Economic adjustments and continued market volatility have changed the landscape of the skilled labor available to operate and maintain well intervention equipment such as liquid nitrogen pumping equipment. Traditional solutions and standard maintenance plans are now insufficient due to capex budget restrictions and a pronounced need for reductions in the total cost of ownership for capital equipment. To help address the demand for cost reduction in this domain, National Oilwell Varco (NOV) recently developed a condition-based maintenance (CBM) system for its intervention and stimulation equipment. NOV’s Genesis nitrogen unit incorporates automated controls with GoConnect and the CBM system. The new data-driven system provides safer, more efficient operations and remote monitoring via available LTE wireless broadband connections.
Technology
The GoConnect CBM system with automated controls is designed to help less-experienced field personnel more easily operate the equipment. Due to the industry’s recent loss of field personnel with key equipment operation skills, providing reliable operation of the field equipment in a safe and repeatable manner has become increasingly difficult. The Genesis nitrogen unit addresses this need through automated priming of the boost pump and cold ends. With use of the automated control system, the nitrogen unit reliably achieves operational readiness in a very short period. In addition, safety is the cornerstone of the unit’s design. Optimal operation of the equipment through automated control improves equipment operation, thereby reducing the risk of introducing damaging temperatures or pressures. More importantly, personnel safety is achieved through wellsite pressure monitoring by the onboard system. The control system also provides an attractive benefit from a maintenance perspective, as the reliability of the control system significantly decreases the need for urgent repairs that can be costly. Though this is an improvement, the system does not remove the need for standard maintenance intervals. The CBM system continuously monitors the health of filters, pumps and hydraulic fluid. The equipment health data are stored locally and in the cloud on GoConnect for remote viewing from any internet-enabled device. In addiition, GoConnect’s ability to monitor and send automated alerts via text or email to key personnel when preset equipment thresholds have been exceeded is a highly valued feature of the product.
Case histories
Alpha & Omega Nitrogen Services chose a Genesis nitrogen unit with automation and GoConnect digital monitoring capabilities to improve its operational performance in the Permian Basin. During the third job, Alpha & Omega needed to operate while filling the onboard liquid nitrogen tank. The unit unexpectedly lost prime on the pump, and the boost bump was stopped due to potential cavitation that could cause damage. At that point, with prime on the boost pump lost, the equipment was not catching prime again to allow operations to continue. The operator contacted NOV to request assistance, and an investigation of the data within GoConnect allowed NOV to assist the customer in restoring the equipment and allowed the operator to finish the job.
Later in the month, GoConnect remote-monitoring personnel recognized the hydraulic tank temperature had reached 202 F, seven degrees above the recommended high temperature for the unit. Further review of the data revealed the engine was running at 1,800 rpm, and the boost pump was running without the triplex pump running for several hours. After calling and confirming with the operator that the unit was idle and waiting on the job, NOV recommended stopping the unit until the job began approximately 4 hours later. Once the actual field job started, the operator started the unit and was operational within 8 minutes. The hydraulic tank temperature cooled down and remained well below its recommended maximum operating temperature of 195 F for the rest of the operations.
On a subsequent field job, the GoConnect team was called by the equipment operator to inform them that he was concerned about the high discharge temperature on the unit and that the unit appeared to be “out of control.” The operator was using the unit to pump nitrogen at a low rate of 500 scf/min, which required operation of the tempering valve on the unit. A review of the data in GoConnect found that the automated tempering valve had ceased operation. On NOV’s recommendation and the company man’s acceptance, the operator sped up the unit to 750 scf/min, and then the discharge temperature fell within the job’s requirements and the field operation was successfully completed. Continued post-job troubleshooting of this issue identified a faulty actuator for the tempering valve, and an improved warranty-replacement part was ordered.
The unit has returned to the field and performed several successful jobs. Alpha & Omega is now able to effectively use the unit to achieve greater levels of consistency and efficiency in its operations, particularly related to system temperature and rate control.
Figure 1 shows a recent project with multiple rate changes and a stable discharge temperature within ±3 F. This is even better than the typical temperature range, which is expected to stay within ±5 F of a given threshold. Temperature stability was achieved even with increases in the pump rate, which typically cause cooling of the discharge temperatures, because the control system was automatically managing the unit’s performance. It is expected that such consistency will become the standard as automation is implemented across other pieces of equipment.
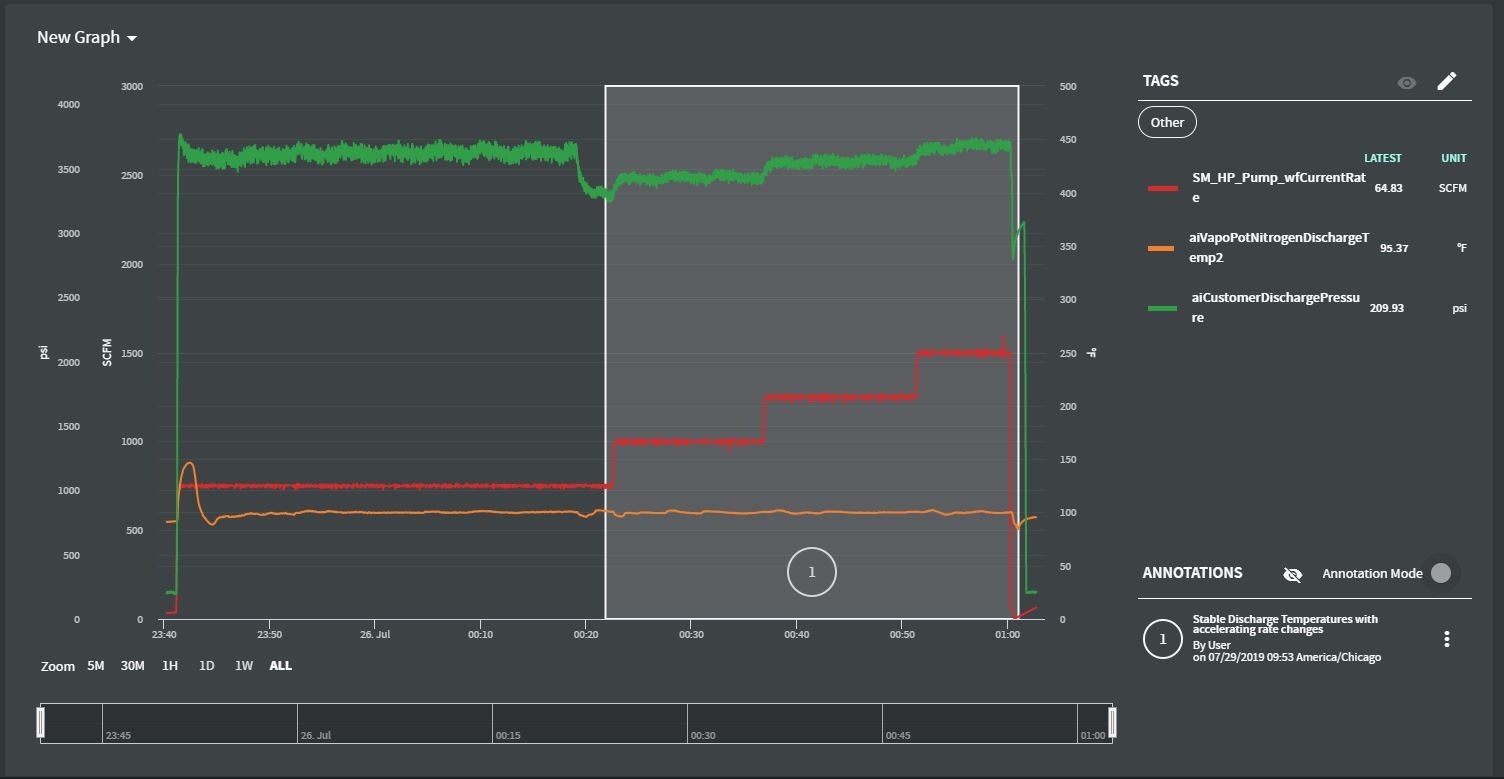
Looking forward
The automated nitrogen unit was returned to NOV for various upgrades, including the ability for enhanced manual intervention for maintaining prime during nitrogen fill operations and disabling the auto-stop function for loss-of prime indication on the boost pump. Customer feedback from future field operations will result in additional equipment and software design enhancements that will help address even more customer challenges.
Recommended Reading
Chevron Gets Approval for Farm-in Offshore Uruguay
2024-09-26 - Chevron Corp. received approval for farm-in at the AREA OFF-1 block offshore Uruguay and along with partner CEG Uruguay SA eyes the acquisition of 3D seismic over the remainder of 2024.
IOCs See Opportunity in Offshore Mexico, Despite Potential for Policy Changes
2024-08-14 - Five IOCs with offshore experience and capital—Eni, Harbour, Talos, Wintershall Dea and Woodside—continue to pursue promising opportunities offshore Mexico despite the country’s energy sovereignty push in favor of state-owned entities Pemex and CFE.
OPEC Gets Updated Plans From Iraq, Kazakhstan on Overproduction Compensation
2024-08-22 - OPEC and other producers including Russia, known as OPEC+, have implemented a series of output cuts since late 2022 to support the market.
E&P Highlights: Aug. 26, 2024
2024-08-26 - Here’s a roundup of the latest E&P headlines, with Ovintiv considering selling its Uinta assets and drilling operations beginning at the Anchois project offshore Morocco.
E&P Highlights: Sep. 2, 2024
2024-09-03 - Here's a roundup of the latest E&P headlines, with Valeura increasing production at their Nong Yao C development and Oceaneering securing several contracts in the U.K. North Sea.
Comments
Add new comment
This conversation is moderated according to Hart Energy community rules. Please read the rules before joining the discussion. If you’re experiencing any technical problems, please contact our customer care team.