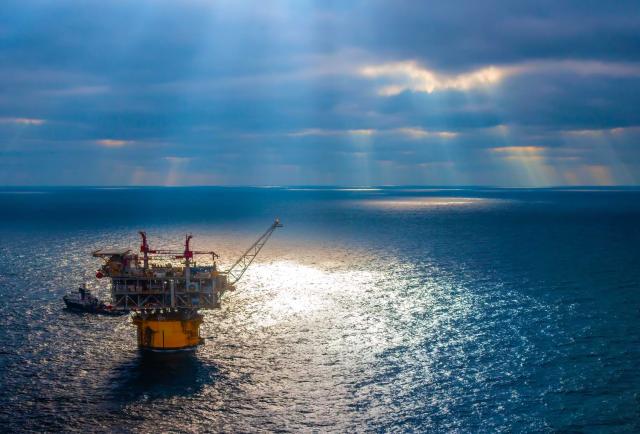
(Source: Marc Morrison/marcmorrison.com)
Presented by:
Editor's note: The full version of this article originally appeared in the February issue of E&P Plus.
Subscribe to the digital publication here.
It has long been a dream for offshore energy explorers to go where many have not gone before. That means searching for oil and gas deposits in deeper waters and farther from shore than previously charted.
Many issues arise from these special projects: safety, time and cost. Keeping offshore workers safe in harsh, remote environments is of the utmost importance as operators strive to maintain the same (or better) exploration results.
The prolonged downturn in the oil and gas industry, coupled with an ongoing global pandemic, has increased the difficulty of normal operations. It is a necessity to reduce offshore personnel so that essential staff members can do their jobs unhindered and safely social distanced. Remote solutions can boost worker safety and improve environmental conditions.
Remote operations make it easy to reduce mobilization and logistics costs. Subject matter experts (SMEs) can work from a dedicated onshore base and safely and intelligently communicate with personnel on the rig or vessel.
Since 2004, Oceaneering has been at the forefront of remote piloting and control technology, which allows subsea vehicles, such as ROVs, to be piloted from shore rather than onboard vessels and rigs. Recent advances in offshore communication networks are ensuring that resident ROVs and AUVs are a trustworthy option for carrying out offshore operations. Advanced subsea vehicles are benefiting from increased 4G offshore coverage along with faster, stable and more cost-efficient satellite communications. Additionally, more offshore facilities feature installations with direct fiber-to-shore connectivity allowing lower latency and higher fidelity connections.
Oceaneering has invested in Remote Control Monitoring Stations (RCMS) in Houston and Lafayette, La., for its remote survey operations. An SME working from an onshore base can lend expertise and remotely monitor multiple projects from one location. These onshore bases also enable customers to safely view operations from anywhere in the world and further reduce the need for expert personnel to be located offshore to monitor or troubleshoot operations.

The ROS system
Oceaneering’s Remotely Operated Survey (ROS) system can be used to execute exploration work, FPSO vessel hookup, plugging and abandonment, development, and re-latch and re-spud activities. The company also conducts remote inertial jumper metrologies, remote inertial marker buoy sets and remote monitoring of Acoustic Doppler Current Profiles (ADCPs) data.
Reliable data and communications between the rig or vessel and the onshore base are the backbone of the ROS system. The required bandwidth is determined by project scope, and some operations can be run with as little as 256 kbps of bandwidth on the rig or vessel’s existing internet access.
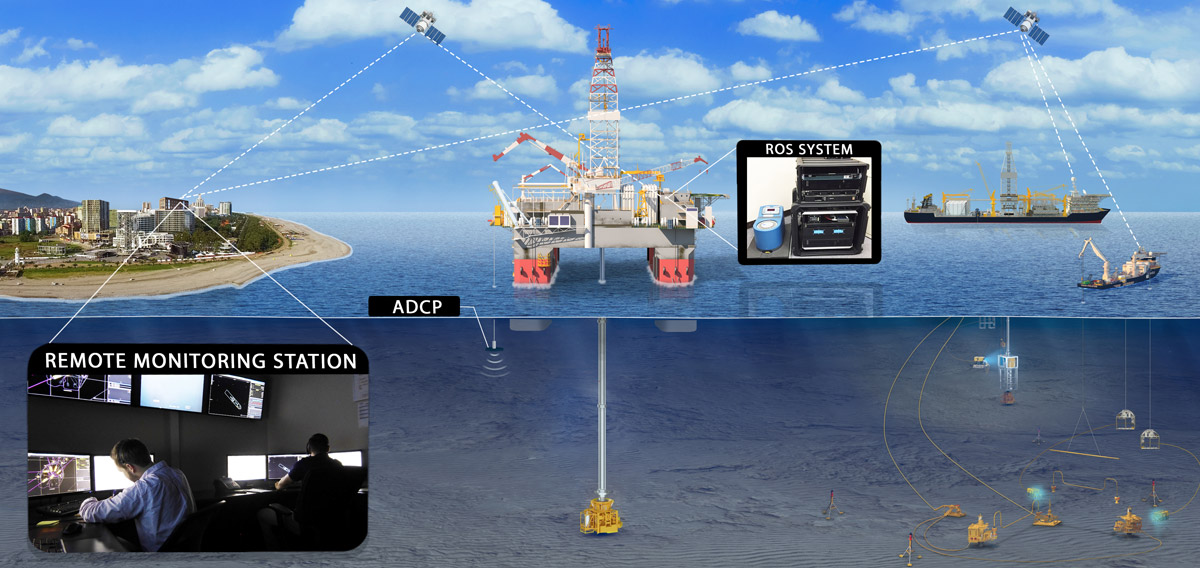
However, when the campaigns are more advanced, such as jumper metrologies, more data bandwidth is necessary to conduct remote monitoring operations and maintain constant contact with the dynamic positioning officer, ROV pilots and party chiefs.
With jumper metrology, getting the correct distance between point A and point B (e.g., from well site to manifold) is critical. By using inertial technology, the ROV will fly back and forth to secure the distance, and that calculation will be used by engineers to produce jumpers to fit to the exact space available.
Subsea marker buoy sets are launched directly from the rig as it comes onto location. Four markers are placed down, and then the conductor is set down in the middle of the buoys.
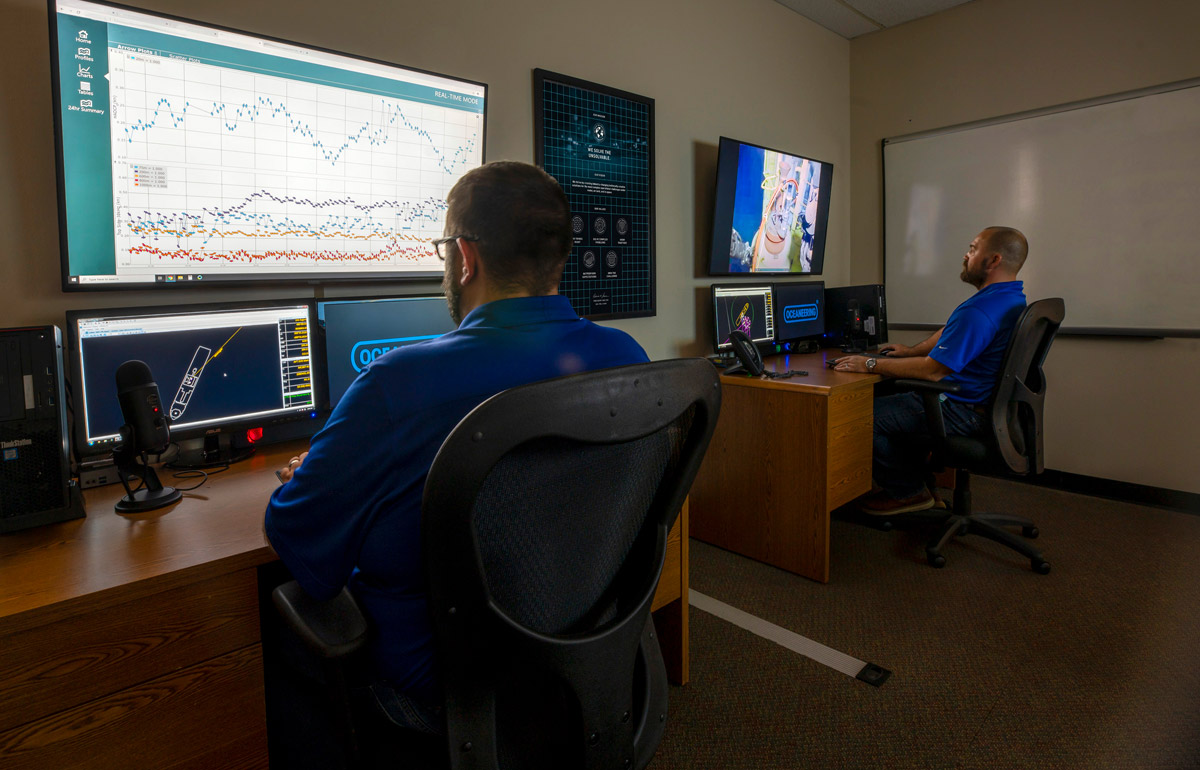
This acts as an “x marks the spot” so the rig can drill on the correct location. All of this is done remotely without having to send out additional surveyors.
Oceaneering can apply ADCPs on ROS campaigns as well. ADCPs enable the ability to monitor flow of currents past a vessel or a rig. Underwater currents can be extremely harsh, almost like rivers or spinning hurricanes called eddies; currents of 4 to 6 knots can hinder operations. The ADCP provides the ability to see what is happening on the rig but also monitor the current flow underneath.
The system provides the drilling team with real-time data, which can be reported back to the National Oceanic and Atmospheric Administration’s National Buoy Center, which in turn uses the data to create oceanographic current maps. Oceaneering’s cross-trained ROV crews offshore lower the equipment overboard when data are needed to be acquired.
First ROS campaign
In 2016 Oceaneering was approached by a major U.S. operator to find a long-term, cost-efficient positioning solution for offshore drilling moves. The operator sought a way to improve safety while also reducing costs. The solution Oceaneering proposed would provide the customer with 24/7 remote access from shore to the rig.
Oceaneering executed a one-day survey of the operator’s rig and then mobilized and installed its equipment on board in a three-day period, one week after the initial survey. The rig move occurred over a two-day period, and a preliminary field report and certified location plat were delivered in 48 hours. This allowed the operator to identify the final well position, close out drilling permits and continue field development planning.
The ROS package included two Oceaneering C-NAV3050 GNSS receivers with precise point positioning correction service, one gyrocompass, one GNSS heading sensor, one survey navigation supplemented with in-house software applications, one survey remote access and communications package with internet security.
Testing the waters off South America
In 2019 Oceaneering was contacted by a different operator to provide integrated rig services for a drillship it intended to use for a three-well campaign offshore South America. Oceaneering mobilized an ROS system, ROV and ADCP system for the campaign in summer 2019. The drillship then transited to the drilling location where it began operations in the early fall of that year.
Having the ROS system installed onboard supporting survey operations provided the operator more than 52% in actual project operational savings as compared to conventional operations. The operator saved 96 personnel onboard days as the campaign extended to a fourth well. These savings do not include other potential cost savings from logistics of crew and equipment, lodging and meals. The pandemic also has provided extra savings on quarantining costs of crew that would have normally been required in a conventional operation.
The operator went on to conduct successful drilling campaigns offshore South America into 2020.
New milestone
In 2020 Oceaneering achieved its biggest milestone yet for ROS, conducting its 100th rig move and recording 150,000 hours of operations with 99.9% uptime. Advancements in these areas will enable operators to rethink the way they conduct offshore work. To date, Oceaneering has 13 active ROS systems in use around the world with additional units in production to meet growing demand.
Recommended Reading
US NatGas Prices Rise More Than 2% on Hot-weather Forecasts
2024-07-12 - U.S. natural gas futures rose more than 2% on July 12 after touching their lowest in close to two-months earlier.
Hurricane Threatens LNG and Power Demand as Francine Forms in GoM
2024-09-09 - LNG export plants and offshore oil platforms in the Gulf of Mexico are already taking a hit as as Francine strengthens.
OPEC+ Agrees to Delay October Output Hike for Two Months, Sources Say
2024-09-05 - Oil prices edged up from multi-month lows on reports of an OPEC+ delay as well as a decline in U.S. inventories, though gains were capped by persistent demand concerns.
Port of Corpus Christi Closes as Tropical Storm Beryl Approaches
2024-07-07 - Port closures could temporarily halt crude oil exports, shipments of crude oil to refineries and motor fuels from those plants.
Oil, Gas Industry Braces for Storm After Beryl Shifts Toward Houston
2024-07-07 - Chevron and Shell have evacuated offshore platforms as Tropical Storm Beryl could grow into a Category 2 hurricane when it makes landfall in the Houston area on July 8.
Comments
Add new comment
This conversation is moderated according to Hart Energy community rules. Please read the rules before joining the discussion. If you’re experiencing any technical problems, please contact our customer care team.