Presented by:
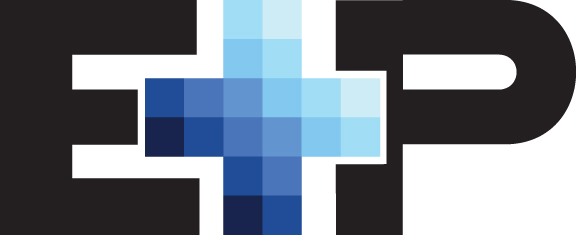
This article appears in the E&P newsletter. Subscribe to the E&P newsletter here.
To stay competitive in an unpredictable marketspace, service provider companies are providing the technology to keep operators competitive. With a higher focus on digitalization and emissions management than ever before, Halliburton and Schlumberger weighed in on what technology is proving to be most effective in the Permian Basin.
A technological aspect that is often overlooked, according to Halliburton, is the importance of artificial lift. In a basin with plenty of older wells, artificial lift is key to keeping the wells functioning properly. Halliburton is working now to introduce lift technologies to best serve Permian operators.
Meanwhile, Schlumberger is focusing its energy on reducing methane emissions in its Permian operations through its end-to-end technology development. Through a customer-centric approach, the company customizes its approach for each different methane measurement project to maximize emissions management.
Sriram Srinivasan, senior vice president of global technology at Halliburton, and Simon Edmundson, low carbon tech marketing manager for Schlumberger, joined Hart Energy to share some of the latest technology trends in the Permian Basin, as well as what to expect from the region in the future.
Hart Energy: What advancements in upstream drilling in the Permian Basin has your company made in the past year?
Srinivasan: On drilling, from Sperry, we are implementing a new version of the iCruise that we call iCruise X, which is a hardened version of iCruise specifically designed for tough drilling conditions in the Permian. It’s being used in the Middle East and similar harsh conditions in the Permian. There are specific drill bits for the Permian Basin also being introduced.
The latest version of our all-electric frac [Zeus] was introduced to an operator in the Permian a couple of months ago. And then we also have introduced in the Permian grid-powered electric fracturing as well.
In addition, we often maybe don't talk about it enough, but our artificial lift business and lift is really important in the Permian as well, but we've introduced a lot of new things in the lift business: new ESPs [electrical submersible pumps], slim line, smaller size ESPs, permanent magnet motors gas separators. We have industry-leading gas separators important for the Permian. So, a lot of new things in the artificial lift business as well, which is important for the Permian for actually for North America in general, but specifically for Permian.
I think in general for all unconventional wells, lift is important because after the decline, you have to have lift and in the lift business two things are important. First, efficiency is always important, but it's becoming ever more important. So permanent magnet motors and things like that are important for increasing improving the efficiency of the lift system. And second, gas separators are important because anytime that you ingest gas into the gas pockets into the well – and this happens a lot in the Permian – it messes up with the operation of the ESPs. It can really reduce its life.
Hart Energy: What kind of R&D projects has your company been implementing in the Permian?
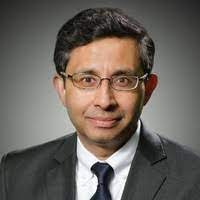
Srinivasan: SmartFleet is the first intelligent system to give operators control of the subsurface while pumping. It integrates real-time subsurface fiber measurements, live visualization and automation to optimize fracture placement. SmartFleet is more than just automating treating pressures. Through its visualization and automation, operators can make confident design changes on the fly to improve cluster efficiency and better manage frac hits. It is a tool that places operators in the driver’s seat, giving them control to better place stages, drive performance and optimize well placement.
Edmundson: While we certainly have ongoing R&D for technologies aligned with the needs of the Permian Basin, one of our key focus areas over the past several years has been related to technologies and offerings aimed at helping our customers reduce their emissions in the Permian, particularly those from methane.
We recently launched Schlumberger end-to-end Solutions, known as our SEES business, which is aimed at partnering with operators to reduce or eliminate both methane and routine flaring emissions. Customers also have access to our growing Transition Technologies portfolio, which includes technologies and services with a quantifiable emissions reduction impact.
On the Transition Technologies side, we've recently quantified the impact that our Vx Spectra surface multiphase flowmeter has in reducing methane emissions in metering applications compared to a separator. Vx Spectra eliminates separator components that vent methane by design, and also results in less complex well pad setups that can also reduce fugitive emissions. The quantity of vented methane emissions avoided depends on the pneumatic components replaced, but it can be up to 500 tons of CO2 equivalent per separator replaced per year.
Hart Energy: What trends in digitization have you seen or implemented in the Permian as ESG remains a prevalent topic among both producers and investors?
Srinivasan: I think [digitalization and ESG] are two separate things. We are doing digital for improving a lot of things, including ESG, but it's even beyond that. There's some indirect ESG [in SmartFleet] because if you're optimized on how you pump you lower treating pressures, you save fuel. So you burn less fuel. So therefore ESG benefits.
We are using a lot of our own [cement that’s] not new, but it's a non-Portland cement called NeoCem. The traditional cementing uses something called Portland cement, and the act of making Portland cement has a lot of ESG footprint emissions and things like that. By going to this NeoCem, you just cut all of that out. So it's inherently has a much better ESG profile than a regular Portland cement.
If you think about ESG impact, frac operations are the biggest contributors for emissions. Electric fracturing reduces those emissions, but electric isn’t a one size fits all. Halliburton has focused on electric solutions that exceed in performance, while offering flexibility to use various power sources, including the grid and reciprocating engines. So that's the innovative things we're doing for ESG. There are other things which don't receive as much press necessarily, but again, going back to lift because every well has an artificial lift system, and these things consume a lot of electricity. So anything you do to reduce you know make them more efficient improves the ESG footprint.
Edmundson: We've managed to prove and quantify the impact of various technologies to reduce drilling time and reduce emissions. One of the most interesting of these is our Performance Live service. The value proposition of Performance Live is it's a remote collaboration, digital ecosystem that not only enables you to perform directional drilling operations remotely, but also automates routine tasks and enables experts to collaborate in one place to be able to make real-time decisions on operations.
So, the value proposition is we can drive performance improvements with this service by leveraging the collaborative environment: All the right experts are in the right place, making decisions at the right time to nip any issues in the bud throughout the drilling process. Competency development is accelerated within our drilling teams, by having them all working remotely and having that cross collaboration of ideas and best practices of specific drilling challenges in the Permian.
In the Permian specifically, we were able to show that Performance Live operations quantifiably improved drilling efficiency and reduced up to two days of drilling time in a typical Permian lateral well, which equates to around 50 tons of CO2 emissions from the rig.
Specific to methane and routine flaring reduction or elimination, our SEES business incorporates a digital platform that can consolidate all data and measurements to enable the best quality strategic decisions to happen in the right place at the right time.
Hart Energy: How has your company been developing emissions management projects in the Permian? What impact has that made on your company’s net-zero and ESG goals?
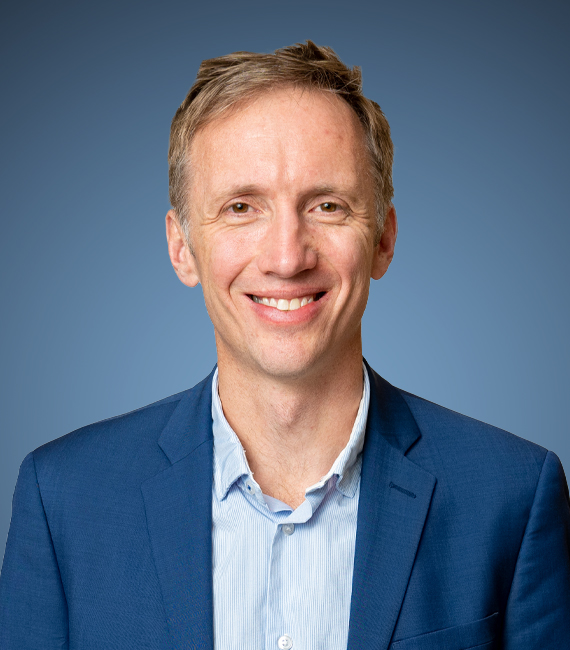
Edmundson: As I’ve already mentioned, top of the list is reducing methane and routine flaring emissions. Methane is a potent greenhouse gas; over a 20-year time period, it has 84 times the global warming effect compared to CO2, and it's coming under ever stricter regulatory requirements. There's also been a lot of discussion and activity in the Permian recently around methane. You could view that negatively, but on the positive side, I think this offers a great opportunity for our industry to showcase our ability to address challenges with collaboration and technology solutions to quickly tackle methane emissions sources.
Within the global SEES initiative, we're a part of the Project Astra collaborative, which is a project in the Permian that is aims to optimize the use of point sensors to detect, quantify and locate methane leaks.
Another question which you'd posed, and we often get, is, “How do all these efforts tie into Schlumberger’s net-zero emissions commitment?” As background, last year, we committed to net zero emissions across all our emissions scopes—Scopes 1, 2 and 3—by 2050. Our path to net-zero includes both reduction in our emissions across along with carbon negative actions. Of course, our technology options will help us to reduce our own Scope 3 emissions footprint, but our main focus is on developing these emissions reduction technologies to help our customers reduce their footprint.
Hart Energy: What tools or devices would you say has made the biggest impact on the Permian in the past year?
Srinivasan: If you can point to one thing for operational efficiency [it’s] simul frac because you use the same spread to do multiple wells in the pad. You are making sure that there's minimal downtime, and you're optimizing the use of your assets. So it's working sort of on a continuous basis as opposed to having lots of downtimes in between. You simultaneously frac multiple wells.
Hart Energy: What kind of technologies or advancements do you predict will become more popular in the Permian in the next few years?
Srinivasan: I think the frac space is just going to become sort of the de facto standard; [it] already has become, I think, increased usage of electric, frac dual fuel.
This is where I think it's unique to us: [what] we're pushing is this idea of disposable fibers. So if you have fiber optic sensors and there's many ways of doing it, you can have fiber optics behind casing, which may be slightly more expensive as opposed to disposable fibers. For a more affordable and routine option, disposable fiber can be pumped down hole in minutes to provide direct measurements of well interactions and fracture performance. Having that kind of real-time sensor data feeding intelligent systems such as SmartFleet can optimize fracture placement.
I think this is going to be differentiating for us because we are the only ones who have it, but I think this is where we're pushing in the Permian. As operators see the value of it, we predict this will take off in a big way.
Edmundson: I think we'll see a development of technologies in the methane detection and measurement space, and in fact we’re already deeply involved in both vetting and development of these types of technologies. As we collectively sharpen our focus on methane emissions, matching sensor applications and technologies to potential locations and sources as part of an efficient measurement array will become increasingly critical to ensuring that our actions are as effective as they can possibly be. Of course, there is a strategic element to this equation in defining the optimal combination of detection methods to use, but the bottom line is that the better the detection technologies are, the faster we are going to be able to find and fix leaks. We’re already seeing a lot of interesting innovation in this space, and I expect it to be exciting field during the next few years.
Recommended Reading
E&P Highlights: July 29, 2024
2024-07-29 - Here’s a roundup of the latest E&P headlines including Energean taking FID on the Katlan development project and SLB developing an AI-based platform with Aker BP.
E&P Highlights: Aug. 19, 2024
2024-08-19 - Here’s a roundup of the latest E&P headlines including new seismic solutions being deployed and space exploration intersecting with oil and gas.
E&P Highlights: July 15, 2024
2024-07-15 - Here’s a roundup of the latest E&P headlines, including Freeport LNG’s restart after Hurricane Beryl and ADNOC’s deployment of AI-powered tech at its offshore fields.
E&P Highlights: Aug. 26, 2024
2024-08-26 - Here’s a roundup of the latest E&P headlines, with Ovintiv considering selling its Uinta assets and drilling operations beginning at the Anchois project offshore Morocco.
E&P Highlights: Sept. 16, 2024
2024-09-16 - Here’s a roundup of the latest E&P headlines, with an update on Hurricane Francine and a major contract between Saipem and QatarEnergy.
Comments
Add new comment
This conversation is moderated according to Hart Energy community rules. Please read the rules before joining the discussion. If you’re experiencing any technical problems, please contact our customer care team.