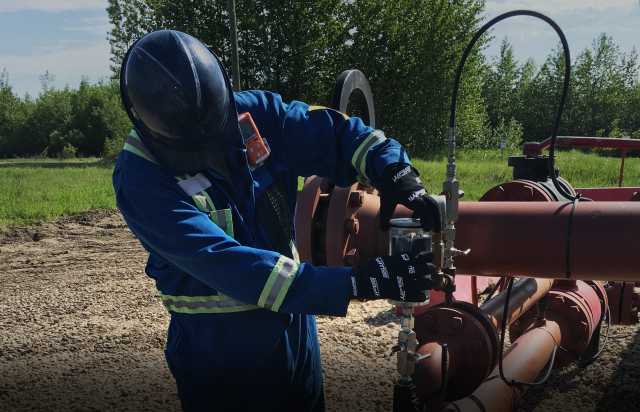
Ease of installation and service enhances the ability of a midstream operator to quickly add remote data monitoring. (Source for all photos: TOKU Systems)
[Editor's note: A version of this story appears in the June 2020 edition of Midstream Business. Subscribe to the magazine here. It was originally published June 1, 2020.]
New technologies enter the market each year, raising awareness of the need for innovation in an industry viewed by some as reliant on legacy systems and traditional work methods. When it comes to pipeline operations, midstream and upstream companies are focused on creating efficiencies in daily work methods to maximize uptime and minimize the risk of interruptions.
Field service technologies offer significant upside opportunities to ensure reliable operations for companies with extensive assets. In terms of monitoring, current methods are laborious and unreliable, and history shows the costly impact of leaks and ruptures to operations.
As the size of the workforce continues to decline and the industry loses expertise due to demographic shifts, the need for greater business efficiencies in oil and gas operations increases. This need, along with the problems of aging pipeline infrastructure, creates an immediate need for companies to improve their monitoring capabilities.
Costs of incidents
Past incidents show that the implications of a pipeline breach can last months—from detection of the leak to conducting the cleanup effort, reclaiming the land and paying the fine. Industry failures have become costlier, with reports of eight- and nine-figure cleanups and some companies losing the ability to be insured for future events.
Companies cannot afford to go weeks to months without knowing about a problem with their pipelines. Manual or noncontinuous methods of conducting pipeline checkups, such as deploying an operations team via helicopter or capturing video with a drone, are time-intensive, burdensome and unreliable.
As companies look to streamline operations and reduce costs, it is critical to evaluate opportunities for regular and continuous monitoring made available via a remote monitoring system. Having complete visibility into a pipeline will not only mitigate financial risks but also shelter a company from vulnerabilities and potential long-term setbacks.
Manual monitoring
According to estimates, if a sizeable leak or rupture is not caught within 48 hours, a company is subject to cleanup costs averaging $100,000 per day. This adds up quickly, depending on the size of the pipeline breach, and the longer it takes to detect the leak, the more the company stands to lose. It may take months to clean contaminated soil and reclaim the land—and even longer to restore the company’s losses.
Whether the liquid leak is oil emulsion or produced water, each rupture has varying consequences. For example, oil emulsions tend to collect on the surface, while produced water, along with its chlorides and other contaminants, will be absorbed into the soil. Therefore, cleanup procedures vary greatly and can often result in widespread sterilization of vegetation and natural surface water bodies. The result can be an altered landscape that impacts wildlife, vegetation and livestock.
When monitoring manually, companies must factor in the equipment and associated labor, which can force the operations team to divide resources between production and monitoring. Sometimes, it compels companies to hire additional staff for both areas. Additional monitoring costs, which may include canine inspections, vehicle-based visual surveillance and static pressure tests, can add up.
Additionally, winter and rainy seasons can add access challenges to in-person inspections, forcing the operations to consider more costly monitoring alternatives.
Businesses can also face significant fines and regulatory penalties if issues go undetected for a duration of time. These costs compound the loss of revenue associated with the facility not being permitted to flow again until the regulatory body releases it.
Pipelines run across thousands of acres—usually land that is not owned by the company—which means if the land is damaged because of the leak, the company is subject to facing lawsuits from landowners. If the land is crown land (government owned) or in watershed areas, downstream parties also will be eligible for compensation or reclamation.
If the product is marketable, the associated profit loss will impact the bottomline. It is up to the company to take the necessary operational steps to prevent a large-scale accident from happening in the future. When it comes to pipelines, leaks may be inevitable, but a quick response and thorough planning can prevent it from causing severe financial loss.
The risks associated with ruptures and leaks extend beyond the operational, material, environmental and public arenas. Negative press from a poorly managed leak detection strategy will impact the organization at the shareholder level. This results in loss of investor confidence, personal liability and long-term consequences to the reputation of the organization and its directors.
Digital monitoring
Reliable, continuous and detailed pressure monitoring provides an effective way to avoid the risks and the additional costs associated with traditional monitoring. While such monitoring requires an upfront investment, new technologies have lowered the initial investment needed to begin remote digital monitoring of assets.
These new monitoring technologies allow companies to remotely and efficiently visualize how their pipelines are operating and remain aware of any potential issues. By investing in digital monitoring systems, operators can accurately know what is happening within their pipelines and create a more efficient and cost-effective practice that will save money at the back end.
Through continuous remote digital monitoring, a company’s operations team no longer must record data collected through dated, noncontinuous methods and instead can look for trends or patterns in the data themselves that could help identify a potential issue. The time it takes to collect and analyze the data is significantly reduced as the digital system captures it in real time, allowing operators to streamline the entire monitoring process and spend time and resources elsewhere on other critical operations.
The smartphone has become an indispensable tool in the hands of any field operator. A monitoring system that provides detailed pressure data direct to a smartphone allows an operations team to check on pipeline performance throughout the day without the extra travel or scheduling to get to a computer at a field office and assess alarms. Real-time monitoring via smartphones allows teams to take prompt action.
Additionally, the analytics that a digitalized system can provide not only creates efficiencies in monitoring but also can enhance business operations. By having detailed data readily at hand through the monitoring system, machine learning or artificial intelligence can be applied so that companies rapidly gain information on trends and insights, such as the pipeline’s week-over-week, month-over-month or year-over-year health. Without quality data, companies obtain no value from the numbers received from traditional monitoring processes.
Having detailed and continuous pressure monitoring of a pipeline can provide insight into the performance of a system’s equipment. Whether it is a downhole pump, a surface injection pump or some form of automated valve control, all parts will have performance characterized by the pressure changes that are produced in the pipelines to which the pieces are connected.
Reactive versus proactive
When they shift from reactive to proactive monitoring, companies can visualize ongoing changes in pumping equipment, have insights into operational efficiency and gain information on performance degradation. Companies can practice proactive maintenance, which avoids the higher costs of an unexpected failure and associated downtime, by identifying when a pump begins to fail.
Furthermore, when an operator covers the remote operations, field and pipeline systems with a network of remote sensors connected to a single platform, they can visualize the entire pipeline operation. This networked visibility enables operators to see and track pigs, catch valve failures and know when, where and how slugs are forming. With new technologies, companies can implement this type in a few days and at a fraction of the cost.
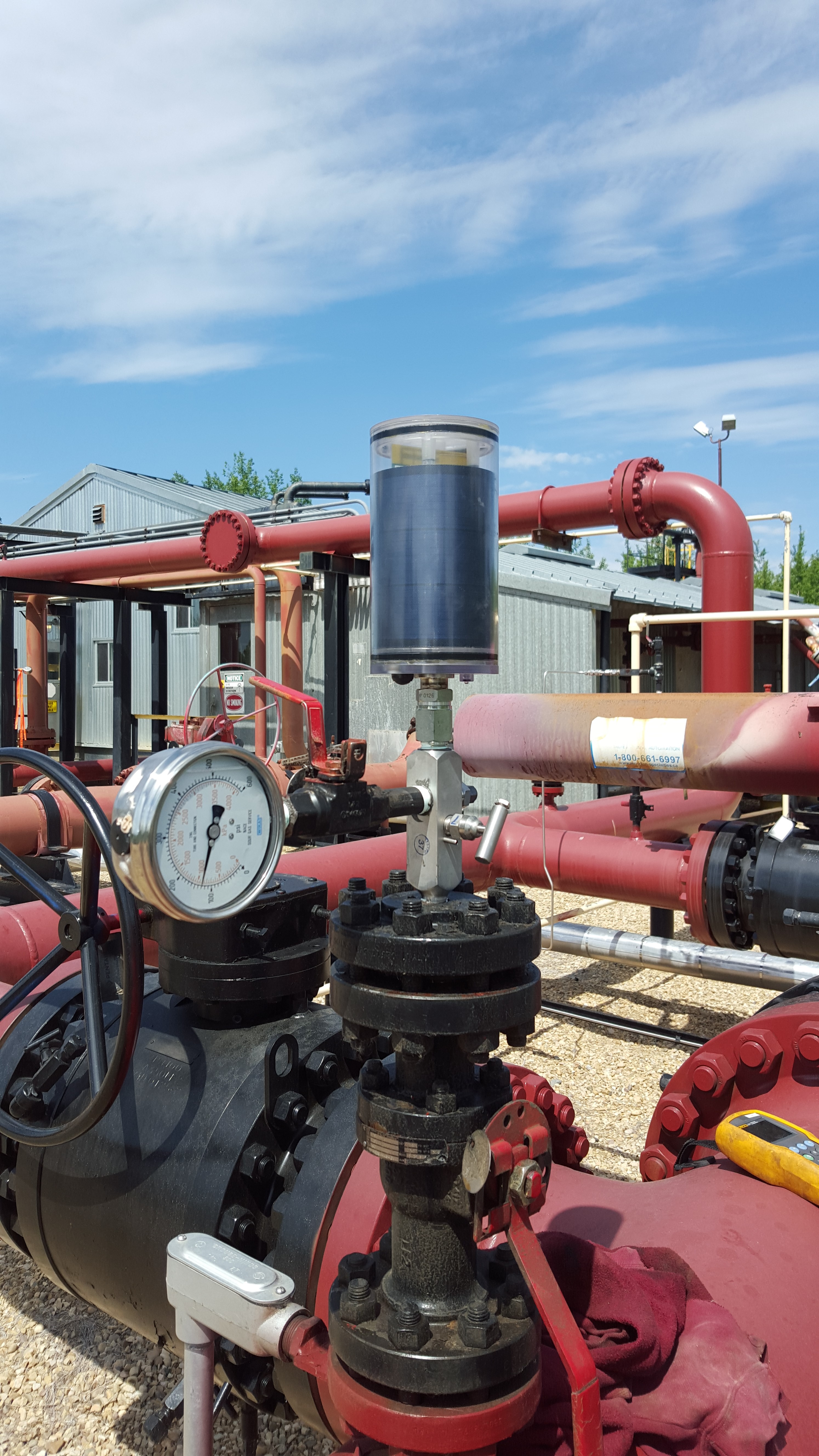
If a monitoring system detects a change in pipeline pressure, it sends alerts and notifications immediately to an operations team. The team can then quickly investigate the specific location within the pipeline to identify if there is an issue and, if a problem is found, address it early, thereby preventing a significant leak, blockage or other costly problem.
An example of a remote digital monitoring system is the TOKU device, an intelligent plug and play service that informs operators of their pipeline operations’ health from a cloud-based digital platform, available on any device, including web and mobile applications. The TOKU device can be implemented without an engineering and installation specialist or a design fabrication team. It sends operators high-resolution, per-second data on the changes in pipeline pressure, alerting them of any conditions that could jeopardize safety, efficiency or performance.
With its own battery, solar cell and a built-in cell antenna, the device has autonomous operational capabilities that allow it to automatically update and stay connected to the user. It facilitates significant cost savings and efficiencies, and it mitigates operational risk—creating new growth possibilities for companies.
Given that current market conditions have created significant challenges in the oil and gas industry, companies must make an effort, now more than ever, to adopt new technologies that reduce costs and create efficiencies. Continuous monitoring can be part of that effort, and remote digital monitoring systems reduce uncertainty by allowing companies to maintain awareness of their operations virtually and in real time.
Dr. Toku Ito is CEO and founder of TOKU Systems, a Calgary, Alberta-based developer of remote monitoring systems for oil and gas companies.
Recommended Reading
Chevron Boosts Oil, NatGas Recovery in Gulf of Mexico
2024-09-03 - Chevron’s Jack/St. Malo and Tahiti facilities have produced 400 MMboe and 500 MMboe, respectively.
CNOOC Makes Ultra-deepwater Discovery in the Pearl River Mouth Basin
2024-09-11 - CNOOC drilled a natural gas well in the ultra-deepwater area of the Liwan 4-1 structure in the Pearl River Mouth Basin. The well marks the first major breakthrough in China’s ultra-deepwater carbonate exploration.
Southeast Asia NatGas Projects Could Unlock $100B Boom- Rystad
2024-07-17 - Southeast Asia's offshore gas industry is set for a $100 billion boom by 2028, driven by a flurry of final investment decisions by oil and gas majors and national oil companies, according to Rystad Energy.
Comet Ridge Awarded Mahalo Far East Extension for 6-year Term
2024-07-22 - Comet Ridge was awarded 100% ownership and operator of Australia’s Mahalo Far East Extension for an initial term of 6 years.
BP Takes FID on US GoM Development Kaskida
2024-07-30 - BP has taken a final investment decision on its Kaskida development in the U.S. GoM, with production of 80,000 bbl/d expected to start flowing in 2029.
Comments
Add new comment
This conversation is moderated according to Hart Energy community rules. Please read the rules before joining the discussion. If you’re experiencing any technical problems, please contact our customer care team.