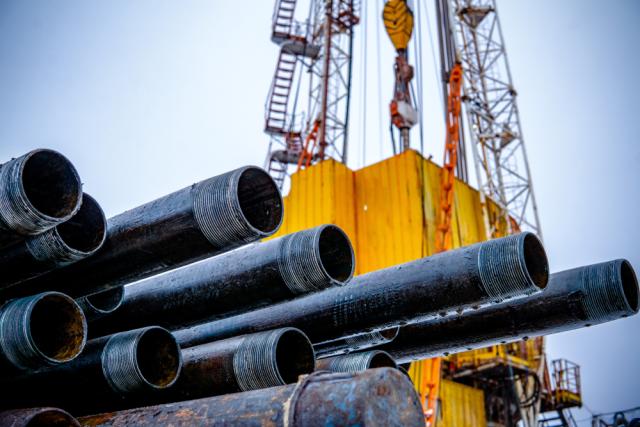
Peak Completion Technologies Inc. created the Killshot tool as a large-bore, single-trip tool that can kill a well prior to placing electrical submersible pumps (ESP) and can prevent an ESP from falling out of reach should it accidentally come loose during its service life or removal. (Source: Shutterstock)
The engineers at Peak Completion Technologies Inc. created the Killshot tool as a bespoke solution to kill wells without heavy fluids and catch loosened downhole pumps.
Designed as a large-bore, single-trip tool, it can kill a well prior to placing electrical submersible pumps (ESP) and can prevent an ESP from falling out of reach should it accidentally come loose during its service life or removal.
ESPs don’t typically fall, but when they do, retrieving them can be costly and time-consuming.
Combining the two functions in a large-bore tool saves time and money against ever-rising completion costs, said Sloane Muscroft, vice president of engineering for Peak.
Killshot eliminates the need for a fluid kill while placing the ESP. Fluid kills are costly and difficult to remove. The tool combines the isolation plug insertion trip with the ESP catch tool trip, saving time and money in the process. And the large bore allows for almost completely free production flow once the isolation plug is pumped out or ruptured, depending on what type of plug a completion team uses.
The Killshot’s pedigree
The Killshot descends from two previous frac products. The first one was the Set-a-Seat frac baffle, designed to replace composite plugs. Developed many years ago, “the idea was that you could set it, drop a frac ball into it and frac against it,” Muscroft said. Composite balls need to be cleaned up while dissolvable frac balls generally required no cleanup, saving the cost of a second downhole trip.
With the advent of current composite plugs, the Set-a-Seat became less necessary, although Muscroft said Peak continued to sell some, mostly in international markets.
Set-a-Stop was the next step, created at customer request as just an ESP catcher, without the sealing function “in case their tubing breaks” during ESP placement or retrieval, he said.
“Operators already do that, but they generally do it with a tubing anchor or a double grip arrow set.”
The problem with those is they have a smaller bore, about half the bore of the casing. The smaller bore can restrict oil flow, and the tools can corrode or become clogged with sand or other downhole debris, requiring a cleanout or fishing trip to remove the hardware. The second tool was similar to the first, with the isolation function removed.
Set-a-Stop was also intended as a one-off solution, but its usefulness started a new product line for Peak, Muscroft said.
One tool catches ESPs, replaces fluid kills
Killing a well with heavy fluid is costly and time-consuming to undo, requiring a separate downhole service trip, he said. Customers “wanted the sealing ability, and they wanted the ability to plug off the production zones of the well for wells that were coming in or that might create concerns about gas pockets, or other issues could happen while they were installing the ESP,” he said.
To meet well control requirements, Peak added a sealing element, bi-directional load-carrying capabilities and a pressure retaining mechanism. The latter is removed once the ESP is installed. Developers based the element and the opposing slips on the Set-a-Seat design.
Installing the ESP—which can be 30 ft or longer and includes power cables, control lines and other equipment—while doing a fluid kill can be complicated, Muscroft said.
“What the Killshot allows them to do is to not worry about kill fluids or plugs. They can run a simple wireline lubricator setup, if they’re concerned about well control, just to get the Killshot in place. Once the Killshot’s on depth, they can pull that all off and insert the ESP, generally speaking, without the same concerns that they would have if they didn’t have the Killshot in place.”
Reception and future
Muscroft said clients have especially appreciated the fact that the Killshot saves “time and money associated with fluid swaps at the end of the completion, prior to putting the well on production. This also eliminates the risk of decreased flow” associated with a fluid kill, which allows operators to maximize flow from the start of production. It also allows for nearly unrestricted fluid flow during the production phase.
“Looking forward,” Muscroft said, “we see additional potential for this tool to be used in other completions, including frac-protect type operations as well as scab-liner applications in production casing.”
Recommended Reading
Hurricane Helene Shuts in Nearly 30% of GoM Crude Production
2024-09-25 - Bumped up to hurricane classification on Sept. 25, Hurricane Helene has shut in 29% of crude and 17% of natural gas production in the Gulf of Mexico as it nears landfall in Florida tomorrow.
Baseline Energy Opens New Uinta Basin Power Generator Facility
2024-09-24 - Baseline Energy Services’ facility in the Uinta Basin plans to support the region’s mobile power generator fleet with a range of maintenance and repair services.
Quantum Backs Tug Hill Team in New E&P Vickery Energy
2024-09-24 - Quantum Capital Group is backing the executives behind Tug Hill Operating, which sold to EQT Corp. for $5.2 billion, in a new Appalachian Basin company Vickery Energy Partners.
VTX Energy Quickly Ramps to 42,000 bbl/d in Southern Delaware Basin
2024-09-24 - VTX Energy’s founder was previously among the leadership that built and sold an adjacent southern Delaware operator, Brigham Resources, for $2.6 billion.
E&P Highlights: Sept. 23, 2024
2024-09-23 - Here's a roundup of the latest E&P headlines, including Turkey receiving its first floating LNG platform and a partnership between SLB and Aramco.
Comments
Add new comment
This conversation is moderated according to Hart Energy community rules. Please read the rules before joining the discussion. If you’re experiencing any technical problems, please contact our customer care team.