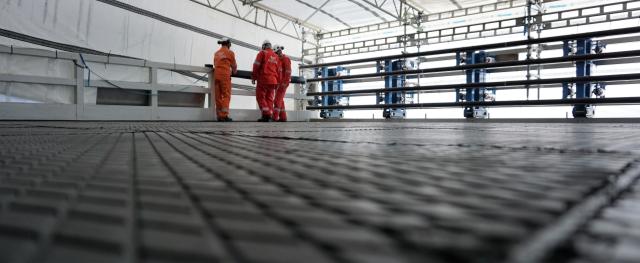
The unique features of Vikodeck make it a good fit for a large variety of applications. (Source: Trelleborg)
Fire protection is a critical part of onboard safety in harsh offshore environments. Reducing the risk of fire hazards is a vital and challenging part of designing and engineering offshore oil and gas installations. With these challenges in mind, Tony Westerlund, senior design engineer at Trelleborg’s offshore operation, looks at why Vikodeck could be the next generation of corrosion-free, rubber-based fireproofing that ensures the protection of people, structures and equipment.
Designed to offer surface protection against blast, jet and pool fire in harsh demanding environments, Vikodeck provides corrosion protection and anti-fatigue dampening support for the comfort and safety of employees. The intrinsic flexibility of the system’s rubber tiles allows them to withstand movement and impact that could possible damage or crack rigid systems.
Manufactured using Trelleborg’s next-generation Firestop material, Vikodeck tiles are lighter and thinner than any current passive fire protection materials available to the market and can be tailored to withstand various chemical and mechanical conditions depending on application and customer specification. As a flexible decking fire protection material, Vikodeck is capable of withstanding harsh conditions while providing corrosion, environmental, impact and fire protection.
Westerlund said, “Vikodeck is very simple to install, remove and re-apply to structures as it is glued directly onto a surface, including flooring, walls, roofing or any surface needing protection. It can be used for protection in several places, be it in a load bearing application, an escape route or a critical control room.”
Without fire protection, these areas could rapidly heat up and risk collapse or failure. A typical hydrocarbon fire can hit between +1,100 C to +1,200 C (2,012 F to 2,192 F) rapidly and continue to burn at this heat for a long period of time.
“One vital area of application for Vikodeck is laydown deck areas, which are susceptible to regular impact and abrasion when containers are loaded, dropped and transported,” he said. “This is due to the tile’s strong properties for protection against mechanical wear and tear. Since these areas tend to be close to the living quarters on offshore platforms, the dampening and noise reduction properties of the material are a real advantage.”
Certified For Extreme Conditions
Vikodeck tiles were tested in the most extreme conditions to simulate a worst-case scenario on an 8-sq-m (86-sq-ft) deck mounted in the roof of a testing chamber at an independent testing facility to gain DNV-GL certification. Both securing options typically used to glue the tiles to the surface were tested and include an adhesive and a sealant.
“Vikodeck has been in constant development since its introduction in 2000. The DNV-GL certification ensures functionality of product performance in a fire scenario,” Westerland said.
For diverse applications, Vikodeck tiles are available in four types:
• Vikodeck HF protects according to certified hydrocarbon fireproofing requirements;
• Vikodeck JF protects and insulates assets in a possible jet fire scenario;
• Vikodeck S protects structures from hang fires; and
• Vikodeck L is for areas that need sound, impact, weather or tear protection.
Vikodeck tiles are normally delivered in 1-sq-m (10.7-sq-ft) sheets but can be drilled, cut or shaped to fit the area of installation to suit any surface. The tiles feature insulation to isolate fire temperatures and ensure a nonslip surface for worker safety. The flexibility of these rubber-based tiles ensures they can take up movement in any direction, reducing the likelihood of cracking. Similarly, as the tiles are regularly exposed to the sun, the system ensures UV and ozone protection so it does not damage over time.
Recommended Reading
Mexico Pacific Signs Long-term SPA with Korea’s POSCO International
2024-08-29 - Mexico Pacific and Korea’s POSCO International Corp. signed a 20-year sales and purchase agreement for the Asian company to acquire 0.7 mtpa of LNG from the proposed the Saguaro Energía LNG facility on Mexico’s Pacific Coast.
Industry Warns Ruling Could Disrupt GoM Oil, Gas Production
2024-09-12 - The energy industry slammed a reversal on a 2020 biological opinion that may potentially put an indefinite stop to oil and gas operations in the Gulf of Mexico—by December.
Chevron Warns of Ongoing Uncertainties in Venezuela After Elections
2024-08-08 - Chevron, the only U.S. company operating in Venezuela, warned of ongoing uncertainties in the South American after recent presidential elections, and the company has already said it will not invest new capital into the country.
Zachry Proposes Settlement Agreement to End Golden Pass LNG Standoff
2024-07-22 - Zachry, an engineering contractor for the Golden Pass LNG project, submitted a settlement agreement in bankruptcy court that would allow Exxon Mobil and QatarEnergy to move forward with the delayed project.
New FERC Commissioner Calls Slow Permitting Process ‘Huge Problem’
2024-09-17 - FERC Commissioner David Rosner said the commission is aware that the permitting process is too slow overall at Gastech Houston 2024.
Comments
Add new comment
This conversation is moderated according to Hart Energy community rules. Please read the rules before joining the discussion. If you’re experiencing any technical problems, please contact our customer care team.