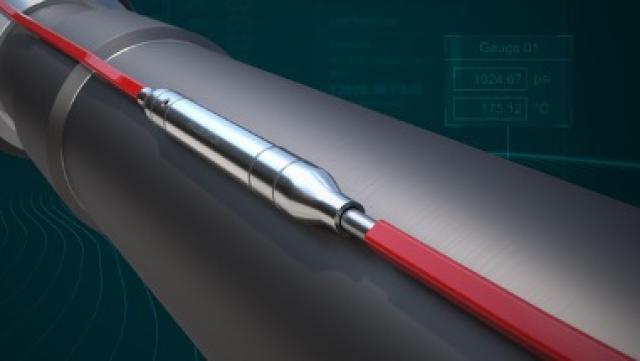
DataSphere Array Sensor deployed on tubing or on casing prior to cementing (clamp not shown for visibility). (Source: Halliburton)
One of the appeals of downhole sensors is that they can provide real-time data about wellbore conditions.
Armed with that data, operators can validate construction of the well, make better-informed decisions about well spacing and get a sense of a reservoir’s reaction to fracturing and production. Deploying one or more sensing devices in casing and cemented in place between the open hole and casing provide far well-bore information.
“You can’t have an intelligent completion without data,” said Elias Garcia, Halliburton’s global business development manager for intelligent completions.
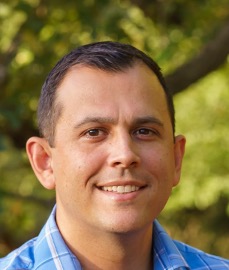
Gerald Stutes, senior technical advisor at Intelligent Completion Tools – North America, noted the importance of having real-time downhole data available to make decisions based on the most current information available.
With data, companies can make informed decisions about completions and production and have a better sense of what’s going on with the reservoir.
From a reservoir perspective, data can help an engineer understand if the modeling was correct, he said.
The technology can tell Stutes whether his “wellbore [is] reacting like I expected it to from the initial design phase, and with the information that I'm getting, [I can tell] whether I was off or I was correct, and the impact going forward in the development of the field,” he said.
Halliburton’s DataSphere Array system, with its 5/8 inch outside diameter, uses a miniaturized quartz gauge that measures pressure and temperature through cement.
“The goal was to be able to deploy more sensors in the line, reduce the power constraints, reduce the heat dissipation and increase the lifetime,” Garcia said.
By reducing the size of the gauges, Halliburton was also able to lower the power consumption, which made it possible to deploy “many more sensors in a line,” he said. “Before, we were able to deploy only eight to ten sensors because the power consumption was much higher.”
Halliburton started cementing DataSphere Arrays in place between the open hole and casing and was able to prove the sensors were able to measure pressure through the cement.
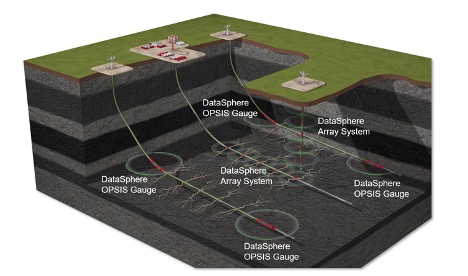
“It can deploy on casing, can be cemented in place and monitor [the] pressure and temperature of the formation without a perf” even through the cement, Stutes said.
Garcia said that an array can be run wherever a line to downhole gauges is run. The array doesn’t have a mandrel and the sensors are pre-welded onto the line, so no connections are required, he added.
“This is clamp and go, saving a lot of time,” he said.
Garcia said the approach challenges standard thinking.
“Standard convention tells you that cement is a barrier, and that’s why your well doesn’t flow to the surface, because you’ve got cement protecting it,” he said. “But cement is porous, and cement is permeable, even though it’s very small permeability.”
DataSphere Array can also be deployed in existing wells, but a perf is necessary to get through the casing before a new production string is run downhole, Stutes said.
“It’s a string inside of a string, and the newer string has the sensors on it inside the casing,” he said.
Proving grounds
The first deployment of the DataSphere Array in 2018 initially focused on showing that the sensors could provide useful data in cemented applications, Stutes said.
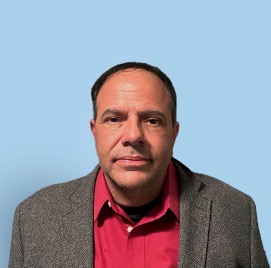
Garcia said that operator acceptance of the technology has been growing.
“If an operator tries one with five sensors, then the next one will probably be tried with 10 to 15 sensors, and then the next one will be tried with 20 to 25 sensors. They're getting really good data from these sensors,” he said.
Halliburton has installed a record 75 DataSphere Array sensors in a 20,000-ft well, he said. In total, Halliburton has run 54 array strings across 38 wells with a total of 625 sensors since 2018, he added.
In one deployment, Garcia said, a customer had drilled multiple horizontal wells with a frac plan in mind. But with the data available from the DataSphere Array, the customer saw the fracs from the first couple of wells propagated further than expected, he said.
“That had repercussions into the frac plan for the next well” because the customer wanted to avoid over-fracking, he said. The customer adjusted the frac volumes on subsequent wells and “basically saved many times what they paid for our system.”
The DataSphere Array has been deployed in the Permian Basin, Haynesville Shale, the Bakken and the Marcellus Shale in the U.S., as well as the Montney in Canada. Garcia said there is interest in the technology in the Middle East, as well as in offshore wells where operators are seeking information from lower completions about where production is coming from across multiple sand screens.
The DataSphere Array technology has also helped operators validate the construction of carbon capture and sequestration wells.
“A big part of the well is to have a really good cement job, to be sure things are correct in the well,” Stutes said.
Garcia said the DataSphere Array can help operators prove to regulators that the CO2 storage wells are not affecting nearby water tables or inducing fractures that let gasses migrate to the surface.
“Our sensors are instrumental in providing that information to regulators in many of these carbon sequestration type wells,” he said. “We provide multiple monitoring points for different layers to understand how the CO₂ plume is distributed across the reservoir.”
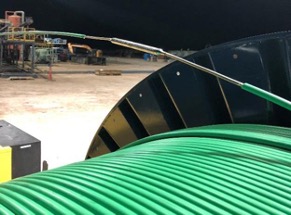
Complementary technologies
According to Garcia, the DataSphere Array “plays really well” with the fiber optics that companies are deploying in their wellbores.
“Operators think they need to run fiber or this technology, but in reality, you need both,” he said, adding that the combination of technologies gives operators the ability to monitor both the near- and far-wellbore. “This technology is about the closest you get to distributed pressure sensing. We certainly cannot provide as many points as (distributed temperature sensing) DTS on fiber, but we provide more pressure granularity than has been available in the past.”
Recommended Reading
Lake Charles LNG Selects Technip Energies, KBR for Export Terminal
2024-09-20 - Lake Charles LNG has selected KTJV, the joint venture between Technip Energies and KBR, for the engineering, procurement, fabrication and construction of an LNG export terminal project on the Gulf Coast.
Macquarie Sees Potential for Large Crude Draw Next Week
2024-09-19 - Macquarie analysts estimate an 8.2 MMbbl draw down in U.S. crude stocks and exports rebound.
EIA Reports Natural Gas Storage Jumped 58 Bcf
2024-09-19 - The weekly storage report, released Sept. 19, showed a 58 Bcf increase from the week before, missing consensus market expectations of 53 Bcf, according to East Daley Analytics.
Electrification Lights Up Need for Gas, LNG
2024-09-20 - As global power demand rises, much of the world is unable to grasp the need for gas or the connection to LNG, experts said.
Woodside to Maintain at Least 50% Interest in Driftwood LNG
2024-09-18 - Australia’s Woodside Energy plans to maintain at least a 50% interest in the 27.6 mtpa Driftwood LNG project that it's buying from Tellurian, CEO Meg O’Neill said during a media briefing at Gastech in Houston.
Comments
Add new comment
This conversation is moderated according to Hart Energy community rules. Please read the rules before joining the discussion. If you’re experiencing any technical problems, please contact our customer care team.