynamic systems all in one location for a better, more complete system understanding that reveals where problems could occur.
- Scenario 2: Forecasting for increased water production
Increasing water production is a common concern, and advanced modeling enables engineers to recalculate fluid composition based on changing water cut, then automatically populate those changes elsewhere in the model file. Using these updated definitions, engineers can run simulations to see when or where there is a future risk of liquids overrunning and take action to avoid equipment damage or facility downtime.
- Scenario 3: Optimizing a new pigging schedule
Pig schedules are traditionally defined initially and then left unchanged until issues occur, which can lead to stress and panic. Through simulations, engineers can set custom criteria to trigger the launch of a pig and run multiple cycles through the model to see how the system responds. Based on this analysis, engineers can transmit new pigging schedules designed to keep downstream equipment up and running.
Learn how simulations give you the power to manage changes and understand their effects on the entire system from wellhead to product sale. Watch how to run three different scenarios so you can better understand your overall system, make adjustments as fluid composition changes, and optimize cleaning schedules to avoid unplanned downtime. Uncover the root cause of potential operational issues before they happen.