
(Source: Hart Energy; Shutterstock.com)
[Editor's note: A version of this story appears in the June 2020 edition of E&P. Subscribe to the magazine here. It was originally published June 1, 2020.]
Operators’ needs for operational efficiency, especially today, are driving them to continuously try different technologies such as new bits, bottomhole assembly (BHA) components, string designs, well designs and new operating parameters for those technologies. This takes time to implement, can have some trial and error and always requires performance tracking (time) and cost tracking to determine the overall performance gains well by well.
The oil and gas industry had “Big Data” before that term was used as widely as it is today. Those data were used to provide broad drilling key performance indicators (KPIs) such as days versus depth curves, slide versus rotate percentages, tripping times and has been used to track nonproductive time (NPT). Data quality, computing and analytical resources limited more detailed performance evaluation, and performance improvement generally didn’t require anything more granular. The unseen consequence was often more lengthy and repeated trial and error loops, untracked procedural changes as well as large amounts of invisible lost time and flat time. All of this adds to drilling risk, HSE events and hidden costs.
KPI improvements
As on-bottom performance improvement slowed, and market conditions changed, operators have looked for additional methods to continually improve to reduce costs and improve performance to satisfy investor demand for return on investment (ROI), especially in higher volume markets such as those in the U.S. onshore. The adoption and industrialization of drilling data acquisition systems and cloud-based computing for analytics enabled operators to utilize their Big Data, and the analytical capabilities cloud computing offers to develop and refine more granular KPIs to deliver operational efficiencies to the market are demanding. This change has brought other challenges.
More detailed KPIs for drilling and related activities require access to high-quality datasets. Operators realized data quality issues, such as sensor calibration, data frequency (10 seconds, 5 seconds, 1 second, etc.), consistent variable naming and data storage, all needed to be addressed to apply algorithms from simple logic statements to more complex mathematical calculations to derive new and improved KPIs.
These challenges are being met by operators and service companies by standardizing rig data acquisition systems, industrializing rig connectivity and utilizing cloud-based systems to store the data and have those readily accessible. The result is an internal understanding of the performance gains, from on-bottom drilling performance, tripping times and connections times. These can be subdivided by well, hole section, bit type, BHA type, formation, operating parameter and a host of other categories to develop a more detailed understanding of where and how performance gains have been achieved. With the advent of cloud computing and remote access, these indicators are available at the rig site to track performance in real time down to minutes compared to relevant offset wells.
Increased data sharing
The adoption of Big Data by the oil and gas industry is giving operators the tools to internally assess new methodologies, but there is a need to scale this even further. The industry is moving toward increasing data sharing among operators. The development of open forums (such as Open Subsurface Data Universe) for subsurface data sharing is one such example. Sharing KPIs and micro-KPIs to more effectively benchmark performance across a basin will incentivize the industry to deliver operational efficiencies to match peer groups.
A challenge for those operators willing to lead the way on creating a data ecosystem for their drilling operations includes data quality control, data accuracy, data aggregation, storage and security, standard analytics logics and calculations, and service company neutrality.
Shared KPIs
A proposed solution to these challenges was created so operators could share KPIs and micro-KPIs among themselves and quickly drive drilling operations to best in class.
First, the data need to be aggregated from different sources such as electronic drilling recorders, MWD tools, and planning and reporting systems. After this, aggregating the data needs to be quality controlled so the raw data coming in are correct. The data need to be stored on secure servers available for approved users with a robust and consistent analytics engine applied to the data to derive the KPIs.
Another challenge is how to show enough valuable information without disclosing any intellectual property the operators want to keep private. This is accomplished by creating a quid pro quo environment where operators can only see the level of details on KPIs they are willing to share and all other operator names are hidden.
The value proposition of this information is directly linked to its accuracy, so these KPIs must be generated from raw sensor data to avoid any bias or reporting errors. These KPIs also must be updated in real time so all users have the most relevant information readily available. From here, the utilization of the information by each operator will drive value. Data must also be complete across a basin so all wells, good and bad, are available so benchmarking isn’t skewed to misrepresent overall performance.
One of the pioneers of this project is Noble Energy. In its desire to further increase its drilling operations efficiency, the company started to contribute high-quality KPIs and micro-KPIs to a third-party vendor-agnostic platform. Some of the value extracted from this information includes
- Realistic benchmarking operations against other players in the basins they operate in and use of this information to drive their own operations to those levels of efficiency;
- Compare in real time how their BHA, string and/or procedure changes are improving performance when compared to others; and
- Provide investors with peer group benchmarking to demonstrate industry-leading performance and continual improvement.
An example of such a system is shown in Figure 1. In this example, well days versus measured depth are displayed, where the colored curves are the subject operator and the gray curves are the operators within a user-selected radius. The analysis can be performed for total drilled days, average ROP, rotating ROP, sliding, ROP, drilling connection times and tripping speeds, to name a few. All either on a radial search by county, spud date and detailed by sections.
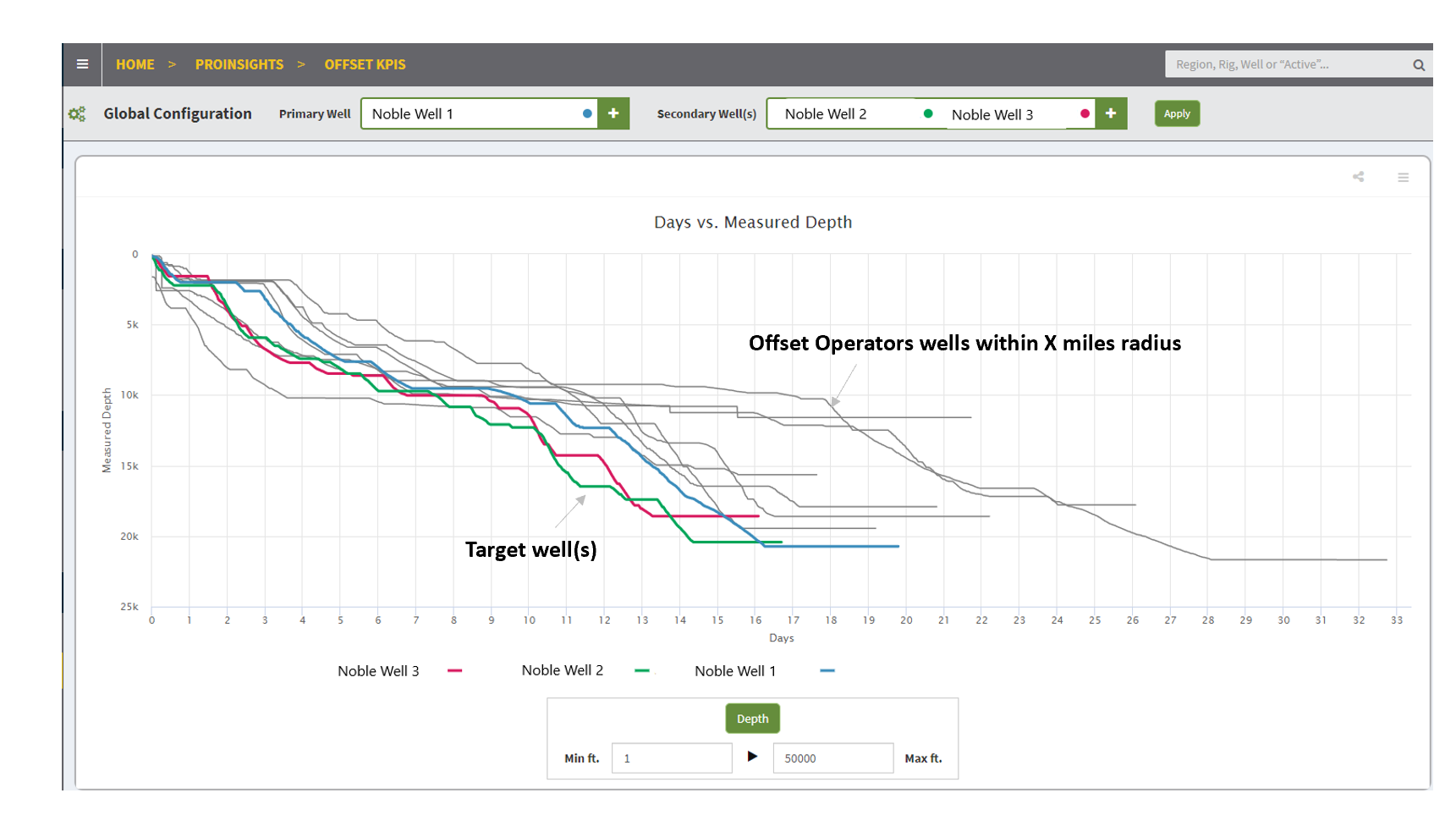
All of these KPIs provide each participating operator with a clear comparison of their overall and detailed performance. Using those comparisons enables operators to focus on critical performance improvement initiatives specific to their operating area being achieved by peers, which will deliver a step change in performance, time and costs.
As the appetite for operator data sharing increases, these databases and KPIs will grow more detailed and complex to include but not be limited to NPT, costs and parameters—driving continuous improvements for operators and the industry as a whole. As data sharing becomes more accepted, moving from anonymized to open benchmarking may become standard practice. Including additional well construction information, data often available through regulatory sites but delayed in availability may also become more accepted.
There are still additional ways data can be shared in the future, promoting multifaceted and complete benchmarking for more robust analysis. To progress situational awareness, gathering and sharing HSE data could greatly benefit the industry. A tie in with service companies’ data streams will award top performers and drive innovation and reliability to meet the market needs of both the operator and service company. What is more, once the groundwork for data acquisition and streaming capabilities are established for completions and production data, there is potential for them to see the same benefits as drilling: the ability to see how others are designing, implementing and performing, with the end goal of presenting to partners and/or investors how they are performing accurately.
RELATED CONTENT: Completions Lessons: Cracking the Shale Code
Recommended Reading
Viper Buys $330MM Midland Interests in Shadow of $4.5B Dropdown
2025-01-31 - Viper Energy said that in addition to a $4.45 billion dropdown by Diamondback Energy, the company would also purchase royalty acreage in Howard County, Texas, for $330 million.
Prairie Operating to Buy Bayswater D-J Basin Assets for $600MM
2025-02-07 - Prairie Operating Co. will purchase about 24,000 net acres from Bayswater Exploration & Production, which will still retain assets in Colorado and continue development of its northern Midland Basin assets.
Ovintiv Closes Montney Acquisition, Completing $4.3B in M&A
2025-02-02 - Ovintiv closed its $2.3 billion acquisition of Paramount Resource’s Montney Shale assets on Jan. 31 after divesting Unita Basin assets for $2 billion last week.
Murphy Oil Buys BW's Pioneer FPSO for $125MM
2025-03-13 - Murphy Oil Corp. is buying an FPSO from BW Offshore for $125 million.
Summit Acquires Moonrise Midstream Assets to Alleviate D-J Constraints
2025-03-10 - A Summit Midstream Corp. (SMC) subsidiary will acquire Moonrise Midstream from Fundare Resources Co. in a cash-and-stock deal valued at $90 million.
Comments
Add new comment
This conversation is moderated according to Hart Energy community rules. Please read the rules before joining the discussion. If you’re experiencing any technical problems, please contact our customer care team.