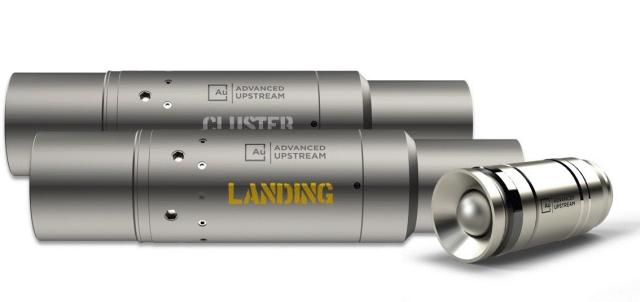
Increasing global energy demand, highly volatile oil prices, and strict environmental regulations put a lot of pressure on the oil and gas industry. The energy demand post COVID-19 is expected to increase. At the same time, energy is to be produced at a lower cost with less environmental impact. That what can not be achieved without innovation.
Advanced Upstream Ltd., a Calgary-based oilfield equipment company specializing in the engineering and production of downhole completion tools, came to the market with a revolutionary fracturing system that utilizes Contactless Sleeve Recognition (CSR) technology - Limitless™. Limitless™ enables any number of fracturing stages and non-stop stimulation without the need for well intervention. Compared to plug-and-perf, which is currently the most common reservoir access method in North America, Limitless™ has a smaller footprint, requires less equipment and personnel, and has other time and cost-saving benefits, in particular requires less water and fuel. This allows operators to improve operational efficiency and help to meet their Environment, Society, and Governance (ESG) requirements.
Limitless™ features a compact, intelligent, programmable dart made of a magnesium alloy. The dart is programmed and launched at the surface to land in a target sleeve. Reliable, microelectronic onboard sensors allow the dart to track its location within the wellbore and activate the dart before landing on to the target sleeve. After the fracturing treatment, the dart dissolves, leaving behind a large wellbore for production. A short video to LimitlessTM is provided below:
LIMITLESS™ Fracturing System - Advanced Upstream
According to Jeyhun Najafov, President/CEO of Advanced Upstream, who has decades of work experience in the oil and gas industry around the world, from the field operations to R&D, and a great passion for new technologies, “the intent in designing LimitlessTM was to provide continuous pumping operations without the need of any explosives, wireline, coiled tubing, and milling-outs”. “We wanted to develop a fracturing system that would be safe, quick, environmentally friendly, and cost-effective. We are very excited to see that after a series of successful field trials, the technology is at the commercial stage”, Mr. Najafov says.
The benefits of the system are as follows:
- Simplified process: no wireline, coiled tubing or mill-out operations
- Time reduction in completing the process: 70% time-saving per fracturing job
- Significant cost improvements: over 400,000 USD savings expected per well (depends on the well)
- Safety and quality improvements: no perforation guns, reduced crane activity, less simultaneous wellhead operations, less personnel on site
- Reduced environmental impact: over 20% water savings, 35% fuel savings and approximately 40% reduction in CO2 emissions
Cost/benefit analysis validates the success of LimitlessTM and the economic desirability of the use of the system compared to plug-and-perf, in particular for extended reach wells. Thus, for a 30 stage plug-and-perf frac (three groups of cluster perforations) compared to 30 stages with three LimitlessTM sleeves and a dart, savings per fractured stage are close to 20%. Savings can be even higher for fracturing operations in a single well pad or Simultaneous Fracturing Operations (Simu Frac – fracturing 2-4 wells at the same time).
We look forward to being your partner in setting the golden standard in completion technology.
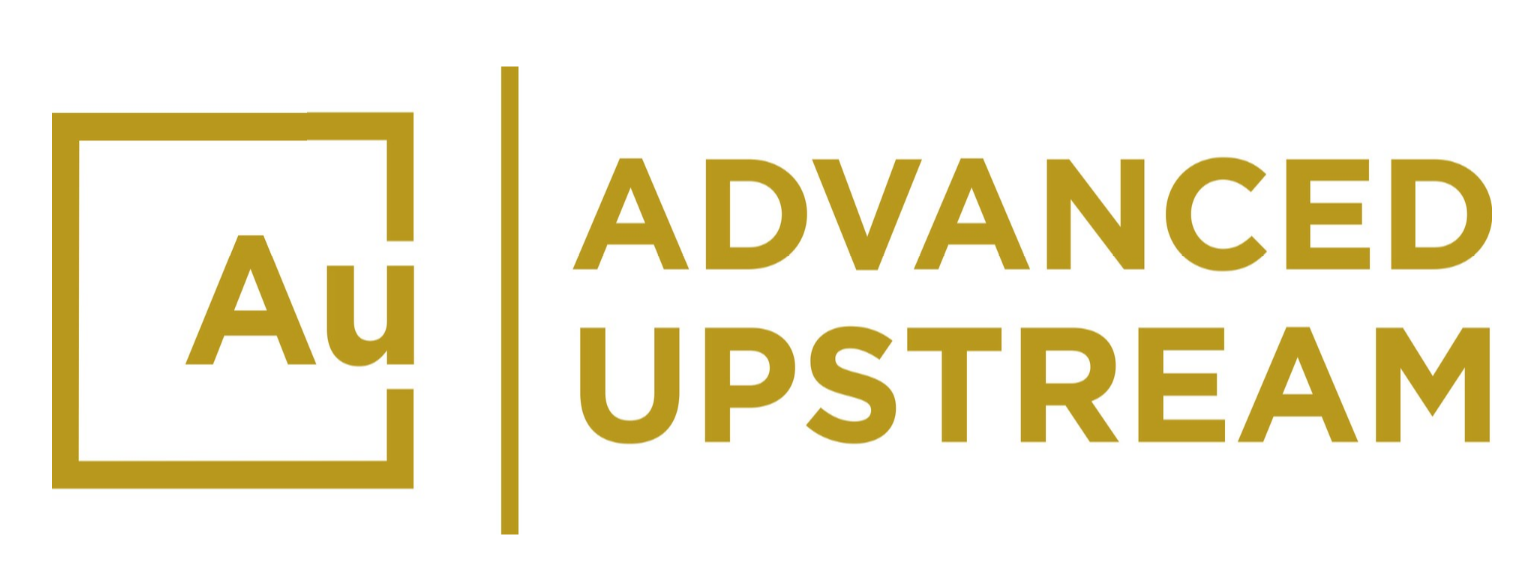
www.advancedupstream.com I info@advancedupstream.com I 1-403-862-3340