As oil and gas companies face increasing pressures to become more efficient, U.S. shale operators are becoming smarter and faster—and it’s more important than ever.
The demand for energy continues outstripping supply despite a rising rig count. According to industry analyst Enverus Foundations, the number of rigs running in the U.S. in the second quarter rose 9% compared to the first quarter, and the rig count is 54% higher year-over-year.
Challenging the status quo of long-held assumptions or approaches in the field is necessary to uncover new methods that can lead to greater productivity to maximize capital and human resources. Continuing to do an activity the same way it has always been done can cause companies to lose efficiency gains that could make a difference in their profits.
The understanding and use of proppant is a prime example. Operators rely on large quantities of water, chemicals and sand to extract oil and gas, allowing those assets to flow to the surface. Sand and fluid are essential to open and keep fractures open in a well and stimulate the well to produce. Proppant materials are sorted for size and sphericity to ensure they serve as an efficient conduit for hydrocarbon production from the reservoir to the wellbore.
The oil and gas industry has long assumed that sand and fluid flow uniformly together through casing. Surface tests conducted by GEODynamics and six shale operators in the U.S. unequivocally proved otherwise. This revelation is important because inconsistent proppant placement impacts well productivity and frac operations and increases risk of screen-out.
The surface tests revealed important insights. First, larger grains of proppant are far more likely to slip past early clusters than smaller grains, which tend to be distributed evenly among clusters. Second, perforating designs can result in more evenly distributed proppant among clusters and further flatten the distribution. Indeed, the irregular flow of proppant in the casing is just as important as formation variability or stress shadowing. Third, larger-sized 40/70 mesh sand is more likely to slip past earlier clusters than 100 mesh sand.
A second round of tests with the U.S. shale operators followed, which showed that a change in the fracture design which focused on a more even slurry distribution from cluster to cluster further reduced the differences among clusters although larger grains still slipped past early clusters.
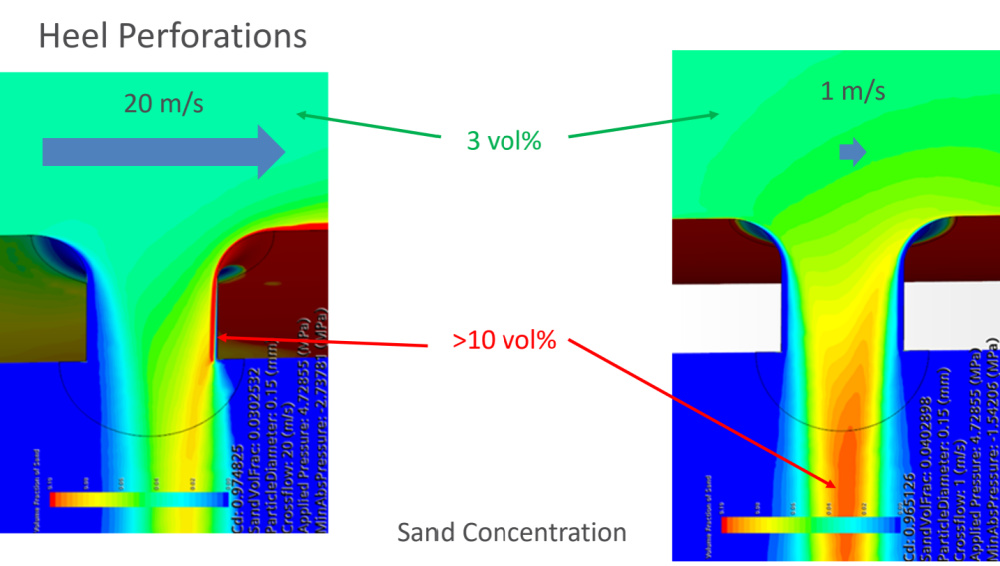
Fine sand is distributed uniformly throughout the length of a perforated completion while coarser sand tends to slip past the heel perforations and concentrate on the bottom toward the toe of the completion. As these are broad statements, the main point is that gravity and physics work. Fluid velocity (which varies), fluid properties, proppant size and perforation orientation all matter.
While not all perforation holes are created equal, it is now possible to predict how proppant will flow. This gives oil and gas companies insight into when and where to invest to maximize their returns.
As a result of the previously mentioned surface tests conducted with U.S. shale operators, StageCoach was developed to accurately predict how proppant and fluid will flow through casing. The surface testing also provided insight on hole placement: outflow can be optimized by placing perforations in the middle rather than the top of the pipe.
By accurately modeling proppant transport, distribution and erosion across clusters, operators are empowered to be more deliberate when selecting hole size and/or charge type, enabling them to achieve the assumed distribution without cost variances. Computational fluid dynamics modeling of proppant slurry movement powers predictive insights, which optimizes job parameters to ensure a more uniform proppant distribution from cluster to cluster.
Beyond the applicable learnings and predictive insights this software modeling can deliver, it’s poignant to note how the creation and application of digital technologies has helped oil and gas companies carve out competitive advantages that impact production and the bottom line.
Digitizing surface test information to predict where sand will go in a stage debunked historical assumptions about proppant flow that could negatively impact companies’ well productivity. This enables crews to work smarter and more efficiently. It also enables crews to make the proposed frac design on paper a reality in the field. Better fracs lead to better stimulation, which results in better performing wells and optimized completions.
Maximizing production is key to all stakeholders in the production chain as completing a well is very expensive. The ability to predict how proppant will flow allows oil and gas companies to create more accurate frac designs that result in more productive wells. The efficiencies gained through this process can positively impact profits.
About the Authors: Phil Snider is consulting completions adviser at GEODynamics. Steve Baumgartner serves as GEODynamics’ senior engineering technical adviser.
Recommended Reading
No Good Vibrations: Neo Oiltools’ Solution to Vibrational Drilling Problems
2024-09-10 - Vibrations cause plenty of costly issues when drilling downhole, but Neo Oiltool’s NeoTork combats these issues, enhancing efficiency and reducing costs.
TGS Releases Illinois Basin Carbon Storage Assessment
2024-09-03 - TGS’ assessment is intended to help energy companies and environmental stakeholders make informed, data-driven decisions for carbon storage projects.
As Permian Gas Pipelines Quickly Fill, More Buildout Likely—EDA
2024-10-28 - Natural gas volatility remains—typically with prices down, and then down further—but demand is developing rapidly for an expanded energy market, East Daley Analytics says.
HNR Increases Permian Efficiencies with Automation Rollout
2024-09-13 - Upon completion of a pilot test of the new application, the technology will be rolled out to the rest of HNR Acquisition Corp.’s field operators.
Liberty Capitalizes on Frac Tech Expertise to Navigate Soft Market
2024-10-18 - Liberty Energy capitalized on its “competitive edge” when navigating a challenging demand environment in third-quarter 2024, CEO Chris Wright said in the company’s quarterly earnings call.
Comments
Add new comment
This conversation is moderated according to Hart Energy community rules. Please read the rules before joining the discussion. If you’re experiencing any technical problems, please contact our customer care team.