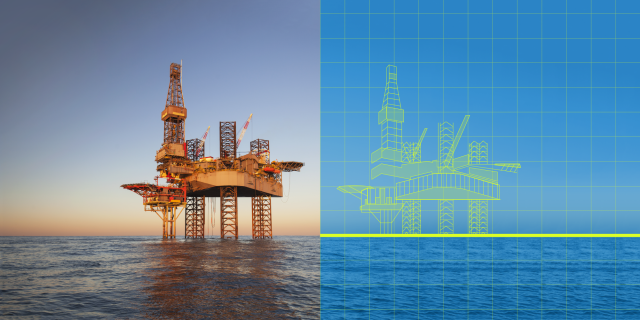
Digital twins create models to accurately identify hot spot stresses on offshore facilities. (Source: Akselos)
Against the backdrop of uncertain energy prices—which are expected to be lower for longer—and aging assets attached to maturing hydrocarbon developments, the energy industry is adopting digital transformation strategies. By exploring new, disruptive technologies that challenge established operating models, assets will be able to operate well beyond their intended design life, safely and cost effectively.
In 2016 Shell challenged technology developer Akselos to deploy its next-generation structural simulation software to one of its late-life assets in the North Sea. The goal was to provide sufficient structural integrity and performance data to demonstrate compliance with current codes and standards as well as support a life extension of 20 years on a 50-year-old asset without an increase in inspection requirements.
A two-year joint industry project (JIP) ensued with the aim to transform asset structural integrity management by pairing a detailed 3-D, condition-based structural model with real-time sensors to create the first predictive digital twin of an entire asset in the industry. Danish engineering firm LIC Engineering was a key partner in the project.
Large-scale simulations
Now approaching the end of the two-year project, Shell and Akselos have successfully implemented a fast, accurate and cost-effective life extension technology and methodology. The new approach ultimately improves the performance of the platform by introducing unprecedented levels of accuracy, made possible by new technology developed at the Massachusetts Institute of Technology and the Swiss Federal Institute of Technology.
“We were in need of a new methodology,” said Emmanuel Fakas, Shell’s structural technical authority. “The traditional approach using existing simulation tools has served the industry well for decades, but there was a significant amount of time-consuming sub-modeling required, which resulted in, at times, overly conservative estimates. When we became aware of new technology that was capable of industrial scale simulations with absolute accuracy, we understood how powerful this could be.”
On a beam model example, conventional models using stress concentration factors estimated that each joint was in need of immediate repair or replacement. The Akselos sensor-enabled model showed that each of the joints had decades of safe operating life remaining, with many far surpassing Shell’s life-extension objective of 20 years.
“The software has the ability to mesh all joints, estimating the hot spot stresses accurately at the right locations,” Fakas said. “It accounts for the chord flexibility explicitly and in a simple analysis. The traditional approach requires several separate analyses, which can really escalate the time involved based on the number of local joint models required.”
This new level of understanding and accuracy is the difference between a significant investment in maintenance (or even decommissioning) and safe life extension.
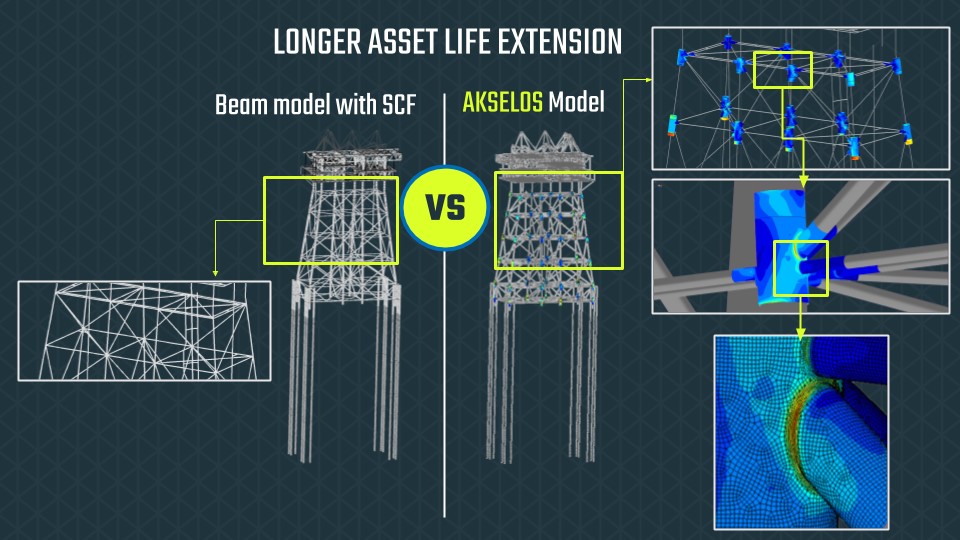
Eliminating uncertainty
Digital twins are not a new concept. But the numerical model that is traditionally used as a basis for the technology is based on best estimates and does not eliminate uncertainty. The key to eliminating this uncertainty and achieving true accuracy is a simulation that is fast enough to integrate sensor data at the speed of a sensor feed.
The computational method behind the digital twin selected by Shell for this project is based on an algorithm called reduced basis finite element analysis (RB-FEA). It produces models 1,000 times faster than the industry standard numerical method, finite element analysis (FEA). Without this speed, true condition-based modeling of large assets would not be possible because of the time required to perform the calculations using conventional FEA software.
This speed allows the Akselos model to accurately identify hot spot stresses. These data are used to focus inspections on areas of risk rather than wasting time on inspecting areas that have no issues.
Benefit of sensors
The speed also makes the technology compatible with operational sensor data and, as a result, the accurate simulation tool that aligns with Shell’s vision for true condition-based monitoring of large assets.
Accelerometers and wave radar data are assimilated into the digital twin to provide a true picture of the loading conditions and resulting hot spot stresses. Engineering technology inputs, like wave and current loading condition, run and failure criteria are integrated into the digital twin. This is part of an integrated workflow interfacing with operational feeds such as sensor and inspection data. The outputs are then interpreted through a dashboard to understand current and future condition.
From laboratory to asset
Early in the two-year JIP, LIC Engineering mocked up a laboratory model to demonstrate the procedures of establishing a digital twin, using eight accelerometers and three displacement sensors. The laboratory model had the structural complexity of an offshore jacket foundation, and a digital twin was set up to demonstrate the high-fidelity structural analysis using the RB-FEA method.
This demonstrated the accuracy of RB-FEA, and a simulation of the real-life assets was modeled. The finite element model has 3.1 million FE degrees of freedom and was solved within a few seconds on a single computing core. While the solution time is comparable to a 1-D beam model, the full 3-D stress field was resolved in this model, which is of particular importance in complex structural components like the joints.
Akselos and LIC Engineering developed a streamlined workflow based on real-life experience of offshore engineers. This industry knowledge was digitalized to enable much faster detailed analysis of offshore assets. The result was a single streamlined workflow in place of a process that used to require multiple software applications, and a complex workflow transition from holistic beam models to detailed 3-D joints. This new workflow fully integrates with wave loading and other preprocessing plug-ins as well as post-processing add-ons for fatigue and code checks.
Operational and added value
The physics-based digital twin, now fully operational for the North Sea asset, aims to provide understanding of the real structural life and health of the fixed platform. The results should enable the asset team to significantly improve the inspection strategy and introduce a next-generation methodology for asset integrity management.
With an improved risk-based inspection strategy, Shell expects to safely continue operating this particular asset up to 20 years. With successful results, the technology might be rolled out to other aging assets across Shell’s upstream portfolio and across younger assets to lower opex through improved health analysis.
Shell and Akselos have pioneered accurate condition-based monitoring that could completely transform asset integrity management in mature basins like the North Sea and beyond.
Have a story idea for Tech Watch? This feature highlights leading-edge technology that has the potential to eventually address real-life upstream challenges. Submit your story ideas to Group Managing Editor Jo Ann Davy at jdavy@hartenergy.com.
Recommended Reading
US NatGas Prices Rise More Than 2% on Hot-weather Forecasts
2024-07-12 - U.S. natural gas futures rose more than 2% on July 12 after touching their lowest in close to two-months earlier.
Hurricane Threatens LNG and Power Demand as Francine Forms in GoM
2024-09-09 - LNG export plants and offshore oil platforms in the Gulf of Mexico are already taking a hit as as Francine strengthens.
OPEC+ Agrees to Delay October Output Hike for Two Months, Sources Say
2024-09-05 - Oil prices edged up from multi-month lows on reports of an OPEC+ delay as well as a decline in U.S. inventories, though gains were capped by persistent demand concerns.
Beryl Makes Landfall East of U.S.’ Largest Energy Export Gateway Corpus Christi
2024-07-08 - Tropical storm Beryl made landfall in Texas as a Category 1. Life-threatening storm surges are expected to continue along the coast of Texas from Port O’Connor to Sabine Pass, including the eastern portion of Matagorda Bay and Galveston Bay, according to the National Hurricane Center.
The Biden Effect: LNG SPAs Fall 15% in First Half 2024 After Pause
2024-07-03 - Poten & Partners data show that the total volumes associated with LNG sale and purchase agreements fell by 15% in the first half of 2024 compared to the same period in 2023 following the Biden administration’s LNG pause.
Comments
Add new comment
This conversation is moderated according to Hart Energy community rules. Please read the rules before joining the discussion. If you’re experiencing any technical problems, please contact our customer care team.