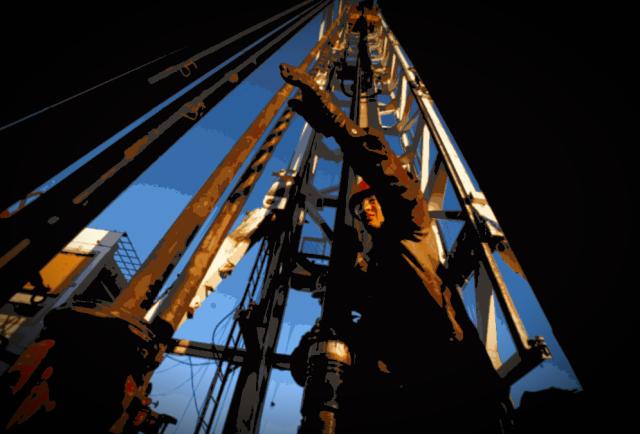
(Source: Hart Energy)
Wellbore quality is one of the most pressing issues facing the modern oil and gas industry. A “drill faster” performance mantra based on reaching TD as quickly as possible and moving to the next well drove massive improvements in efficiency over the past decade, but what operators are now finding out in many instances is that those efficiency gains came at the cost of wellbore quality.
Tortuous wellbores, which twist and turn due to frequent need to steer the wellbore back to plan, cause significant issues when it comes to completion and production operations, such as increased torque and drag, higher potential for tubing/casing wear, equipment that cannot fit downhole within OEM tolerances, and decreased production from liquid drop-out, among many others. In an industry that is now surviving at sub-$60 per barrel WTI pricing, addressing these challenges while remaining focused on achieving economic drilling times is more critical than ever. Through its high-resolution MicroGuide tortuosity logs, Gyrodata aims to provide the industry with a means of identifying the anomalies that happen between the MWD surveys and understanding microdoglegs and sideloading forces in ways previously impossible.
Technology
Gyrodata introduced MicroGuide, a novel wellbore tortuosity log, to provide operators with a way of obtaining and analyzing high-density wellbore tortuosity data. The system looks at tortuosity from survey stations on the wellbore log via gyroscopic tools. The system defines reference lines for the wellbore path and displacements from that path based on the received data, allowing 3D visualization of the wellbore. The use of the high-density, high-resolution data from the system’s 1-ft log intervals provides insight into accurate wellbore geometry, which would often go undetermined when using data from other survey types. Obtaining and analyzing such detailed wellbore geometry and tortuosity data allows the operator to make informed decisions on where to place artificial lift, rod guides, and other production equipment.
Wellbore tortuosity has a significant impact on the design and installation of artificial lift equipment. The well path, and tortuosity, is commonly determined from data based on MWD technology and stationary directional surveys at stand-length intervals. Making decisions with low-quality data received in such limited quantities made proper production equipment placement an exercise in assumptions and guesswork, ultimately causing a substantial amount of unpredicted failures. Wells with more complex geometry and challenging downhole conditions complicate an already-fraught issue, leading to a higher failure rate in production equipment, as well as increased downtime, reduced run life, and lost production. By using MicroGuide wellbore tortuosity logs to make informed decisions, operators can make better decisions to mitigate these issues.
Case studies
An operator was experiencing issues with rod guide failure in one of their wells. Though there were several areas of concern throughout the well, the failures were concentrated primarily in the last 1,900 ft of the well. These repeated failures were causing the operator to exceed AFE on the well, which presented an economic challenge to their future production efforts. To better understand the cause of failure and determine an optimal means of addressing it, the operator decided to run Gyrodata’s MicroGuide wellbore tortuosity logs to obtain detailed information on true downhole conditions.
As the operator previously only had MWD survey data available, it was critical that they obtain higher density data to understand tortuosity over the entire length of the well in greater detail. Processing measurements in 1-ft increments versus typical stand-length intervals provided the operator with a much clearer picture of the downhole conditions and issues that were causing the repeated failures with their rod guides. The MicroGuide analysis showed that there were several severe spikes in sideloading force against the tubing (Fig. 1) that were not visible in the MWD data. The analysis also revealed that the casing was helically buckled from 8,700 to 10,560 ft, which was causing the increased sideloading force throughout the section as well as the issue with rod guide parting. Without such detailed wellbore tortuosity information, the operator would have had inadequate data on the bottom hole to properly make decisions on the best artificial lift method to meet their operational and financial objectives.

Another operator found that one of their wells had significant issues with rod parting and tubing leaks, primarily from 2,500 to 5,550 ft. The repeated failures were not only costly from an equipment perspective but were continually impacting production, rapidly transforming the well into an economic drain on the operator. To better understand the potential cause of the problems and determine a solution, the operator decided to run Gyrodata’s MicroGuide wellbore tortuosity logs to acquire the information necessary to understand the performance-mitigating downhole phenomena.
The operator needed the detailed wellbore tortuosity data to remedy the low-quality survey information from the original MWD surveys, which had not showed that there was any cause for concern. Though the operator opted to run the analysis over the entire depth of the well, they indicated that focus should be concentrated on the areas of repeated failure. An immediate red flag raised by the MicroGuide logs was missing MWD survey data from 0 to 2,700 ft, where there were two significant tortuosity spikes. The logs also revealed that there was significant sideloading force against the tubing in the identified problem area from 2,500 to 5,550 ft, indicating that the root cause of failure was severe tortuosity (Fig. 2). Understanding that the problem was not equipment-based but rather the result of well design, the operator was able to develop a plan to properly place the rod guides and prevent the occurrence of similar issues in future wells.

Moving forward, it is imperative that the oil and gas industry understand the role that wellbore quality plays in overall profitability. Despite ongoing challenges with approved spend in an industry that remains capital-constrained, operators need to take a harder look at what kind of well they are drilling and how they can optimize production from those wells. Much has been said in journals and industry papers on the need for accelerated technology adoption and digitalization in the industry, and tackling the fundamental issues at the heart of low wellbore quality means investing in a means of understanding tortuosity in a way that hasn’t been done before. With MicroGuide, a means of visualizing wellbores in 3D and mitigating the problems that plague wells with lower production and higher equipment failure rates is a clear solution.
RELATED:
Hart Energy’s 2020 Artificial Lift Technology Showcase (featuring Gyrodata)
Recommended Reading
TotalEnergies Signs LNG Agreements in China, Turkey
2024-09-19 - TotalEnergies announced two separate long-term LNG sales in China and a non-binding agreement with Turkey’s BOTAŞ in an effort to grow its long-term LNG sales.
Quantum to Buy Carlyle’s Power Producer for $3B
2024-08-05 - Managed by investment firm Carlyle, Cogentrix Energy’s platform is comprised of 5.3 gigawatts of natural gas-fired power plants, located throughout electricity servicers PJM, ERCOT and ISO-NE.
WoodMac: Are MidEast, Asia NOCs Poised For M&A Resurgence?
2024-07-18 - International M&A spend by national oil companies (NOCs) has dwindled from nearly 50% to less than 5% today. But Wood Mackenzie researchers see NOCs playing a larger role in international M&A in the future.
Kimmeridge Signs Natgas, LNG Agreement with Glencore
2024-09-19 - Under the terms of the agreement, set to be finalized later this year, Glencore will purchase 2 mtpa of LNG from Commonwealth LNG and source natural gas from Kimmeridge Texas Gas.
Beyond Energy: EnergyNet Expands Marketplace For Land, Real Assets
2024-09-03 - A pioneer in facilitating online oil and gas A&D transactions, EnergyNet is expanding its reach into surface land, renewables and other asset classes.
Comments
Add new comment
This conversation is moderated according to Hart Energy community rules. Please read the rules before joining the discussion. If you’re experiencing any technical problems, please contact our customer care team.